
18 minute read
News
Montgomery Group, the organiser of W Exhibition, the UK’s flagship event for the manufacturing and joinery industries, has revealed unprecedented levels of visitor appetite for its 6-9th February, 2022 show.
When the W Exhibition opens its doors at the NEC next February, it is anticipating record levels of visitor numbers as it brings the industry back together for the first time since 2018.
Visitor registration figures are tracking at more than 250% above the numbers for the same point in the campaign for 2018. Montgomery has also observed a broadening of the types of people who have registered to visit the exhibition, with over 500 registering in one week alone in September.
The top job function for those who have pre-registered to visit the event include joiners, furniture manufacturers, cabinet makers, carpenters and buyers. The broad mixture of categories spans right through to fitters, CAD designers and retailers.
Furniture manufacturing (18.85%) remains the top of pre-registered visitors’ main company activity, closely followed by cabinet makers (13.63%), joiners (12.83%) and general woodworkers (12.83). Door, window, staircase and kitchen manufacturers also feature prominently amongst visitors with circa 10% citing these as primary business activities.
Whilst machinery (13.19%) is a key area of interest for those who have registered to visit the show, this features comparatively to tooling (10.63%), timber boards and materials (10.08%), finishing products (9.97%), fittings and fixtures (8.75%) … all indicating that visitors are seeking a broad mixture of products and not just running machinery as previous figures might have indicated.
The W Exhibition typically attracts 10,000 visitors across the four days of the show. A large proportion of those who have registered to visit are budget holders, with over 20% of these holding a purchasing authority of circa £50,000.
Speaking about the encouraging visitor data, W Exhibition managing director, Nickie West comments: “It’s hugely encouraging to see such strong appetite for the W Exhibition, as reflected in the high number of visitors who have pre-registered much earlier in our campaign. With no industry event since 2018, it’s time to get back together and reconnect.
“I’m always eager to dig deeper into our visitor data and have been encouraged by the breadth of interest we have received from various job functions. But what I am most excited to see within the data is the broadening breadth of the areas of interest from our pre registered visitors. It’s far from being isolated to just the big running machinery that people want to see – which has traditionally been viewed as the sole attraction, whilst still showing as a significant pull – there is a new and growing appetite for tooling, timber boards and materials, finishing products and fittings.
“Historically, the W Exhibition has been dominated by a small number of large brands occupying lots of space on the show floor. However, this model has often left visitors with fewer opportunities to see new and emerging brands who arguably have just as much to offer. We’ve been working hard to address the balance between the brands that are exhibiting – alongside the brand leaders, our visitors can expect to see lots of new and exciting companies who will be making their W Exhibition debuts.
“After an extended period of restricted face-to-face business we hope that the entire industry will share in our enthusiasm at getting back to doing what we do best. The W Exhibition & Elements is the UK’s flagship event for the joinery and furniture making industry and we are excited to showcase all of the latest products and machinery when we return in February 2022.”
The W Exhibition has over 40 years of heritage, and continues to grow. It will return to the NEC for its biennial four-day showcase from 6-9th February 2022. The show brings together some of the world’s leading suppliers of woodworking machinery, materials and tooling.
W Exhibition managing director, Nickie West ‘It’s far from being isolated to just the big running machinery that people want to see – there is a new and growing appetite for tooling, timber boards and materials, finishing products and fittings’
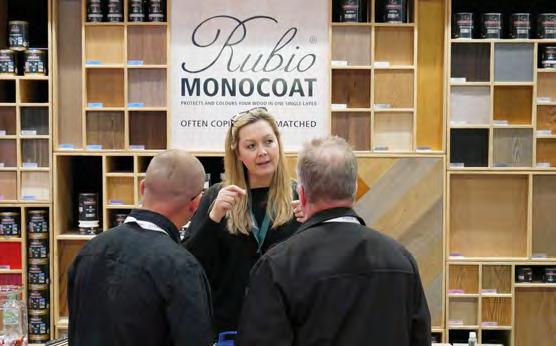
New dates announced for BFM webinars
Imports, insurance and social media are on the agenda for the autumn webinar series hosted by British Furniture Manufacturers (BFM).
Experts from chartered accountant Rayner Essex, business insurance broker Premierline and social media strategist Fraggleworks will give online seminars to the furniture trade in October and November.
On Wednesday, 6th October, Rayner Essex will deliver a webinar around doing business with the EU and NI post Brexit, including importing and exporting goods, import duty and the Import One Stop Show (IOSS).
Premierline will discuss the diverse insurance needs of businesses and the importance of securing the correct cover at a webinar on Tuesday, 19th October, while Holly Whittles from Fraggleworks will cover social media channels, strategy and content at a webinar on Thursday, 11th November.
The webinars continue a series of free online events which launched last month with sessions from Reddie & Grose, Fox Williams and the Furniture and Home Improvement Ombudsman service.
BFM MD Nick Garratt says: “The BFM webinars are a useful way for members and the trade to access expertise on subjects that are meaningful to the running of their business. We are grateful to our partners for sharing their insight, experience and knowledge.”
Each webinar will last between 30-90 mins, with an opportunity to ask questions at the end. The sessions are free, and the trade can book a place online at Furniture Manufacturers Events | Furniture Shows, Fabric Shows (bfm.org.uk).
As well as booking details, this online area lists all upcoming webinars from the BFM.
www.bfm.org.uk
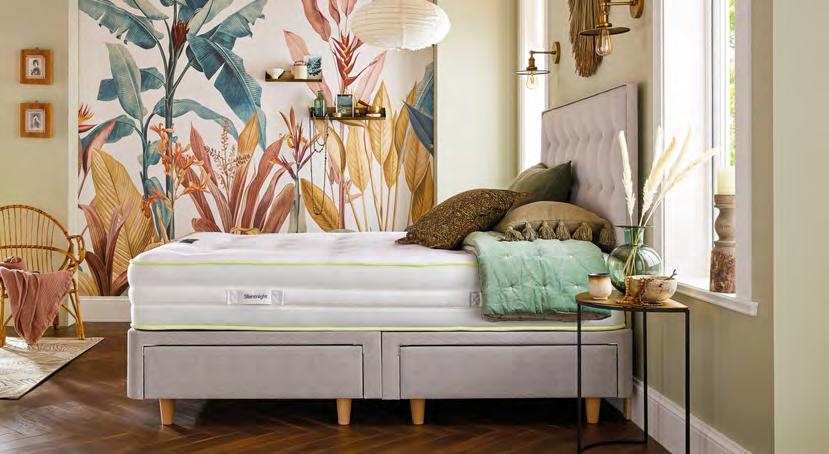
Silentnight becomes world’s first sleep brand to join UN-backed decarbonisation project
British bed brand, Silentnight, is the world’s first bed and mattress manufacturer to commit to the Science-based target initiative (SBTi), one of the planet’s leading decarbonisation initiatives, with partner organisations including the UN Global Compact, the World Resource Institute, CDP and the WWF.
In working alongside SBTi, Silentnight joins some of the world’s biggest brands, including IKEA and Selfridges, to set the following three collective targets: setting a net zero long-term goal when it comes to carbon emissions; reducing emissions at a pace consistent with keeping global warming below 1.5°C; and disclosing progress towards these goals annually and transparently. All businesses participating in SBTi undertake three umbrella strategies, with further substrategies to move towards decarbonisation. These comprise mitigating fossil fuel consumption, reducing energy demand and switching to renewable energy sources – then demonstrating that their own suppliers are also making these changes, and collating clear, quality data to illustrate the impact of the supply chain’s changes. Collectively, these strategies reduce emissions both upstream and downstream from the brand, creating an even better overall result.
The bed brand is already making headway on its sustainability goals, and has reduced its carbon emissions by -49% during the last four years alone. Projects which have helped the business achieve this success including sourcing 70% of its raw materials close to its Lancashire headquarters, using 100% renewable electricity, cutting one million kilos of fuel consumption, and sending zero waste to landfill via its manufacturing site. In the past five years Silentnight has sold over 1,500,000 Eco Comfort mattresses, bringing sustainable sleep at an affordable price to the mass market. The range features recycled plastic bottles that are ground and spun into comfortable eco fibres. Silentnight reduces its consumption of virgin raw materials by using materials from 450 million recycled plastic bottles each year within its range of mattresses, pillows, duvets and mattress protectors. Angela Moran, product strategy director, says: “We’re proud to be market leaders in sustainable sleep solutions, and have put sustainability at the heart of product development for many years, ensuring that affordable beds and mattresses that also help to care for the environment are accessible to all.
“Now we’re taking these successes, which include reducing our carbon emissions by almost a half in four years, and making an even bigger commitment by becoming the world’s first sleep brand to set climate science-based targets.
“We’re already making plans as to how we can work alongside our counterparts across the globe to take on our fair share of the responsibility towards ensuring a future below 1.5°C global warming, and we look forward to reporting even greater results as our work within the project progresses.”
Silentnight has made other shorter-term, yet still major, commitments, to ensure its business operates sustainably while other long-term moves towards net zero carbon emissions are underway. This includes operating as a carbon-neutral business by offsetting 3600 tonnes of carbon, and investing in tree planting and renewable power projects in the UK and worldwide. The business is also a supporter of The Marine Conservation Society, which works to maintain healthy seas and reduce marine litter.
