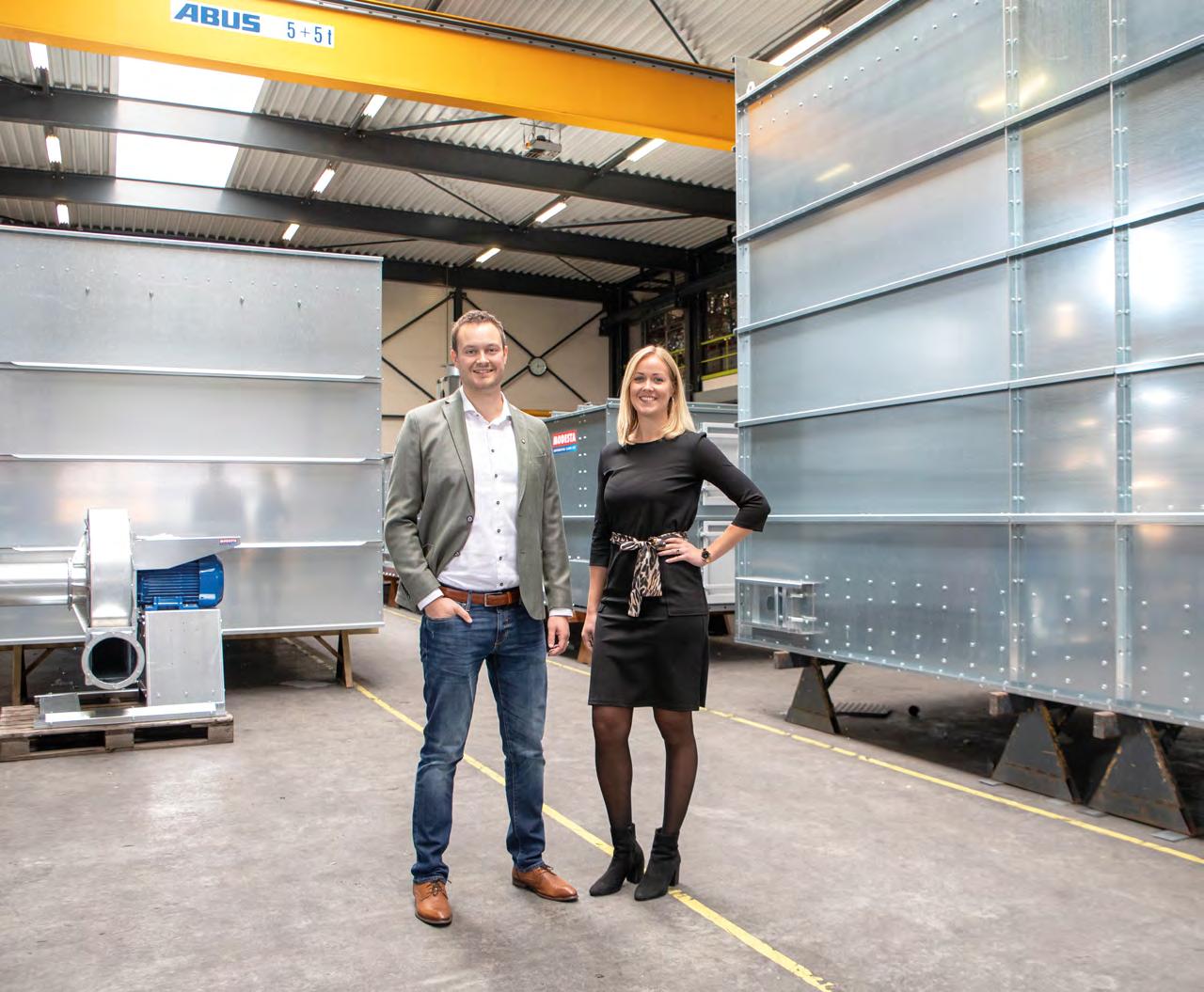
26 minute read
Dust Extraction & Woodwaste Management
62
Dust extraction & wood waste managment The best way to save energy is to not use it
Wyboud and Marianne Kloppenburg (brother and sister): third generation to lead family business Modesta
Energy consumption is a big expense for any factory owner – now more than ever. The perfect dust extraction solution uses just the capacity that’s needed in a specific moment, ensuring the lowest possible energy use. With a Modesta filter, this scenario is closer than you think.
In many factories, the biggest source of energy consumption is the dust extraction system. Most filter systems are suitable for the maximum volume required by the factory’s machinery, but are not designed to use energy efficiently when the machines are not running at maximum capacity. Switching from a basic ‘on or off’ extraction system to a modular solution has a quicker return-on-investment than one might think.
Energy-efficiency, usability, safety
A modular system has many financial and technical advantages. For instance, better pressure at modern CNC machines, longer bag life, and having all controls and energy saving equipment in the same easy-to-use control panel as the filter. A smart filter system will help you reduce energy bills dramatically and contribute to your net-zero energy management strategy. Air to cloth ratios are low, ensuring the lowest operational costs possible. Furthermore, an energy-efficient system is more likely to qualify for grants. Although an initial investment is required, energy-saving technology results in lower total costs of ownership.
At Modesta, safety is a matter of the utmost concern. All Modesta systems have been designed to withstand explosion pressures of wood dust. Explosion burst panels are mounted clear of the filter bags and on the raw air side. Optionally these can point upward to allow for a clear explosion zone. ATEX safety equipment like the rotary valve are certified. This means that in an emergency, the rest of the production facility is safe.
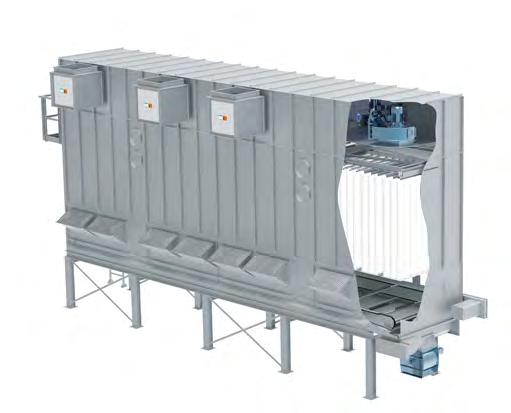
Modesta’s CF 80 Chain Filter Modesta’s CF 50 Chain Filter
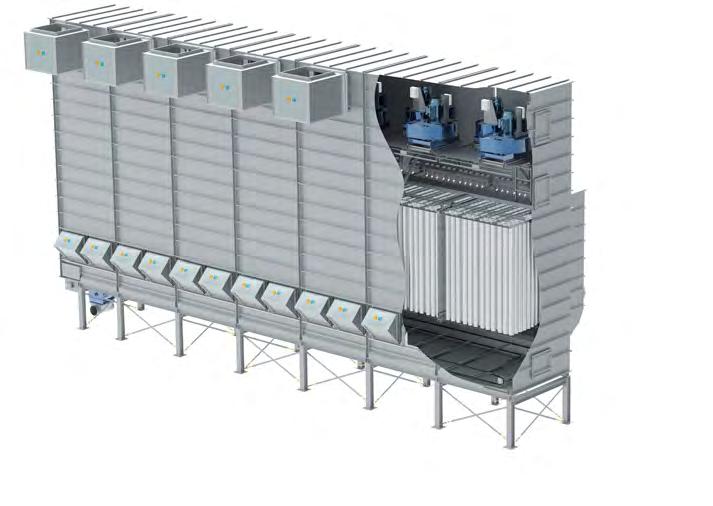
Overcoming challenges
Admittedly, installing and putting to use a new dust extraction system has a big impact on a factory’s infrastructure. Replacing or adding capacity can be challenging. But it can and should be painless. At Modesta, working around existing ducting infrastructure to install multiple new main duct runs to machines and avoiding downtime are standard practice. Modesta has plenty of experience with negative pressure builtin cascading fans. The Dutch clean air specialist has been building these energy-saving systems since the late 90s and were the first to introduce a chain filter with this technology. Modesta’s team will gladly advise you on the different options available and tailor the solution to your specific business.
CF50 filter
This new model has been developed especially for medium-sized businesses. The system utilizes multiple smaller fan sets (up to 7.5kW) installed on the clean side of the system. This negative pressure filter is cleaned offline, for instance during breaks, with a shaker frame system. The square hopper and double Redler chain conveyor have been proven to be efficient since the 60s.
The beauty of this system is that it has all the ‘cleverness’ of the bigger, higher-pressure systems while keeping the investment lower. The system operates with one control panel monitoring pressure. With the right ducting layout and installation of automatic or manual dampers/blast gates, the system saves energy effortlessly. When a machine is turned on, the damper will open and the pressure in the system will drop. The filter reacts accordingly and simply switches on an extra fan. This works the other way around too. Not running your edge bander? The damper will close and fans will turn off, lowering the energy bill.
