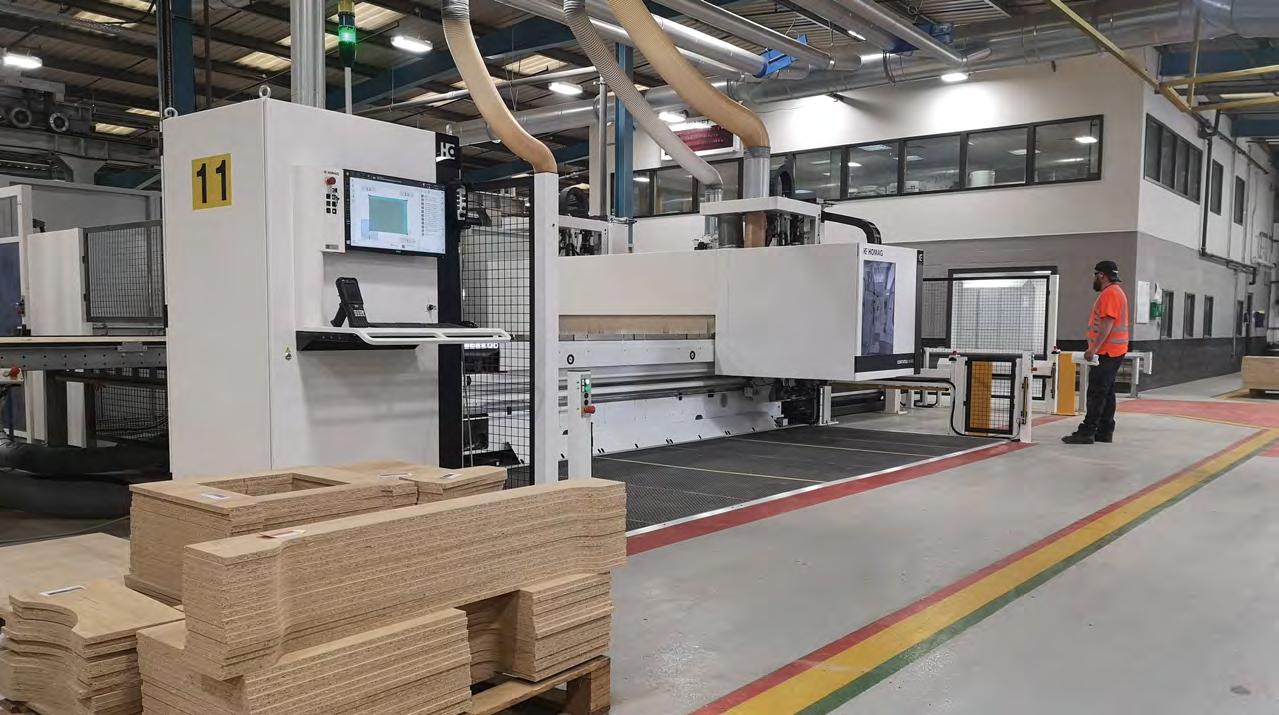
4 minute read
The Swift Group partners with HOMAG to completely redesign its production facility
Founded in 1964 by Ken Smith, the Swift Group has grown to become one of the largest manufacturers of caravans and holiday homes in the UK. With a turnover in excess of £300m, it is unique in that it operates in all three sectors of the market – caravans, motorhomes and holiday homes. The development of the business has been built on the simple principle of making products that innovate in the key areas of design, quality and value for money.
In 2021 Swift undertook a review of its machining facilities with a view to improving the efficiency and production output of this part of its manufacturing process.
“We were experiencing high product demand and needed to significantly increase our manufacturing capacity,” explains Swift Group’s CEO, James Turner. “The easiest solution would have been to simply replace the existing machinery on a like for like basis. Whilst this would have improved our capacity in the shortterm, it wouldn’t have given us the kind of stepchange we envisaged for the long-term growth of the business.
“In assessing the situation internally, we developed a vision for the Swift Group that would require a complete redesign of our existing machining facility and the work flow through it. The vision was driven by five key factors: the need for growth, improved efficiency, a single directional work flow through the facility, simplified processes and the replacement of the current machinery.”
Team work – a vital ingredient for success
“Once we agreed a strategy to drive the business forward, we appointed an internal team consisting of Lee Atkinson, (Head of Manufacturing), Graham Jacobs (Head of Facilities) and Paul Cowell (Senior Machine Shop Manager) to work alongside Phil Pitchford and Alan Betteridge from HOMAG UK. Working closely together, they were able to design a solution that would end up putting Swift at the forefront of the leisure vehicle and holiday home manufacturing market.
“The remit was clear; HOMAG had to deliver a number of essential elements including a high output saw cell with a compact footprint; a production cell with multiple nesting CNCs to machine Swift’s many components; a high output nesting CNC for machining melamine faced chipboard (MFC) panels for holiday homes and several edge banding machines to provide additional capacity for processing both curved and straight panels.
“With the floor area of our machining facility limited to 3,200m2, fitting the number of machines necessary in the desired work flow pattern was no easy matter. The new cells had to deliver high output with high quality finishing. It was important, therefore, that the machines offered fast rates of acceleration and rapid feed speeds to minimise cycle times.
“The solution also had to ensure that workforce safety was of the highest priority. One consequence of this was the elimination of the manual handling of large, heavy panels. The set-up, therefore, had to provide safe transfer of these unfinished panels from the storage area to each of the CNC processing machines without the need to use forklift trucks in the production area.”
