
4 minute read
District Heating for Schools
Pre-insulated pipe enhanced installation speed and energy efficiency.
By Ali Sajjadi
With many young families moving to Victoria’s Western Communities, Sooke School District 62 recently found itself with a need to quickly build more schools to accommodate approximately 1,200 elementary and middle school students.
After seeking community input for the project, the district chose to build the new PEXSISEN Elementary School and Centre Mountain Lellum Middle School. (The former, named by the Songhees First Nation, refers to the opening of hands; while the latter, named by the Beecher Bay Nation, suggests ‘house’ or ‘the idea of community, where we raise our children.’)
Designed by HCMA and built by Farmer Construction, both schools opened in 2022.
Going for gold
The district sought to integrate the new schools into the existing landscape in an earth-friendly way. Its goals included optimizing energy efficiency and achieving the Canadian Green Building Council’s (CaGBC’s) Leadership in Environmental and Energy Design (LEED) v4 Gold certification. To do so, the project incorporated photovoltaic (PV) solar panels on the roofs, strategically positioned the windows and deployed geothermally boosted heating, ventilation and air conditioning (HVAC) systems, which would run heating and cooling water through the ground to extract or reject heat, as needed.
The planners also decided to follow a district heating model, whereby a central plant would collect and distribute energy between the two schools, for greater flexibility in heating and cooling. Rather than running two separate mechanical rooms, the single heating/ cooling plant conditions water to accommodate the schools’ different energy cycles. This way, if one school requires less heat, the system can move excess heat to
854 the other school.
Heating and cooling can be produced simultaneously by a water source heat pump (WSHP), with additional heating provided by electric boilers if needed. The water is delivered through underground piping to the terminal units of each school, where it is then used in local HVAC systems to provide comfortable heating and cooling.
Meeting the challenge
The engineering firm behind the project was SMcN Consulting. According to its principal, Michael Hladky, the key to success in distribution piping or energy transfer piping applications is to prevent the heating or cooling energy from escaping while it travels. Only then could temperatures be maintained efficiently in both schools.
To meet this challenge, SMcN’s team specified Rehau’s pre-insulated cross-linked polyethylene (PEX) pipe as the basis of its system design. The pipe is engineered to efficiently transfer hot or chilled fluid through buried pipelines, minimizing energy loss.
The system uses 125-mm thick pipe to transfer energy from the central plant to each school. The middle school uses 671 m (2,200 ft) of pipe, while the elementary school uses 183 m (600 ft).
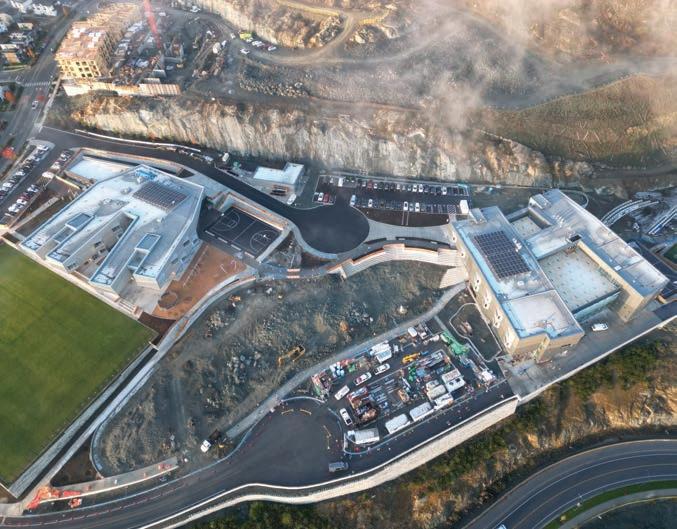
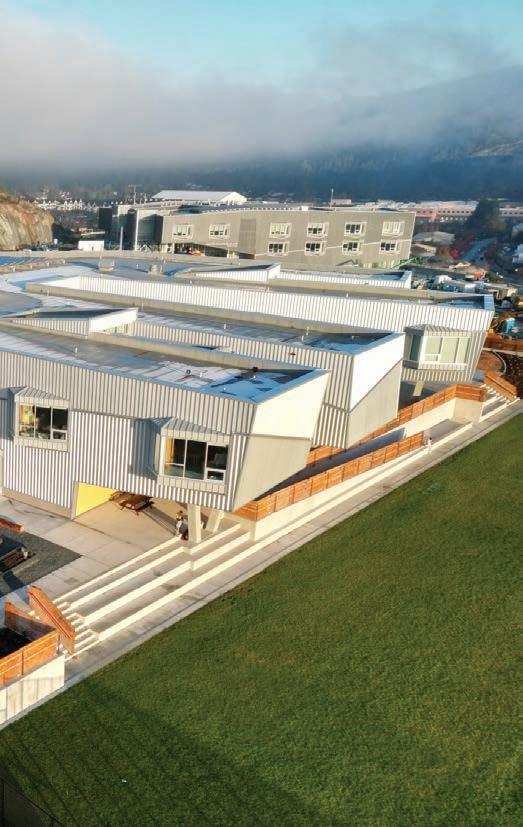
In both cases, the flexible pipe was supplied in coil lengths of 40 m (130 ft) or greater, consisting of PEX oxygen (O2) barrier pipe surrounded by foam insulation and a durable corrugated polyethylene (PE) outer jacket. The O2 barrier pipe’s co-extruded oxygen diffusion layer would help prevent the corrosion of any cast iron components within the heating system, as per the requirements of DIN 4726, ‘Warm water surface heating systems and radiator connecting systems – Plastics piping systems and multilayer piping systems.’
