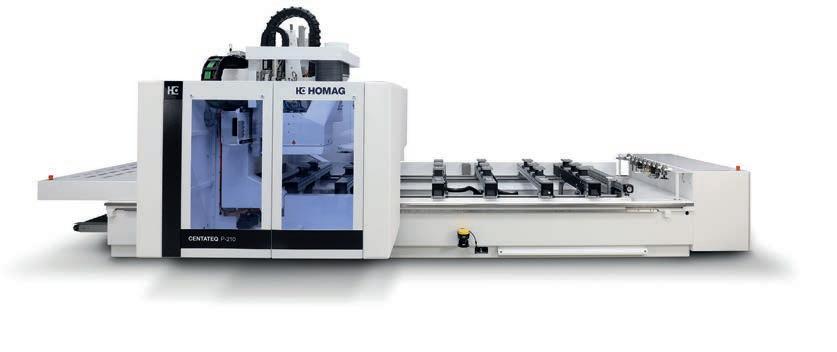
6 minute read
Installations
All-round furniture and joinery producer, Christopher Bell, recently selected Homag as its preferred supplier to upgrade its wood processing equipment.
Christopher Bell is a well-established company that has traded for over 25 years. It has 30 employees working at its 95,000ft2 manufacturing facility in Banbury. Not long ago, the company’s owner and managing director decided to purchase a state-of-theart Homag Centateq P-210 CNC processing centre to improve the company’s production effi ciencies.
Homag Centateq P-210 CNC facilitates more economical production
All of Christopher Bell’s furniture and joinery components were made by hand before the arrival of the new Homag machine. With the automation of much of its wood processing, the Homag Centateq P-210 CNC processing centre has signifi cantly improved the company’s manufacturing effi ciencies and reduced its labour costs.
To create automated processing programs, Christopher Bell employs Homag’s woodWOP workshop-based program system and CAM Plugin for its new CNC machine. This advanced 3D programming software enables the easy programming of routing, drilling or sawing.
A large graphics area with a three-dimensional view of the workpiece is the cornerstone of this innovative programming software. It guarantees the highest programming safety and permanent control during program generation.
Increased machining capabilities
According to the eponymous company’s owner and MD, Christopher Bell, the machining fl exibility of the Homag CNC processing centre was one of the most important reasons for the investment.
The machine’s latest generation control technology, drives and software ensure virtually unlimited machining possibilities.
The increased throughput, production effi ciencies and reliability of Homag machinery, backed up by the availability of spare parts, were also crucial factors in the evaluation and selection process for the CNC processing centre purchase.
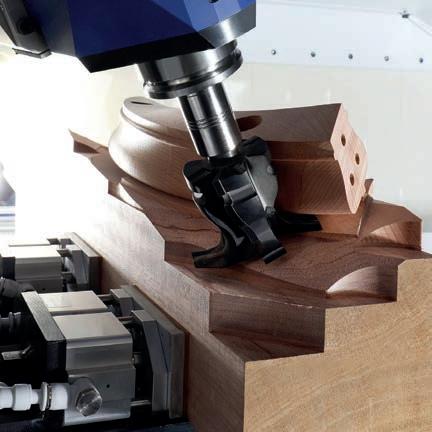
Due diligence built trust in Homag technology
Christopher Bell and his colleagues saw the Homag machinery at an exhibition before investing in the new equipment. In addition, Homag’s sales representative, Phil Pitchford, took Christopher and his colleagues to view a Centateq P-210 CNC processing centre in operation at a local factory.
Homag Centateq P-210 CNC processing centre
Christopher and his team found this really useful, and the feedback they gained from the visit helped to cement their confi dence in the long term reliability of the German-engineered, state-of-theart equipment.
Exceptional aftersales service
Commenting on the service Homag has delivered, Christopher says: ”Phil Pitchford, the Homag sales representative, helped us get the right solution and all within our budget.
“The aftersales service we have received from Homag has been exceptional – they have promptly addressed the occasional issues we have had, limiting downtime to a minimum. Homag’s helpline and online forum have been really useful for the machine operators, too – these resources have backed up the comprehensive operator training they received from Homag.”
For a demonstration or more information on Homag’s machinery or software, contact Adele Hunt at Homag UK on 01332 856424. www.homag.com
It has been over five years since JJ Smith installed the first MZ Pluris CNC working centre in the UK and, since that time, it has become the machine of choice for many of the leading sofa and chair frame manufacturers. 15 machines have been installed to date, the latest being at Blackburn-based ASF Sofa Frames.
