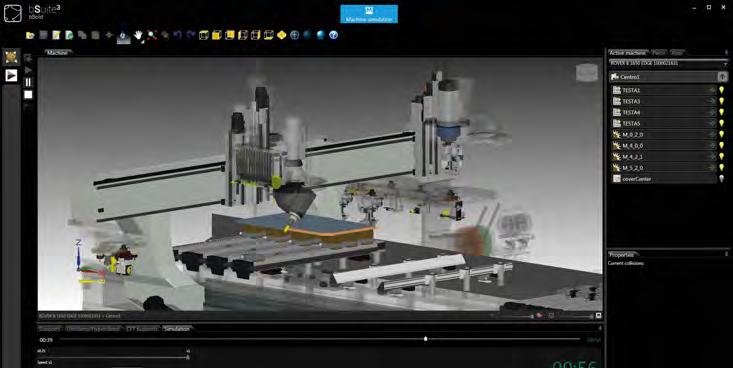
3 minute read
Digital twin simulation software delivers hard benefits to CNC users
Prevention of costly collisions and accurate calculation of job lengths are just two of the benefits of digital twin simulation – available to CNC operations via Biesse’s B_SOLID software. Software is often overlooked as a way of driving efficiencies and reducing CNC processing errors. This is mainly because many furniture and joinery manufacturers have experienced the limitations of manual coordinate-based software, whose lack of 3D functionality precludes five-axis simulation.
A sharper simulation tool
However, in recent years, software has advanced significantly, opening up new opportunities for a value-driven approach to CNC software development. Biesse has harnessed these advancements in the shape of its B_SOLID software, which allows machining operations to create a digital twin simulation of the CNC process. With B_SOLID, powerful processing, sophisticated 3D visuals and machine learning capabilities combine to elevate machine software functionality to a new plane.
What does B_SOLID actually do?
B-SOLID gives users a unique view into their CNC machine by creating a digital twin – that is a virtual replica of their real-world machine. Working on the machine’s control panel or on a remote PC, the user can use B_SOLID to design a machining programme for a particular project – whether that is a kitchen, office, bathroom or shop fit. They can then run a rapid and realistic 3D simulation of that programme – de-risking the project by verifying the feasibility of the intended tool path, machining speed and tool selection, and giving an accurate estimate of job completion time.
Collision Control: accident prevention
Unfortunately, clashes between the machine head and work table do happen, particularly during five-axis work, and they have costly consequences – often resulting in pods having to be replaced and damage to the operating unit itself. Historically, to safeguard against collisions, CNC users have run the programme very slowly using a controller – however, this is less than ideal as it eats into valuable machining time.
B_SOLID’s Collision Control feature, which allows users to run the programme in a virtual environment, is the solution to this issue. A collision check carried out in an office setting will highlight any contact between machine parts, enabling the user to correct any errors and amend the programme without any actual damage being inflicted.
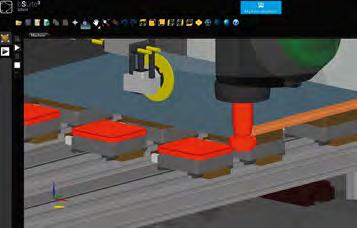
The reason the software is able to calculate whether a collision will occur is because the virtual machine’s parameters and specification are a mirror image of the actual machine – right down to the profile of the tooling and the axis movements.
The sophisticated tool visualisation functionality within B_SOLID is key to this feature. Users can build a visual profile of every tool and aggregate that is available on their machine, along with all of its associated data, and store this within the software’s tool register. They can even assign the tool a cutting edge and a noncutting edge, a rotating speed (RPM), a diameter and – crucially – a length.
Job length calculator: assisting scheduling, staffing and costing
Simulation is not only handy when it comes to preventing collisions, it also means CNC users can calculate exactly how much time will be needed to carry out the required machining operations. This knowledge is extremely useful for pricing purposes – if a kitchen manufacturer knows exactly how a long it will take to machine the panels for each cabinet in a scheme, they can use this as the basis for their costing process. This feature is also helpful when planning staffing and scheduling jobs. Within B_SOLID it is possible to create a ‘work list’ of jobs for a particular machine and the software will calculate how long it will take to run this list of programmes.
With previous generation software, it wasn’t possible to calculate job lengths to the same degree of accuracy because simulations were only able to show the machining cycle. The simulation that can be performed via B_SOLID is far more advanced, taking into account variables such as ramp up and ramp down speeds as well as tool changes to emulate a real-life machining operation and build an accurate picture of overall job time.
On-site CAD drawing capabilities
Typically, furniture manufacturers will obtain a CAD drawing of the project and import that directly into the machine software. However, if errors are detected or changes to the design are required at this stage, the CAD drawing has to be sent back to the originator and amended. With B_ SOLID this isn’t necessary. Users can manipulate CAD drawings within the machine’s drawing tool, without the need for additional software. This saves time going back and forth to the customer when changes need to be made.
This functionality also extends to imported files from third party software providers. These files are imported as a native Biesse CIX file and therefore can be manipulated in the same way as an original Biesse part programme and can be integrated into the simulator and work list.