The CF50 is mostly suited for business requiring around 20,000 – 50,000m3/h. It only has one integrated control panel so there’s no need for complicated third-party control systems. Return air systems allow for the filtered air to be blown back into the building, making sure warm air is used to heat the factory.
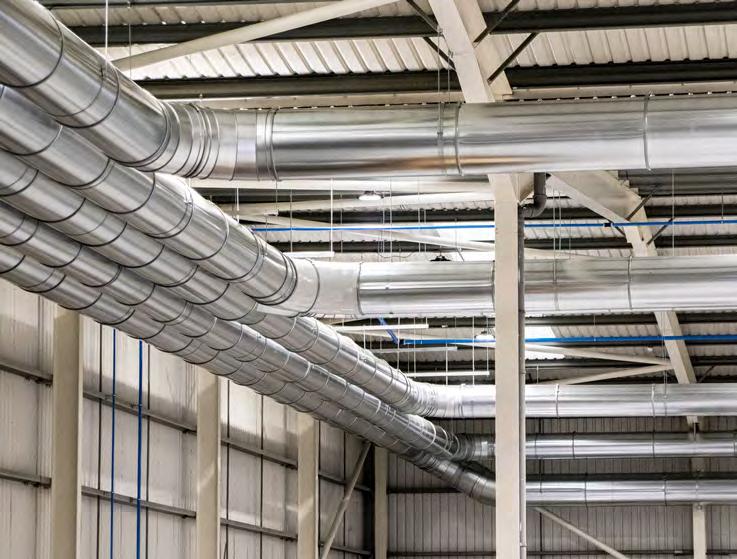
CF80 filter
For higher pressure requirements with operating pressures between 4000 and 5000 Pascals, the CF80 is the solution. Equipped with compressed air cleaning and fan options up to 37kW, these beasts will really blow you away while keeping an eye on your energy usage and wallet. Specifically designed for longer duct runs and CNC machines with higher pressure and speed requirements, these systems will achieve what is necessary without breaking the bank on energy costs.
About Modesta
Modesta is a Dutch family business founded in 1949 and has been serving some of the UK’s biggest interior businesses for years. Run by brother and sister Wyboud and Marianne Kloppenburg, the company has grown into a fullservice business for the wood dust extraction industry. Working together with family-owned Sheffield and Huddersfield-based partner Extraction Solutions, Modesta provides the best and most energy-efficient extraction possible in the UK. www.modestafilters.com
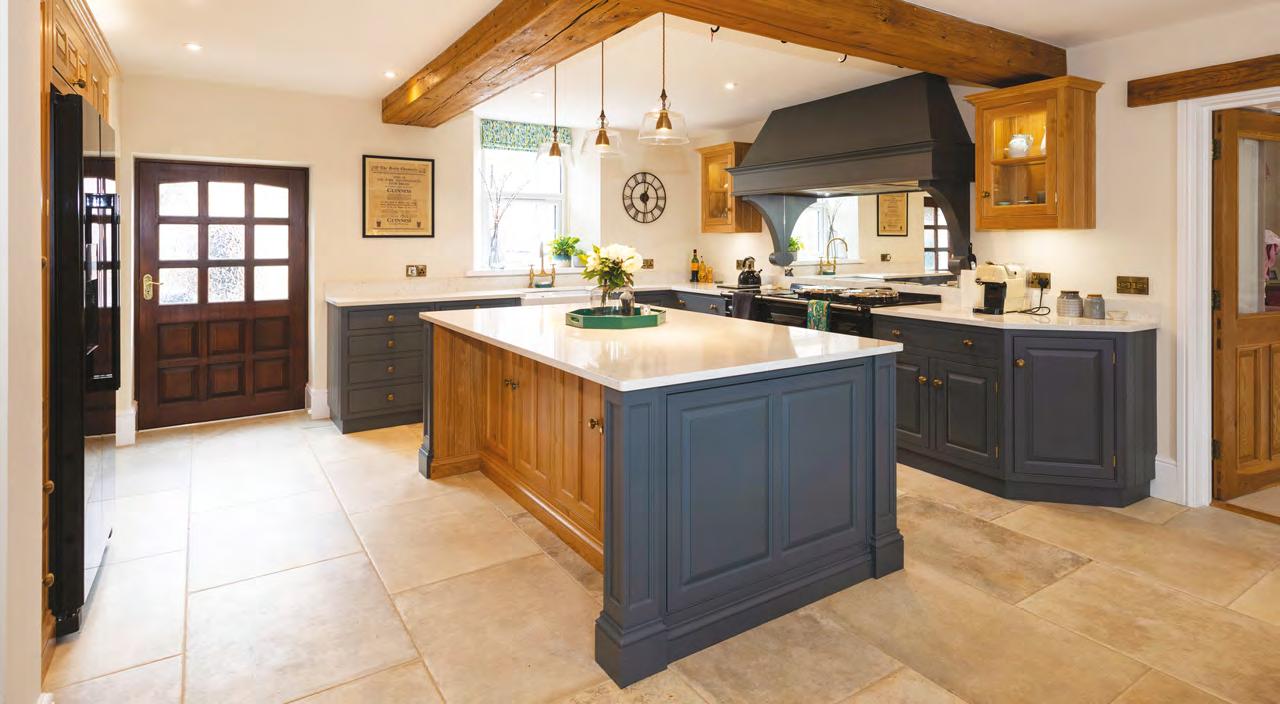
How a luxury kitchen manufacturer managed to lower their electricity consumption, saving them 66,000kWh per year
When Thwaite Holme, manufacturer and installer of quality fitted kitchens and bedrooms, expanded their premises, they contacted the dust and fume extraction company, Extractly Ltd, for help. Extractly used Nordfab ducting throughout the new building and enabled the factory to be reorganised to optimise workflow, giving Thwaite Holme a 35% energy consumption reduction.
CHALLENGE: reorganising the ductwork arrangement to create an optimised workflow for about 40 machines.
Located in Dalston, UK, Thwaite Holme specialise in high-end, luxury kitchen and bedroom furniture; designing and manufacturing quality, bespoke fitted furniture to suit individual tastes and style. Working in traditional hardwoods such as oak, walnut, maple, and ash, the craftmanship and attention to detail is obvious in every piece of furniture.
Details of this nature are not produced on high-speed CNC machines, but crafted on a vast range of individual machines, in fact more than 40 different machines. With all these machines,
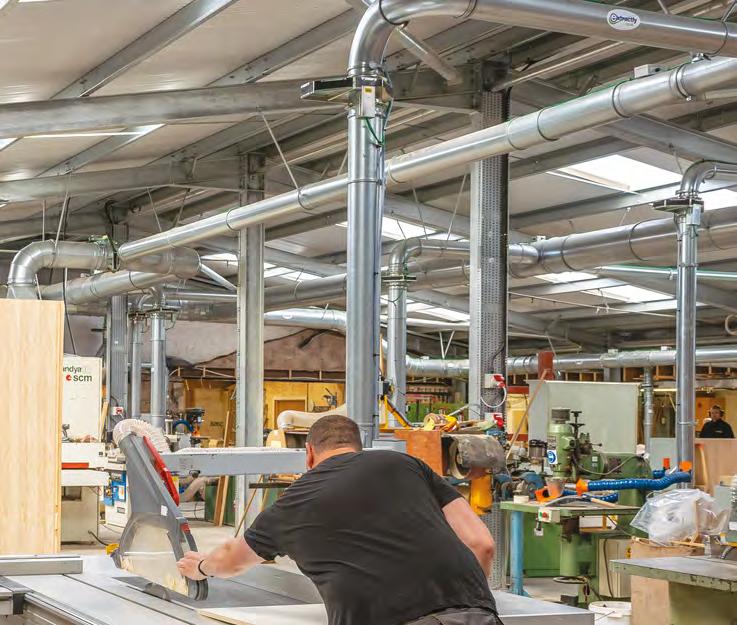
With new ducting throughout, the reorganised
factory gave Thwaite Holme a 35% energy consumption reduction
Thwaite Holme realised they were outgrowing their premises and a new extension were in the planning, giving them more than double the current space.
Now was the chance to reorganise the factory layout and make changes to their extraction system to optimise workflow.
SOLUTION: conducting an energy-saving survey predicting a 35% energy consumption reduction.
When Extractly were contacted they quickly realised, after been shown the newly extended factory, that the task was going to involve much more than an update of the ductwork arrangement.
After a brief inspection of the factory, Extractly carried out a comprehensive evaluation of the extraction requirements, including a full energysaving survey.
With around 40 machines requiring extraction, and yet only a small number of them ever in use at any given time, the potential savings were substantial. The laws of physics, ‘rule of thumb’, is that electricity consumption is halved if fan speed is reduced by just 20% and, with the energy survey having determined that a 35% reduction could be achieved, the predicted savings were substantial.
