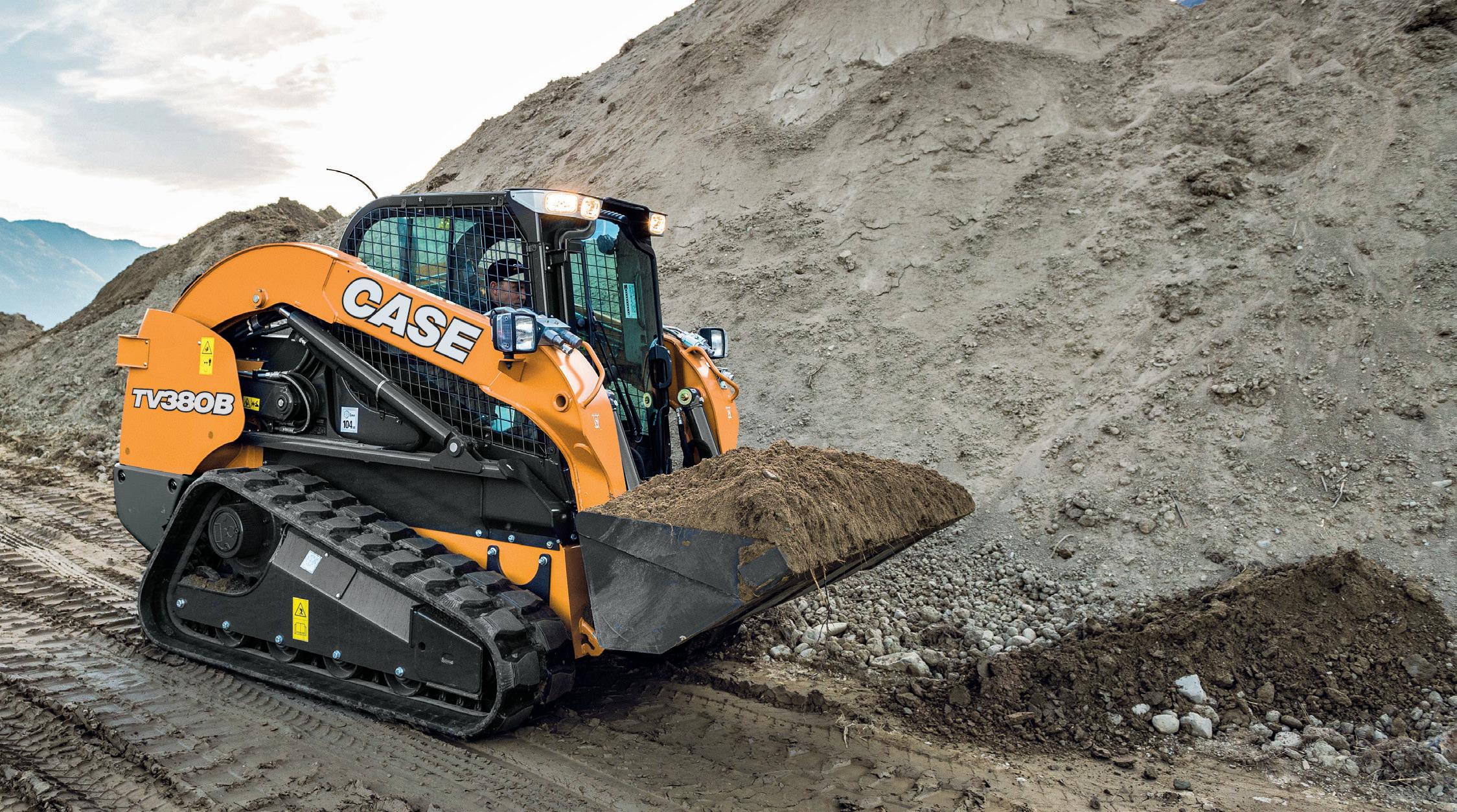
11 minute read
FEATURE STORY
In 1943, Abraham Maslow introduced the concept that ‘safety’ is a basic human need as part of a needs hierarchy for individuals. It is the second tier in his hierarchy of needs that is studied and applied throughout education and business, followed by physiological needs.
