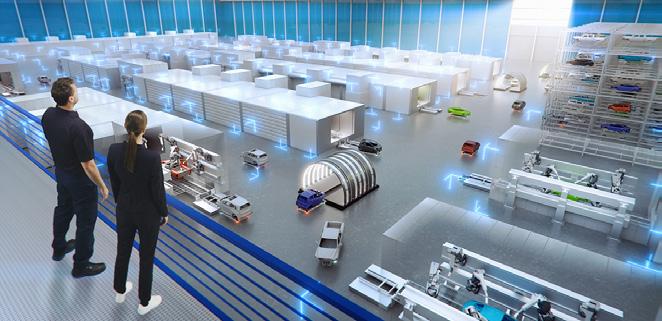
4 minute read
Paint shop of the future – flexible, sustainable and scalable
Andrej Capek
Model series and application processes are becoming more diverse in today’s automotive manufacturing. A greater variety of automotive models painted on one line leads to process inefficiencies. Globally as well as in Southeast Asia, we are seeing greater demand for more flexible and scalable paint shops as customers want to integrate new models, such as e-vehicles, more easily into existing systems. At the same time, market developments are not always predictable. Scalable paint shops allow customers to customise their volumes. Manufacturers must respond more quickly to customer and market requirements.
Dürr’s new “Paint shop of the future” concept breaks away from the traditional line layout, splitting up industrial automotive painting into boxes or short process sections for the first time. This introduces a new level of flexibility in the automotive industry’s processes and investments. In addition, the "Paint shop of the future" saves time and materials, increases availability, and makes painting more sustainable.
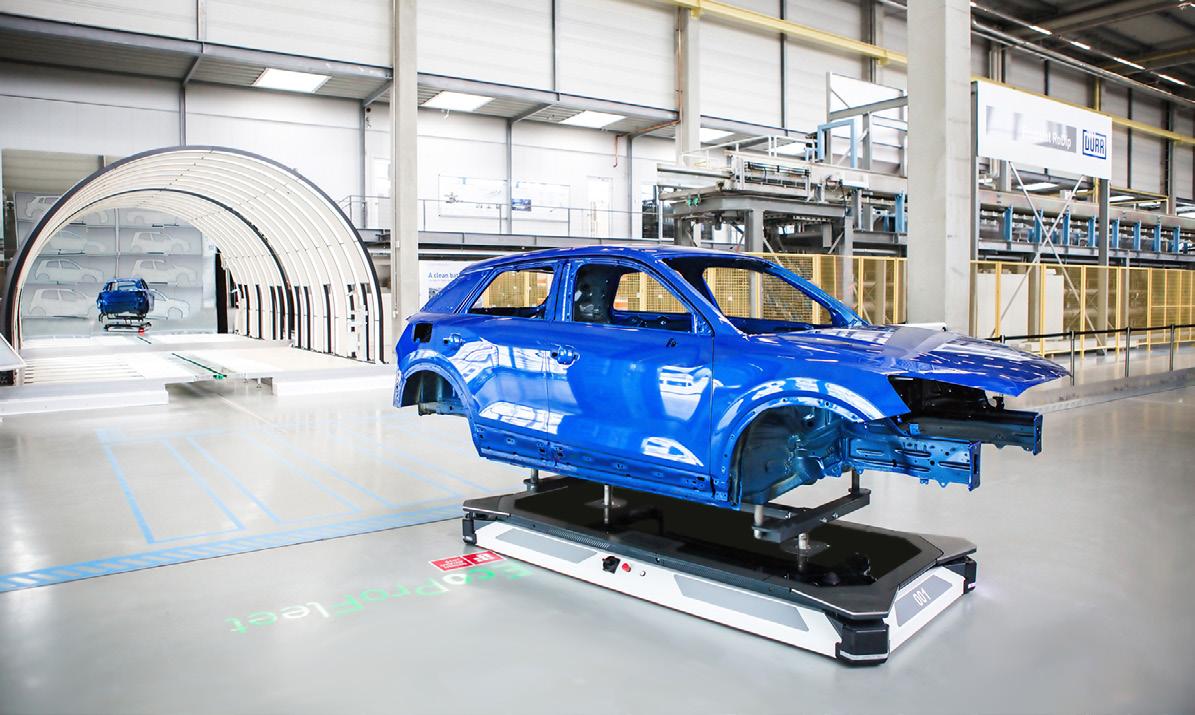
MAXIMUM FLEXIBILITY WITH ON-DEMAND CYCLE TIMES
The “Paint shop of the future” concept is based on splitting up the 120 work steps involved in a painting process into distinct boxes and smaller sections. Instead of following a fixed cycle, the process times in each box are precisely tailored to the unique needs of each body. This adaptability is achieved through parallel processes within the boxes, in conjunction with a central highbay base storage system and the automated guided vehicle (AGV) system EcoProFleet.