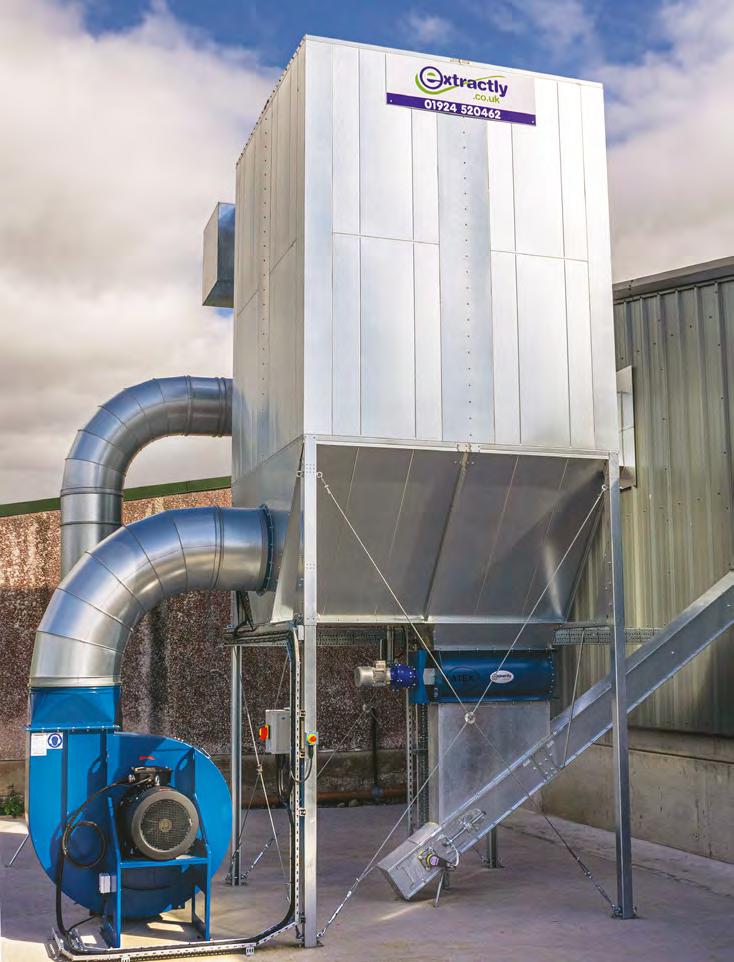
RESULT: 66,000 kWh in yearly savings
For almost 50 years, Nordfab has been used around the world for dust collection in woodworking facilities, from one-person shops in home garages to large manufacturing plants, just like Thwaite Holme.
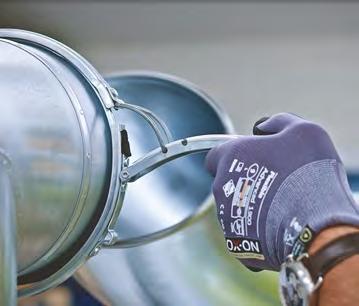
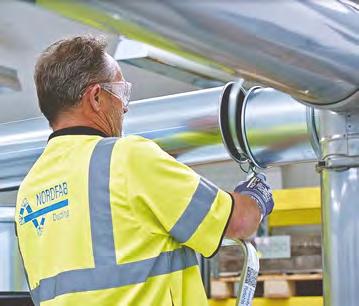
Nordfab is proud to have partners such as Extractly Ltd, who are extremely knowledgeable in LEV, can provide smart ductwork design, and supply and install products. With proven methods and well design products, Extracly managed to let Thwaine Holme reduce their energy consumption with 66,000kWh a year, saving them thousands of pounds every year on electricity costs by using: smart technology, good factory floor design; efficient duct design system using Nordfab Quick-Fit ductwork throughout the factory, connecting equipment to the main ductwork via four separate branches.
A 37kW direct drive fan provides the capacity to extract in excess of 20,000m3 of air per hour, delivering sawdust, shavings and wood chips to be filtered through the externally-sited filter unit.
With the current economic uncertainty in the energy supply market, this yearly savings was a welcoming news for the Thwaine Holme’s owners. 01132 739 400 sales@nordfab.co.uk www.nordfab.co.uk NORDFAB DUCTING IN WOOD SHOPS AND MILLS: A PROVEN APPLICATION
There is no secret that wood shops, small or large, generate lots of sawdust, shavings, and wood chips that would need extraction in order to create clean air for the workers.
Because Nordfab’s Quick-Fit duct is wellconstructed, modular, easy to put together or take apart, and because it is re-usable, it has become a standard ducting in the woodworking industry and for applications just like this with Thwaine Holme. Some of the reasons for why the dust and fume extraction company, Extracly, chose Nordfab Quick-Fit ducting for Thwaine Holme include: • Quick-Fit ducting is very easy to install, the components are assembled with a so called QuickFit clip. • Quick-Fit duct can easily be disassembled for relocation when woodworking machines are moved or changed, or when new machines installed in the shop. Thanks to its sturdy construction, Quick-Fit ducting can be re-used again and again. • Quick-Fit ducting can easily be moved from one building to another. • Leakage is virtually non-existent, resulting in a highly efficient system where the suction is provided to the machines, not leakage in the ductwork.
Superior dust extraction with Elcon wall saws
To help minimise dust exposure to operators, Elcon have developed and patented an awardwinning dust collection system, LIMPIO.
As standard Elcon panel saws have an effective extraction point from the enclosed saw head. The majority of the blade sits within the saw guard during cutting providing adequate dust removal for most operations. When cutting fibrous or cementitious boards such as MDF, Gypsum or GRP on a regular basis, additional extraction methods should be considered to minimise operators exposure to potentially harmful dust.
For maximum extraction efficiency the LIMPIO system includes a rear dust capture tray. With its own secondary extraction point that travels directly behind the saw head whether cutting vertically or horizontally. The point of cut is almost totally enclosed, sandwiched, with the machine extracting dust from both sides of the cut. Dust emission values are reduced to less than 0.5mg/m3 .