Our need for safety is stirred by our environment and how we react to it, this according to an article on Interaction-design.org. In other Maslow research, safety is coupled with financial security, health and wellness, and safety from accidents and injury. Verywellmind.com presents a very abridged version of Maslow’s concept of needs and its criticisms, but it still manages to influence education and business.
People make countless decisions every day, which have a seemingly endless amount of outcomes and consequences - with their ‘what-if’ scenarios and hypotheticals. But, it is important to note that the construction industry is a driving force - ensuring, not just the progress of any community, but its overall safety at the forefront as well.
In June, the nation celebrates National Safety Month. The National Safety Council promotes safety across industries. For over a century, the National Safety Council has been the leading nonprofit advocate for America’s safety. Their website provides resources and tools for a series of topics1 , which pose a lot of safety concerns. These concerns include falls, substance abuse, distracted walking, COVID-19, mental health, and even workplace violence. According to the NCS’s website, the construction industry was considered one of four of the most dangerous industries2 in 2020.
As we celebrate National Safety Month, it is also important to look into programs that could enhance and augment existing safety protocols, as well as build partnerships. One such program, the Voluntary Protection Programs (VPP), falls under the United States Department of Labor Occupational Safety and Health Administration (OSHA). The OSHA website states, the programs started originally in California over forty years ago as an experimental program, and, in 1982, it became an official program under OSHA. Further, federal worksites became eligible for the program in 1998.
“[The programs] recognize employers and workers in the private industry and federal agencies who have implemented effective safety and health management systems and maintain injury and illness rates below national Bureau of Labor Statistics averages for their respective industries,” it states on the VPP page on the OSHA website. The website adds, “Approval into VPP is OSHA’s official recognition of the outstanding efforts of employers and employees who have achieved exemplary occupational safety and health.”
The VPP website summarizes the programs’ call for an organization’s management and workers to work cooperatively with OSHA in promoting worksite safety through implementing safety and health management systems in the workplace. These systems are aimed at preventing fatalities, injuries, and illnesses while focused on “hazard prevention and control, worksite analysis, training, and management commitment and worker involvement,” Roger Forstner, OSHA Area Director stated.
Forstner added that participation is incumbent on an employers’ application submission to OSHA, and ‘a rigorous onsite evaluation by a team of safety and health professionals.’ He further stated that applicants represented by a bargaining unit require support from their respective union.
Forstner stated, “The main goal of safety and health programs is to prevent workplace injuries, illnesses, and deaths, as well as the suffering and financial hardship these events can cause for workers, their families, and employers.” A big part of prevention is being proactive - it should not have to come to an accident for protocols and systems to be reexamined or reimagined. The VPP prompts proactive steps in approaching a workplace’s safety and health rather than traditionally being reactive.
The VPP is focused on finding and fixing hazards before an injury or illness occurs, and it’s a far more effective approach. It starts with a basic program for an organization with simple goals to attain and grow. “If you focus on achieving goals, monitoring performance, and evaluating outcomes, your workplace can progress along the path to higher levels of safety and health achievement,” Forstner expressed.
The OSHA website presents the process in seeking approval with the VPP. There is performance-based criteria for the safety and health systems, an application process, and then OSHA would assess the applicants against their set criteria. This includes a review of applications and a ‘rigorous onsite evaluation’ by OSHA safety and health experts.
Forstner discussed how when the safety and health program is set, it should be assessed to verify if it is implemented as intended, and revisited every year so that employers can assess what is working and what isn’t, as well as whether or not the program is on track to achieve its goals. “Whenever these assessments identify opportunities to improve the program, employers, managers, and supervisors—in coordination with workers—should make adjustments and monitor how well the program performs as a result,” stated Forstner. He added how collaborative monitoring and discussion within the workplace, while also celebrating the successes, gives way to further improvement of the program overall.
