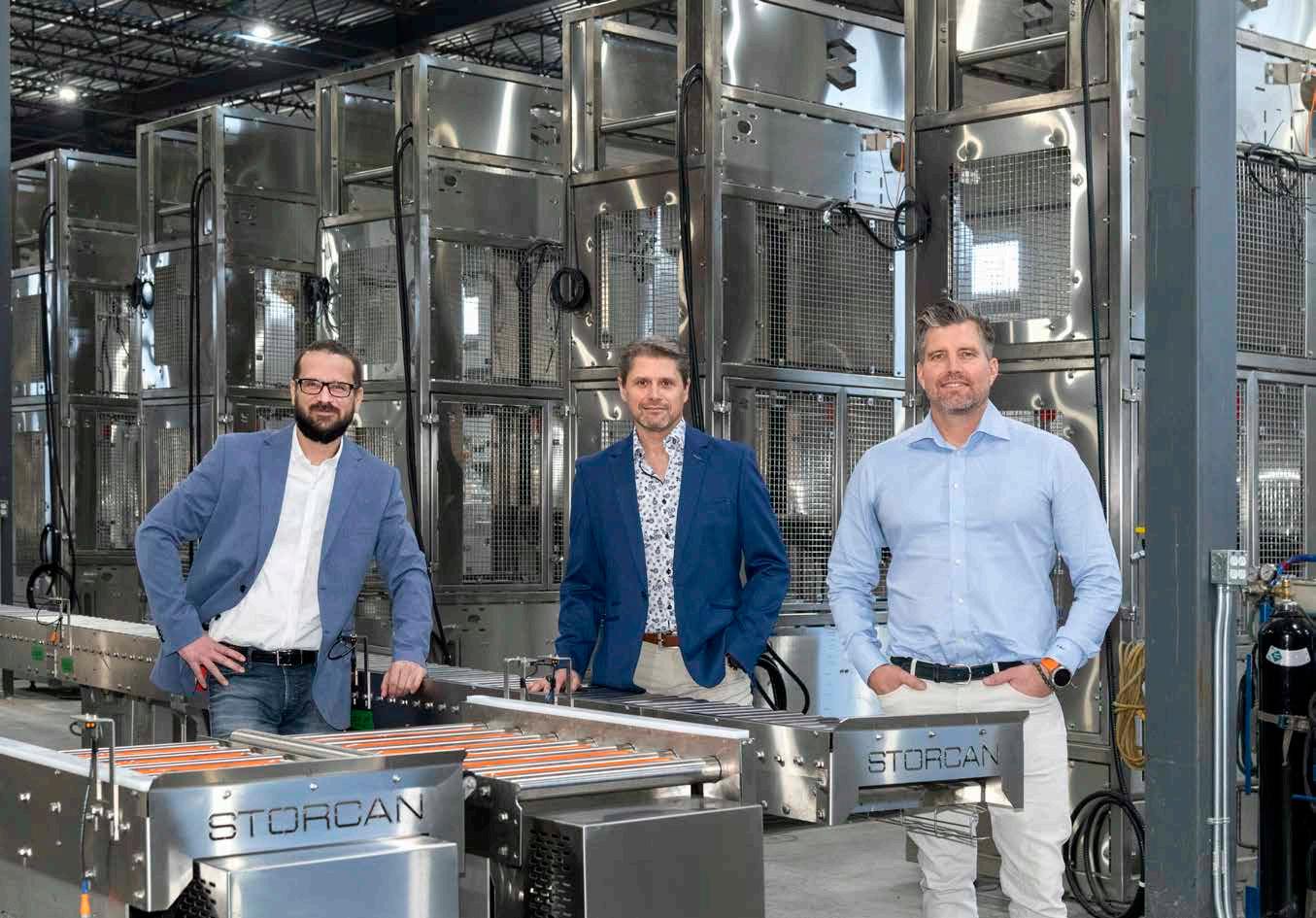
12 minute read
Home Sweet Home
From Left: Storcan International director of integration and application Hugo Lorquet, director of technical services Benoît Cliche and president Jean-Martin Savoie make up the company’s ownership team.
Conveyor manufacturer completes move to new production facility to open up the next chapter in its evolution as turnkey packaging solutions expert By George Guidoni, Editor Photos by Pierre Longtin
Few things feel as fulfilling and rewarding in business life as seeing a good plan come together. The bigger and bolder the plan, in fact, the better.