The LIMPIO system is available on the majority of the Elcon range. Machines cater for all standard sheet material sizes as well custom built frames for bespoke applications. 0115 986 5201 info@daltonswadkin.com www.daltonswadkin
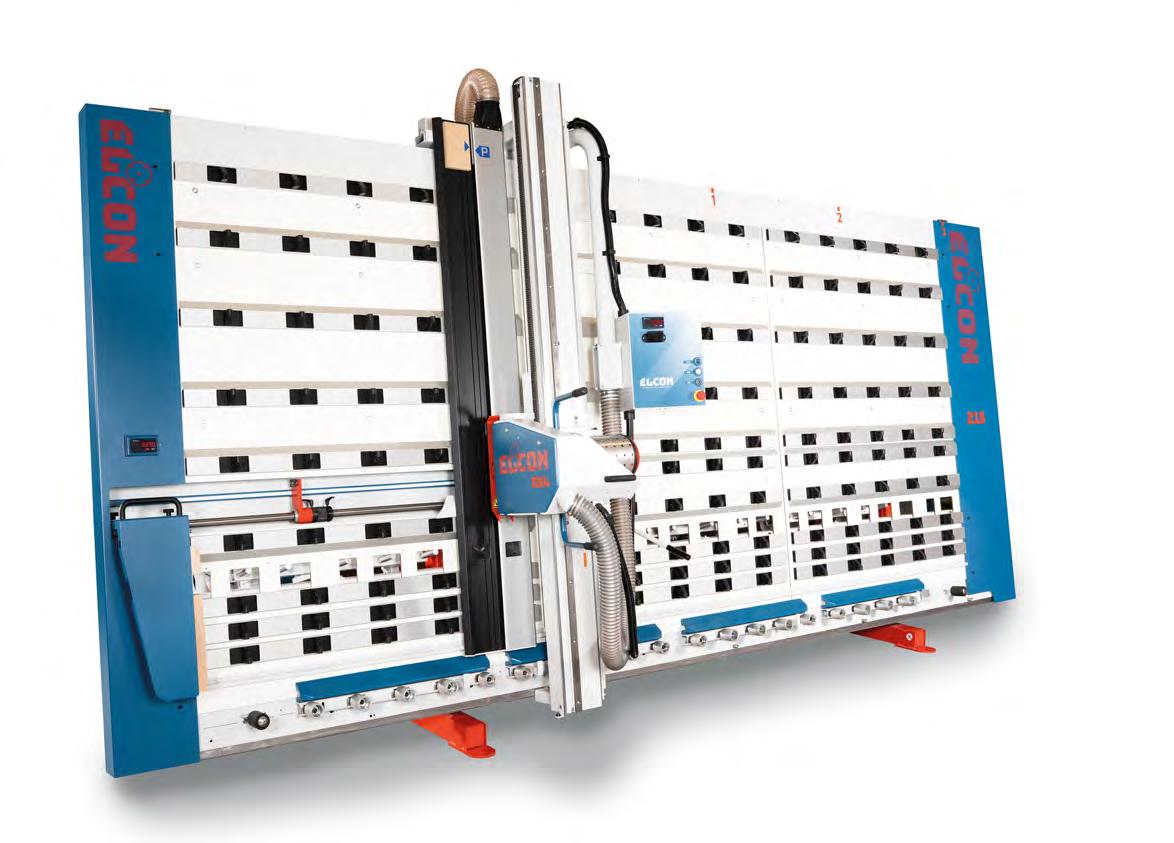
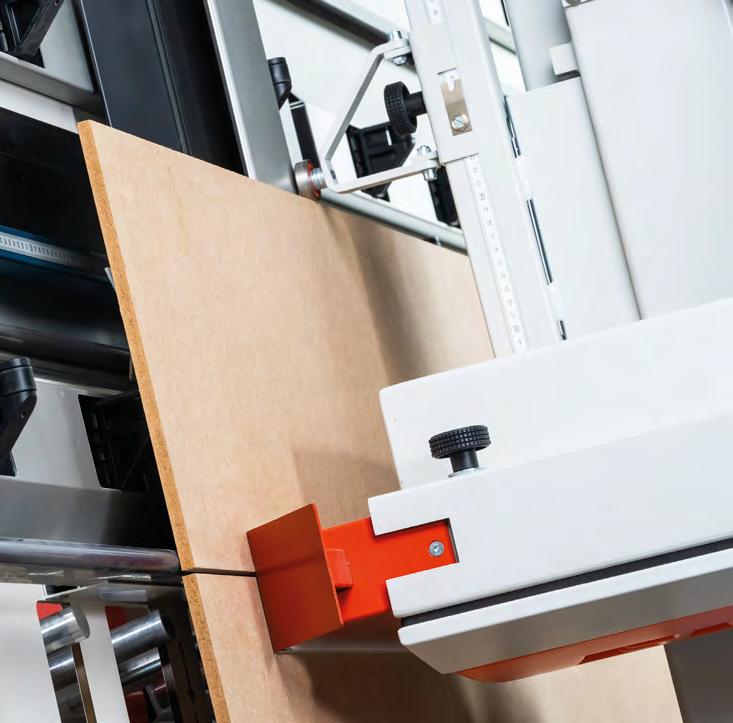
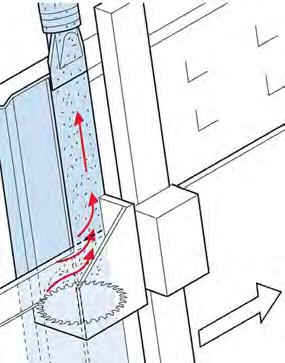
Savings on energy costs has always been at the forefront now with higher and higher energy costs it’s an essential design consideration.
Use less energy, pay less
Chris Franklin, managing director at Ranheat Engineering, one of the UK’s leading manufacturers of industrial wood-waste burning equipment. Continues his series of articles exclusively for Furniture and Joinery production. This month he looks at running costs for wood burning equipment – in particular collecting the wood-waste – as costeffectively as possible.
Energy costs have being thrust to the forefront of design, so how can we reduce running costs within the wood-working industry? In simple terms, use less energy and pay less.
In most modern woodworking factories the largest single electric motor is the dust extraction main extract fan. This draws the wood-waste to a central filter and separates the air from the wood-waste. This fan or in some cases fan sets can be 60-100kW.
The traditional way was then to blow from the filter with a transfer fan to a silo, or a boxcart. Often this fan was 14-18 kW and ran the entire time the factory operated. That’s a lot of electrical consumption!
Transfer fans are sized to cope with the large volume of wood-waste that occurs when the filter system cleans. Some filters have continuous cleaning, cleaning a portion of the dust extraction filters on a rotor system. Less well-designed extraction systems do not have this feature.
Cleaning occurs when the main extract fan switches off at the end of a work period. At this time any fine waste held in suspension drops and could overload a less powerful transfer fan.
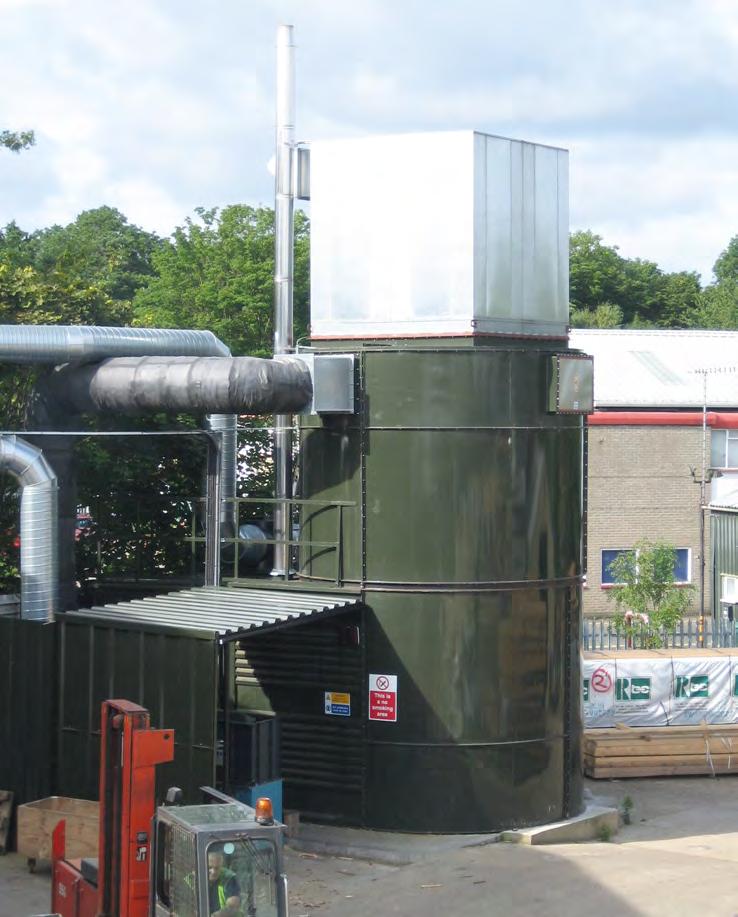
Silo mounted filter system
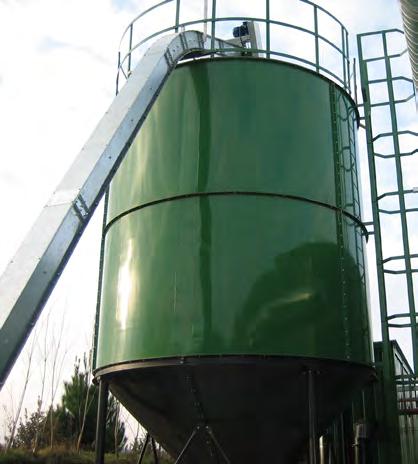
So the transfer fan overloads if not big enough. 95% of it’s running time per day the fan is too big and wasting electricity.
So, what are the alternatives?
One answer is to mount the filter unit directly on the storage silo as shown in the photograph above. The extracted wood-waste falls directly into the storage silo. No expensive to run transfer fan. So how is this achieved? Simple the silo must be strong enough and designed to withstand the weight and the pressure. Ranheat do not make dust extraction systems, but they make silos strong enough to have most makes of dust extraction filter, mounted directly onto the roof of the silo. Not only is this energy saving but also space saving.
So, what if my filter system is too big to fit on the silo?
Consider using a drag-link conveyor. Typically, a drag-link conveyor uses 2.2 -3kW as opposed to 15-18kW.
Using your own wood-waste to heat your factory has never made more sense but in the design of the system it has never been more important to reduce the cost of getting the wood fuel to the combustion equipment.
Ranheat design, manufacture and instal a wide range of industrial silo’s and non- pneumatic transfer systems as low running cost options.