There are three programs that OSHA approves, which include STAR, MERIT, and DEMONSTRATION, and are described below from the website directly. • “Star: Recognition for employers and employees who demonstrate exemplary achievement in the prevention and control of occupational safety and health hazards the development, implementation and continuous
improvement of their safety and health management system. • “Merit: Recognition for employers and employees who have developed and implemented good safety and health management systems but who must take additional steps to reach Star quality • “Demonstration: Recognition for employers and employees who operate effective safety and health management systems that differ from current VPP requirements. This program enables OSHA to test the efficacy of different approaches.”
Forstner shared how an average VPP worksite has a Days Away Restricted or Transferred (DART) case rate of 52-percent below the average for its industry, which speaks to the VPP’s success. The OSHA website defines the DART rate as one “that represents the total non-fatal injuries and illnesses resulting in days away from work, restricted work activity, and/or job/transfer per 100 full-time employees for a given period of time (usually 1 to 3 years).”
According to Forstner, worksites do not typically have such low rates starting out, but generally see them once they adopt and commit to the VPP approach toward safety and health management and its application process. “Fewer injuries and illnesses mean greater profits as workers’ compensation premiums and other costs plummet,” Forstner added. “Entire industries benefit as VPP sites evolve into models of excellence and influence practices industry-wide.”
Currently there is only ONE company in Guam that holds VPP certification - ECC. ECC is an employee-owned business founded in 1985 with offices in the United States, the United Kingdom, Italy, Germany, and our slice of paradise. Their company provides design-build, construction, environmental remediation, disaster response, energy, munitions response, and international development services to their government and commercial clientele throughout the globe according to their website3. According to EXO ESQ Manager Rich Mendenhall, “ECC started as an environmental company and built its business model from there.” He continued, “ECC has shown throughout its past 35 years that it is a premier company that focuses on the environment, which is integrated as a major component of our ESQ program.” ESQ stands for environment, safety, and quality, a tagline - more of an institution; concepts that are at the heart of their code of conduct - of ECC.
It is important to think and consider critically about what to base a company’s safety and health management systems on. As stated earlier, it also includes the collaboration of a company’s employees and management to manifest the goals of the company. Mendenhall shared several criteria that are vital to consider. “These [criteria] are all vital parts of an effective and efficient program that fosters a positive safety culture, which incorporates management support, accountability, empowerment, active engagement, and continual improvement,” Mendenhall asserted. Mendenhall, with the assistance of Kym Edelman, ECC Corporate Safety Director, pointed to having active, senior-level leadership engagement providing resources and support to promote a positive company culture. Additionally, when considering safety and health, there needs to be accountability and empowerment in a company. “Employees need to understand expectations, [be] held accountable for adhering to those expectations, empowered to take action if there is an issue, and most importantly, understand that our people are most important,” Mendenhall emphasized. “We must value each other, work together, and protect each other.”
In an industry that is continuously growing and expanding, it is important to have training when it comes to performing job duties and tasks with particular emphasis on those duties’ safety aspects. This means that every employee - from management to the field staff - has the tools necessary to perform their work without compromising safety and quality. “Training enables employees to understand when something is not as it should be, allowing them to report anything they see that might be an issue or concern, [and] facilitating prompt corrective action,” Mendenhall added.
This includes emergency preparedness training, which calls for a system of protocol, access to first-aid materials and emergency equipment in offices, worksites, and vehicles, CPR training, and open communication about safety issues or injuries on the job for tracking.
Mendenhall shared it is important to strive to be the safest place to work. “ECC believes that everyone deserves a place they can go to work where they feel is a safe environment to work and they will go home to see their families or loved ones the same way they left them that morning,” he started. This prompts a safety and quality system where high loss potential incidents and actual incidents are reported, and shared with the ESQ Staff and corporate management. “Once the potential and actual issue or incident is investigated it’s published and sent out to the entire ECC Employee staff so that everyone can benefit from the lessons learned and prevent reoccurrence.” All of this data is also tracked and reported, which helps refine protocols and procedures as a means to improve.
