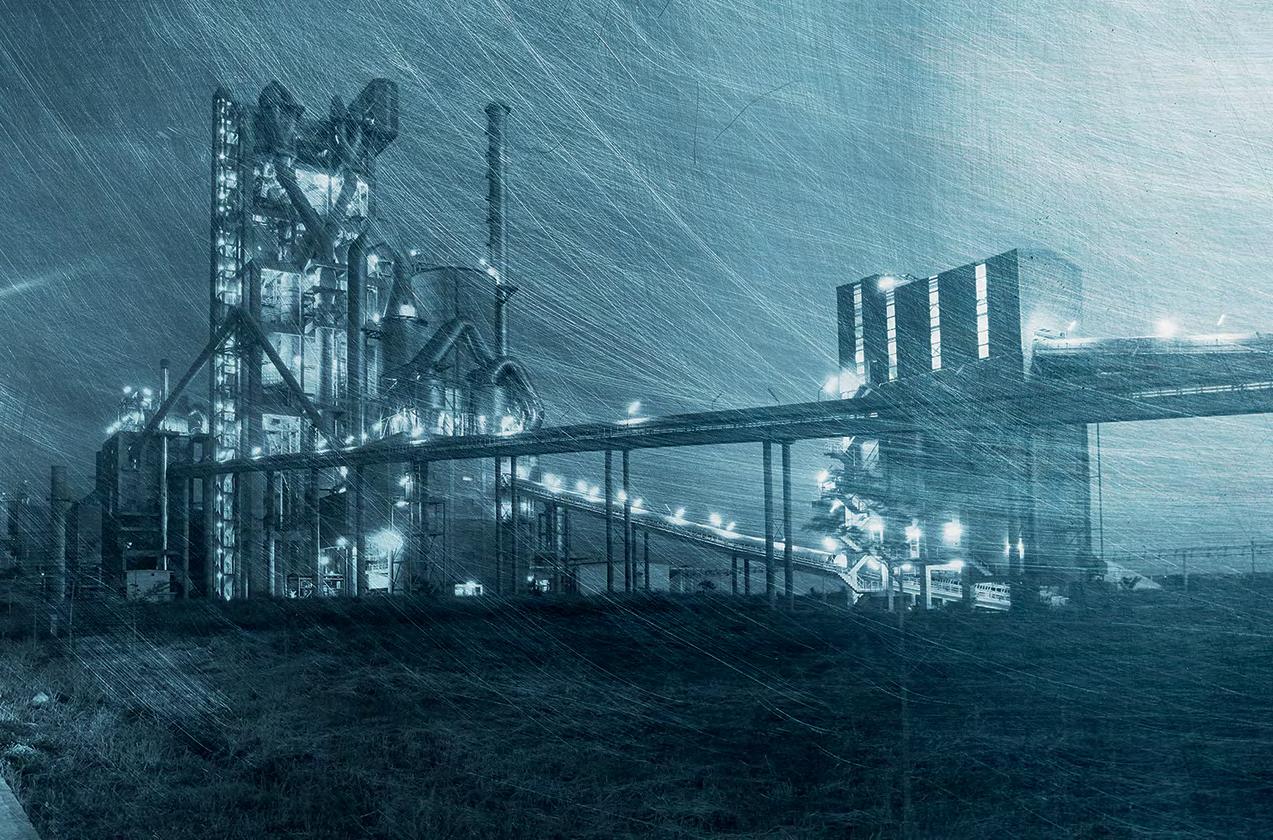
6 minute read
BEUMER Group – Your partner for the cement plant of the future
Amir Sinai
Concrete is the single most widely-used building material in the world. The core of the concrete value chain is the cement plant. Similar to other energy and labour-intensive industries, cement producers are embracing automation, digitization and sustainability as their main strategic pillars to navigate through disruptive and challenging times. Digital and automation technologies, considered by some as the fourth industrial revolution and referred to as Industry 4.0, have led to massive changes in the way we work, communicate and produce. Where does the Thai cement industry stand today in terms of Industry 4.0 and what developments do we expect in the next years?