DXQcontrol software controls the fleet of AGVs. It intelligently guides the AGVs with car bodies to the next process, ensuring efficient utilisation of all boxes. It enables the bodies to be sorted for future processes, delivered, and collected from the right workstation with pinpoint accuracy, and passed on to final assembly in the sequence planned by the manufacturer. The concept also allows for easy capacity expansion and seamless integration of new models.
SUSTAINABLE PAINT SHOP WITH FEWER RESOURCES, GREATER EFFICIENCY
In terms of the concrete implementation, the box concept consolidates three painting processes – the interior and two exterior applications – can be combined into a single booth. This patented concept, known as the EcoProBooth, significantly streamlines the process by eliminating two of the previously standard three conveying processes. This not only saves time but also reduces paint-loss during the color change process by up to ten percent, especially if just one paint is applied in a box, for instance, the current top seller white. Splitting up the painting process into boxes shortens the overall process by tailoring the application time for each individual vehicle. This approach contributes to a reduction in CO2 and VOC emissions.
Additionally, overall equipment availability improves, as a malfunction only affects the specific box section in question and not the entire production line, as seen in the classic line manufacturing model. The variable layout also makes integrating special processes such as a special paint supply or overspray-free two-tone painting easier and more cost-efficient.
Highly Scalable And Adaptable To Both Large And Small Production
Customisation is important to meet the specific requirements of various OEMs and the “Paint shop of the future” concept is suited to manufacturers in Asia. It offers major high-volume manufacturers with a high hourly capacity the opportunity to integrate new models and technologies more easily. For those aiming to control initial investment, expansion e.g. from 24 units per hour to 48 and 72 units can occur in two steps. Startups can begin manufacturing with minimal quantities and gradually expand as demand increases. The modular concept is also Industry 4.0 ready and can be combined with Dürr’s intelligent DXQ software products for various scenarios.
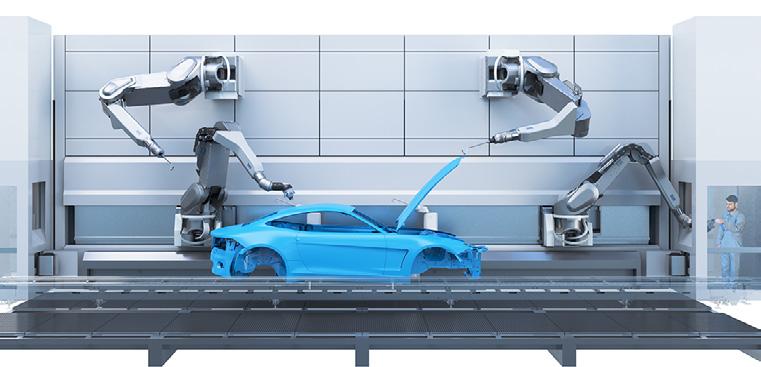
Sustainability As An Enabler
As a global innovation and technology leader in mechanical and plant engineering, Dürr aims to make a significant contribution to resource conservation and emissions reduction during the utilisation phase of Dürr products through greater efficiency. The goals are clearly defined:
• Enable electrification of paint shops to operate them Co2-neutrally when using green electricity
• Achieve climate neutrality throughout the vehicle's life and production chain, from the mining of raw materials to vehicle recycling at the end of its life cycle
• Ensure environmentally-friendly procurement of all materials used
Sustainability is an integral part of the “Paint shop of the future.” Here, Dürr relies on the optimised interaction of all processes in combination with exceptionally efficient products. Recent major successes were achieved in terms of energy, paint, solvent, and water consumption.
With Dürr, it is already possible to run a CO2-neutral paint shop with high energy efficiency in all areas. Sustainability also means conserving paint, chemicals, water and other consumables. Where less is consumed, less must be disposed of.
Contact details:
Andrej Capek
CEO
Dürr Systems Southeast Asia