www.silentnight.co.uk
CAD/CAM/CIM SOFTWARE FOR WOODWORKERS
Streamline your design to manufacturing workflows
Powered by
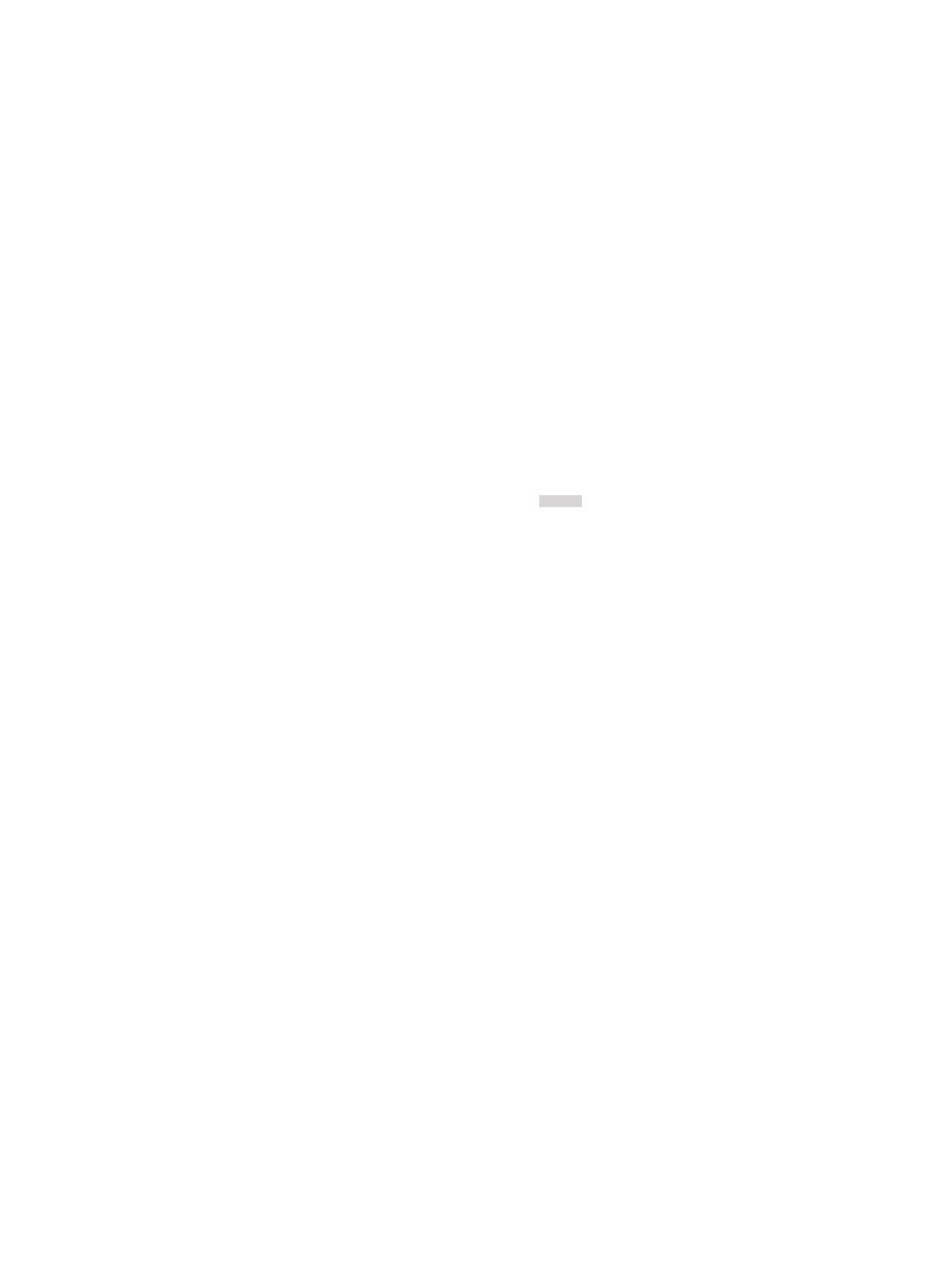
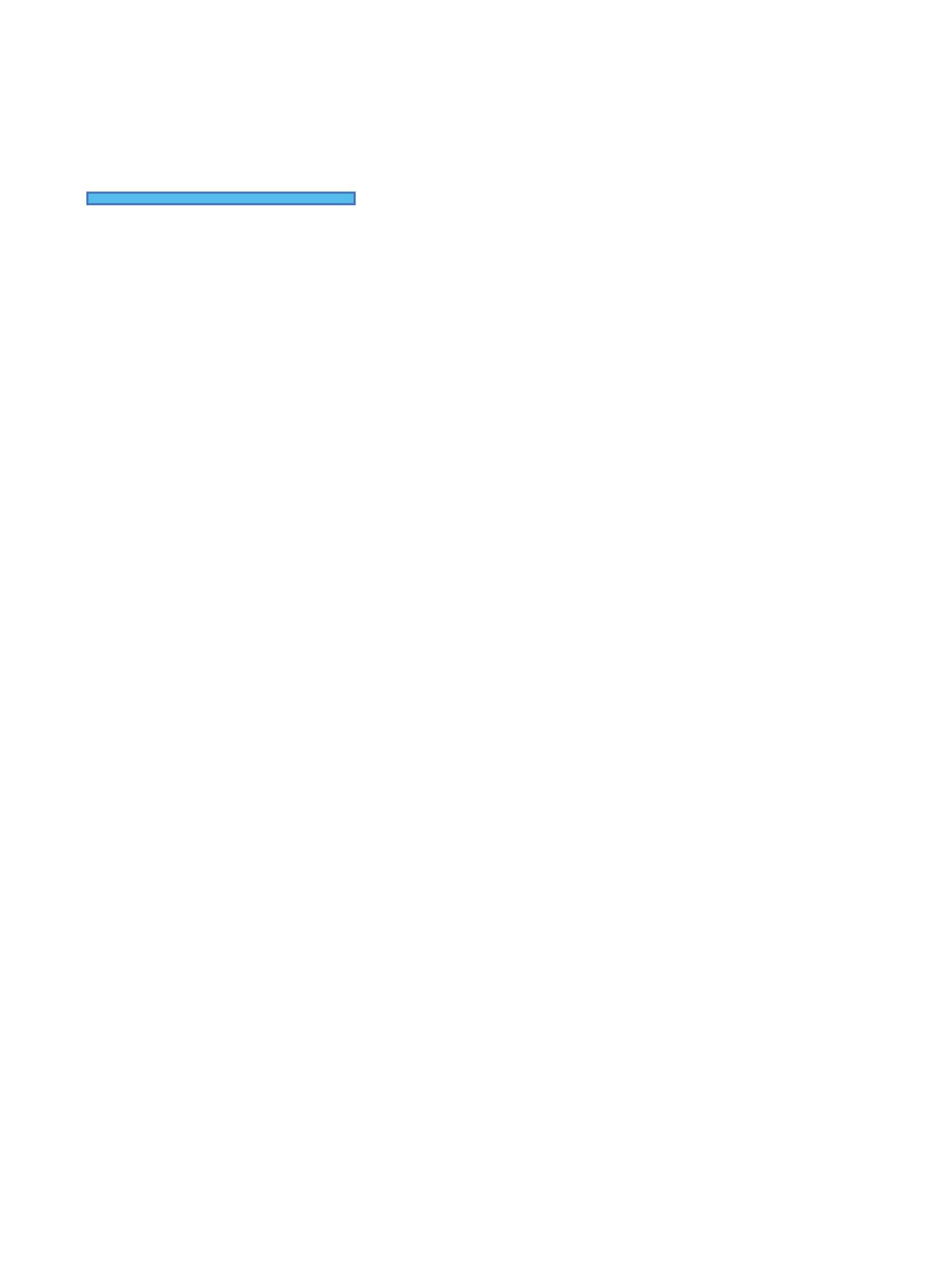
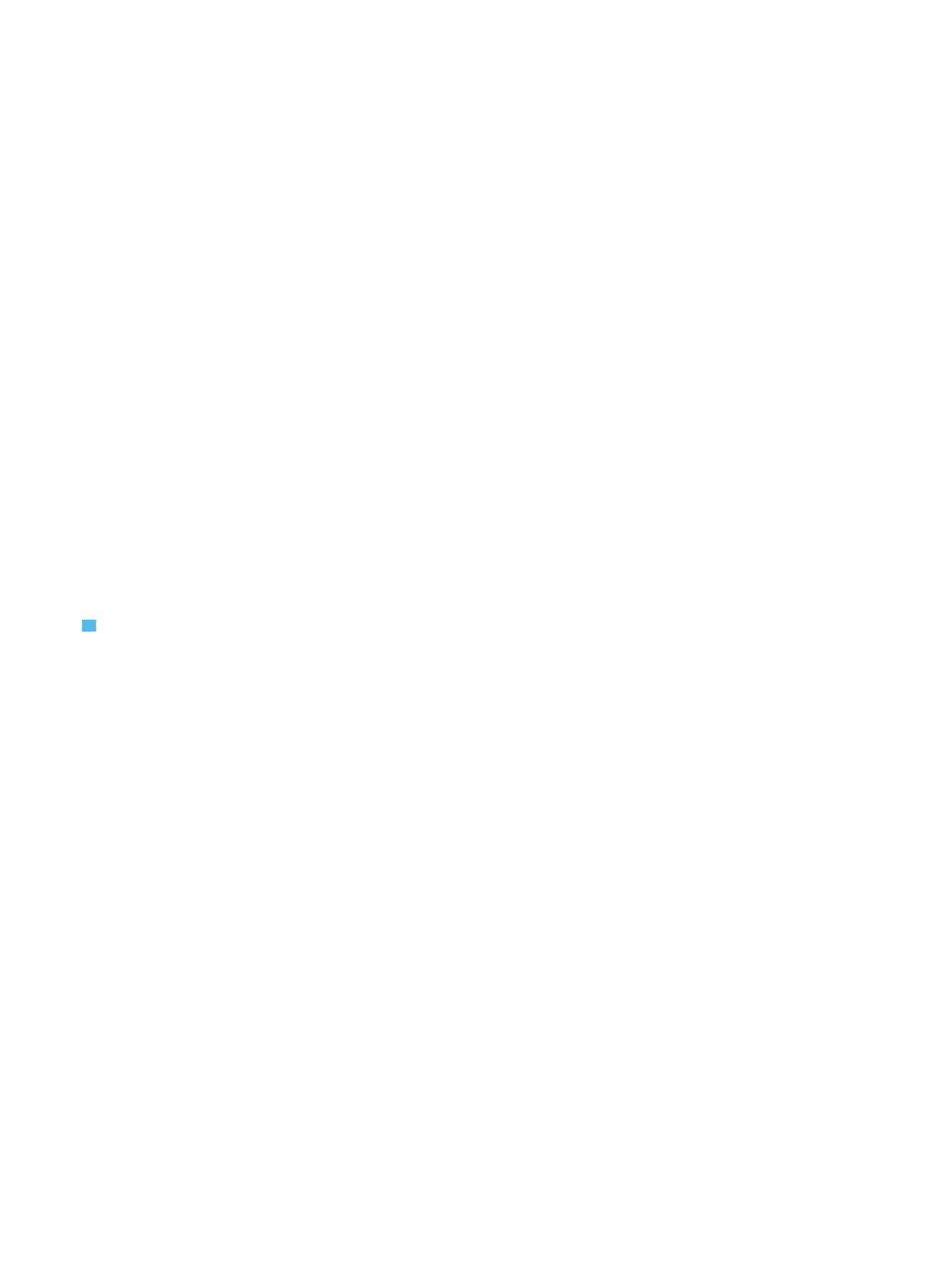
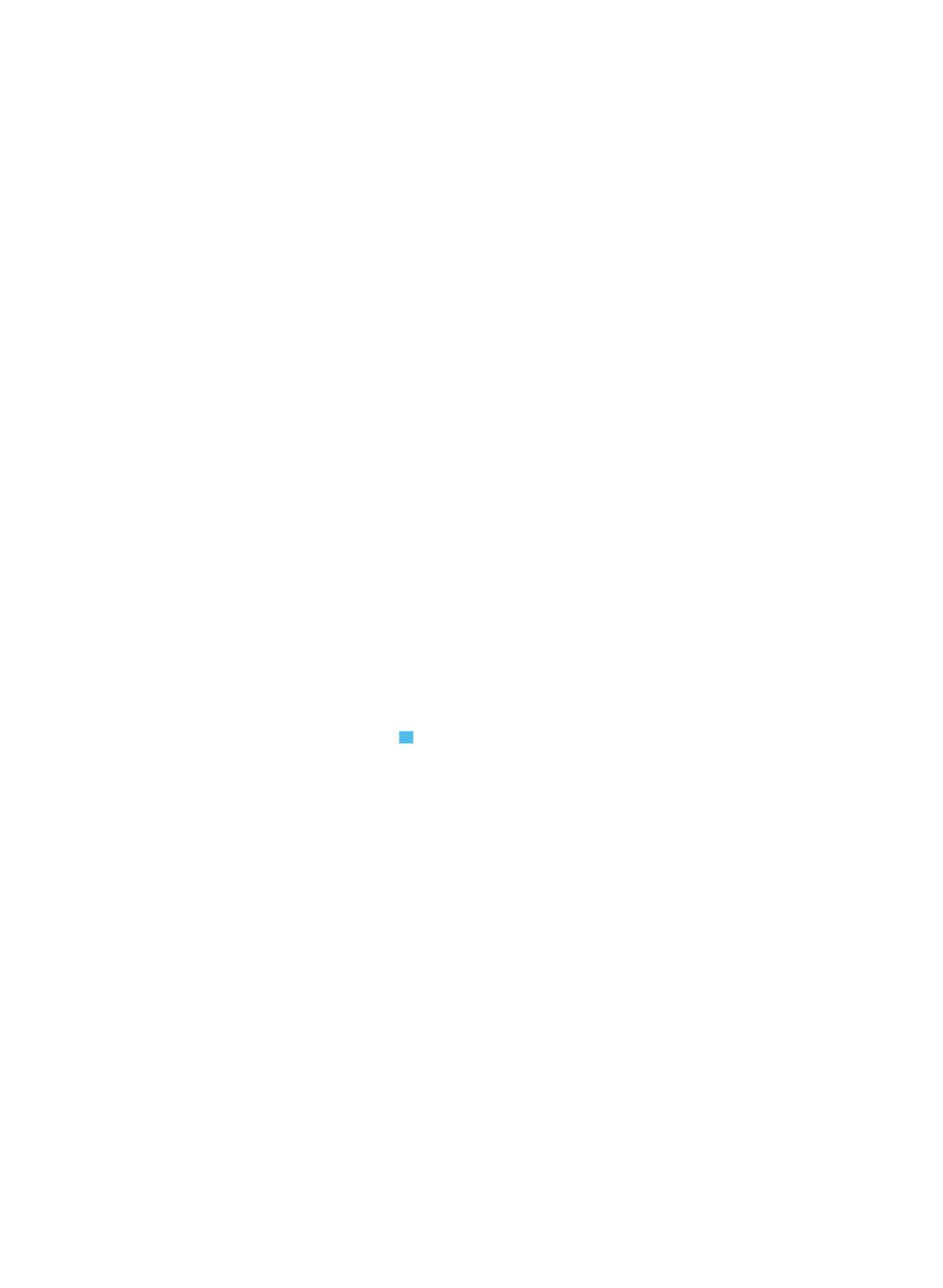
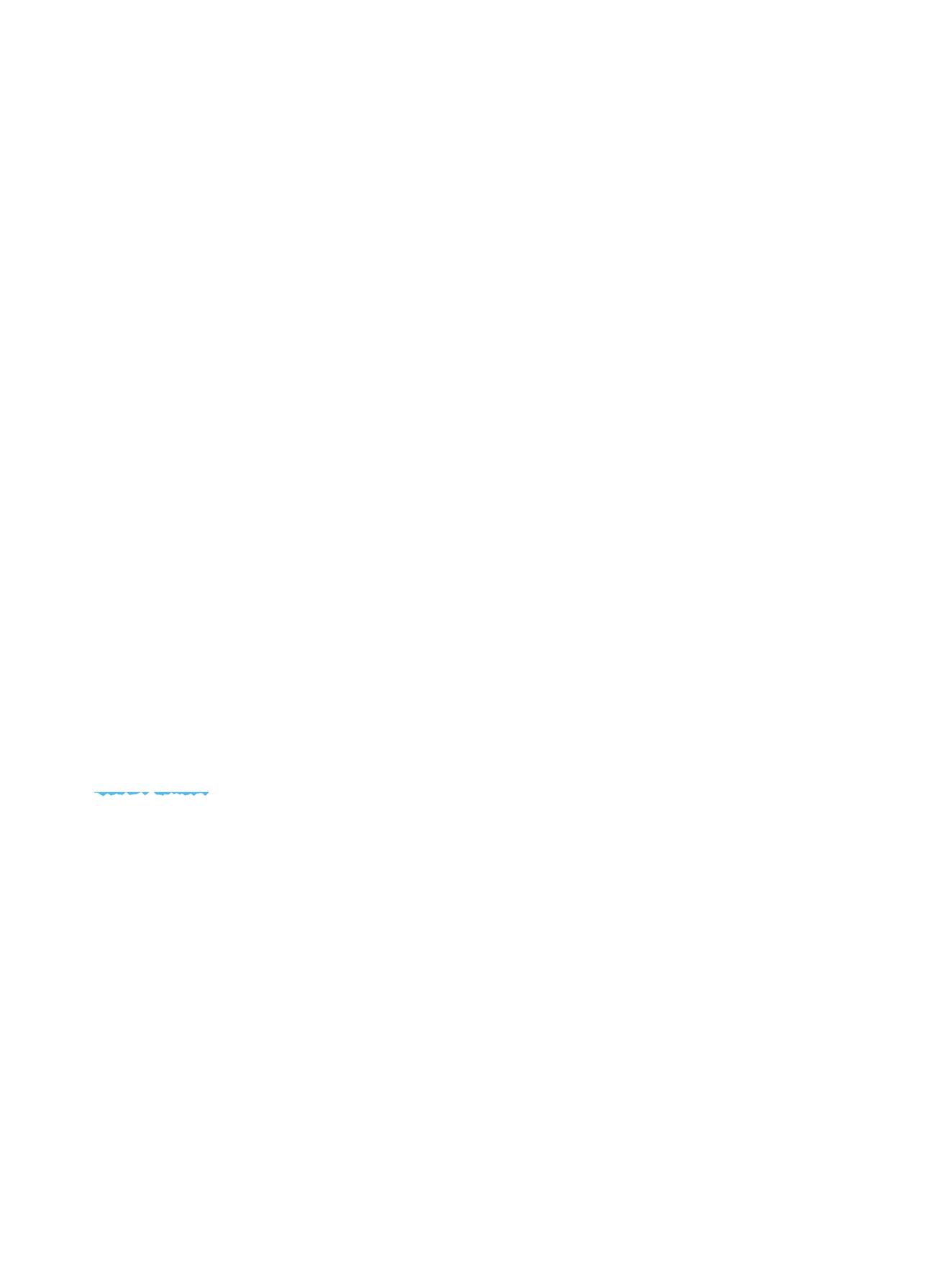
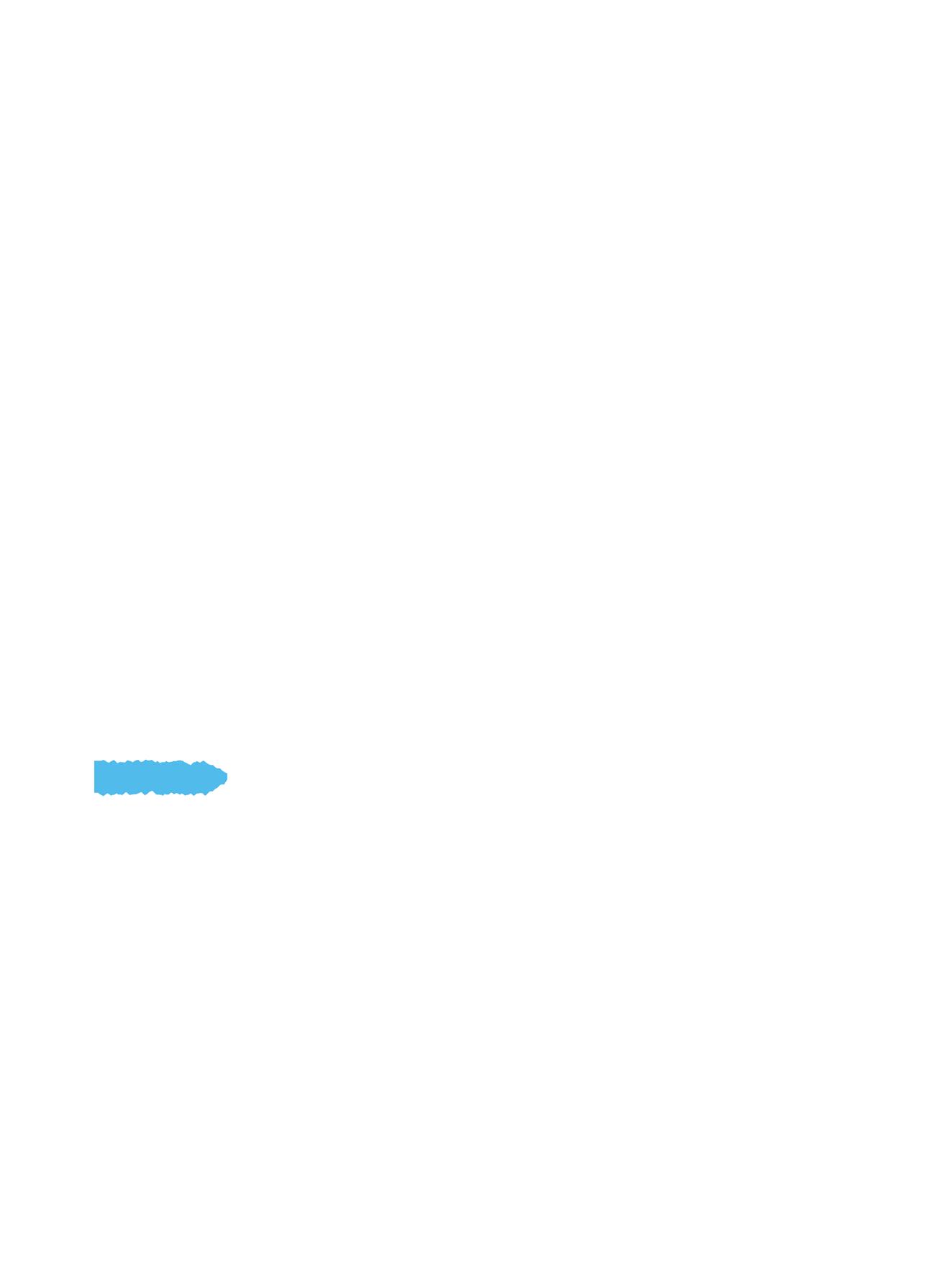
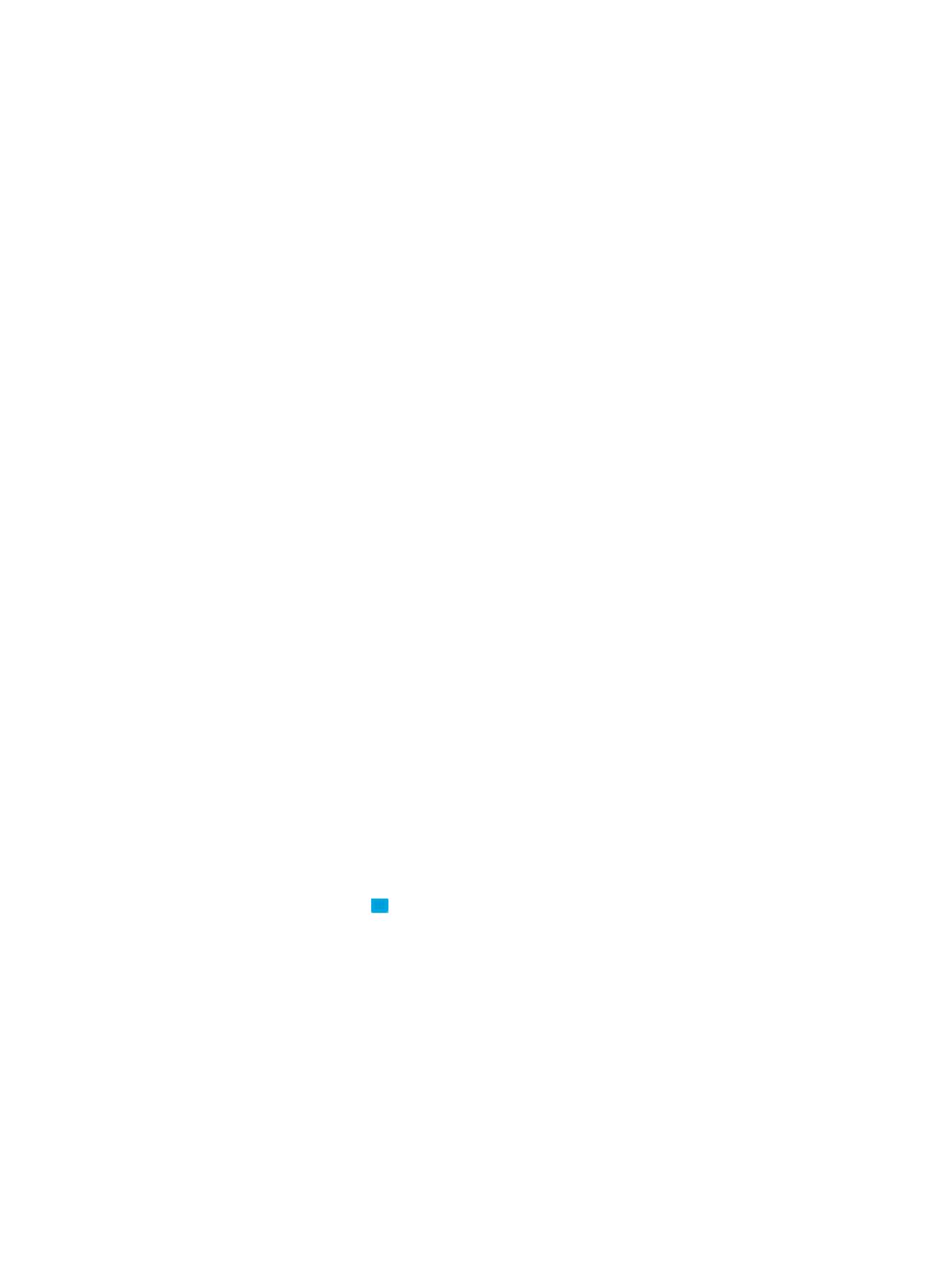
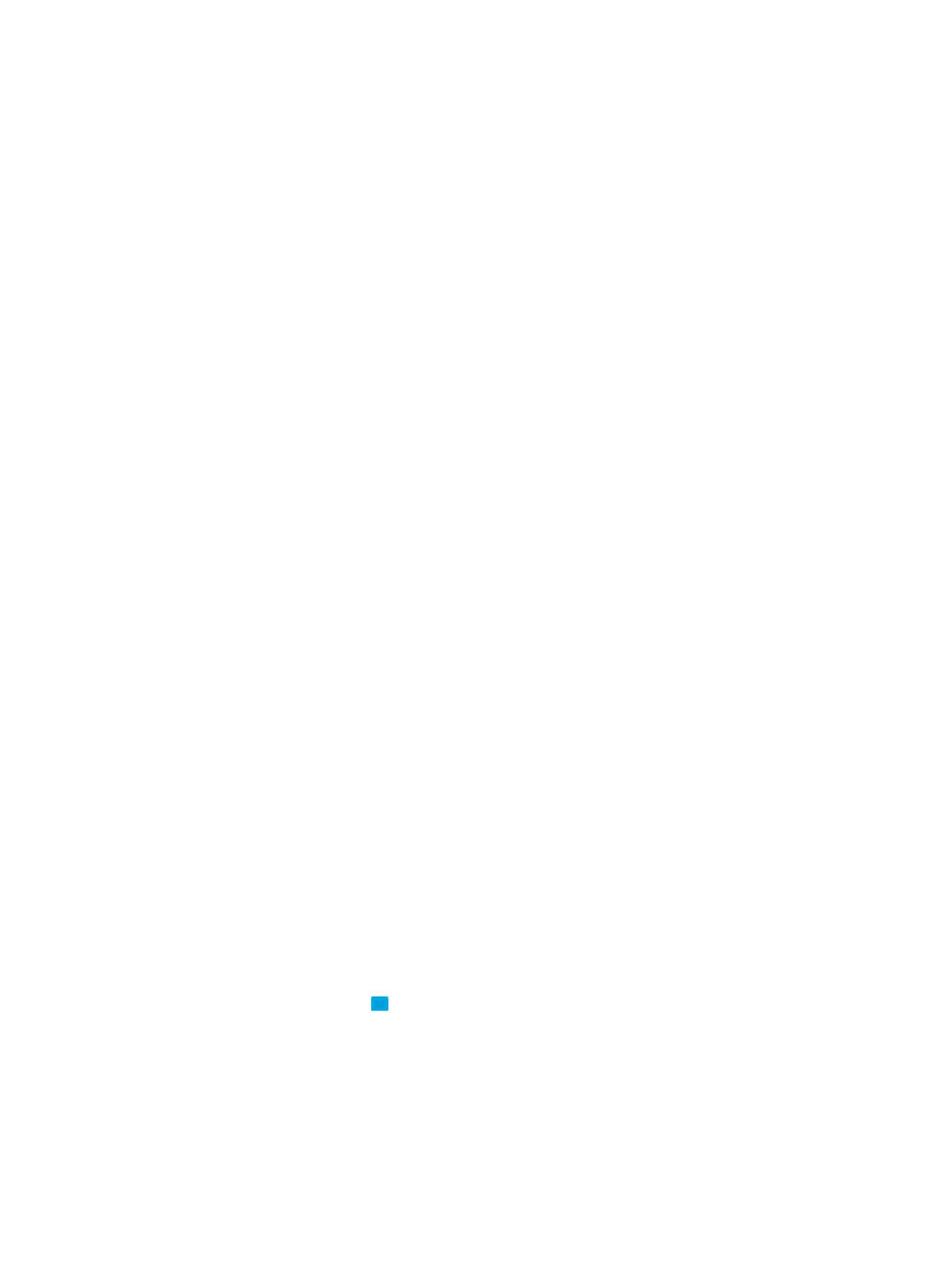
Microvellum has changed the way we do business. Their staff in the UK have not only assisted me to get the best out of my software and machinery but their extensive knowledge of manufacturing has helped us to be more professional and efficient. ” Scott Purdom
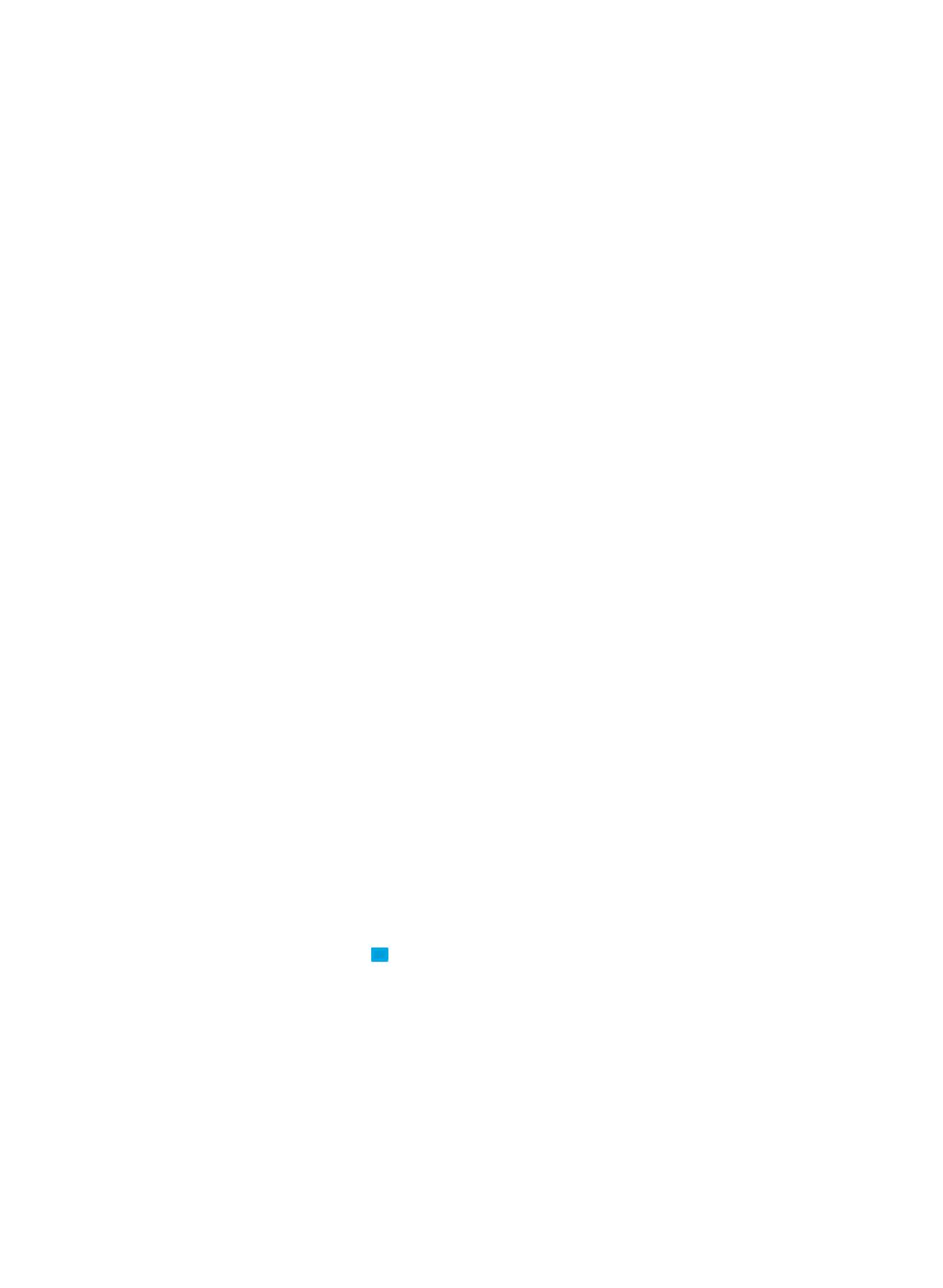
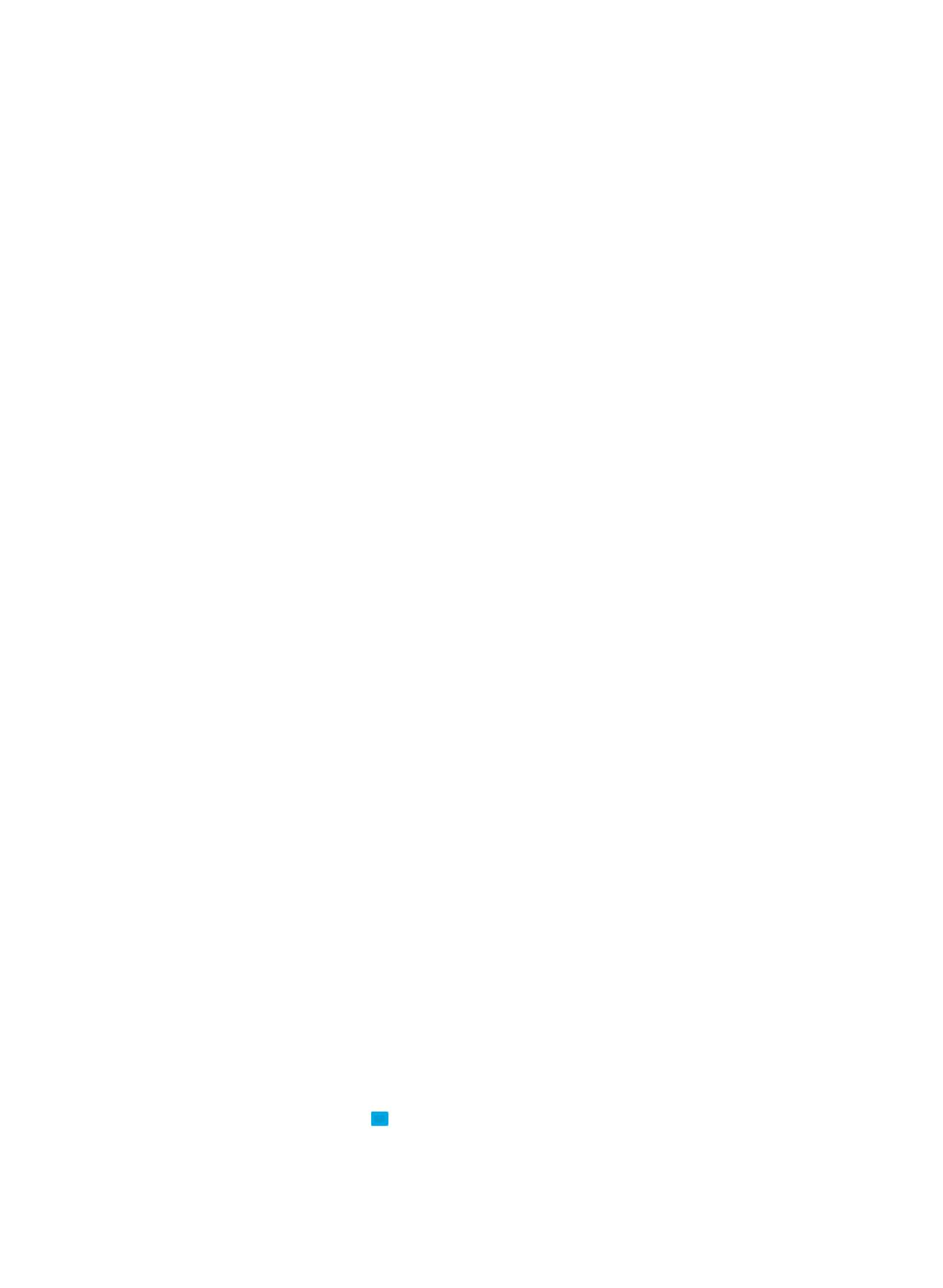
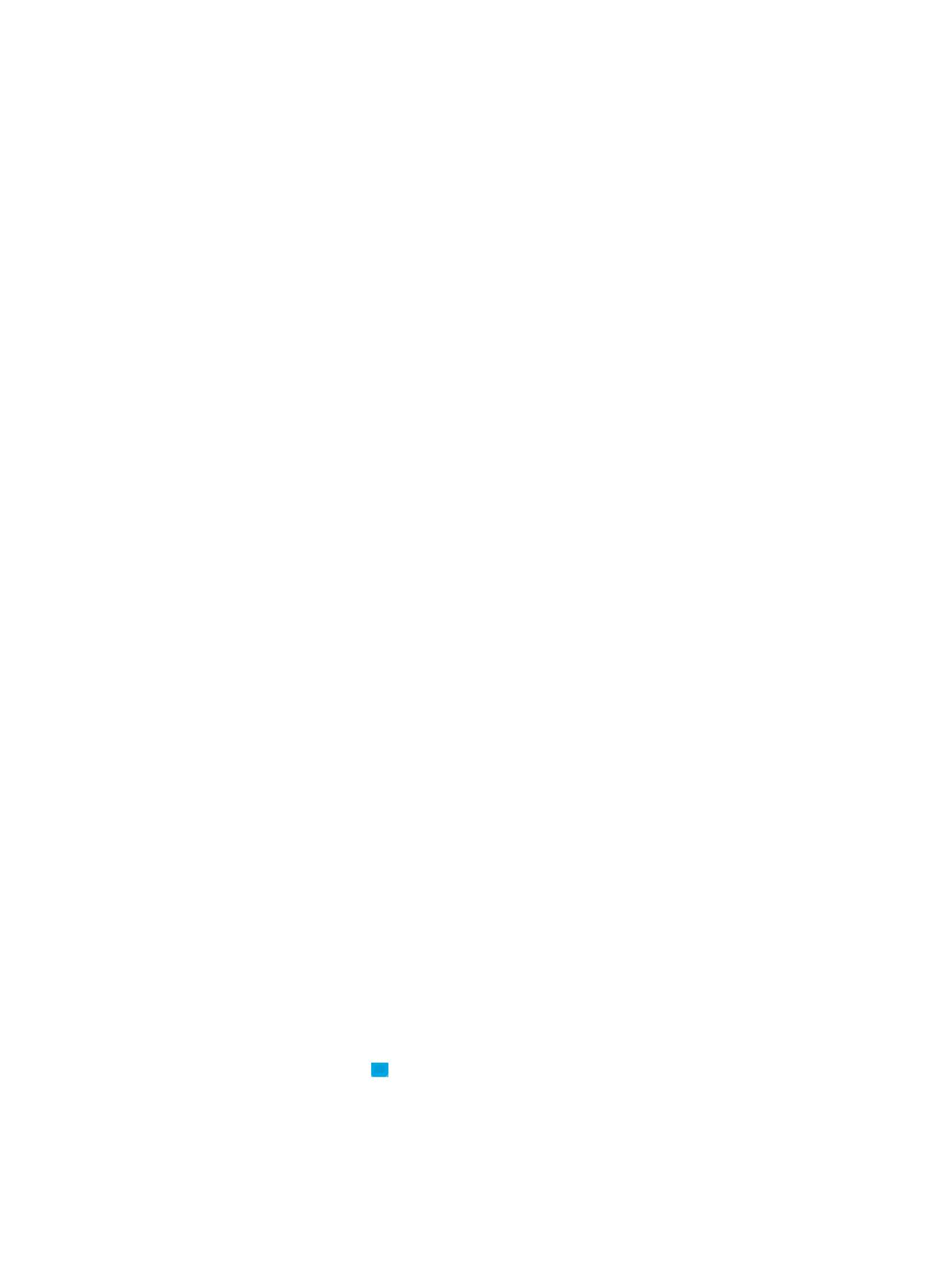
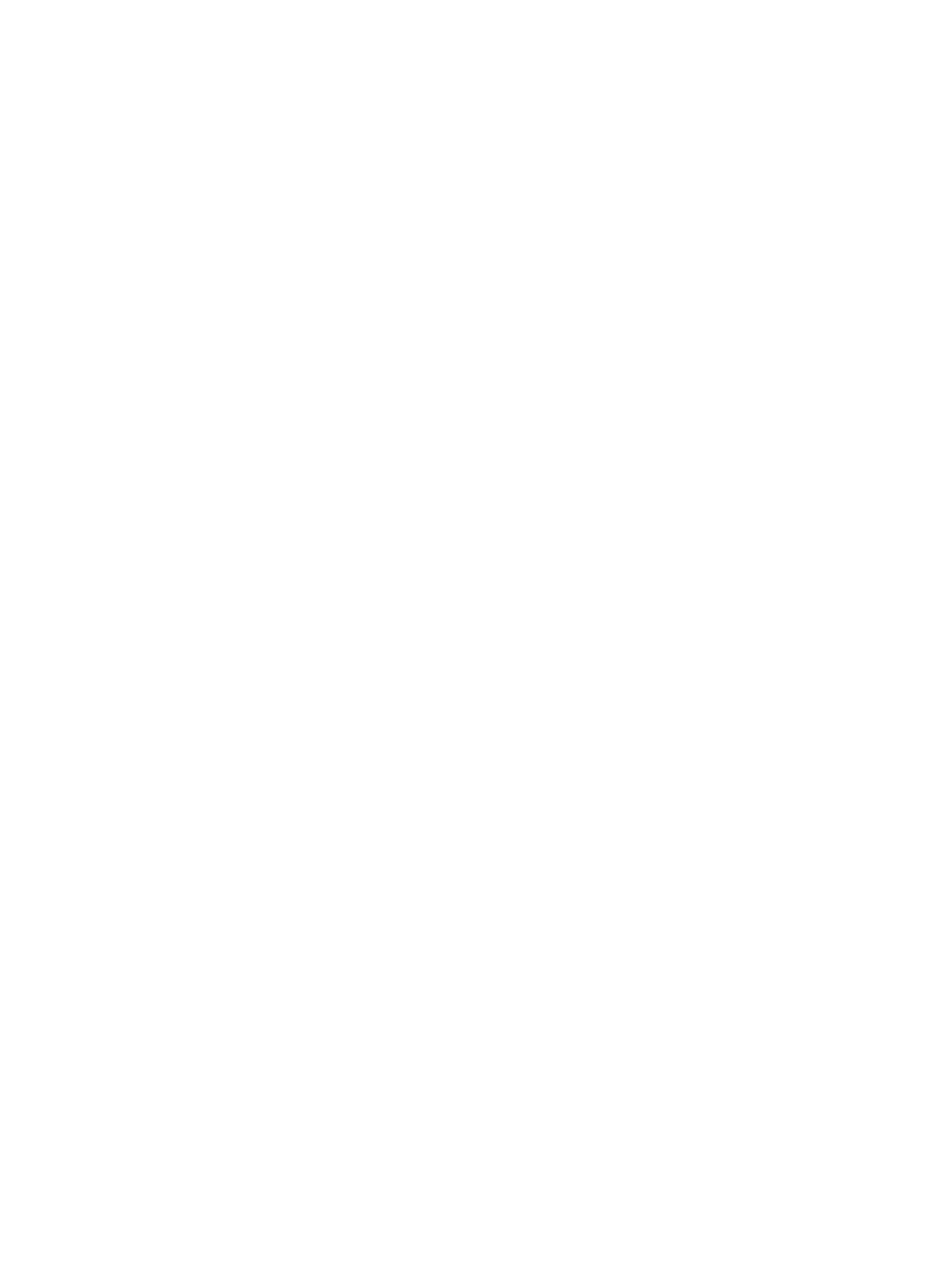
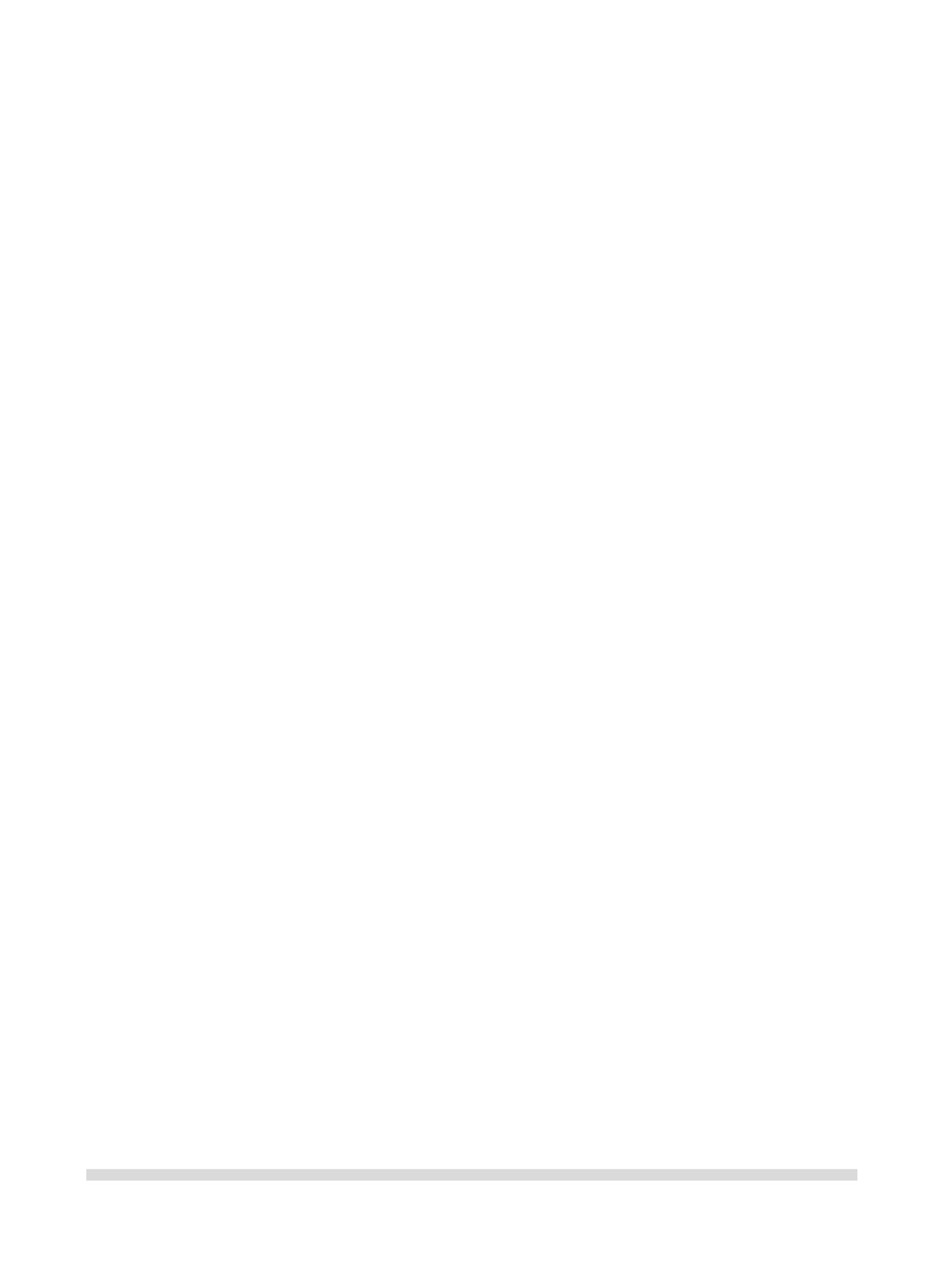
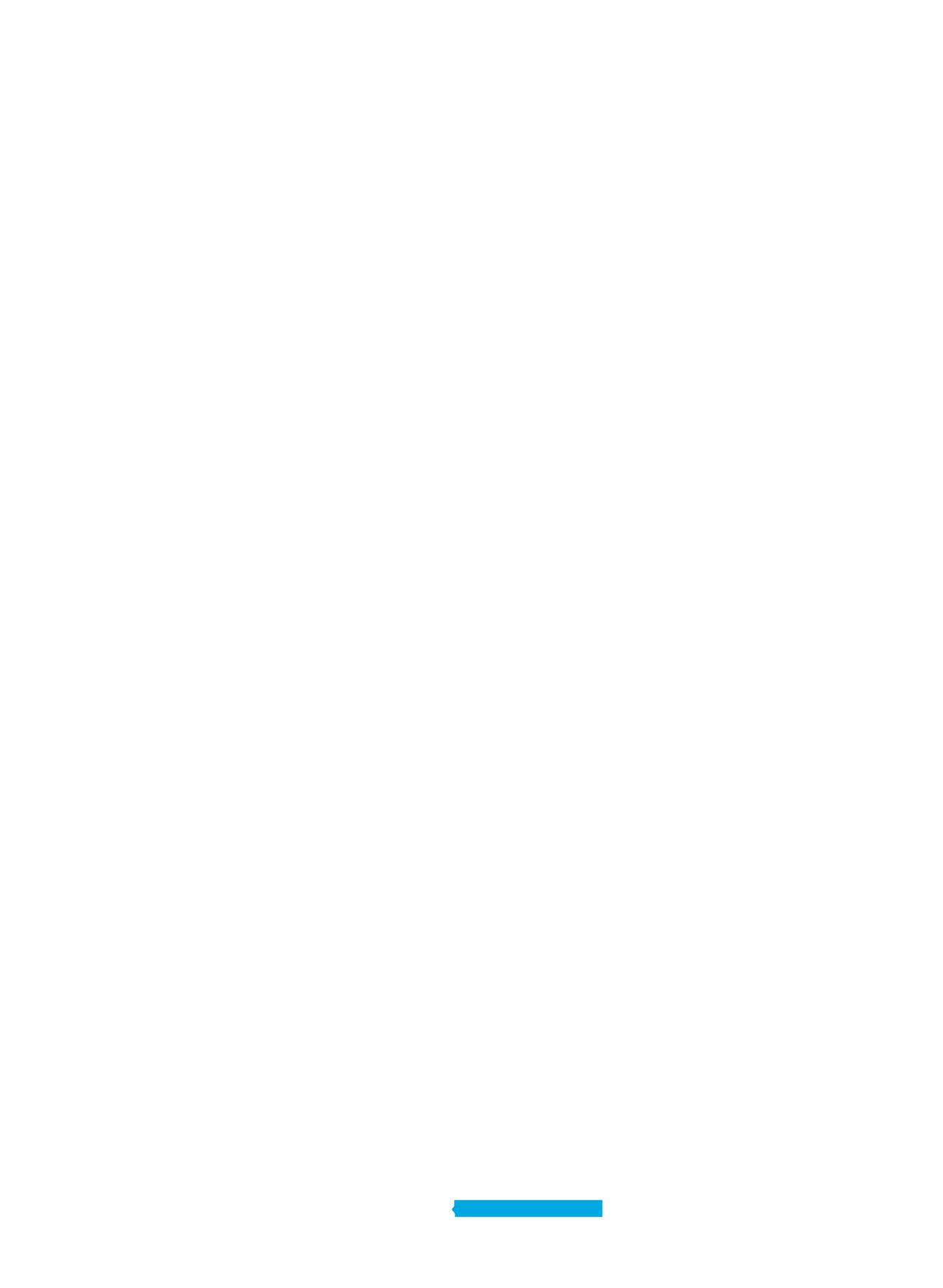
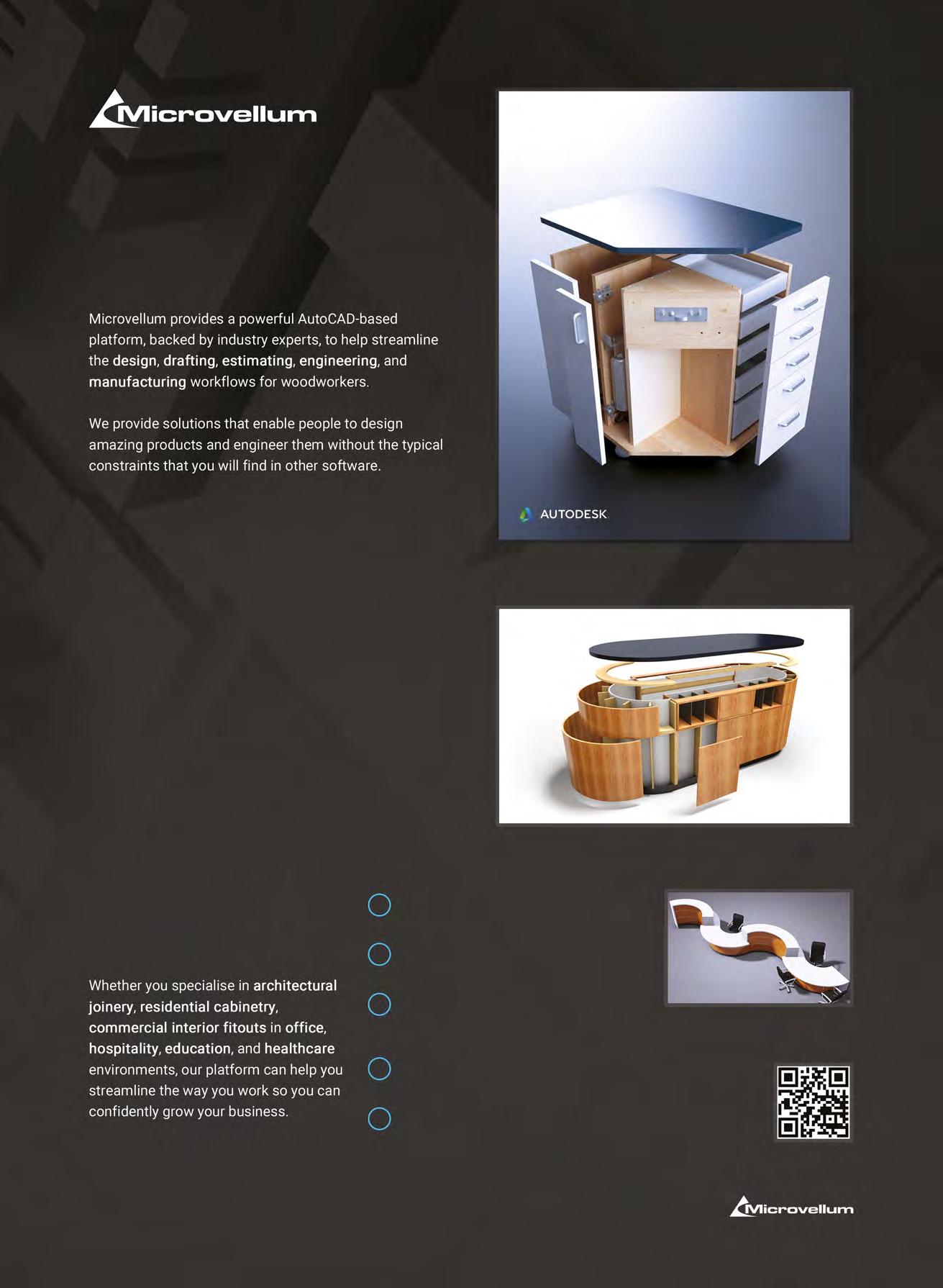
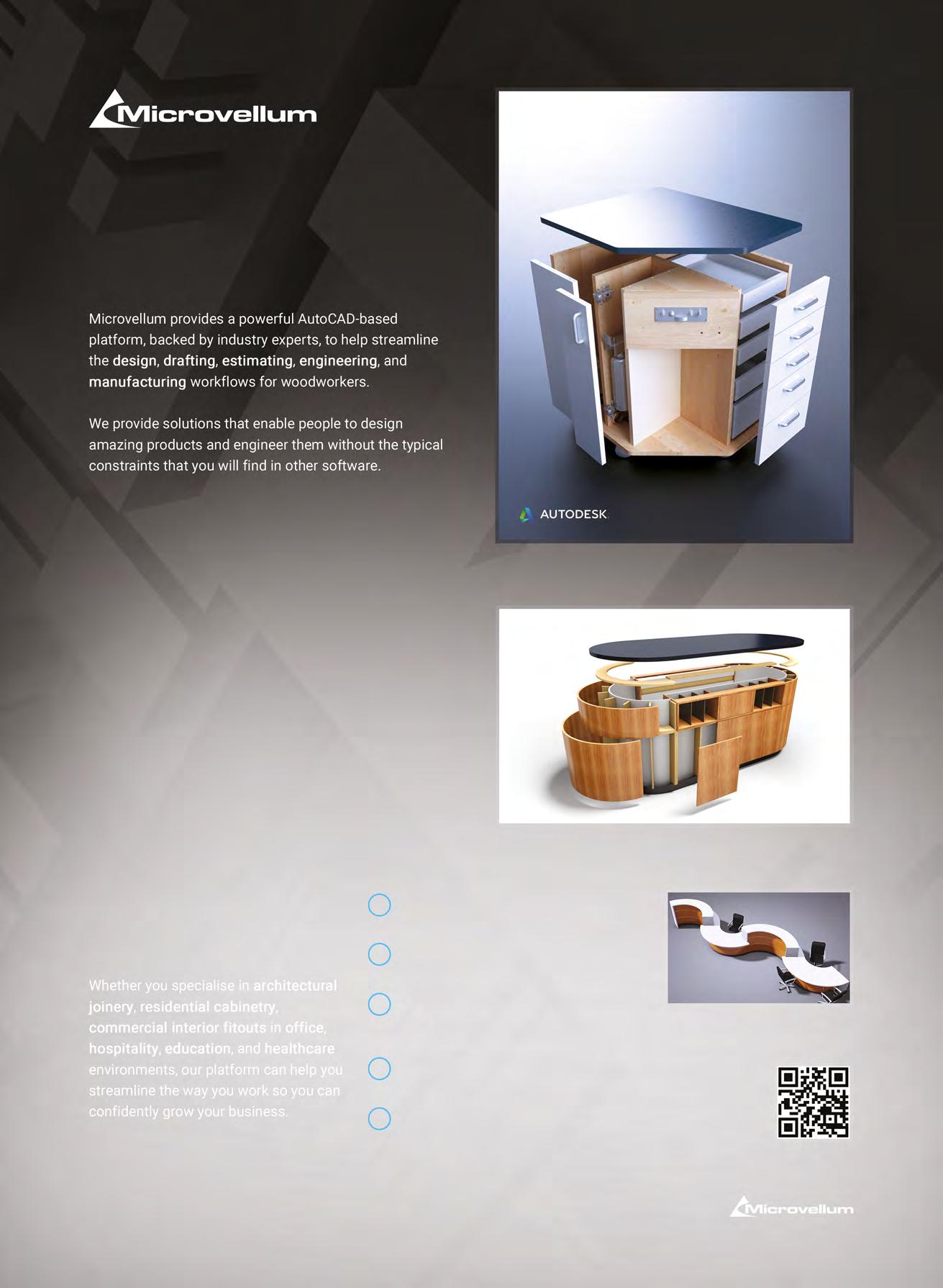
Lamin8 Scotland / Robe Lamin8 Scotland / Robert Sinclair Interiors
