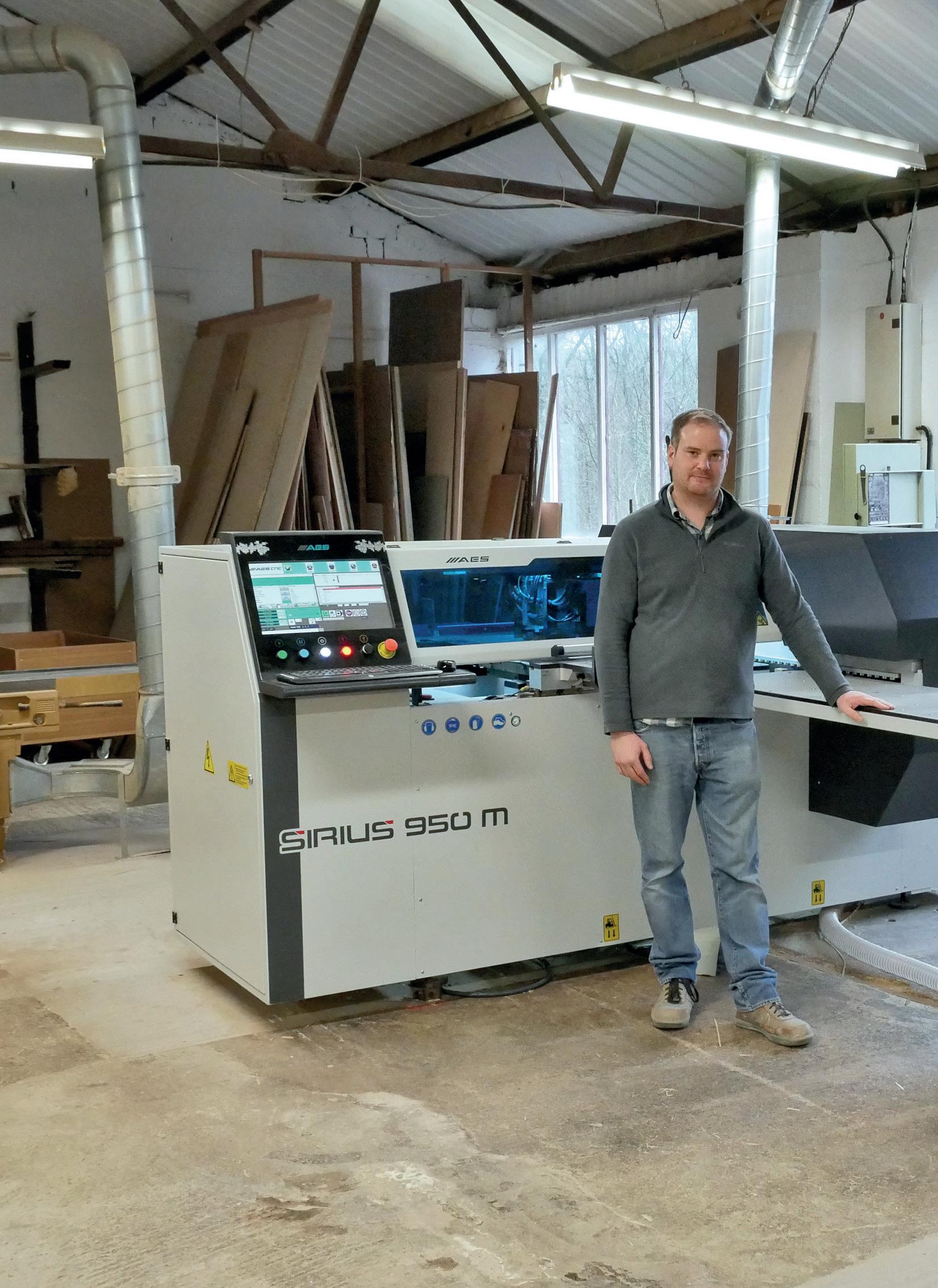
23 minute read
Installations
With a reputation for quality work, but somewhat held back by its tired production set-up, TaylorMade by Stanton took the plunge with a new CNC drill, which has proved a revelation for the Gloucester business – John Legg paid the company a visit …
Improving production efficiency and design capability, the easy way
Based in Longhope, Gloucester, TaylorMade by Stanton is a highly reputed manufacturer of high-quality bespoke interiors and kitchen, bedroom and home office furniture. Since June 2000, the company’s designs have always been composed of top-quality materials, appliances and worktops, in order to give its customers a true tailor-made service with quality at the forefront and an attention to detail that is second-to-none.
The company’s showroom is impressive, and features a choice of fully-built designs which demonstrate the company’s dexterous capabilities to the full – from clean and classic upscale Shaker-style options through curving counters and statement lacquered cabinetry styles, to cool, urban contemporary chic – it’s clear partners Jeremy Stanton and Tom Hancock know their onions.
However, despite initial investment in the business running only to mainly used machinery – much of which is still functioning as intended – TaylorMade has built a healthy business based on delivering a quality product.
To achieve such a prime finish with very simple machines, the workshop team laboured with countless jigs and manual benchwork and drilling operations, which was naturally time-consuming and occasionally lacked the precision needed, and in turn led to reworkings in order to pass muster.
To help the business achieve greater efficiency, partners Jeremy and Tom researched the market for a solution, and found it in the shape of a compact AES Sirius 950M CNC drilling machine, which, at the time of my visit, had already helped their process significantly.
AES’ recently introduced Sirius CNC point-topoint boring machine is a well-made, heavyduty machine, weighing almost 1.5 tons – this heft comes in handy, with the X and Y axis able to move at speeds of up to 70m/min. Even the largest panels are loaded and move through the machine with ease, thanks to the air floatation tables which are firmly held for positioning by the pneumatic gripper.
The machine has a generous 950mm working width and is equipped with 10 vertical drills, drilling from below to ensure the working surface and all holes are kept dust-free. It also has the benefit of increased accuracy, as the drilling depth will always be correct, despite any tolerances in the thickness of the workpiece.