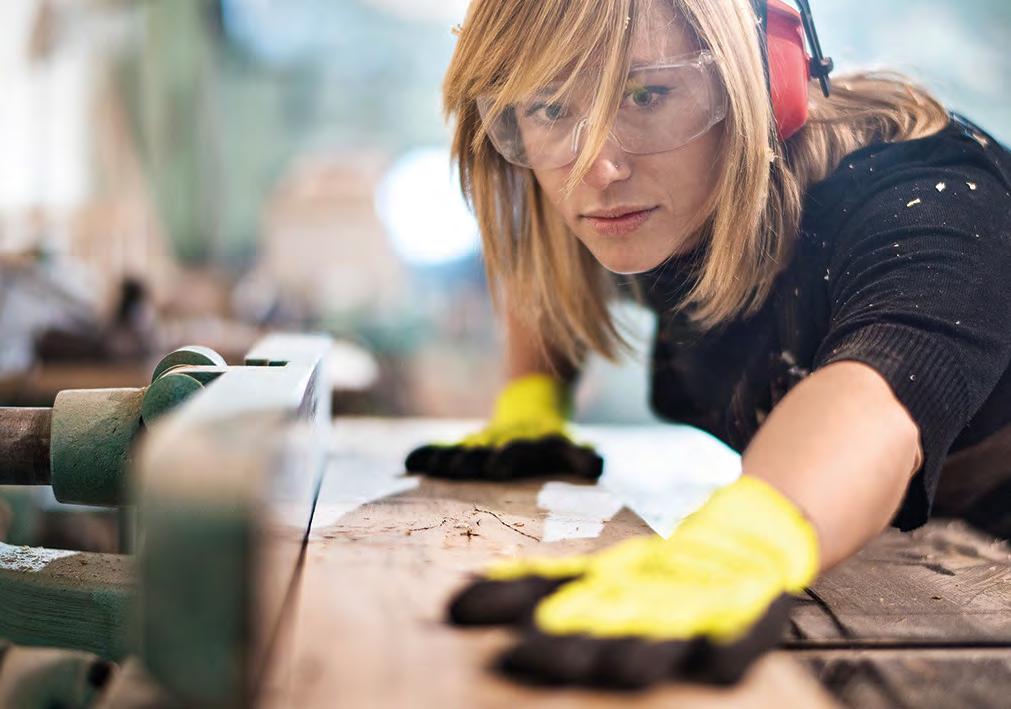
WORLD’S FASTEST DUCTING - NOW EVEN FASTER!
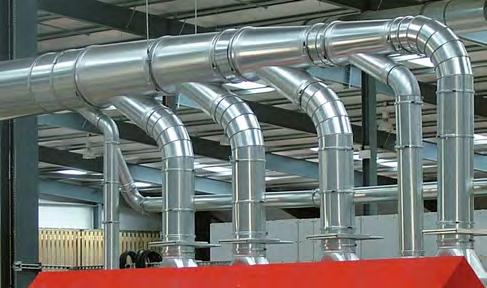
For more than 40 years, Nordfab ducting has been used around the world for dust collection in woodshops, from one-person shops to large manufacturing plants. Because Nordfab’s Quick-Fit® duct is wellconstructed, modular, and easy to put together or take apart, and because it is re-usable, it has become a standard for ducting in the woodworking industry. The new 2-meter length duct makes it more efficient to install ducting, using less joins. In other words, the world’s fastest ducting just became even faster! 2 M
DUCTING
Easy & Fast to install Re-Useable Fits most applications
Because our ducting systems clip together, no rivets screws, or welding are needed. This cuts installation and downtime by more than 45% compared to flanged ductwork installation. Fast Quick-Fit ducting is easy to uninstall and relocate as you move machinery or have other changes in work areas, providing one of the lowest life cycle cost of any ducting product. Friendly Quick-Fit ducting components are adaptable to existing ductwork and Quick-Fit has been used in a wide variety of applications, wherever dust collection or fine particulate transfer is required. Reliable
Energy from waste wood
Holzbau Rohrmoser relies on UNTHA shredding technology to heat its business premises as well as the adjacent residential building
The Rohrmoser carpentry and timber construction business based in Flachau/ Salzburg appreciates the quality of the UNTHA LR700 shredder. The waste wood from the company’s production as well as building sites is processed by the compact shredder into highgrade fuel for a wood-chip heating system. The business and the residential building that joins it cover their energy needs for the winter with the material produced in-house.
Wood is a precious resource and a fuel source produced in Austria, making it crisisproof and renewable. This not only means that value creation stays in the region, but also constitutes a possibility for woodworking and timber-processing businesses to use their waste wood efficiently – as is the case for Holzbau Rohrmoser in Flachau.
“By utilising and shredding the waste wood from our production and building sites as well as from disposable pallets, we are able to dispose of waste wood quickly and use 100% of it as an energy source,” says proprietor and master carpenter Johann Rohrmoser. The business was founded in 1992, employs six people and does general carpentry work, builds wooden houses, car ports, roof structures, balconies and “anything else that comes along,” as Johann Rohrmoser puts it.
LR700: robust, compact, crucial
Rohrmoser first began to use an LR700 unit from UNTHA shredding technology for the shredding of waste wood around Christmas 2016. Johann sees the benefits of the unit in the cutting system with a swivelling pusher and the low maintenance requirements. Waste wood from joinery constructions, splinters from circular saw operations and waste wood from the construction sites are all fed into the shredder and are mixed with wood shavings, resulting in a particularly productive heating material. The chips are extracted into the chip silo straight after the shredding process, where they are stored until the winter, when they are fed into the wood chip heating plant via a discharge system. “The wood chips see us through the winter,” says Johann, who uses the heating plant not just for his business, but also for his home that adjoins it.
The LR700 shredder is filled twice a day and runs for an hour each time. In the three and a half years since the unit was first put into operation, it has completed approximately 250 operating hours. It is the second UNTHA unit in operation at Rohrmoser, where a smaller, twoshaft shredder provided a valuable service over many years. Johann is more than happy with the purchase he made in 2016. He sums up the main features of the unit: “It is robust, compact, and crucial to us in our daily workflows.”
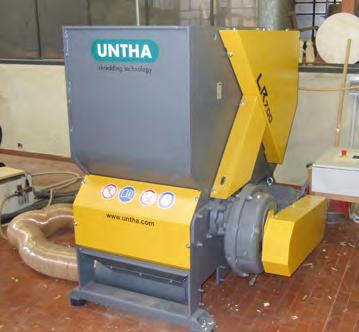
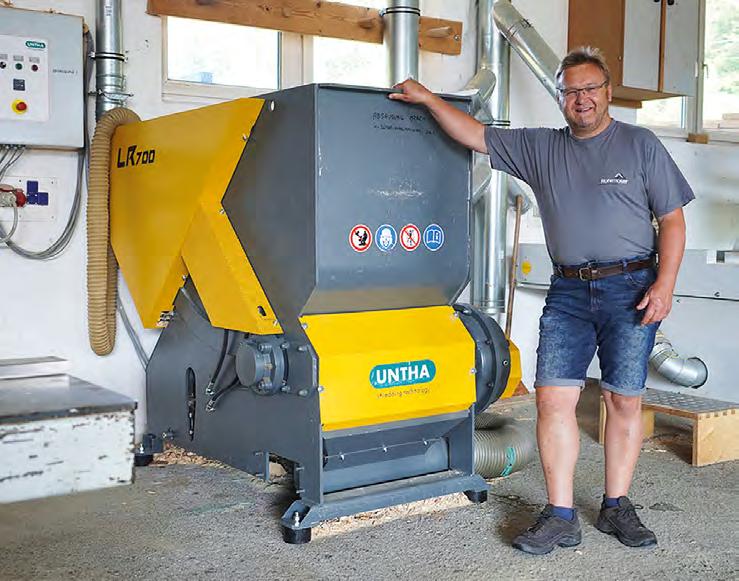
Flexible LR series
With the LR series, UNTHA offers a family of machines that ensure compact shredding for carpentry workshops, cabinetmakers, joiners, sawmills and timber industry businesses of all sizes. These shredders with tried-and-tested single-shaft technology come with rated capacities from 11 to 60kW and fulfil the needs of smaller as well as larger players. Overall, the LR series stands out for its efficient cutting system, longevity and reliability.
All models of the LR series have a high level of efficiency and economy and are maintenance-friendly. For users, this translates into homogeneous wood chips ranging from 12 to 80mm, at a low cost and with little effort in terms of operation. The final product is suitable for wood-chip heating plants and for briquetting, which offers yet another layer of energy efficiency for users who are able to recycle their own residual wood. Thanks to UNTHA shredding technology, users of the LR series are able to make an important contribution to the sensible use of precious raw materials that nature provides.
Reliable shredding technology that goes back more than 50 years!
UNTHA shredding technology develops and manufactures customised, reliable shredding systems that are used in a wide range of applications, from material recycling to processing of residual and waste wood and the reprocessing of waste to produce alternative fuels. In this way, the company makes an important contribution towards the conservation of resources and the sustainable processing and reduction of waste.
The company was founded in 1970 and is headquartered in Kuchl near Salzburg. UNTHA has more than 250 highly qualified employees and a worldwide sales network that spans 40 countries on all continents, placing it among the world’s leading manufacturers in this growing, future-orientated industry.