Confidently grow your business
Professional design and drafting tools built for woodworkers.
Predict your time, material and labour costs with confidence.
Limitless engineering possibilities allowing you to grow beyond simple cabinetry.
Helping you get the right data, in the Helping you get the right data, in the right place, at the right time.
A streamlined solution for design to CNC manufacturing
New recycling plant to create more sustainable bed manufacturing
Fifth-generation bed and mattress manufacturer, Harrison Spinks, is bolstering its sustainability credentials by launching a dedicated recycling plant and unveiling its first-ever annual sustainability report.
Having been at the forefront of sustainable bedmaking for years – including innovations in glue-free, foam-free and FR chemical treatmentfree manufacturing, Harrison Spinks has pledged to reach net carbon zero by 2023 through its focus on ethical and sustainable circular design.
Richard Essery
The company’s recycling plant is located in Scunthorpe, and will facilitate the disassembly and recycling of all Harrison Spinks mattresses containing its patented Cortec spring systems.
The recycled components can be reprocessed into new raw material for future use as part of the company’s ‘circular by design’ ethos, meaning that no Harrison Spinks mattress should end up in landfill. Other sustainable initiatives announced in the sustainability report include: the appointment of a taskforce to deliver sustainable initiatives on a monthly basis; further investment in in-house weaving looms to reduce the company’s carbon footprint; launching Harrison Spinks Renewables, with plans to invest in solar projects in the future; significant tree planting with the Northern Forest; partnering with British Wool to be the first bed manufacturer to be part of its new traceable wool initiative supporting British farmers; and going fully electric with all on-site and company vehicles. Director of sustainability and innovation, Richard Essery, comments: “Our Beyond Circular approach sees us commit to an entirely recyclable, reusable and zero-to-landfill production, to ensure we continue to lead the way in sustainability and change the way the world sleeps.