Advertisement
The Thai cement industry has been greatly affected by the COVID-19 pandemic. While demand is rising again in 2022, last year saw demand for cement and building materials decrease by more than 20 per cent. The slump led producers to decrease production by closing mostly older or less efficient production lines. The road the cement industry needs to take is clear – embrace ever higher levels of automation and digitalization while reducing the dependability on fossil fuels, especially coal, as the main source of energy. Combining these activities will allow the Thai cement industry to catch up with their European peers in terms of efficiency and sustainability, and pave the way for producers to recover from the effects of the pandemic while becoming more resilient to future challenges.
The BEUMER Group believes that cement plants of the future will be required to be more efficient, connected and green to ensure continued operation and competitiveness. This article presents view of the top three trends in the industry.
DIGITALIZATION AND MACHINE CONNECTIVITY
In a networked production plant, all machines and components can be connected with a higher-level control system. Web-enabled user interfaces and visualization software provide operators with the necessary tools for configuration, monitoring and reporting. With modules and the dashboards, data analytics in the machine processes and prepares all the information that the system provider collects in a clear and understandable manner. Machine data, error messages and information on the operation enable the user to minimize downtimes with parameter optimization, and predictive maintenance and spare part management.
The cement plants in Thailand as well as other South-East Asian countries have yet to embark on the road to digital transformation. The current focus of most producers ranges from cost reduction in times of low demand to volume maximization when the market allows. However, BEUMER believes that rapidly changing market requirements and increased competition will force cement plants to digitally transform and implement real-time decisionmaking and problem-solving processes based on data analytics and algorithms.
AUTOMATION
With rising salaries and people's unwillingness to do arduous manual labour, cement plants should minimize their number of workers by further automatizing their production processes, especially in the loading of the cement bags on pallets or trucks. With higher levels of automation, producers can focus on engaging employees in value-added activities.
SUSTAINABILITY AND DECARBONIZATION
Cement production, with 2.8 billion tons of CO2, contributes to approximately 8 per cent of global emissions. The global effort to combat climate change and stricter curbs by Governments on emissions will have a major impact the cement industry. The German cement industry has targeted carbon neutrality by 2050, a trend which surely will be followed in South-East Asia. The inevitable introduction of the carbon tax in Thailand has the potential to disrupt the entire value chain of local producers.
In contrast to other heavy industries, such as steel production, which emit CO2 mostly due to their high energy requirements, emissions in cement production are due to the raw material itself. Limestone, the main raw material in cement production, during the burning process releases up to 600 kg of CO2 per ton of produced cement. In addition, high energy requirements reaching more than 1,400 degrees Celsius in the production process are, in Thailand and other SouthEast Asian countries, currently satisfied by using coal.
Cement plants of the future must drastically reduce emissions, better sooner than later. Cement producers and equipment suppliers are working closely together to develop technologies to make cement "greener". Alternative raw materials or additivities as well as substituting fossil fuels play a key role in emission reduction efforts. In the latter case, the increased use of alternative fuels, such as refuse-derived fuels (RDF) produced from various types of waste such as municipal solid waste (MSW), industrial waste or commercial waste, is a visible trend in Thailand. However, while in countries such as Germany, 70 per cent of the plants’ energy demand is covered by alternative fuel, the coal substitution rate in the Thai cement industry is equal to, or under 30 per cent.
However, the management of waste and the availability of alternative fuels varies by region and is a critical factor in Thailand. Effective waste management of municipalities plays a direct role in the availably and quality of alternative fuels available for the cement plants. While the technology to handle and process RDF and other alternative fuels is available, factories face supply bottle necks in terms of quantity and quality.
New innovations in the carbon capture, utilization and storage (CCUS) technologies create hope that significant CO2 emission reductions can be achieved. CCUS technologies capture CO2 from industrial processes to be either reused, for example for a variety of chemicals and fuels or to be stored in long-term facilities. Scientists are optimistic that new CO2 capture technologies for cement plants can cut emissions by 90 per cent.
Although there is no standardized solution or formula to pave the way for the cement plant of the future, there is no doubt that digitalization, automation and sustainability have evolved from fashionable terms to value and efficiency generating tools. Here, the BEUMER Group has been a reliable partner during the past 23 years in Thailand supporting the cement industry in realizing their visions for the future.
Contact details: Amir Sinai Managing Director BEUMER Group (Thailand) Co. Ltd. +66 2 731 7190 th.customer.support@beumergroup.com www.beumergroup.com