Testing LEV efficiency at source
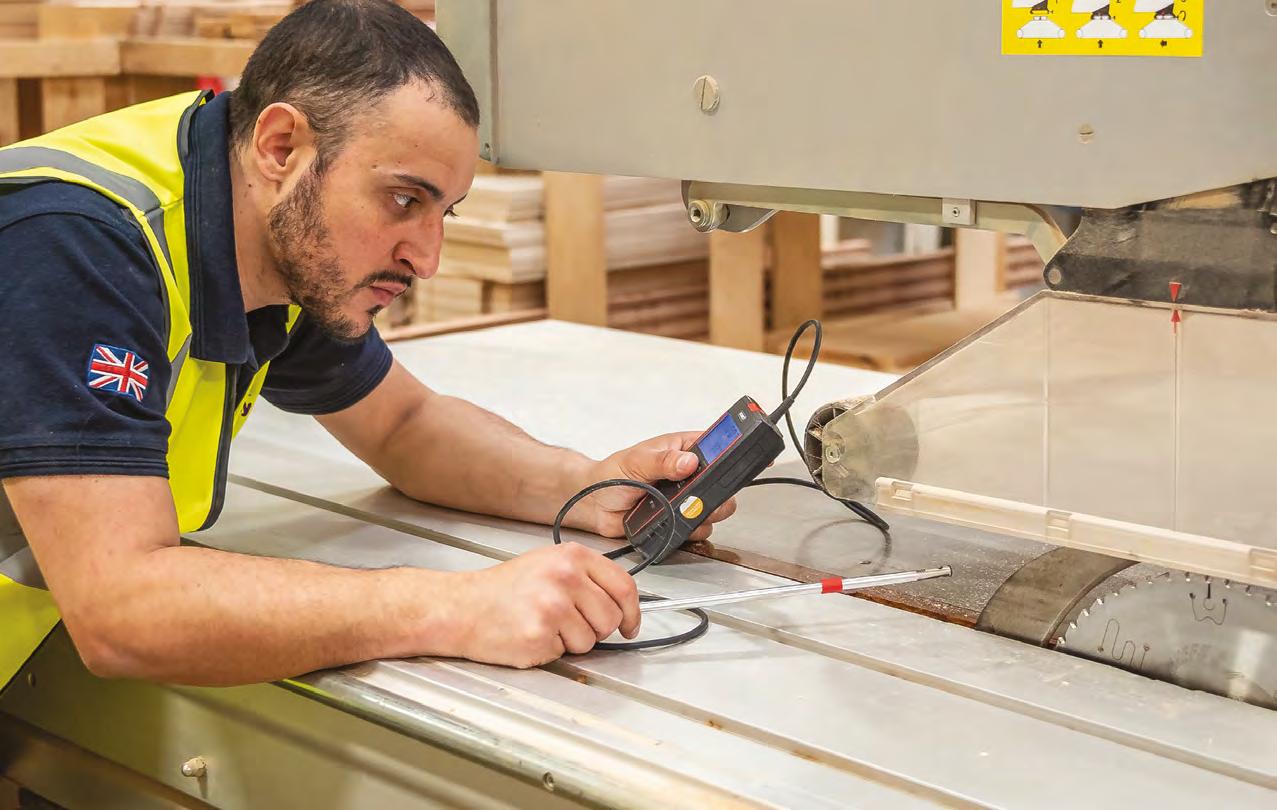
LEV… extractly how it should be
Dust – it’s a dirty subject but, if not controlled effectively, wood dust has the potential to cause serious health problems for workers exposed to the hazard, and it’s something we all have a responsibility to deal with in this industry.
The specific health hazards associated with wood dust are well-documented and regularly reported through the pages of our industry’s media, and the Control of Substances Hazardous to Health (COSHH) Regulations require employers to ensure that the exposure of employees to substances that are hazardous to health is either prevented or, where this is not reasonably practicable, adequately controlled. However, despite all the publicity and the seriousness of potential problems, the Health and Safety Executive continue to report a high incidence of dust exposure regulations being breached by woodworking businesses.
Regulations stipulate Workplace Exposure Limits (WEL) for wood dust based on the average amount of airborne dust present during a nominal 8-hour shift. Since 2020, the maximum WEL for softwood dust has been set at 5 milligrams per cubic metre and, where hardwood dust is prevalent, or a mixture of both softwood and hardwood dust exists, the current limit is 3 milligrams per cubic metre; expected to be reduced to 2 milligrams in 2023.
Since wood dust acts as a respiratory sensitiser, it’s essential that employees’ exposure to dust is not just maintained below the relevant WEL, but that any exposure to wood dust is minimised as far as is reasonably practicable – a respiratory sensitiser is a substance which, when inhaled, can trigger an irreversible allergic reaction in the respiratory system and, once such a reaction has occurred, even the slightest repeat exposure to the substance may produce symptoms.
In a woodworking factory it’s the fine particles of wood dust that are most likely to cause lung damage but, when fine wood dust is airborne, it’s practically invisible. Just to put the exposure limits into perspective, one teaspoon (5ml) of dry
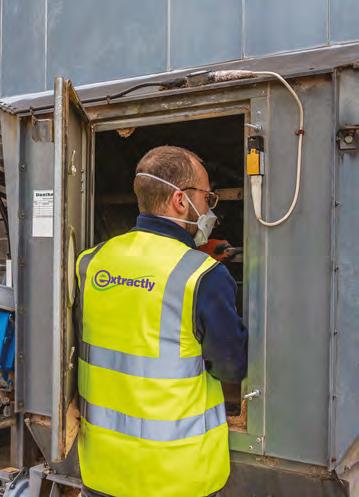
Internal inspection of customer’s filter unit
sawdust typically weighs in at around 1 gram, or 1000 milligrams; which means that 5 milligrams of sawdust per cubic metre equates to around one fiftieth of a teaspoon (0.1ml).
When measured in those terms, it’s not hard to appreciate why such a small amount of dust is difficult to see when it’s floating around in a million cubic centimetres of air, and just how effective dust extraction needs to be to control the hazard.
In order to capture the harmful dust at source, and remove it before it can spread, adequate dust extraction, or Local Exhaust Ventilation (LEV), must be provided wherever woodworking machines are in operation and, crucially, it must be maintained in tip-top condition. There’s a legal
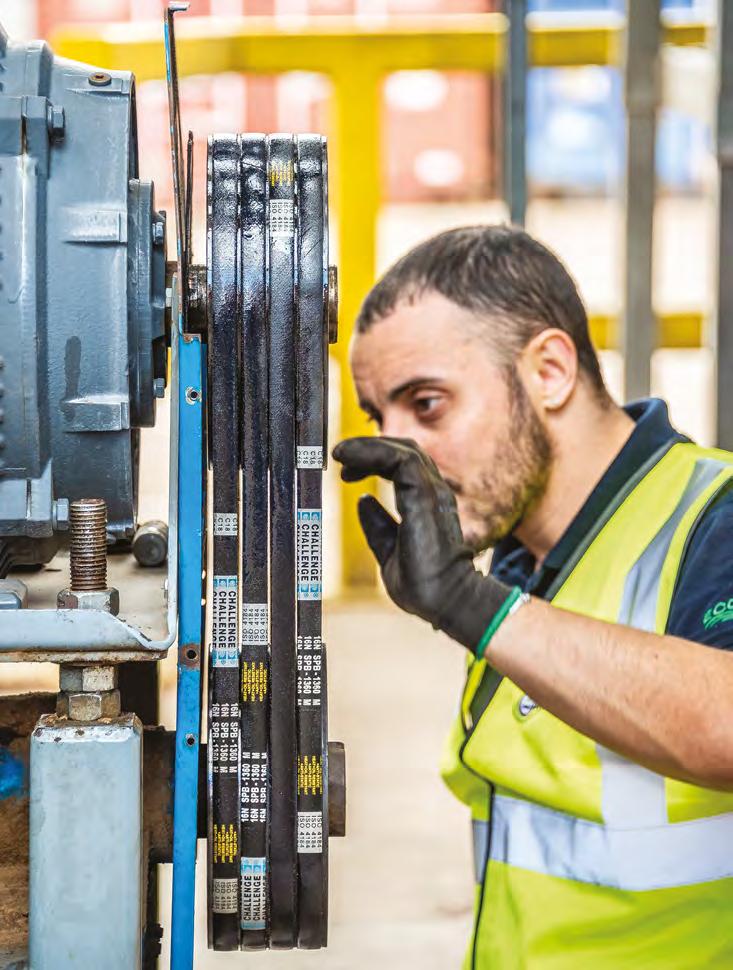
Ecogate system maintenance
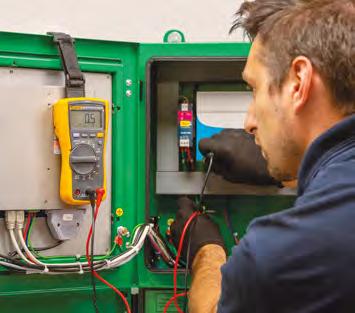
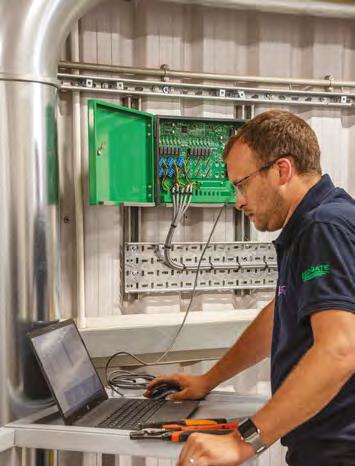
requirement for LEV systems to be examined and tested, by a competent person, at least every 14 months and, especially for complex systems, more frequent checks are strongly recommended. A reputable dust extraction provider will advise on LEV Testing requirements for an individual system based on how complicated the system is, how likely it is to fail, and the consequences if it does.