“The innovative work and initiatives of the business are contributing to saving the planet in many ways.
“The continued efforts to make entirely sustainable products – from the initial stages of growing materials to the end of their long life – have been happening behind the scenes, and it’s time to share these in detail. “While we’ve set the wheels in motion, we’re not afraid to recognise that more needs to be done to become a completely sustainable business, for both the health of our customers and the benefit of the environment. We’re immensely proud to unveil our latest sustainable innovations and future plans through our sustainability report.”
www.harrisonspinks.co.uk/sustainabilityreport-2021
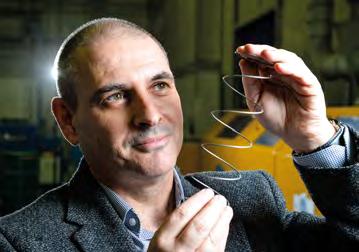
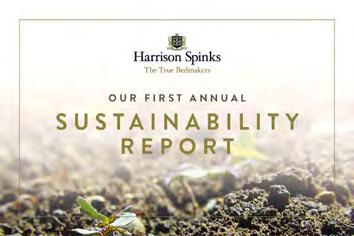
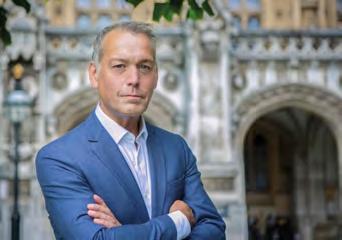
Recognising that the UK must build more homes, quicker, while reducing carbon emissions, the All-Party Parliamentary Group (APPG) for the Timber Industries has launched with a new report that aims to provide solutions to the UK’s housing and climate crises.