The machine also comes equipped with horizontal drilling to all four sides and a grooving saw in the X axis, making it an ideal all-rounder
The machine has a large, industrial-based, 17in colour Windows-based PC, with both USB and remote file transfer.
With the addition of the optional router head, various tasks can be easily resolved – such as grooving for solid backs on carcasses, routing out for cable management, pipes or skirtings, shaping for corner units, and so on.
The further option of the automatic toolchanger improves efficiency where multiple tools are needed, and expands the possibilities yet further.
The J & C O’Meara-supplied product was set up by its regional agent, Southampton-based Sawtec. Regarding the installation of the Sirius, Tom Hancock reports that it went very well, overcoming an initial hard-drive issue very professionally.
After the commissioning and initial training, Tom described the Sirius as a revelation: “After training, even when getting used to it, we got up to speed quite quickly and were making all types of semi-finished furniture parts pretty much straight away.
“It has also allowed us to do things which would have otherwise have been a real head-scratcher. To be honest, I never knew machines like this, at this price, actually existed. It’s brilliant!”
In terms of design potential, the addition of the Sirius is a positive move. Tom quickly realised how the AES Sirius drill is helping the company become more consistently efficient from a production perspective, and also how it has enabled Jeremy’s designs to be more sophisticated when the need arises.
In conclusion, with such a modest investment, the AES Sirius 950M CNC point-to-point boring machine is proving transformational for TaylorMade by Stanton – so much so, the partners are already talking of further investment very soon.
01704 893109 www.ukwoodworkingmachinery.co.uk
Taylor Made Joinery investing in the future with Homag UK
Established in 1981 by James Taylor, Taylor Made Joinery Interiors (TMJ) began trading from a 1500ft2 barn at Newberry Farm in Suffolk. The company manufactured the domestic joinery for GA Taylor Builders, James’ father’s construction company.
The Sawteq B-300 Beam Saw is coupled with the Storeteq S-200 at Taylor Made Joinery Interiors
During the 1990s TMJ moved into a purposebuilt 36,000ft2 works and completed its most prestigious project to date – the refurbishment of 10 Downing Street. Since then, it has completed many notable projects including restoring the Private Chapel at Windsor Castle after the devastating fire in 1992, the Royal Opera House refurbishment of the main auditorium, the £5.5m Royal Festival Hall project and the London 2012 Olympics project, worth £7.5m.
In 2018 the directors of the business could see that the work the business was handling was changing. “There was an increasing demand for cabinetry units,” explains founder and MD, James Taylor. “To accommodate this change, we realised we would need to increase our production to remain competitive in the market.
A major investment
“Rather than opting for a short-term fix, we decided the time was right to make a major investment in the future of the business. We wanted to automate large swathes of our production process to give us a significant competitive advantage.
“So began a thorough market evaluation. We looked at where the market was and where we thought it was heading. We evaluated our main competitors to understand their strengths and weaknesses, and we looked at what new machinery and software were available to automate our production processes.
“Following this, we predicted what we thought the needs of the business would be over the next five years – all of which was done prior to Covid-19, of course.
“Perhaps the biggest commitment we made was to invest in Homag’s automated storage and retrieval system, the Storeteq S-200, along with the Sawteq B-300. Although this machinery itself was a major investment, the overall outlay was much greater. Accommodating this new equipment into our operation meant a £750,000 project for the construction of a new 13,000ft2 building, which required the demolition of part of the existing site.
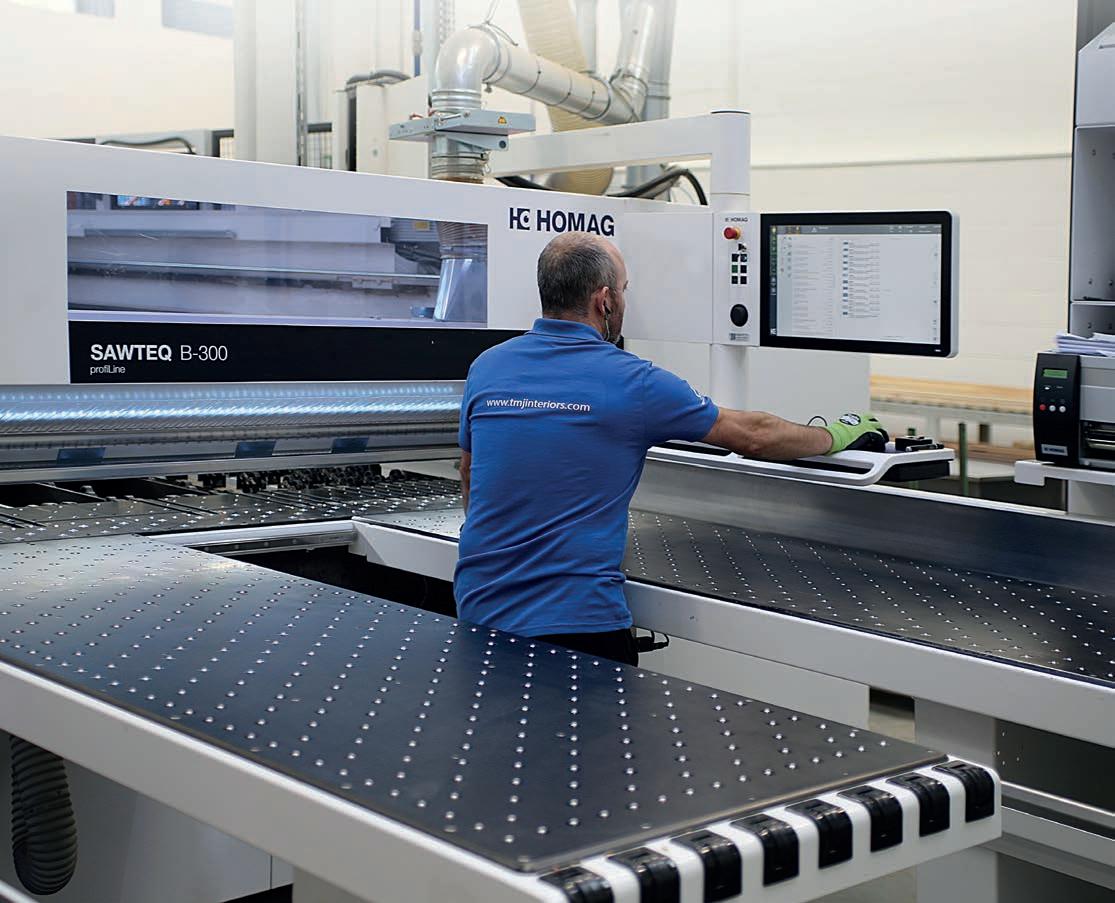
Partnering with Homag UK
“The decision to procure the Storeteq S-200 with the Sawteq B-300 was part of a package of equipment that we eventually purchased from Homag UK. The process of finding the right partner for this equipment began with looking through the various trade magazines and going
to the trade fairs in Germany and the UK.