Extractly Ltd has a highly-dedicated and experienced in-house service team to support its customers in the woodworking industry. The team’s knowledge and skills have been honed and developed through years of experience with countless LEV system configurations and extraction equipment from a myriad of manufacturers. Whether your dust extraction was installed by Extractly or another provider, the service delivered will be customised to meet your specific needs; ensuring maximum uptime and optimum performance from your system, and safeguarding the health of your workforce.
Extractly have the capability to meet all your
Checking fan belt condition and tension
LEV requirements: whether it’s for regular testing and maintenance, updating an existing system to provide additional extraction capacity for new machine installations, to design, install and commission a new and efficient dust extraction system, or simply to reconfigure ductwork to accommodate a machine replacement or relocation.
In addition, as the sole UK Distributor of Ecogate energy-saving extraction equipment, Extractly is uniquely-placed to provide a one-stopshop solution, covering all your dust extraction requirements. Ecogate technology is highly effective when it comes to maintaining optimum airflow in an extraction system and, with fan speed automatically and continuously adjusted to exactly match extraction demand throughout the working day, it is guaranteed to significantly reduce your system’s power consumption and running costs. 01924 520462 info@extractly.co.uk www.extractly.co.uk
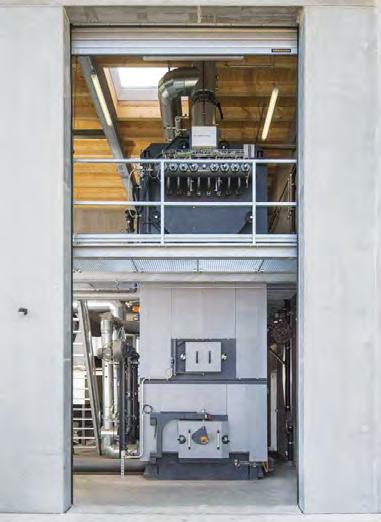
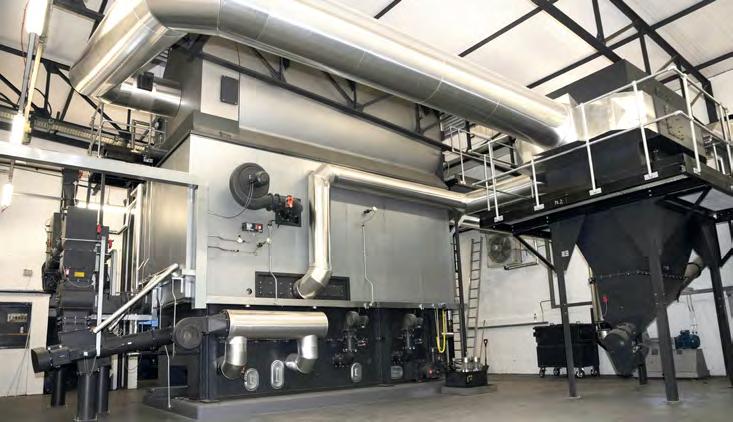

RHI APPROVED
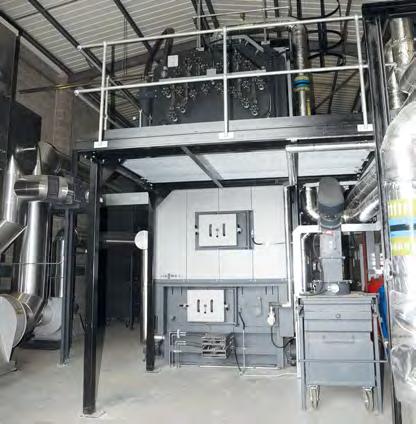

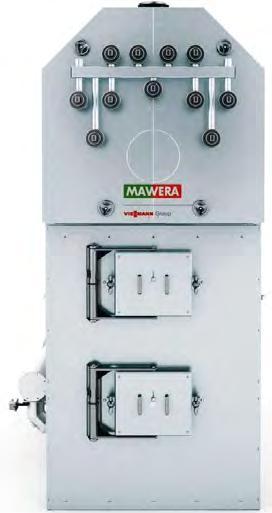
Wood fi red boilers from 110kW to 13000kW
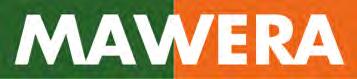
…energy from wood
MAWERA UK LTD PO Box 5581 Lichfi eld, Staffordshire WS14 4FS Tel: O1543 258844 Email: info@mawera.co.uk www.mawera.co.uk
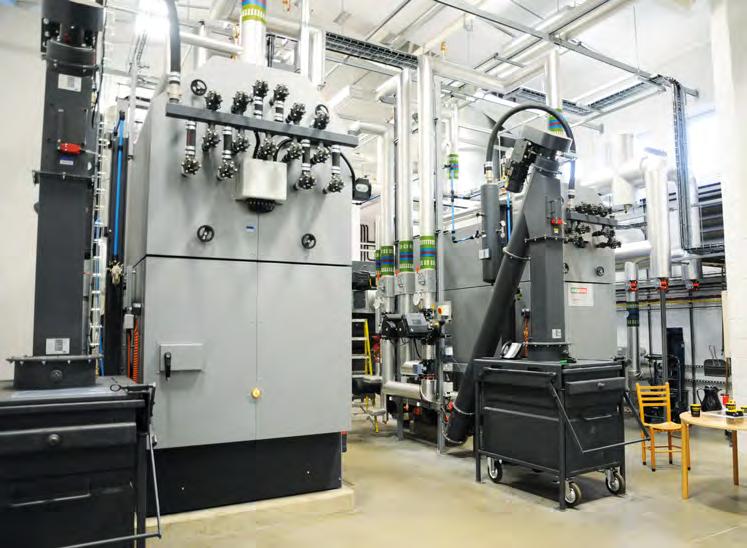
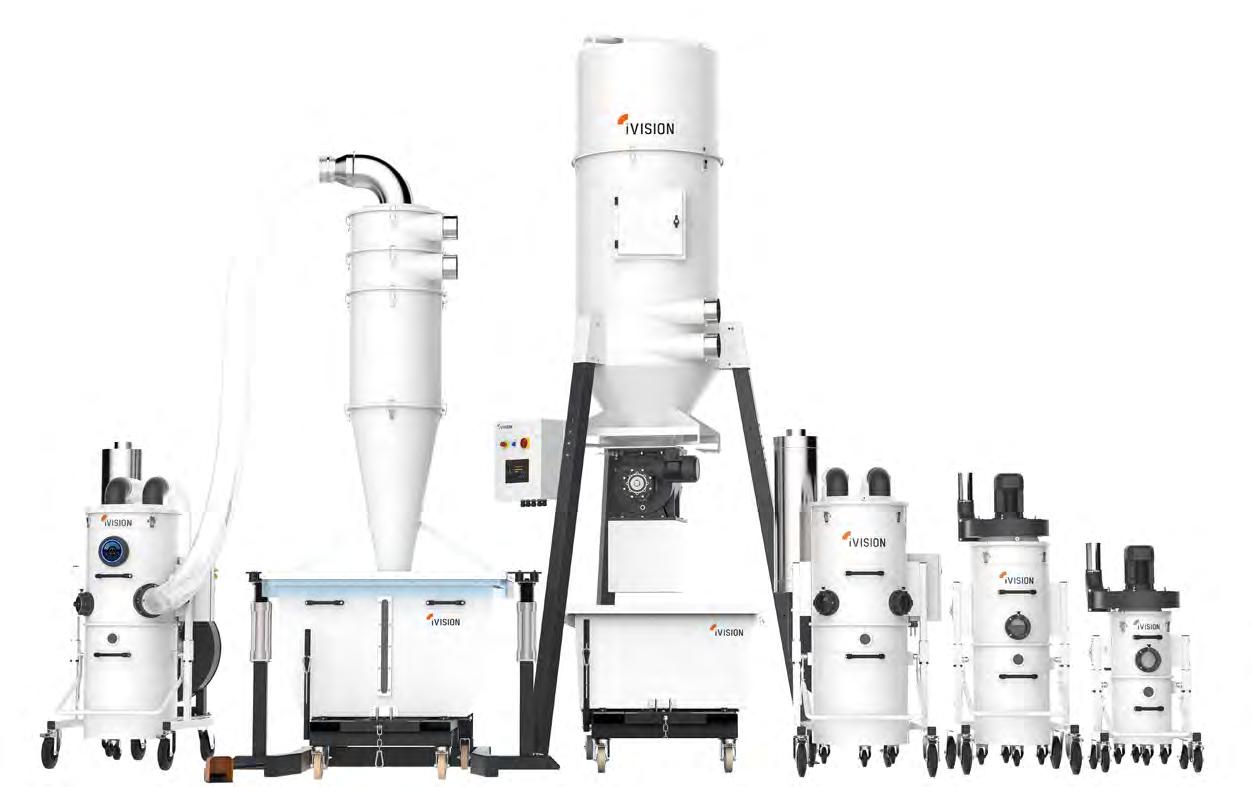
Dust exposure: We need to stop ignoring this silent workplace killer
The woodworking industry has always been a dangerous place to work. Most people attribute that to the number of accidents and the nature of the equipment that we work with. After all, the industry is second only to farming in terms of accident rates.