Safety also means that there is an open line of communication throughout; that concerns do not get muddied or the message does not get lost between sender and receiver. So is it part of the work culture at ECC, which Mendenhall stated encourages and expects employees and subcontractors to have an active role in participating in the safety program. “From the start every employee and subcontractor is provided an initial site safety briefing and expectation to stop work and report any safety issues they find without fear of reprisal from doing so,” he stated. There is also a system set in place for individuals to share safety or quality concerns of improvement electronically, or on forms to provide to management. “Suggestions and concerns are logged to be addressed by safety or quality”, and there is also an incentive program in place to share
It is important to note that part of communication within a company goes beyond just its employees and management, but also its subcontractors. This was actually a positive aspect of the VPP interview process for ECC, as subcontractors who were interviewed “stated they believed that ‘subcontractor’s working on the site felt like they were an integral part of the ECC team and not a subcontractor where several had stated they felt they could bring up safety issues to ECC staff without fear and had done so on several occasions. Subcontractors felt that when they brought up a concern, the staff acted to clear-up or rectify the issues right away, which proved they don’t just talk safety they mean it,’” shared Mendenhall. It is this open communication that lends to a safe environment to share concerns and enhance and augment the successes of all parties.
Forstner stated, “In roughly half a century, OSHA and our state partners, coupled with the efforts of employers, safety and health professionals, unions and advocates, have had a dramatic effect on workplace safety.” According to the United States Bureau of Labor Statistics’s Census of Fatal Occupational Injuries Summary of 20204, 4,764 workers died on the job in 2020 across industries. This is a 10.7-percent decrease from 2019 with 5,333 workers. According to Forstner, “About 20% (1,061) of worker fatalities in private industry in calendar year 2019 were in construction – accounting for one in five worker deaths for the year.” In 2020, the number of worker fatalities in construction was 1,008.
A safety and health management system can reduce compensation costs, absenteeism and insurance premiums, while increasing productivity according to Mendenhall, but the real benefit he says is, “an effective program shows you care about the people that work for you and that influences people’s decision to want to come work for your company.” That really is kind of what it comes down to; knowing that at the end of the day, when you leave the worksite, or the office, or wherever you spent the day earning your living - you were taken care of, that you and the people you work with are safe. That has to be what Maslow was talking about on some level.
1. https://www.nsc.org/workplace/safety-topics 2. https://injuryfacts.nsc.org/work/industry-incidence-rates/most-dangerous-industries/ 3. https://www.ecc.net/ecc/ 4. https://www.bls.gov/news.release/cfoi.nr0.htm
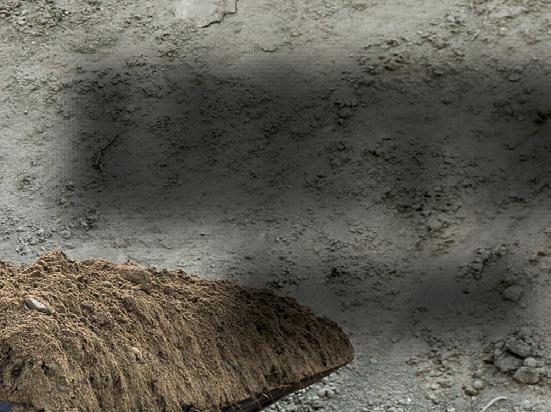
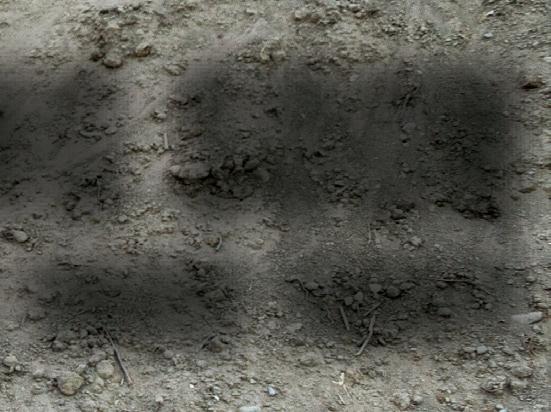