“Once we had completed our initial research we contacted Charles Smith, our Homag UK area manager. We have known Charles for many years, and during this time have built a strong and trusting relationship with him. His knowledge and experience of the industry are second-tonone, and he really understands our business.
“He listened to our goals and then helped us put together a package of machinery and software that would deliver what we were looking for. Charles was able to bring to the party not only his extensive experience, but also the knowledge of successful solutions his other clients have implemented.
“From our side, we wanted to specify machines with a little bit of extra flexibility to cope with the changes in demand that often occur in the market. Whilst we’re doing a lot of cabinetry work at the moment, we need to have the ability to handle more solid joinery jobs and work with other materials when the need arises.
“Together we were able to draw up a list of equipment that included a Drillteq V-500 vertical CNC, the Sawteq B-300 beam saw coupled with the Storeteq S-200 automatic storage and retrieval system, a Loopteq O-300 automatic return system for our airTec edgebander, and a Centateq P-210 five-axis CNC router. We also invested in the MagiCut software to maximise the potential of the beam saw.
“Before committing to the machinery, Charles arranged for us to visit various UK manufacturers who had similar models. Seeing the machines out in the field working on real jobs is very important to us.
“It’s all about engaging our workforce in the procurement process. So when we visited these sites we took some of our operators along with us. This gave them the opportunity to talk to fellow operators in other businesses – not only to understand how the machines perform, but also to learn new techniques and production ideas that could potentially benefit our business.
Setting up the new facility
“Back in 2013 we were one of the first companies to invest in the Homag BHX 200 vertical drilling CNC. Since then, we have experienced exceptional business growth, and a bottleneck had emerged in the production of cabinets – specifically regarding the jointing process.
“Consequently, the first of the new machines to be installed in February 2019 was Homag’s Drillteq V-500. Previously, we used to ‘biscuit’ the joints for cabinets and carcasses – this was done on the bench by hand. It was, however, a slow and far-from-satisfactory process which involved a fair amount of finger crossing when it came to lining up the holes and making the joint flush!
“The Drillteq V-500 has changed all this – it not only drills the holes accurately and quickly, but it also delivers a +50% improvement in timesaving as it automatically inserts the dowels, consistently producing stronger joints with absolute accuracy.
“The Storeteq S-200 with the Sawteq B-300 was perhaps the most significant part of our plan. The installation of this automated storage and retrieval system was critical, and I have to take my hat off to the professionalism of Homag’s installation team. The complex process took time, but the install went very smoothly, and I would like to pay tribute to one particular Homag engineer, Gordon Mackenzie, who was so accommodating throughout the process.
“This technologically advanced system has revolutionised our business. It gives us the ability to increase our production capacity by at least +20%. We can load the sheet material in the daytime, select and prepare the panels in the evening whilst the factory is shut, then cut them when the shift arrives in the morning before sending the workpieces straight to the edgebander and the CNC machines.
“It makes the most of the whole day, not just the normal working hours, and it’s given us options. Previously, a lot of the panels were subbed out for cutting – but now we can handle all of the work in-house so we control everything, especially the quality. And of course, we save on transport, handling and sub-contractor fees, too.

Establishing a door and door-frame cell
“Our new Centateq P-210 CNC was purchased to manufacture our doors and door frames. Again, previously a lot of our door packages were subbed out, but in the last month we’ve made around 400 door sets within the factory, so that’s given us yet another competitive advantage.
“We can now diversify into different products as well. So we are able to target new markets where previously we wouldn’t have been able to compete. For example, we are now competitive in both the hotel fit-out and laboratory markets.
“Our reasons for partnering with Homag are numerous. Over the years a real trust has built between our two companies. This has been cemented by Charles Smith, whose input and professionalism we value highly. The German parent company not only designs and produces innovative, easy-to-operate machinery with a robust build-quality, but it also develops firstclass software and control systems.
“All this is backed up by an extensive network of engineers in the UK who support and service us when the need arises. Financially, the Homag solution works well too – we expect to achieve a return on our recent investments within four years.
The Drillteq V-500 Vertical CNC has delivered a +50% improvement in time-saving for TMJ

“In June this year we added another Homag Drillteq V-500, this time with an automatic return system. This was purchased to handle the increasing amount of repeat business we get.
“Our turnover for this year will be around £36m. However, with recent investments in Homag machinery and software, we will see this grow to over £50m within a few years, despite the Covid-19 pandemic.
“The automated solutions from Homag have helped us operate safely throughout these unprecedented times. We have established a two-shift working pattern with a one-hour gap between shifts to allow for cleaning down.
“It would be remiss of me not to mention our own workforce, whose flexibility and dedication in these challenging conditions have, in no small measure, been responsible for us being able to maintain our production levels,” concludes James.