The reason for the Pluris’ popularity in this manufacturing sector is its production capabilities and increased board yield compared to standard CNC nesting routers. On the Pluris, it is possible to machine a stack of panels up to approximately 60mm in thickness. For example, this would be four 15mm plywood panels instead of only one or two on a standard CNC, meaning over double the production output.
The other unique feature on the Pluris is the fact it uses a bandsaw (which automatically angles) in conjunction with the router head
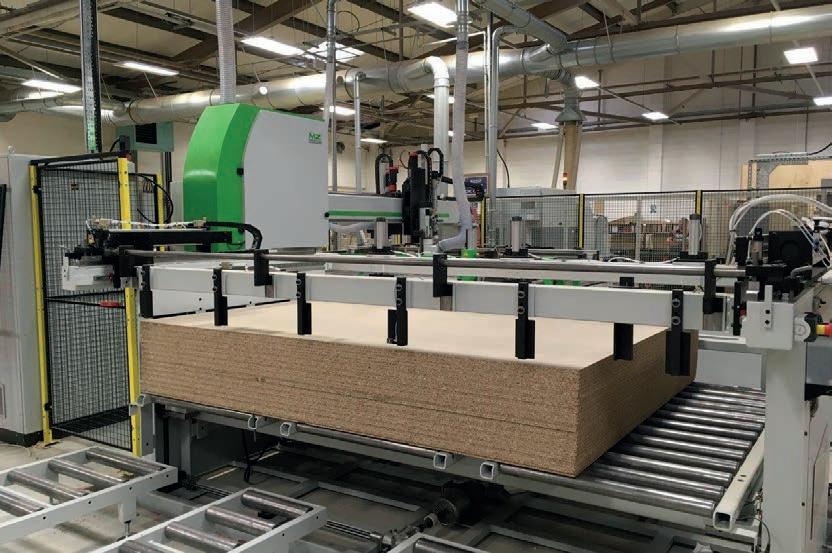
to cut out the nested parts. As the bandsaw thickness is only 0.8mm compared to a router cutter that is, say, 14mm in diameter, it is possible to create much tighter nests, meaning more parts with less material wastage.
The machines are normally supplied with an automatic lift table for loading the stack of panels onto the machine carriage, the standard size being 2550 x 1250mm. On request, this can be increased in width to 1550mm or, for jumbo-size sheets, the machine’s maximum capacity is 3100 x 2100mm.
In addition to the CNC-controlled router head and bandsaw, the Pluris is also equipped with a multispindle, point-to-point drilling head and automatic quick setting of the table support arms and panel grippers through the program. Optionally, a circular saw working in the Y axis can also be specified.
Whilst the Pluris is mainly used for cutting parts from sheet material, it can also be used for cutting, drilling, and shaping solid wood parts for items such as rails.
The Pluris at ASF Sofa Frames has now been installed for several months. “For our company it was a big decision to make such a significant investment, but one we knew we had to do to keep pace with an ever-growing order book,” comments co-owner, Mr Ashraf.
“Already we are seeing a twofold increase in production output, and a big improvement in sheet material yield.”
Contact JJ Smith to find out more about how this machine can increase productivity. 0151 548 900 sales@jjsmith.co.uk www.jjsmith.co.uk
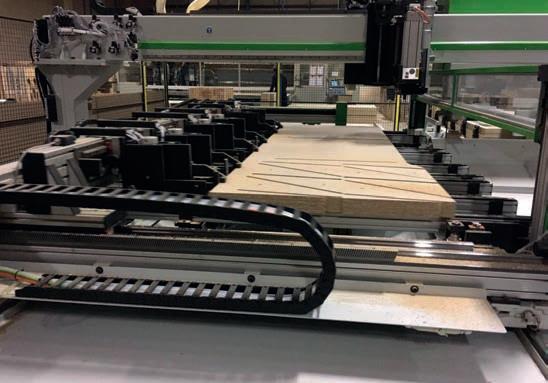
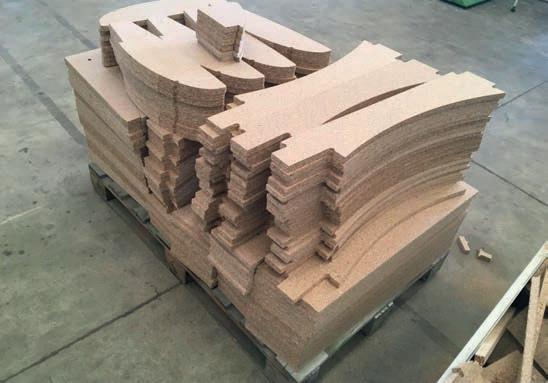
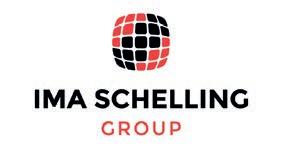
IMA Schelling UK enhances customer service with launch of new website
IMA Schelling UK is a subsidiary of IMA Schelling Anlagenbau in Austria, which is part of IMA Schelling Group, which celebrated 100 years of manufacturing in 2017 and is recognised as one of the most experienced saw manufacturers in the world.