For Jean-Martin Savoie, president and co-owner of
Quebec-based conveying and packaging systems experts Storcan International, seeing his company celebrating its 45th anniversary this year at a brand new state-of-the-art production facility in
Montreal’s o -island suburb of Châteauguay is a resounding validation of his long-term plans to turn the company from a single-focused manufacturer of industrial conveyors into a well-rounded, highly competent integrator and supplier of world-class packaging line equipment for leading food-and-beverage manufacturers across Canada and abroad.
“Of course, we are completely delighted about the expansion of our manufacturing capabilities,” says Savoie, a longtime Storcan employee who purchased the company from its former owners back in 2007 alongside another business partner.
In the first few years under Savoie’s leadership, Storcan by and large remained focused on doing what it’s been doing since the company was founded in 1976—designing and building industrial conveyor systems for packaging and processing applications in the food industry.
And while the company remains a top-level manufacturer of conveying systems—available in a wide assortment of styles, designs, shapes and sizes—
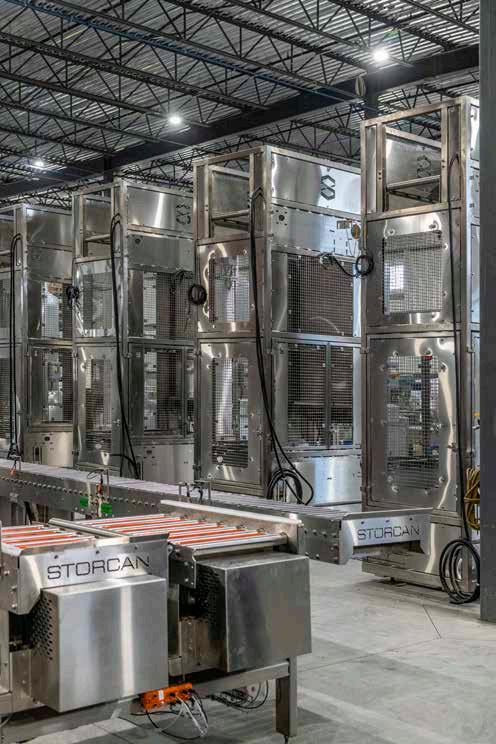
In addition to fabricating high-quality industrial conveying systems to customers’ specs, the Storcan facility also specializes in integrating those conveyors with many other types of industrial equipment and machinery to provide in customers in the food and beverage industries with complete turnkey packaging line solutions.
modern-day Storcan has long outgrown its original market ambitions and influence by vastly expanding its skill-set and core competencies to become a true one-stop-shop supplier of integrated packaging solutions for some of the world’s leading CPG (consumer packaged goods) companies.
“We have developed a new value-added proposition to give our customers a complete 360-degree solution: from consulting, designing and evaluating projects to making them possible by both fabricating the equipment they need, and integrating it with other highend equipment made by some of the best packaging machinery companies in the world,” Savoie states.
“It’s all about serving our customers in the industry better,” says Savoie, who worked tirelessly in the last 10 years to make what he calls his ‘Storcan 2.0’ vision come into being with emphatic commitment and resolve.
As part of the company’s growth in both ambition and in-house talent pool, Storcan had reached the limits of its production capacity around four years ago, according to Savoie, making a move to larger premises an urgent necessity.
Formally opened for business in September of 2020, the company’s new 30,500-square-foot, two-storey building, literally a walking-distance stroll away from its former headquarters, is a key part of an intensive $4.3-million capital investment project that puts Storcan firmly on the path to a prosperous future, according to Savoie.
As part of the run-up to last year’s move, Savoie guided the company through a comprehensive internal restructuring process that created three separate industry-specific business units—Food, Bottling and Packaging— focusing on di erent segments of the CPG marketplace.
According to Savoie, this reorganization has enabled the company sta to take greater ownership of their projects and make the company more nimble and flexible to respond faster to customer needs and identify new business opportunities in the di erent segments.
With a sta of nearly 50 full-time employees, the new facility comfortably houses all of the company’s engineering, project management, administration, sales and marketing teams, notes Savoie, while also o ering su cient room to conduct R&D (research-and-development) activities and on-site FAT (factory acceptance testing) trial runs for which it simply did not have the required space before.
“Our customers really love that,” says Savoie, citing an exceptionally busy production schedule for the company in upcoming months, which already has the production area of the plant operating seven-days-a-week to keep up with growing orders.