For a demonstration, or more information on any of Homag’s machines or software, contact Adele Hunt at Homag UK on 01332 856424.
www.homag.com
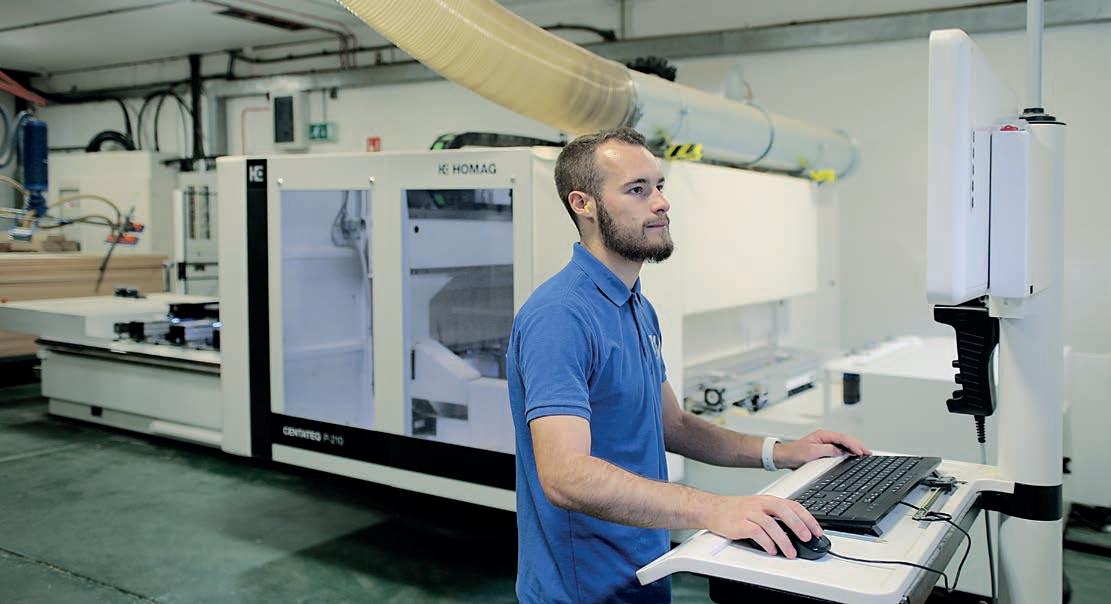


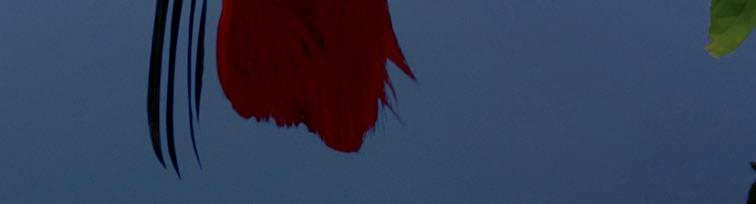



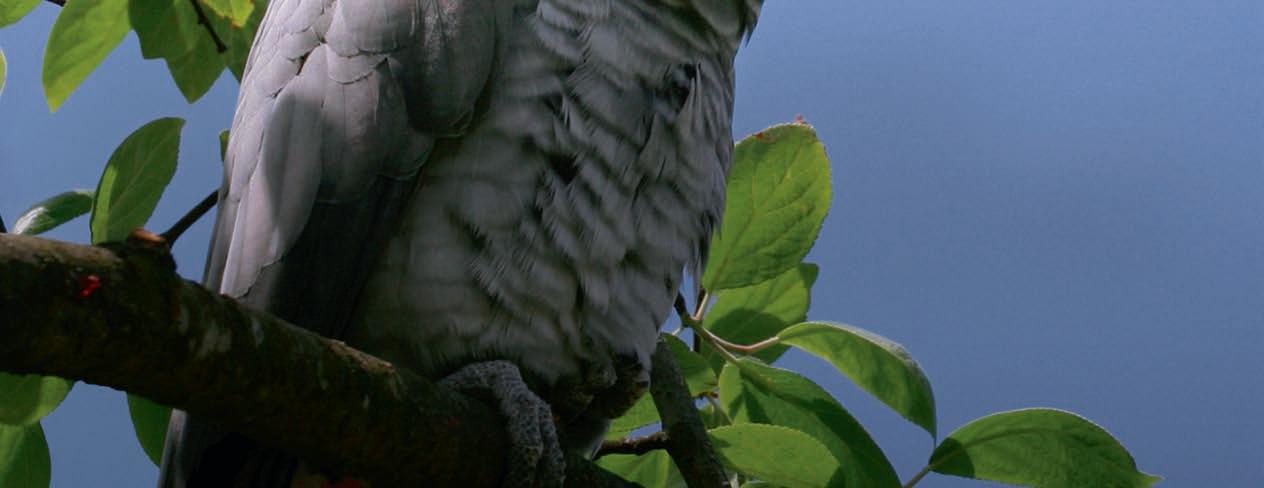

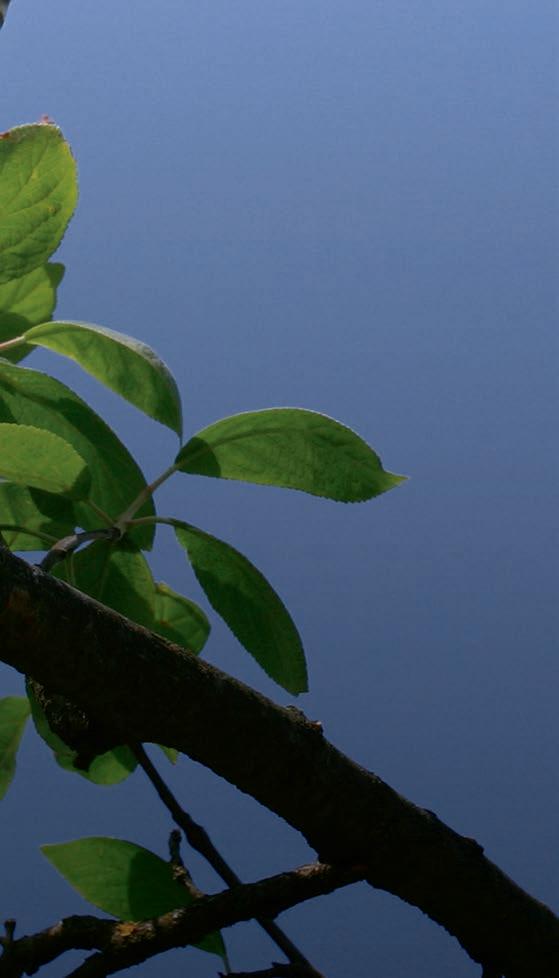
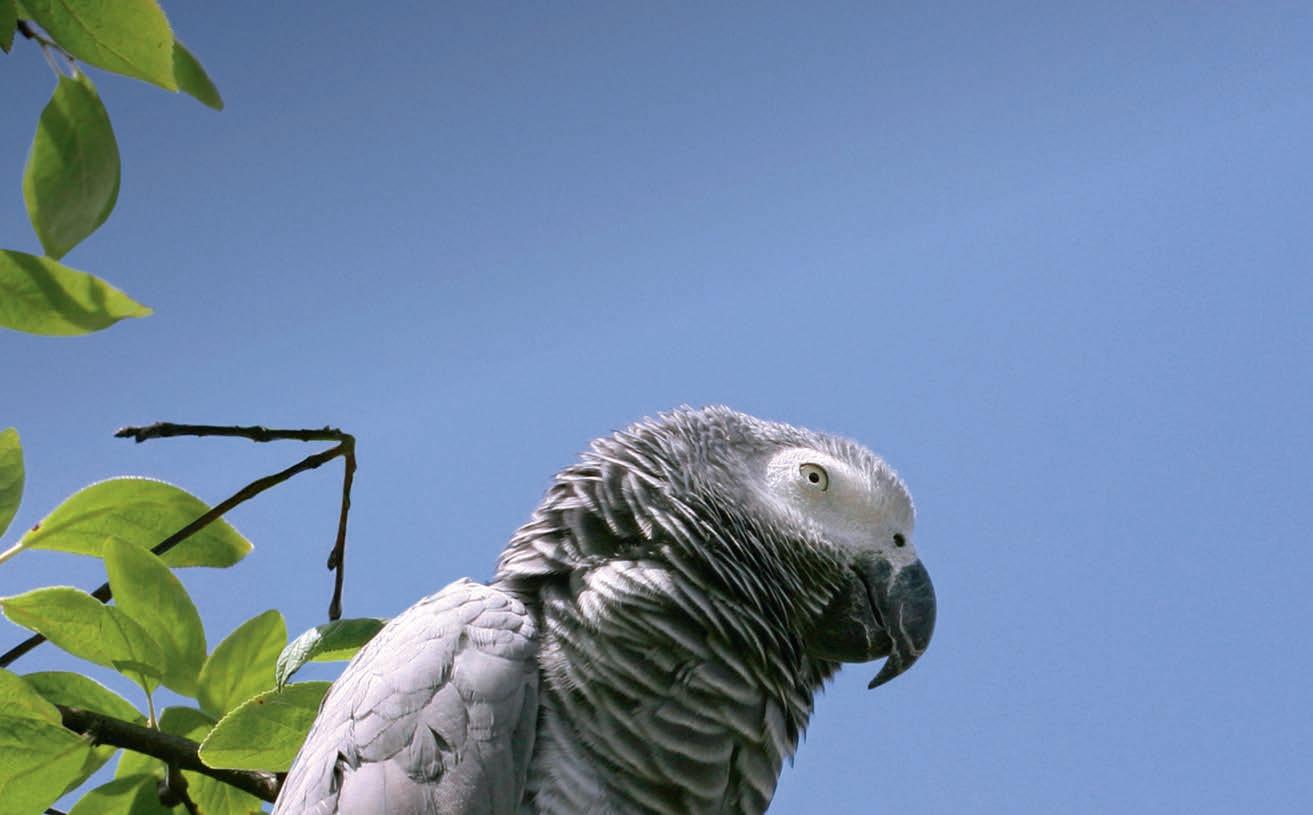
Surfacing & Decorative Panels
A truly great design is one that stands out from the crowd. Kronospan urges the industry to grab attention with its Kollection range, 63 on-trend decors from the panel product industry leader, with 18 brand-new decors added for 2020. Each decor is designed by Kronospan and exclusively copyrighted, and offered in 18mm MFC with matching laminates and edging available. Best of all, every single decor is in stock and available for next-day delivery from distribution titan, Lawcris.
63 one-of-a-kind decors – including 18 new releases – from Kronospan and Lawcris