The report, titled ‘How the timber industries can help solve the housing crisis’, calls on the Government to support the use of wood in construction through policy and procurement, as well as introducing legislation to regulate embodied carbon – starting with mandatory, standardised carbon measurement on all Government projects.
Launched on 16th September at the inaugural general meeting of the APPG, the report makes a series of key recommendations devised to help the Government reach its target of building 300,000 more homes per year, while also significantly boosting the trajectory towards net zero carbon. Crucially, the recommendations call for a new focus on whole-life carbon emissions within the Building Regulations and the introduction of thresholds for embodied carbon within construction.
The report urges the Government to give preference to low-carbon materials and building solutions for all Government projects, pointing to the economic benefits that scaling up the timber and forestry industries would bring. Calls are also made in the report for a more joined-up approach to working with the timber industry, to develop an industrial strategy that can align with Government policy.
Finally, the report highlights that while the Government has – quite rightly – made building safety a top priority in the wake of the Grenfell fire, the regulations around combustible materials have not always reflected the realities of
David Warburton MP
safe construction using timber. A fundamental differentiation must be made between cladding and structural elements, and the report points towards an evidence-based approach to safety regulations.
David Warburton, MP for Somerton and Frome, and chair of the APPG, comments: “We are at a vital junction, where the imperative to build more homes is converging with the urgent need to reduce carbon across all of our markets. Now is the time to put forward policies that will enable us to build a more productive and low-carbon housing sector.
“By levelling up the existing timber and forestry supply chain, and making greater use of modern methods of construction, we can deliver more quality homes – and we can do this sustainably and at pace.”