How can I get B_SOLID?
Part of Biesse’s B_SUITE range of advanced software solutions, B_SOLID is supplied as standard with any Rover CNC machine. Following a feasibility study, existing machines can also be upgraded to run B_SOLID. www.biesse.com
Adhesives A Wide Range For Every Application
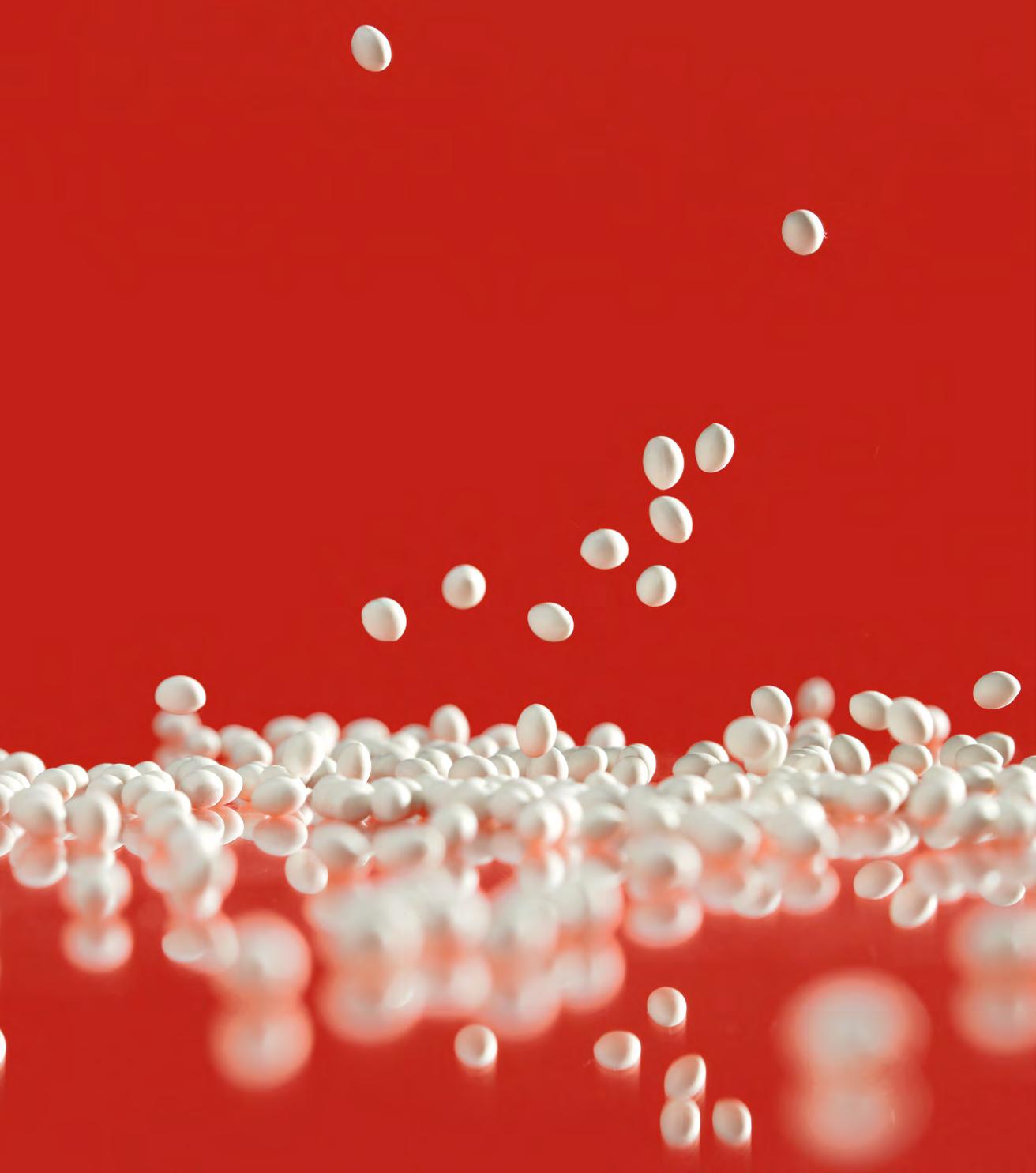
We offer an extensive selection of different hotmelt, PUR, contact and special adhesives, white and wood veneer glues, plus the appropriate application devices and cleaners for your project. In addition, you will also nd practical user tips from our experts.
For further information, go to www.ostermann.eu and type in
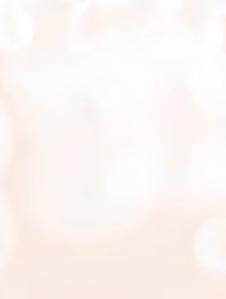
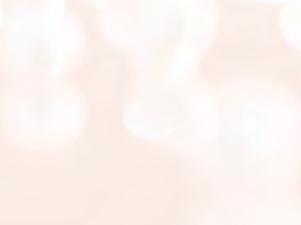
#adhesives
SERVICE, DIVERSITY AND SPEED - THAT IS OSTERMANN.