
3 minute read
Pade five-axis CNC solves production headache at Ideal & WRS Saddles
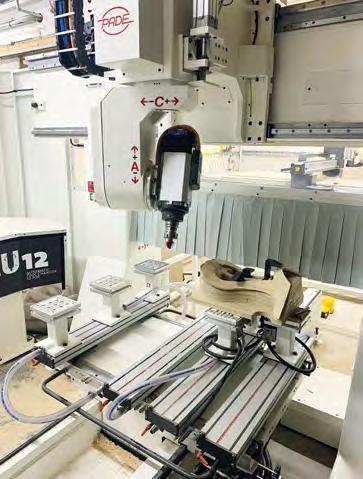
Walsall based Ideal & WRS Saddle Company is one of the world’s largest manufacturers of equestrian saddles which are constructed on a wooden saddle tree (frame). The company’s extensive range of saddles available are suitable for dressage, show jumping, eventing, showing styles or just leisure.
The way the saddles are made has changed little over the last 100 years or more meaning the various manufacturing process are very labour intensive. One of the key elements in the construction involves making the wooden subframe is the variability of different shapes and sizes that need to fit the shape and size of both riders and horses. These parts are made using laminated plywood and are known as the Saddle Tree and Cantle.
The Saddle Tree is pressed and shaped using an aluminium jig, and once this has been done it needs trimming to exact size which usually is done by hand. The Cantle is produced in part on a standard three-axis CNC machine, but certain areas of it still require finishing by hand. This ‘hand working’ is time consuming and requires a highly skilled person to do it.
As a result around 12 months ago the company started to research how they could produce these parts more efficiently and accurately and came to the conclusion a five-axis CNC Work Centre could be the solution.

After looking on line at several manufacturers they selected Pade as their first port of call as it appeared they had a good knowledge of machining complex shaped parts. Production Director James Hitchens picks up the story “We contacted Pade directly, who in turn put us in touch with their UK agent JJ Smith. Following an initial meeting to discuss our requirements, samples where sent over to Pade to review and test.
The results seemed very favourable and so a site visit to the Pade factory was set up for myself and work shop production managers Phil Parsons and Thomas Lugsdin together with Guy Stanley from JJ Smith.”
In the Pade showroom a demonstration machine was set up to produce various size Cantles and Trees as per the customer’s samples. In particular the clamping and precise referencing of the Trees was discussed at length, with the end result being a very simple yet effective clamping set up that Pade designed.
The model of machine that was specified was a Velox Solo ‘gantry style’ five-axis CNC, that due to space restrictions in the customers factory, had to be specially modified to fit.
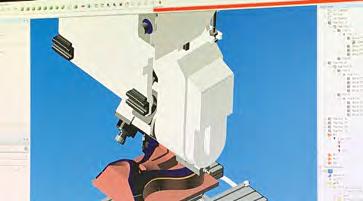
Although working with just one shuttle table – with the option to use vacuum or mechanical clamping – there was the choice to machine both Cantles and Trees at the same time, or selecting to produce a batch of the same parts.
The Velox was also specified up with a 12-position automatic rotary tool change, and for programming, the machine had the Pade E-LAB simulation and anti-collision software along with Alphacam Advanced 3D.
James comments: “From the moment we arrived at Pade we could tell they where a serious company who new their stuff and had a real can do attitude which was refreshing. The machines we looked at where extremely well engineered and we could tell would be up to the job.”
The Velox is just one of six different models of five-axis CNC machining centre that Pade produce for a wide range of complex shaped parts for furniture, construction, garden products, packaging to name but a few.
Once James and his team returned to the UK an order was placed and the machine was delivered and installed on schedule.
Phil Parsons commented: “The whole delivery and installation process was expertly organised and went without a hitch.
For software training and machine operation this was split into three days at the Pade factory and three days at our factory, and I have to say the technicians from Pade and JJ Smith did an excellent job”.
Guy Stanley from JJ Smith adds “This was a very interesting project to work on and one that initially had some challenges. But with close dialogue with Pade and the customer, the end result is a machine that will significantly help increase both production output and accuracy. In addition, it has been a real pleasure to work with the Ideal WRS team who from the outset had a very positive outlook and open to new ways of thinking.”
0151 548 9000 sales@jjsmith.co.uk www.jjsmith.co.uk