Drawing inspiration from four cities across Europe, the brand-new decors for 2020 are another step in Kronospan’s decor development journey. Responding to market demand for contemporary, urban design, and reflecting the varied influences on the evolution of the urban environment, the range aims to encapsulate the spirit of four modern cities: bohemian Barcelona, where industrial meets artisanal; sophisticated Milan, hub of European fashion; contemporary Moscow, where tradition meets rapid modernisation, and dynamic Warsaw, a rising star of Europe’s design sphere.
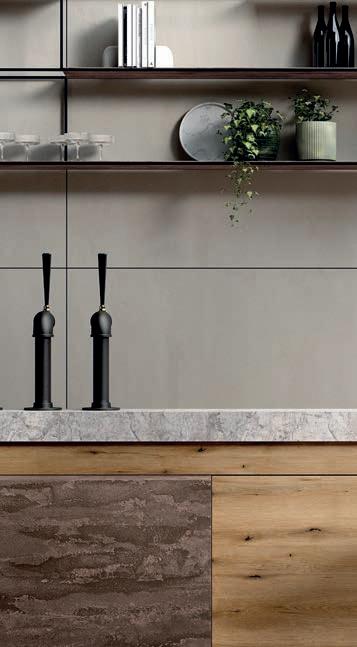
The result of this research and inspiration is a collection of decors that embraces the latest trends, each working harmoniously together to create “exemplary design opportunities”, says Kronospan.
The new decors exude character and charm, with more realistic colouration and feel than ever before. Embracing the flourishing trend for industrial materials, the Kollection’s Flow decors celebrate the raw beauty of metal and concrete textures in hues that range from the chalky Silk Flow (K349) to the moody Charcoal Flow (K353). Rusty Flow (K351), meanwhile, incorporates rich, reddish-brown hues, emulating the exquisite imperfection of oxidised iron.