The project’s scope encompassed 854 m (2,800 ft) of underground energy transfer piping.
Ensuring product compatibility
Hladky explains SMcN’s team had to do a lot of number-crunching and run through many ‘what if’ scenarios from the start to determine the optimal sizing and other specifications for the project.
“Rehau had lots of technical information available online that helped us calculate relative flow rates, pressure drops, pump sizes, heat loss and other aspects of the project,” he says. “Having this information readily available allowed us to efficiently calculate design parameters and determine product compatibility.”

By working up the specifications with the supplier, the team was able to meet the project’s challenges.
“We were using a very low-temperature and high-efficiency heating system, with water at only 46 C (115 F), so we couldn’t afford to lose much heat in the trip through the pipe from the heating plant to the buildings,” he explains. “With the PEX pipe, the heat loss numbers were within tolerance. The pipe met all aspects of the design criteria very well.”
Ease of installation
Once the products were specified, a hydraulic tool kit allowed the installers to achieve quick, yet secure, connections in the field.
“Larger bore pipes are generally more challenging to work with, but the hydraulic tool does it all for you,” says Gord McLaren, division manager of mechanical contractors at Professional Mechanical, which handled the job. “Once you get the hang of it, it’s easy to make the connections.”
“The system is bulletproof,” says project installer Joe Bell. “You can’t put the pipe and fittings together wrong. The tool won’t let you misposition anything.”
C hoosing pre-insulated piping also streamlined the installation process. Metal piping must be manually insulated on the job site, which can become costly and labour-intensive and lead to performance issues if there are assembly errors. As a secure, one-piece s olution, the pre-insulated pipe reduced the client’s costs for materials and labour.
Additionally, the material’s flexibility supports faster installation, compared to rigid piping. Installers can navigate bends or obstacles without the need for extra fittings or couplings, minimizing potential leak points.

“We put in thousands of feet of pipe and had no leaks at all,” says Bell.
For both SMcN’s Hladky and Professional Mechanical’s McLaren, this was the first time specifying these products for outdoor underground piping; they had previously only used them for indoor radiant heating applications.
“In our experience, it’s somewhat uncommon in this climate to bur y building heating piping underground,” says Hladky. “Of course, corrosion would be a concern for metal piping. Pre-insulated plastic piping is the answer for long-term durability and it’s even, consistent and gap-free throughout. The pipe just rolls out and is ready to go. We will certainly con- sider specifying it for similar applications again in the future.”
Increasing awareness
The central plant, meanwhile, was designed with an educational purpose. The project team added colour-coded pipes and a dashboard that displa ys plant data, energy consumption and greenhouse gas (GHG) emission reductions, for the benefit of future engineers and tradespeople.
While central plants are often concealed, this project prioritized visibility, with windows at the front of the building. Both industry professionals and the public can learn more about the inner workings of district heating applications.