IMA Schelling has always maintained a great relationship with all of our customers, and nothing was going to change that during lockdown.
Since the acquisition of IMA Klessmann UK in March of 2021, we have gone from strength to strength and can offer the full range of IMA Schelling group equipment to our customers, not just saws but also edgebanders and CNC machines.
We have also launched a new website in 2021– www.schelling-solutions.co.uk – to inform customers of our other services and product lines.
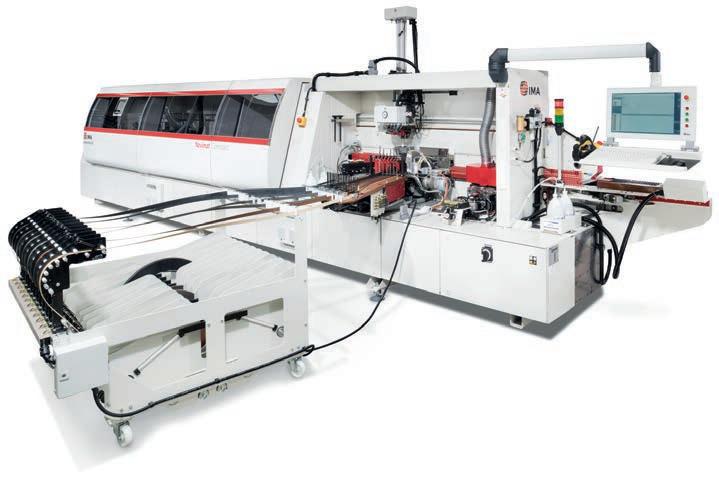
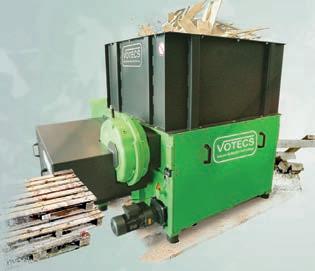
Customers can find other complimentary and supporting equipment, such as lifters and shredders (hoggers) for wood waste, alongside many other items of interest,
IMA Schelling aims to provide the right solution for its customers, no matter what your requirements are.
For further information, call IMA Schelling UK on 01937 586340
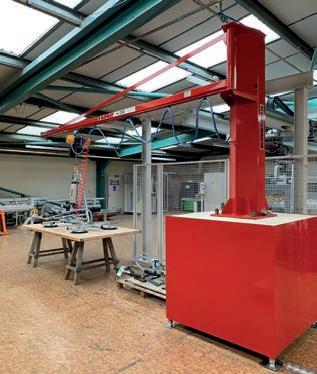
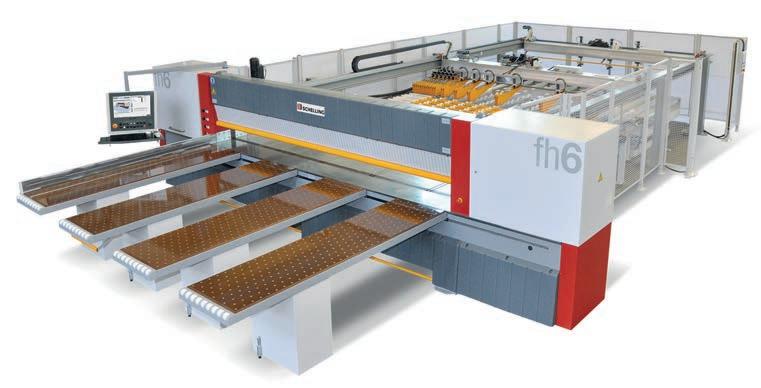