The new Kollection decors also include five distinct woodgrain groups, offering opportunity for emotion-evoking design, with each family expressing a unique personality. The rustic, reclaimed look of the Grange Oak series sits alongside the soft, hazy grain of the Aurora Elms, while the Castello and Harbor Oaks emulate live-sawn wood in contemporary tones, inspiring a wide variety of design interpretation.
These exclusive Kollection decors can be mixed and matched to create original designs that really stand out from the crowd. All 63 MFC decors are in stock at Lawcris, ready for nextday delivery.
www.lawcris.co.uk
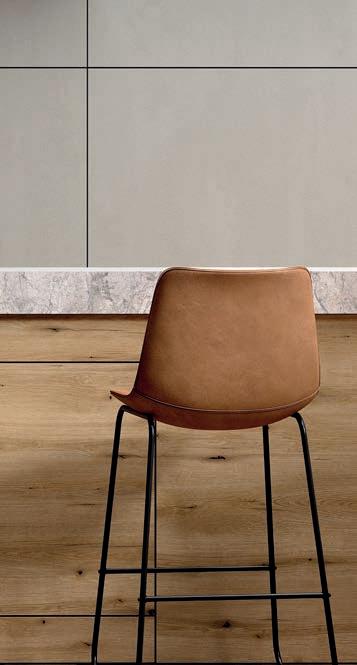
Take a good look around. Whether at home, work or play, there is a good chance there is a Decorative Panels product nearby.
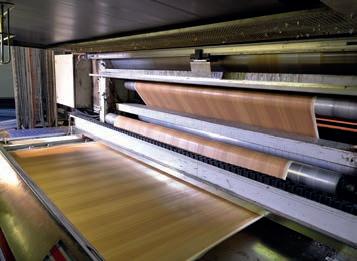
Decorative Panels Lamination is proud to one of be Europe’s leading suppliers of decorativefaced sheet materials. The passion the team clearly feels for the company and industry has opened doors to the innovative approach and high-performance products on offer.
Partnering with Addmaster (UK), which helped pioneer the use of antimicrobial additives with its Biomaster product range, Decorative Panels can offer products with surfaces that are able to inhibit the growth of bacteria by up to 99.99%.
Decorative Panels has offered antimicrobial products within its portfolio for over eight years, but now, as can be imagined, the interest for these has accelerated.
To cater for this demand, a much wider offering than before will be rolled out across all of the dp-group companies using sheet materials and edgebanding, which will offer the highest possible product protection, independently tested to ISO 22196.
It is universally acknowledged that the beauty lies in the detail, and, as a trade laminator of sheet materials for the furniture and allied industries, Decorative Panels Lamination can offer an extensive range of surface designs incorporating Biomaster technology laminated to many different substrates.
These substrates can then be converted – either in-house at sister companies dp-furniture and dp-components, or externally to fellow manufacturers in many different market areas.
Based on silver ion technology, long recognised to have no harmful effects, Biomaster is already extensively used in medical, food and water applications. Biomaster antimicrobial additives are registered with the Biocidal Products Regulation (BPR) and the Food and Drug Administration, and approved by the Environmental Protection Agency (EPA).
When bacteria comes into contact with a Biomaster-protected surface, the silver ions prevent the bacteria from growing, producing energy or replicating, and they die.
The potential areas of application for such products are, as can be imagined, vast, and not limited to the healthcare environment. With all areas of everyday life now demanding increased levels of hygiene, Decorative Panels utilising Biomaster antimicrobial finishes provides a protective solution that never degrades.
Unlike some antimicrobial agents, Biomaster is incredibly durable, long lasting and highly active. When added, it is dispersed throughout the entire item and becomes an integral part of the product.
But how long does the protection last? The answer for Decorative Panels, using Biomaster additive for many years, is 24/7, for the lifetime of the product. It contains built-in antimicrobial product protection that does not wear off or leach out.
Decorative Panels Lamination produces over 300,000m2 of the highest-quality laminated products each week. Having pioneered the use of lightweight paper foils as decorative overlays in the UK, dp-lamination now has one of the largest and most diverse portfolios of decor materials in the UK.
Surface finishes range from woodgrain paper foil veneers through to high gloss and matt acrylics under the brands of dp-decor and dpspecialist, as well as an ever-expanding portfolio of unique and diverse surface solutions under the brand of dp-limitless.
With the dp-decor range from Decorative Panels Lamination, users can discover high levels of design realism. This collection promises to inspire no matter the ambition, no matter the challenge.
Drawing from an extensive range of stock finishes, design exclusivity is also available, ensuring that the beauty of dp-lamination products can satisfy every customer’s demands.
Products are available without commitment to bulk quantities, and deliverable from single sheets up to full loads. Just choose the decor and specify the substrate, and Decorative Panels will laminate it.
Together with Biomaster, Decorative Panels Lamination is ready to clean up in the marketplace.
www.decorativepanels.co.uk
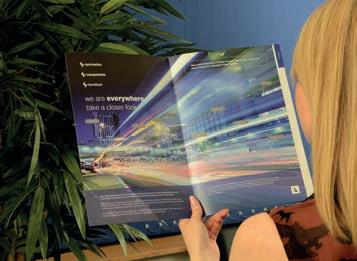
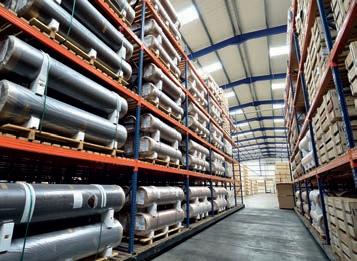
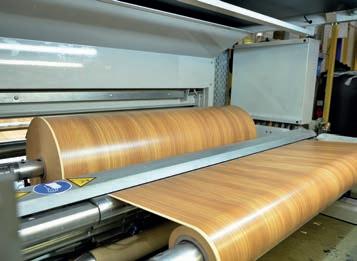
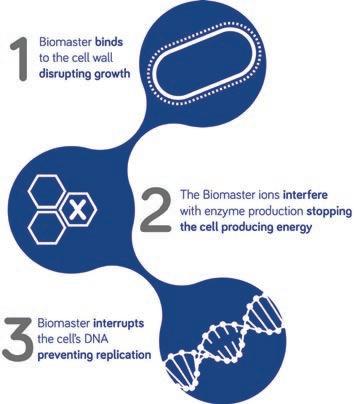
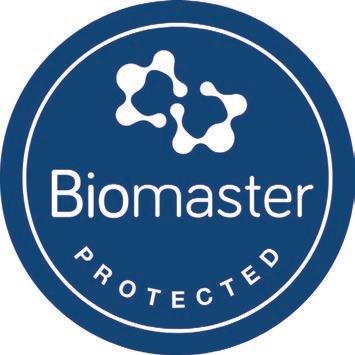

I N T E R V I E W
Graham Buchan
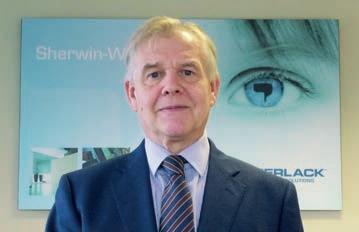
Commercial Director, West Region, EMEAI, The Sherwin-Williams Company
For the uninitiated, please introduce the Sherwin-Williams business.