“There are many projects for us right now because of our involvement in the food-and-beverage industry,” says Savoie, citing increased pressure from leading grocery retailers on CPG brandowners and manufacturers to keep their store-shelves full during the COVID-19 pandemic crisis.
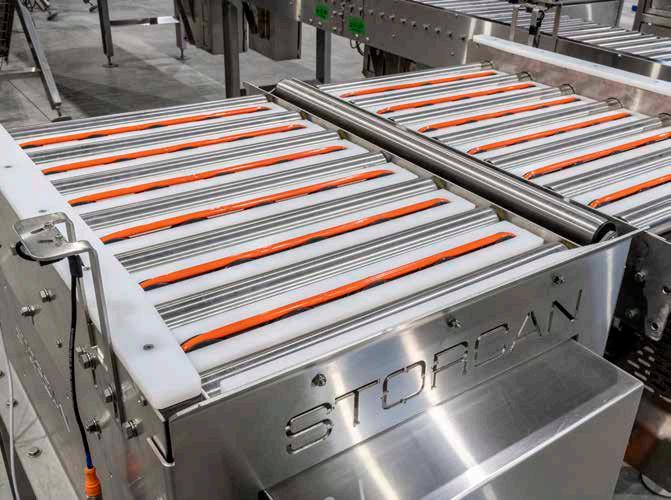
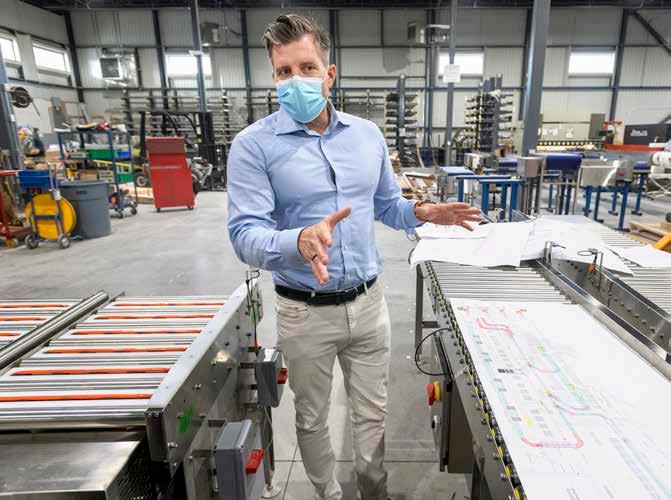




“Companies like Kraft Heinz, Weston and other big-name customers of ours are an essential part of the food supply chain,” Savoie says, “which makes companies like us essential for helping their business operate as e ciently as they can in these times.”
As Savoie relates, the sudden spread of COVID-19 to Canada in March of 2019 actually prompted Storcan to accelerate its plans to move into the new building ahead of the original target date, creating extra stress for the employees and contractors.
“Thankfully, all that stress went away when we finally moved into this nice new building with lots of natural light and more space to move around in,” says Savoie. “It’s a real game-changer.”
Doing business since the spread of COVID-19 to Canada has been especially challenging for Storcan, Savoie relates, because so much of its business is based on customer service and after-sales support that requires in-person site visits to customer facilities.
According to Savoie, the company has incurred a lot of extra legal and other expenses to enable its essential project team member to keep traveling on business even during the height of the epidemic to service its customers and to complete ongoing projects on time.
This involved a lot of extra third-party COVID-19 testing for the traveling employees, as well as filing a lot of extra paperwork to enable the cross-border shipment of essential spare parts and components to satisfy all the changing regulations on both ends of each project.
“Naturally we had to pay a lot of extra costs for transportation to comply with the legislations,” Savoie says, adding it took “a lot of creativity and flexibility” to enable its sta to keep traveling.
“Our technicians never stopped traveling during the pandemic,” Savoie says, “which required us to take a lot of extra precautions internally both before and after travel to make sure our company and our employees remained COVIDfree.”
Combined with all the workplace measures the company put in place to ensure full compliance with all the disinfection, sanitation, protective clothing and social-distancing protocols, the company’s sta has managed to get through the COVID-19 crisis so far without any sta getting infected, but for one notable exception.
“The incredible thing was that not sasingle person at Storcan got tested positive for COVID except for myself,” says Savoie, whose family got hit with coronavirus in April of 2020 after a visit Above clockwise A busy production day unfolding on the plant floor of the new Storcan facility; Storcan operates its own on-site welding department to perfrom most of its fabricating in-house; an SEW-Eurodrvie motor connected to a Storcan conveyor; Jean-Martin Savoie checking the accuracy of an incline roller conveyor assembled at the plant.