Over the next Parliamentary session, the APPG for the Timber Industries will undertake a programme of activity to enable the timber industries to work with Parliamentarians to raise awareness of the vital contribution that the industries make to the UK economy and UK trade. It will also focus on the importance of the timber industries achieving net zero 2050, and the opportunities which exist to support sustainable timber construction in the UK.
www.cti-timber.org
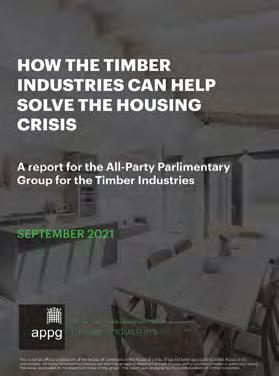
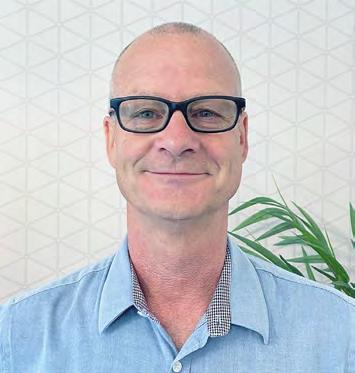
AAG appoints new UK-based MD for EMEA
Leading global supplier of tailored CNC routing and cutting solutions, AAG, has announced the appointment of Chris Arend as MD of its AXYZ Router, WARDJet Waterjet and CNCShop.com operations in Europe, the Middle East and Asia (EMEA). The appointment marks an important phase in AAG’s continuing global influence, product innovation and market diversification.
AAG’s senior VP of sales and marketing, Doug LoFranco, says: “Chris brings a wealth of experience and knowledge to the group, based on the contribution he made to the business success of SCM and, more recently, Biesse.”
Chris will be based at AAG’s UK and Ireland machine assembly and distribution centre in Telford. He will lead the EAMA team and oversee the continued success of the group’s AXYZ, WARDjet and CNCShop.com power brands. Welcoming this new challenge, Chris says: “With my previous experience and familiarity with industries similar to those served by AAG, I hope to enlarge the group’s already considerable customer base.”
01952 291600 www.axyz.co.uk
Customer support with a 360° view
Anyone that manufactures, sells or fits furniture with Blum fittings can benefit from customised, all-round service packages.
Blum has built up a reputation for not only selling quality fittings for kitchens and other home furniture, but also providing an array of services to help every touchpoint of their business. In a holistic sense, Blum understands the term ‘services’ to mean anything that facilitates the work of its customers. Included in this offering are digital services – Blum E-SERVICES such as Cabinet and Product Configurators – and its CAD/CAM Data Service, in addition to personal customer support provided by Blum experts.
Blum also supports its manufacturing customers with logistical services such as order management. Assembly devices – from easy-to-use templates and EASYSTICK, right through to MINIPRESS – are also part of the overall range of service products provided by the fittings specialist.
The technical services hotline is available 12 hours a day during the week (8am-8pm), and 8am-12 noon on a Saturday, on 0800 230 0898, with Blum expertise available free of charge to manufacturers and fitters alike.
Retailers have long been supported in the UK, with dedicated team members that can have a chat, visit showrooms throughout the country to do a quick technical check of the presentation elements, making sure all products are properly adjusted and presented correctly. Blum also helps to maximise displays to further ensure that consumers realise the potential storage offerings that can be achieved by using its storage solutions.
In its marketing activities, Blum supports its customers with communication services such as the Marketing Media Library. Indeed, Blum offers constant support throughout the customer’s process chain.
Which processes are used and which services are appropriate depends on whether the customer is a furniture manufacturer, cabinetmaker, retailer or fitter.
The needs and challenges also vary depending on the customer’s size and degree of automation. Blum considers these on a case-by-case basis, and with a 360° view of everyday operations, to offer service packages that are always relevant. This also makes it possible to inspire customers with a combination of high-quality products and services tailored to their needs.
01908 285700 www.blum.com
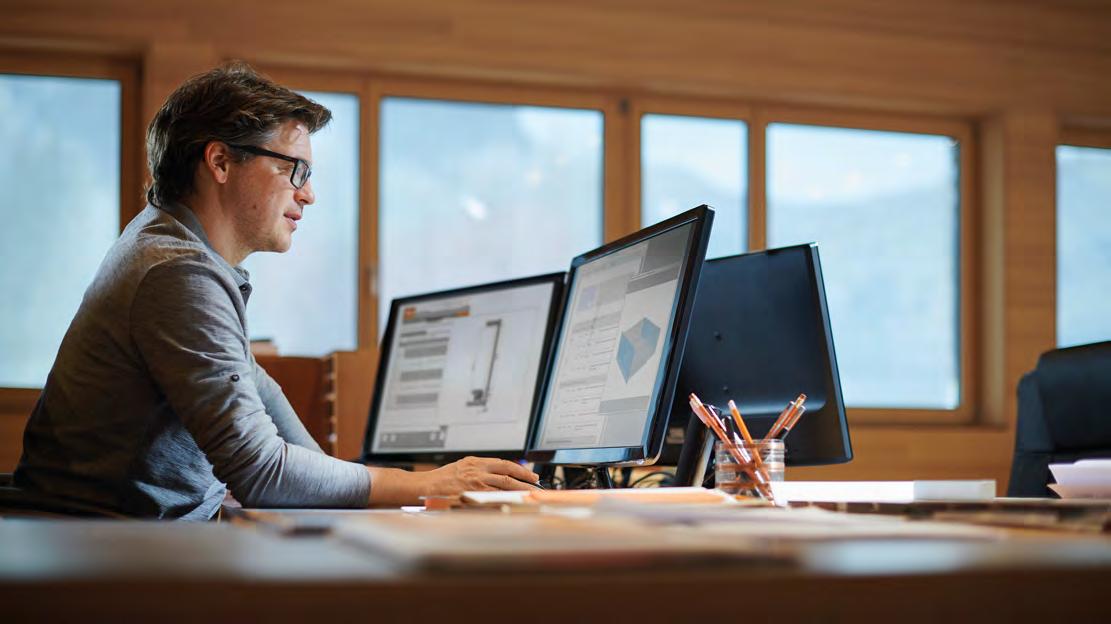
The BFM – putting essential expertise centre stage
Furniture manufacturers can access top-flight expertise via a new webinar series hosted by the British Furniture Manufacturers (BFM) – as part of an enhanced package of online services.
The webinar series follows recent major investment in digital offerings from BFM, including a new website, with individual profile pages for each member.
BFM MD, Nick Garratt, says: “We are delighted to launch the webinar series.
“The topics covered during the webinars will help those in our industry to protect and support their businesses.
“They will provide an informed overview of a range of issues that can present challenges to member businesses on a daily basis, and we are grateful to our partners for sharing their expertise.”
The first session in October kicks off with the topic ‘Doing business with the EU and Northern Ireland, post Brexit’ delivered by Jason Croke, VAT & customs director at Rayner Essex LLP Chartered Accountants.
The webinar, on Wednesday 6th October, will cover importing goods from EU to the UK for B2B and B2C, postponed import VAT accounting and duty deferment accounts, as well as exporting goods from the UK to EU for B2B and B2C, import duty, commodity codes, incoterms, rules of origin and Import One Stop Shop (IOSS).
The webinars are free. Each guest gives a halfhour presentation, and the sessions end with a Q&A session.
The webinar series follows a major investment in the digital realm by BFM in recent months, following the launch of the new website, providing each member with a profile page dedicated to their business and offering customers an easy-to-search showcase of the best of British furniture and homewares.
The service is of particular note for smaller manufacturers, who can take advantage of raising their profile in an engaging format.
BFM also launched a new Legal Hub in June, giving members a free toolkit offering legal and business advice on key topics such as health and safety, employment, contracts and data protection, as well as featuring policies, forms and guides created by qualified solicitors and business experts.
Since 1947, BFM has represented the interests of the British furniture industry, with a membership ranging from rural craftspeople to major household names.
Nick adds: “BFM issues industry-specific updates to members, to keep them abreast of developments in the sector, as well as providing a dedicated hotline and an online members’ area information service, which is constantly updated.
“BFM continues to develop a package of services that meet the needs of its members and champion the nation’s furnituremakers to the wider industry and to customers across the UK.
“The webinar series adds another layer of support, bringing expertise in specific fields to members in a way that is accessible to all, and I’m pleased that further events are planned going forward.”
BFM members can book a place on any of the webinars online.
www.bfm.org.uk/join-us
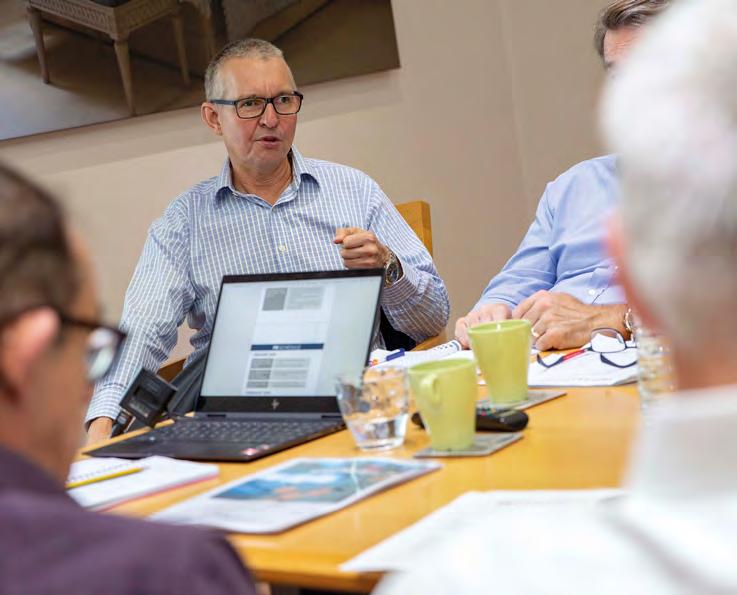
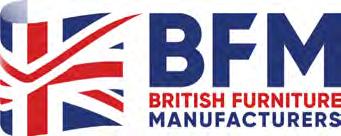
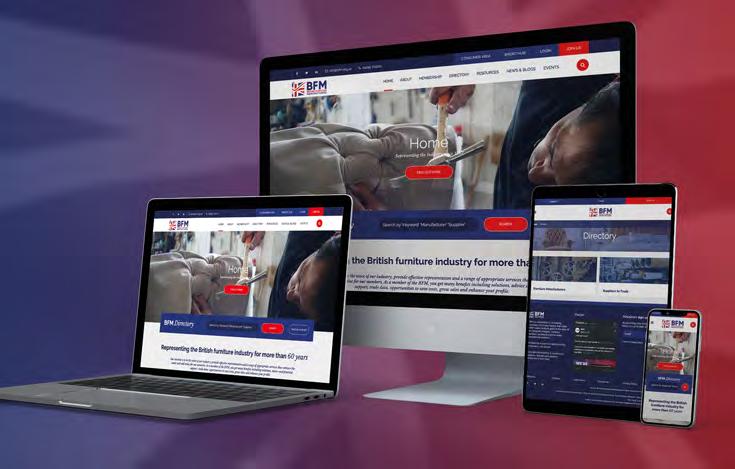