Sherwin-Williams is a US multinational group, with its headquarters in Cleveland, Ohio. With sales of nearly $18b, and over 60,000 employees in 2019, it is one of the largest paint and coatings business in the world. The group is organised into three sales divisions – Paint Stores, Consumer Brands and Performance Coatings. The latter division is focused on industrial coatings, supplying the automotive, general industrial, packaging, protective and marine, coil and industrial wood segments.
Sherwin-Williams UK Coatings Ltd, based at Knottingley, West Yorkshire, is the UK headquarters for our industrial wood coatings business.
Whilst some readers may not be familiar with the Sherwin-Williams name, the roots of the industrial wood coatings business go back many decades, and the company is a combination of previous businesses such as Becker Acroma, Granyte and Hickson.
Sherwin-Williams is well known for its consumer brands – Valspar, Ronseal and others. Please summarise its key options for the UK furniture, joinery and carpentry trades
Sherwin-Williams’ consumer brands such as Valspar and Ronseal are justifiably well known, but the Sherwin-Williams’ industrial business is an important player in its respective markets, and Sherwin-Williams UK is a key supplier to the industrial wood sector, where we provide leading-edge coatings solutions to some of the country’s largest manufacturers producing kitchens, exterior windows and both exterior and interior doors, architectural mouldings and furniture, plus shopfitters and a host of more specialised industries such as luxury yachts, audio, musical instruments, and more.
Additionally working with long-established distribution partners, the business also reaches SMEs operating in sectors such as joinery/ carpentry, shopfitting, hospitality, etc.”
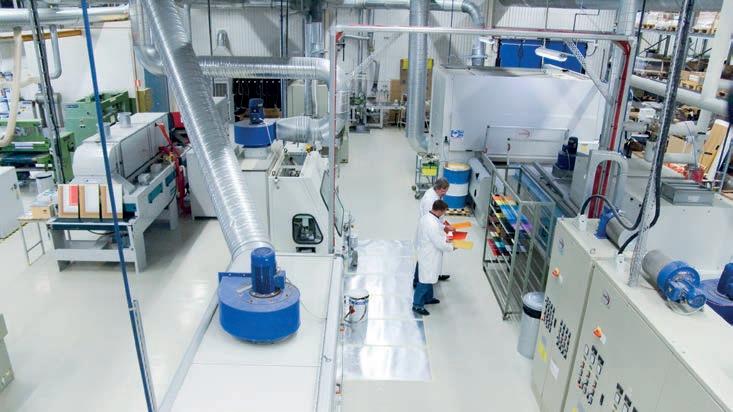
What are the strengths of Sherwin-Williams?
Sherwin-Williams, as part of our European organisation, is uniquely able to draw on the strengths of both its Swedish and Italian laboratories and, through this access to both northern and southern Industrial wood coating technologies, is able to provide effective, lowcost and high-quality solutions to any user requirement. Additionally, at our Knottingley base, Sherwin-Williams UK is able to adjust products to fit the needs of the most exacting customer – this is particularly important due to the growing demand for fast and highly precise volume colours.
Another winning feature is the depth of experience in our great team, and that SherwinWilliams offers a large and very experienced team of field technicians in the UK Industrial wood coatings market.
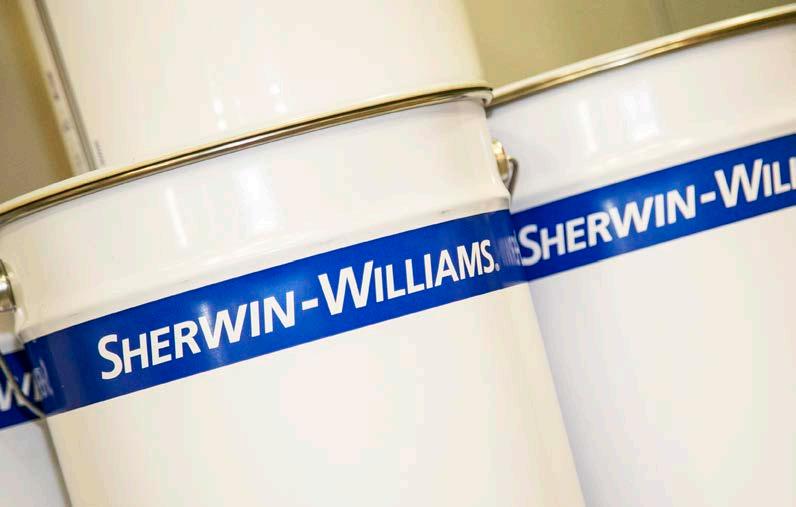
What makes Sherwin-Williams’ product range stand out? What are the key benefits for users?
As outlined above, the product range is uniquely wide in combining the best leading-edge technology from both the north and south of Europe. The range includes, of course, traditional ‘northern’ products such as Pre-Cat and A/C, as well as standard ‘southern’ technologies such as polyurethane and polyester. But SherwinWilliams’ range is considered highly innovative because of its strength in ‘green’ solutions such as waterborne (both for interior and exterior), UV/IR cure and even powder coatings for wood.