Save Space and Increase Throughput.
Like to minimize the cost of ownership?
Ryson can help. Our Spiral Conveyors need less floor space than conventional conveyors and are faster and more reliable than any elevator or lift. All our products are designed for low maintenance and long life and our proprietary modular construction makes future reconfiguring cost effective.
Quality and service come first at Ryson. We are the number one spiral manufacturer in the USA. For application assistance or more information, give us a call or visit www.ryson.com. A group shot of some of Storcan’s highly silled and dedicated employees, some of whom have been with the company right from its formation back in 1976.
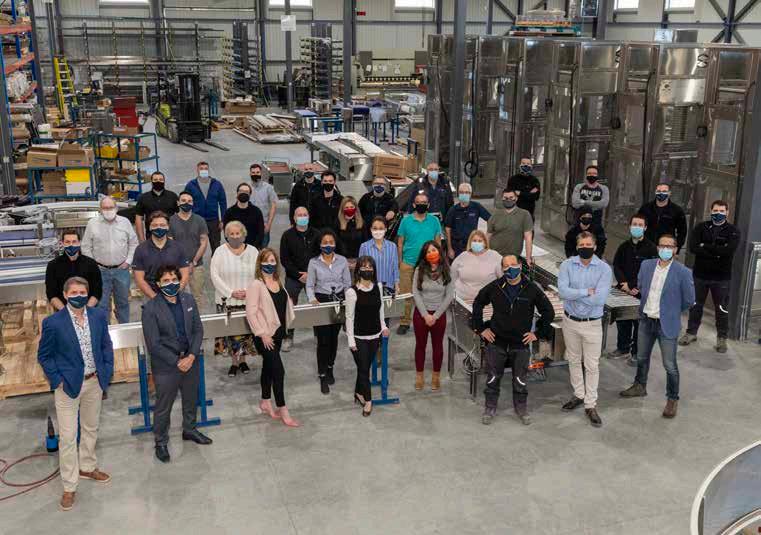
by his sister after she visited an old-age nursing home to check up on their grandmother.
“We met in a garage for about an hour, wearing masks and social-distancing as required, but in the following week my whole family had developed COVID symptoms,” says Savoie, recalling the a two-week struggle with high fever and chronic shortness of breath.
For a life-long fitness bu whose daily exercise routine includes a five-kilometer run, getting sick with COVID was an especially cruel eye-opener about the insidious dangers and risk of the coronavirus pandemic.
“I temporarily lost my sense of smell and taste, and the side-e ects of always being out of breath had persisted for about six weeks,” says Savoie, who has since made a full recovery with the rest of his family.
“We were very fortunate to get through this intact,” Savoie acknowledges, saying he’s grateful to be able to resume his normal running and exercise regimen.
Savoie says the experience has reinforced his appreciation for the people working at Storcan, some of whom began their careers with the company even before he joined it.
“Serving the food-and-beverage industry for 45 years has given us a lot of accumulated knowledge and expertise that provides us a strong competitive advantage that has not only enabled us to become and industry leader in conveyors,” he says, “but also to evolve into a company that can o er customers complete line solutions from A to Z, including integration and supplying all the equipment they need through our incredible network of business partners and suppliers.”
As Savoie relates, the opening of the new facility has also enabled Storcan to attract even more high-skilled talent to the company to reinforce its service and project management competencies.
According to Storcan, the company’s turnkey integration services include: • Consultation. The company’s sales team and solutions department collaborate to analyze the customer’s needs to o er advice, develop an automated production line layout drawing, and o er a budgeted and profitable solution. The process includes traveling to the customer’s site to get better understanding of the production environment and customers’’ specifications to either conceptualize a whole new production line or modify and add equipment to an existing line. • Engineering. After identifying and agreeing upon a solution, the engineering department takes over to take precise technical measurements on-site, model the customized solution with engineering details, and select each technology to integrate. The engineers work closely with project management department, which takes responsibility for managing the project with the customer. • Manufacturing. Storcan uses its own manufacturing facility to create custom conveyor system solutions for the food, bottling and packaging industries, as well as auxiliary machines such as crate elevators, container rinsers, depalletizers, etc. • The company’s high-skilled production team performs general and specialized welding and industrial mechanics on-site to assemble the required equipment. • Distribution of many di erent types of conveyors, process and packaging machines—manufactured by some of the biggest and best OEMs (original equipment manufacturers) in the world—to customers in the food and bottling sectors, including the sale of replacement parts.