Historically, emphasis has always been put on addressing the most obvious dangers in woodworking, but did you know that there’s another extremely dangerous aspect of woodworking that often goes unnoticed? In fact, it can actually lead to occupational asthma, lung disease, and even cancer.
Each year, around 12,000 people die from work-related lung diseases linked to past exposure to hazardous substances at work. That includes dust exposure.
But the problem isn’t being resolved. In fact, it’s getting worse.
Back in February 2022, HSE (Health and Safety Executive) released a report that showed over 50% of the 200 woodworking businesses they visited in the last two quarters were breaching dust exposure regulations.
We know that dust exposure doesn’t sound too threatening on the surface, but there is a major lack of understanding when it comes to dust extraction and how to make it efficient and safe.
We need to make a change
Alex Dalton, director at Daltons Wadkin, explains how his personal experience in the industry led him to believe that businesses weren’t taking dust exposure seriously.
He said: “We’ve suspected for a long time that the LEV (Local Exhaust Ventilation) side of workshops could be improved generally throughout the UK. From my own experience as a salesperson in the early part of my career, going into different businesses to talk about different machine solutions, it would not be uncommon to walk in and see piles of wood chippings and high dust accumulations on work surfaces and window sills
“Without making any excuses, it’s the way the industry has been for a long time. It’s very traditional - the methods followed now were also followed years ago. There’s been a real lack of progression given the modern data and findings we now have access to,” says Alex.
What does dust exposure actually do?
Wood-dust inhalation is included in the figure of 12,000 people dying yearly from work-related lung diseases. It’s not uncommon for inhalation to cause occupational asthma and in the case of hardwoods, sinonasal cancer.
It’s clear that these deaths are absolutely preventable, but it will take businesses putting in the effort to ensure that any exposure is effectively controlled.
Why has dust exposure become such a prominent issue?
Employers working with woodworking equipment know that they have to have their LEV systems checked every 14 months, but with deaths and safety breaches becoming
more common, it has led the industry to wonder whether regulations are truly being followed.
These machines are often in large workshops, and they may just be sitting in a corner of the room. Even if they’re tucked away, it doesn’t stop how quickly they can distribute dust around the whole working area. Even if you are working in another area of the workshop, you are still exposed to that dust regularly.
Alex explained in more detail how uncared-for machines can cause issues: “A lot of systems are designed and installed to service a certain number of machines but over time workshops evolve, equipment is added dust extraction systems modified in-house along the way. When that happens you can lose efficiency very quickly and expose workers to excessive amounts of dust in the workplace. It’s a slippery slope.”
“Depending on the type of material that is being cut and the type of machine being used, it can be extremely obvious that large volumes of dust are being created, but in other situations, it isn’t quite so obvious. Regardless, it is still there, still airborne, still present and workers are breathing it in all day,” says Alex.
How can you protect yourself and your employees?
It’s a law that all woodworking machinery should be LEV tested at least every 14 months, but Daltons Wadkin recommends that LEV systems should be tested every year.
“We have a growing number of service engineers who are trained LEV testing engineers with all the equipment and qualifications that are required,” says Alex.
“Our P601 qualified engineers come out for routine LEV testing for our customers when required and that can be incorporated into general machine maintenance plans too, so we know that all of our customers get the most efficient and safe service possible.
“We also offer a range of dust extraction solutions. To serve individual machines we offer Ivision units; special high-pressure systems from an Italian-based manufacturer that specialises in dealing with all different types of airborne contaminants or material wastage generated from cutting - not just woodworking dust, but also plastics, composites and metal. They offer a wide range of solutions to work with machines that we sell.
“Beyond that, we will always encourage customers to opt for a fully integrated LEV system. These are stand-alone, purpose-designed, extraction systems with externally located collection bins complete with purpose-built ducting and manifolds to suit each machine. Flow rate gauges can also be installed at each machine to give operators a quick visual indication of whether the system is working optimally.
It’s time to solve the problem
“The solutions are clear, but if the whole industry doesn’t make active improvements to deal with dust exposure and extraction, then the problem will only get worse,” says Alex.
“Looking after the health and well-being of our employees is extremely important to us, and we want to help other businesses in every way we can to make sure we stop dust exposure from being a premature cause of health issues.”
To find out more about how Daltons Wadkin can help with dust exposure contact Alex and the team on 0115 986 5201, email info@daltonswadkin.com or visit www. daltonswadkin.com
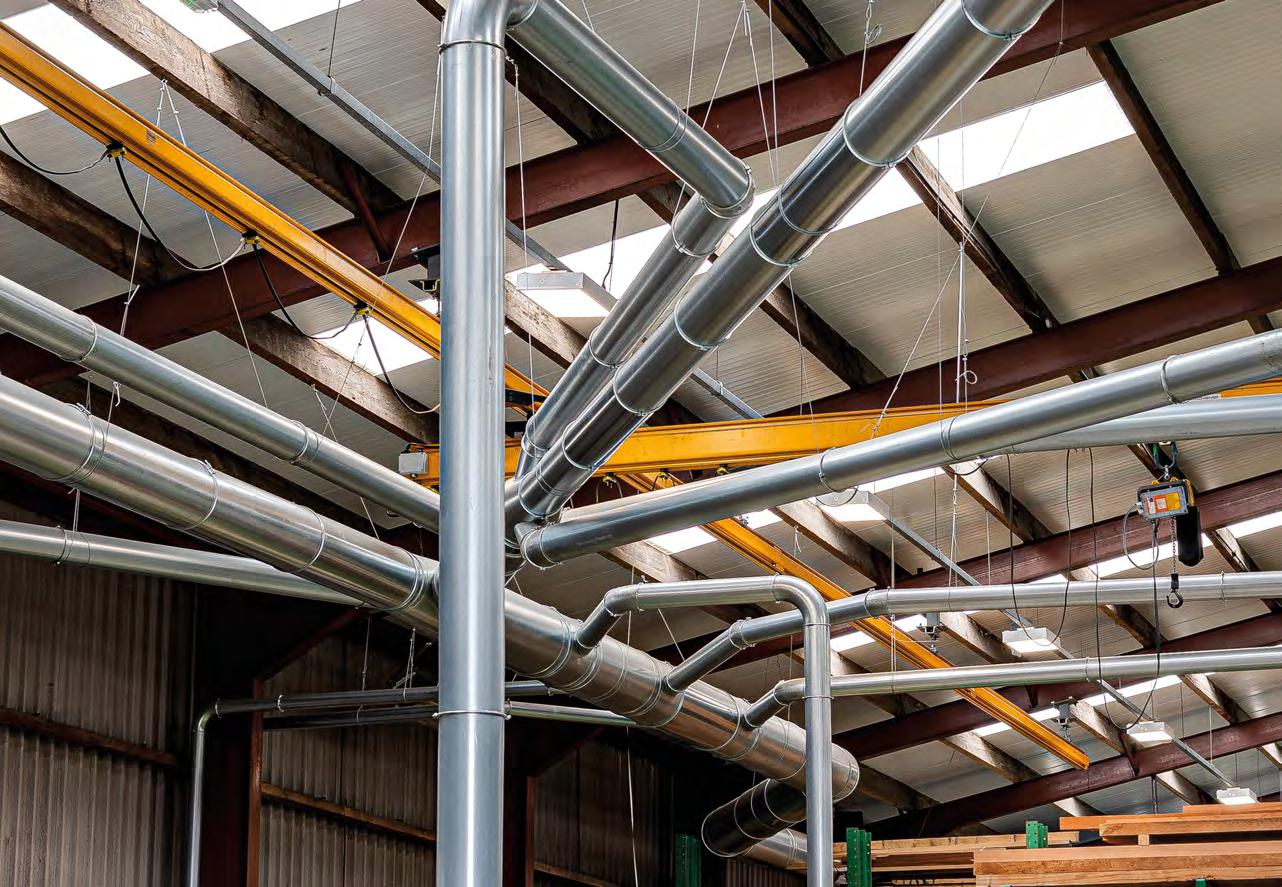