Another important aspect of our business is the strength of the two key brands of SherwinWilliams UK – Sherwin-Williams and Sayerlack – which are sold with pride by our distributors, with full support from our UK team. ››
Describe a typical Sherwin-Williams furniture trade customer – what are the benefits of working with Sherwin-Williams?
Of course, there is no such thing as a typical customer, and that is what makes our job always so stimulating! If a large manufacturer has a specific requirement – it may be that they are looking to reduce their VOC emissions, or increase the efficiency of their production lines, or improve the finish they are achieving on their products, or achieve a better colour consistency across their production, or to change their line configuration and application process – then we are able to provide them all the technical support and products which they will need.
The customer will, of course, benefit from the depth of knowledge of the Sherwin-Williams local team, but we are able to go way beyond this, and work in close conjunction with our Swedish and Italian colleagues to provide the most innovative and cost-effective solutions adapted to the specific requirements of our customers.
We are also able at our Swedish and Italian labs and technical centres to run large-scale trials of systems so that our customers can evaluate the performance without having to interrupt their own production.
Discuss one of your halo products, and explain why it stands out from its peers
One of the features of the Sherwin-Williams industrial wood coatings organisation is that new products are constantly being launched on the market, which is excellent news, both for our customers and for our distribution partners.
There is a lot of work in many areas at the moment – for example, in exterior coatings systems, fire-retardant product, bio-renewable products such as Excimer UV, powder for wood … the list goes on and on. So there are a great many to choose from.
However, if I had to identify one area of particular interest, I’d highlight that we continue to work closely with customers in the interior furniture market - and especially kitchens – to develop new products that provide a combination of durability and stain resistance with a truly excellent finish and feel, as well as delivering significant improvements in VOC emissions and in the working environment for our customers.
Can you tell us about current and future developments?
Like many businesses, our main focus at present is on maintaining a high level of service and supply to our customers whilst keeping them and our own employees safe during the Covid pandemic. We remained open throughout the first lockdown, and we expect to do the same in the coming months.
Brexit is another matter high on our priorities at the moment and, despite the many continuing uncertainties, we are trying to plan as extensively as possible to ensure an excellent continuity of supply and service. Looking further ahead, in 2021 we plan to recommence the growth strategy which has
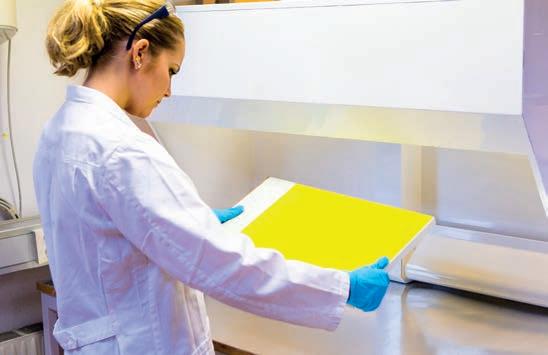
worked so well in recent years. We will be launching new products which we expect will strengthen our position in markets such as exterior joinery, interior mouldings and kitchens, whilst also looking for new market segments where we can grow.
Whatever challenges lie ahead in 2021 and beyond, Sherwin-Williams and our UK team are committed to supporting our customers with continued innovations, especially in the area of environmentally compatible coatings systems, as well as industry-leading service, where our Knottingley facility operates as the local connection to our research and development teams across Europe and around the world.
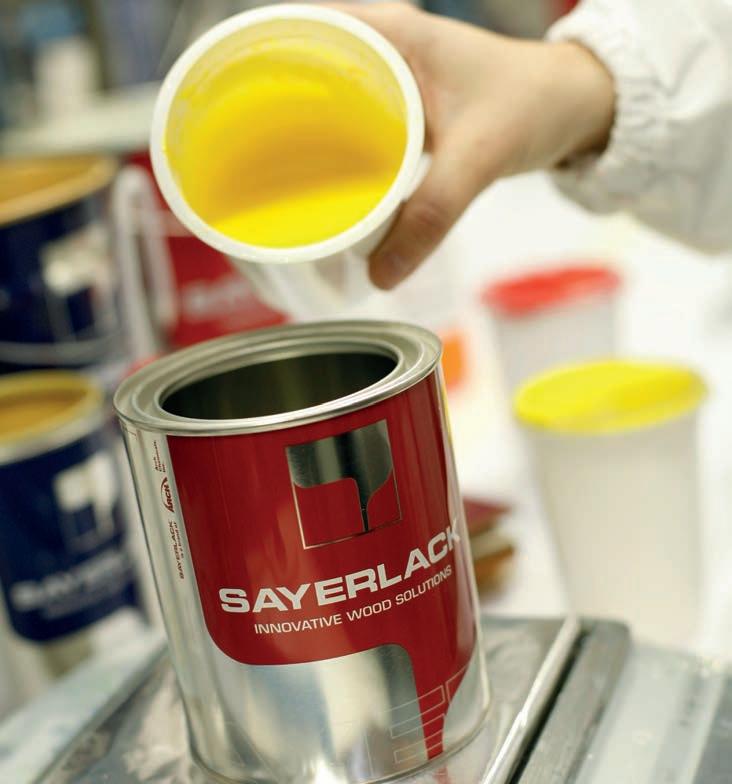
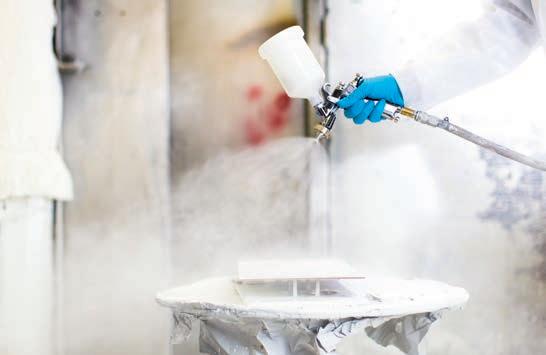