• Project Management & Integra-
tion. As soon as the solution is validated, the project management team takes over to ensure everything runs smoothly: from conceptualization and installation to controls, programming and commissioning of the production line, including on-site training for the costumers’ personnel. • After-sale Service. Working closely with the project management team,
Storcan o ers ongoing mobile after-sales service for equipment maintenance and repairs.
Despite Storcan’s evolution as a full-service packaging line solutions provider, the company remains immensely proud of its original roots as a conveyor manufacturer, according to Savoie.
“Building conveyors is a big part of our DNA make-up,” Savoie states, citing an expansive range of innovative conveyor solutions that includes belt, mat-top and sanitary conveyors for the food industry; air conveyors and accumulation tables for bottling and canning applications; and drag-chain, roller, vertical spiral, sortation, narrow-belt, belted pivot-wheel and just about every other type of conveyor used in highspeed packaging applications in the CPG industries.
According to Savoie, the company’s legacy conveyor manufacturing expertise underpins all of the company’s integration and distribution activities that enable it to market itself as “production line architects,” as he puts it.
“We still have some customers who reach out to us only for conveyors, and we take pride in that because it confirms the high quality of our manufacturing,” says Savoie, adding that Storcan is actually moving forward to forming a new Conveyor Division unit dedicated specifically to this machinery segment.
Savoie says he is particularly excited about the new MDR 48V stainless-steel sanitary conveyors for transporting case and trays weighing up to 125 pounds.
Designed for environments requiring the use of water jets to ensure high sanitation levels, the system uses Interroll motorized conveyor rollers to ensure optimal transporting, diverting and accumulation capabilities with a highly flexible and modular design, whereby each roller in the system can communicate with the control system to ensure optimal zone control along each part of the conveyor line right up to palletizing.
“It’s a real intelligent conveyor system, with fully enclosed wiring and control accessories, that is unlike anything else out there in the industry,” Savoie states, saying it took Storcan a couple of years of intense R&D work to develop and perfect the MDR 48V sanitary conveyor system.
“It gives customers the ability and power for transporting very heavy product loads throughout the facility,” “ he says, “with a lot of flexibility and minimal maintenance requirements.
“We are very excited about bringing this new conveyor line to the market this year,” says Savoie, adding the company is already working on plans to expand the new facility further in the next couple of years to cope with growing market demand for its products and services.
“We have come a long way since we started,” he reflects. “For the fist 30 to 35 years of the company, we were essentially just putting our equipment on the floor and connecting it to other people’s machinery.
“But we have really stepped it up a notch over the last 10 years,” he says, “to become a true packaging systems integrator, with thousands of successful system installations for leading food-and-beverage manufacturers.
“There are plenty of companies out there who can sell conveyors, metal detectors or case-packers,” he reasons, “but it takes a very special skillset to be able to make all those di erent pieces of equipment work as a complete system solution for the customers.
“That’s how we plan to position ourselves going forward in the next few years,” Savoie asserts.
“We have good equipment, good technology, and great new facility that will enable us to become a true North American leader in packaging line solutions that always put its customers first.” Storcan has made major capital investment to improve the company’s IT and CAD/CAM capabilities (top) as part of its move to the new 35,000-squarefoot headquarters (bottom) in Montreal’s suburb of Châteauguay.