Specifying and ordering more than 15 machines
With the layout of the cells agreed and specifications of each machine finalised, orders were placed. They included seven CENTATEQ N-700 CNC nesting machines with end-on loading and reduced length outfeed tables to minimise the footprints.
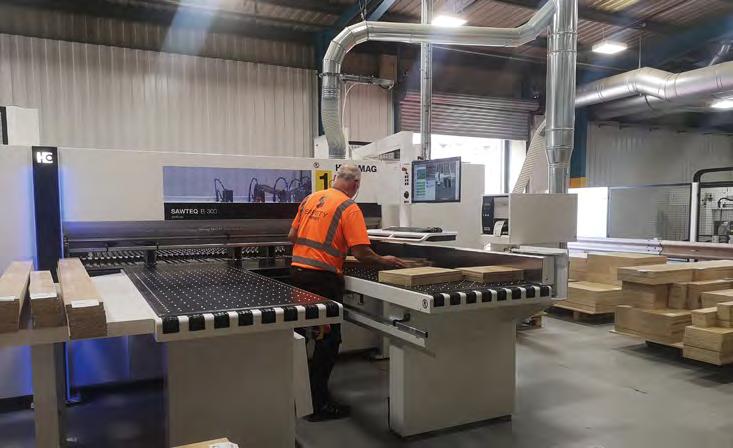
These N-700 CNCs would be fed with large panels direct from storage via a clever trolley system running on rails in the floor and moved by the operator to each machine as required. Additionally, orders were placed for two four-axis twin head gantry CENTATEQ N-600 Concept 2 nesting CNCs with scissor tables.
For the high output saw cell, Swift ordered a SAWTEQ B-300 angular panel dividing saw. This saw is designed to handle high volumes with maximum precision in continuous operation. Completing the order were two EDGETEQ T-100 edge banders, an EDGETEQ T-200, both for shaped parts post-processing, and the highly flexible EDGETEQ S-500 edge bander which provides both PUR and airTec glue options. This cell was finished off with a LOOPTEQ O-300 automated return system for speed and efficiency.
James Turner takes up the story again, “Delivery of the machinery was phased from August 2022 through to May 2023. The project team did an exceptional job planning the removal and disposal of the existing machinery, whilst scheduling the deliveries and installation of the new equipment.
“In the end, every single piece of machinery in the facility was either replaced or moved. Yet throughout the disruption the manufacturing team never missed a delivery date for components, such was the level of planning and attention to detail.
“The HOMAG engineers who installed the machinery did an outstanding job. The machines were commissioned and our operators trained with the minimum of fuss. It speaks volumes that within a week we were fully up to speed with each new production cell as it came on stream. I have to say, the results have been impressive.
Efficient solutions deliver an additional 25 percent capacity
”The cycle times on the new machinery show substantial improvements over the previous set-up,” says James. “We are already seeing capacity increases in excess of 25 percent and the entire manufacturing operation is far more efficient than before.
“When we decided to partner with HOMAG on what was a colossal project, we did so for three very clear reasons: the performance of the HOMAG machinery and software; the reliability – the build quality of HOMAG machines, and the excellent service and support offered by the HOMAG team both in the UK and Germany.
“We have taken out a service contract with HOMAG which gives us complete peace of mind. The HOMAG engineers regularly service the machines and make sure they are all in tiptop condition, keeping downtime negligible. The fact that we have a large number of the same machines means we can hold key spare parts on site further protecting ourselves from potential production interruptions.”
A partnership for the future
“It’s been an exciting ride to say the least, but working in partnership, both companies have risen to the challenges this ambitious, £2.2m project has thrown up. Due to the meticulous planning there have been very few issues, which is evidence of the hard work both teams have put in. It also underlines the fact that with HOMAG, we have a committed partner for the long-term.
“The result of this teamwork is clear to see. Not only do we have a manufacturing facility that will support the growth of the business for many years to come, but also it is one that leads the market in leisure vehicle and holiday home manufacturing,” concludes Turner.
For a demonstration or further information on any HOMAG woodworking machinery or software, contact Adele Hunt at HOMAG UK on 01332 856424 or email: info-uk@homag.com www.homag.com www.swiftgroup.co.uk
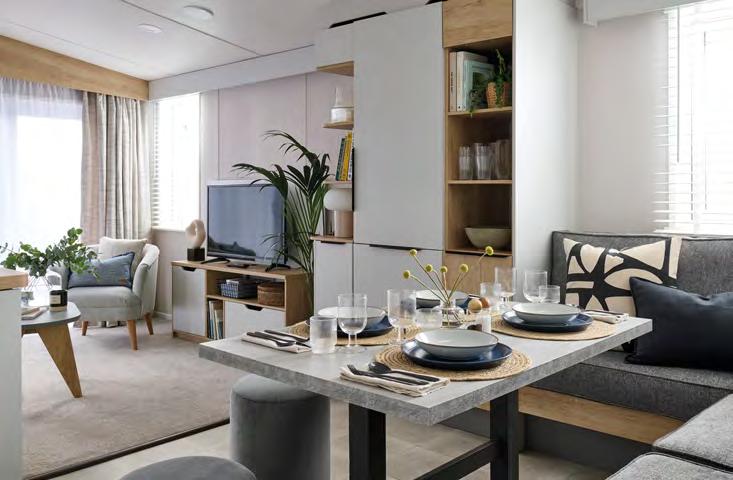