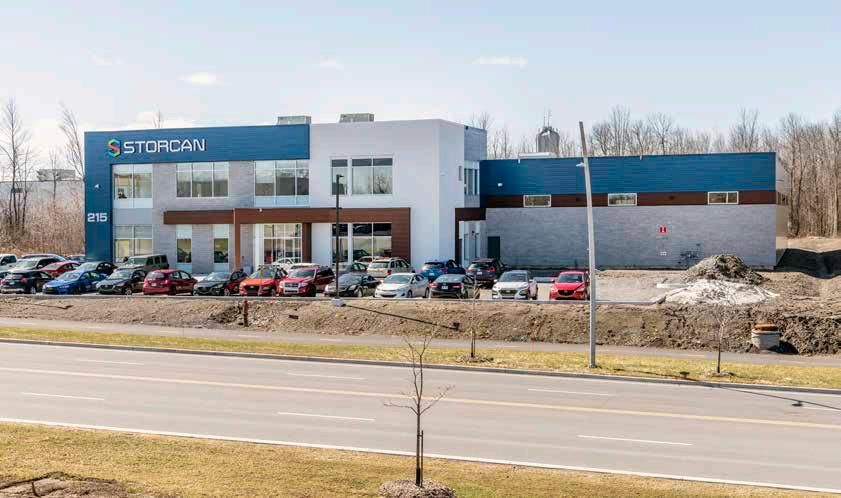
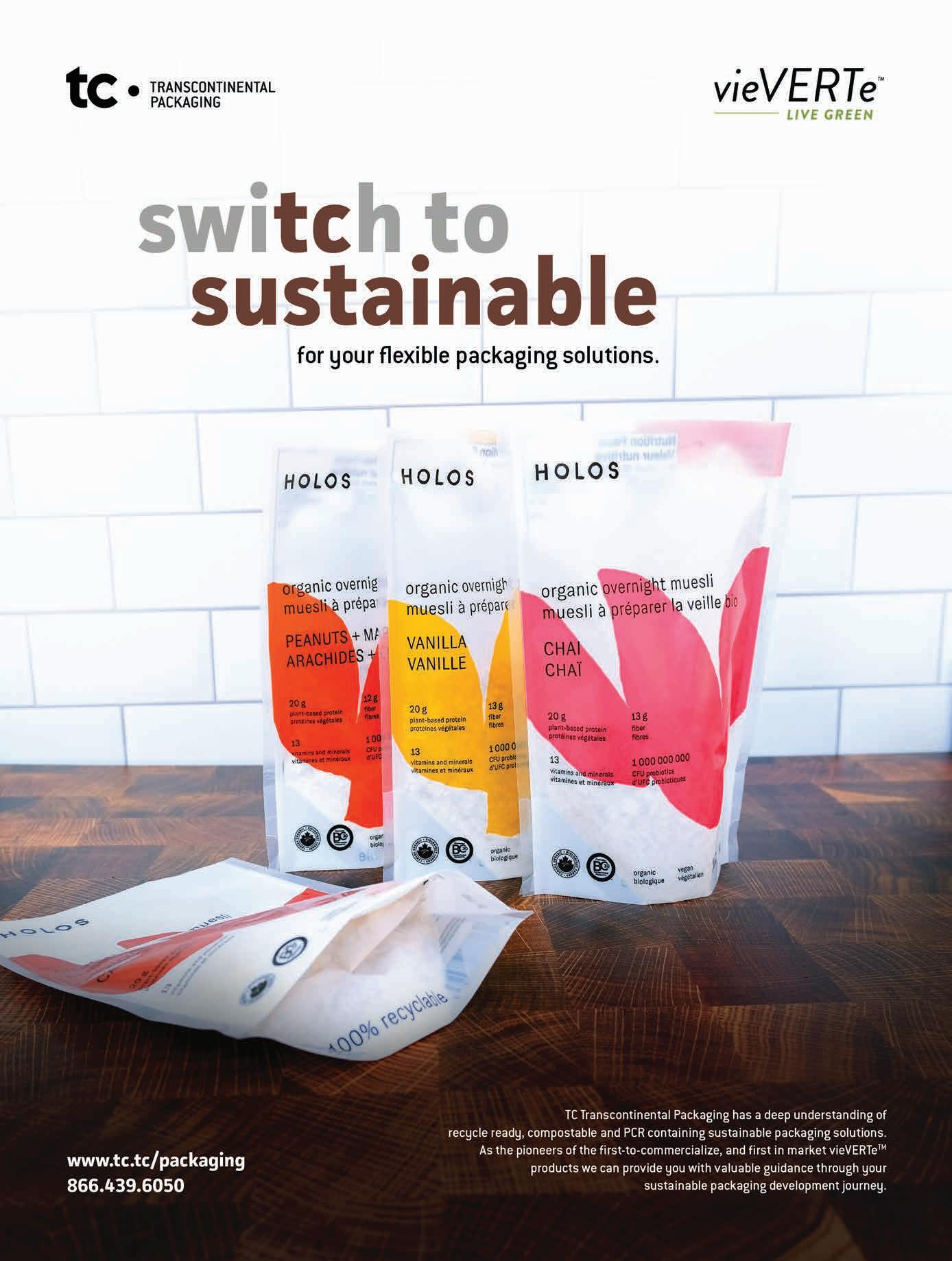