
24 minute read
Veteran Affairs
(From left) Pure Life Cannabis chief financial officer David Moriarity; operations manager Keith Prodonick; and chief technology officer Jonathan Renkema.
Former military heroes join forces in civilian life to embark on new adventures in Canada’s burgeoning cannabis industry By Myles Shane, Photos by Steven Li
Never in a million years did Corporal Dave Moriarity and Sergeant Keith Prodonick expect to be owners of Pure Life Cannabis.
Both of these courageous men had spent most of their careers in the Canadian military protecting Canada from other hostile nations and terrorists. Prodonick served from 1990 until 2011 while Moriarity fought for his country between 2001 and 2007. Both battled terrorists in Kandahar when the U.S. and
Canada went into Afghanistan with the intent of capturing Osama Bin Laden and destroying Al-Qaeda. In 1994 Prodonick accepted a second tour of duty in Afghanistan, and was later stationed in Bosnia and Kosovo.
So how did two career army men end up owning a cannabis LP (licensed producer) company?
Moriarity happily shares the remarkable story: “There were three of us having a poker game in my basement, including myself, Keith and our friend Jonathon Renkema.
“Jonathon started talking about how his kid had an autoimmune disease and that they’d tried all kinds of prescription medications to help him,” he recalls. “Nothing was working until they tried CBD oils.”
At the time, Keith and David were very aware that many veterans were using cannabis to ease the anxiety caused from seeing unforgettable images of battlefield horrors and devastation.
As Moriarity asserts, “I think anyone that has experienced a war zone comes home with some form of trauma, whether
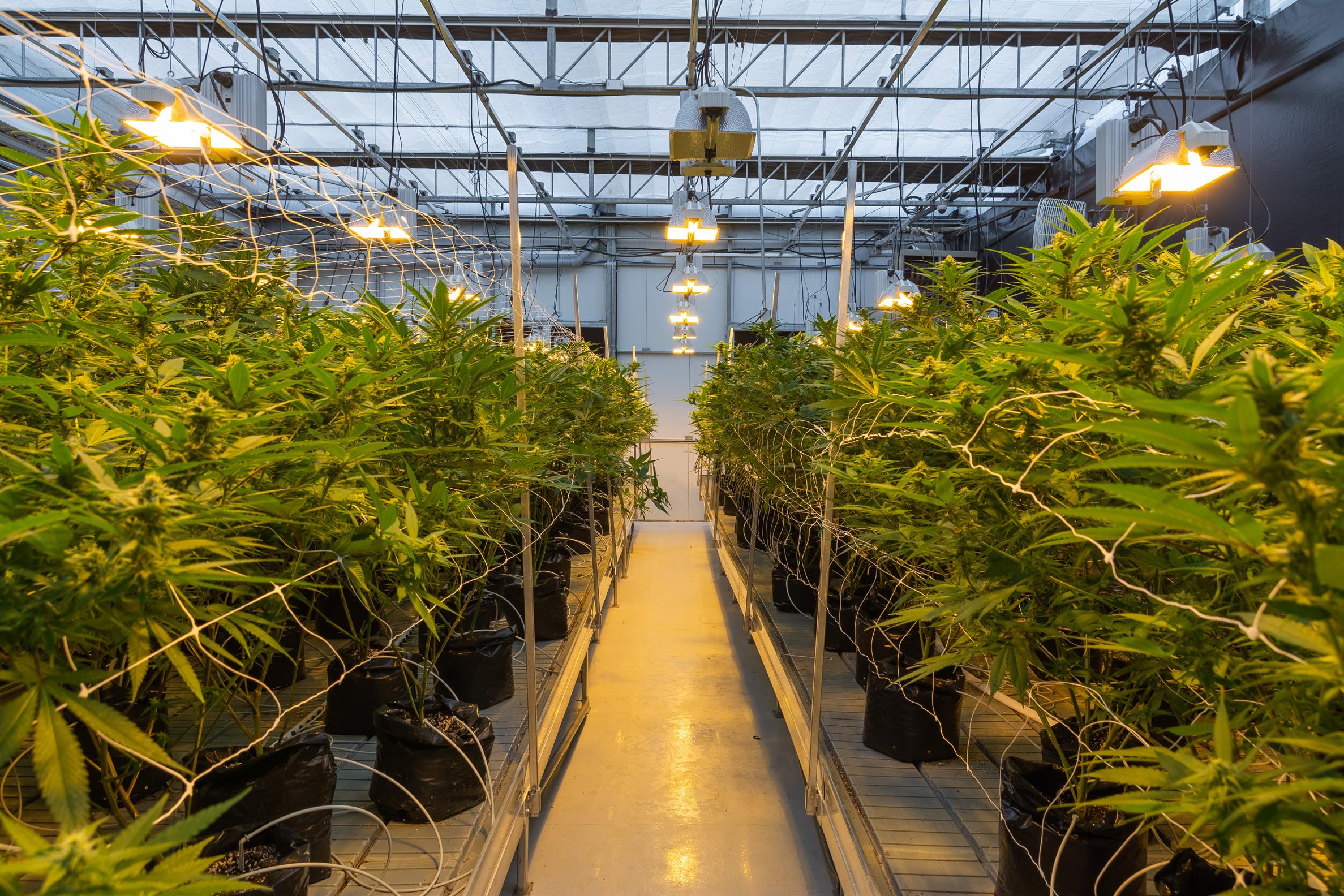
it be visible or non-visible.
“Our goal is to help provide relief where possible for both forms of trauma,” Prodonick interjects. “Before recreational legalization we were only looking at selling medical cannabis.”
Today, Moriarity serves as the director and chief financial officer of the Chipman, Alta.-based Pure Life Cannabis, while Prodonick serves as the operations manager and Renkema is the company’s chief technology officer.
Headed by three co-owners that include Moriarity, Prodonick the company’s program manager David Dhima, the company is competing in the burgeoning recreational cannabis market by using custom cultivation methods to produce high-quality craft cannabis on a commercial scale.
With their marketing slogan of, ‘Cultivating Happiness - Veteran Owned,’ the company has to rely on various unorthodox marketing tools to promote its brands, much like all other Canadian LP producers that have essentially been banned from traditional advertising by the federal government.
So in addition to populating its website with useful product information and the company’s vision of a better life for Canadian veterans, Pure Life conducts a regular series of so-called ‘Product Knowledge Sessions,’ whereby they send their sales team to cannabis stores and provide information on their strains and formats.
As Moriarity points out, Pure Life optimizes every opportunity they can to stand out from the competition.
“We’re a veteran-owned and operated company that has invested in leading-edge programming and automation technologies,” he states..
“This controls every aspect of our environment and packaging process,” he says, “so that our staff can remain focused on the plants to ensure that our end product is always premium craft quality.”
In Moriarity opinion, “We are near the top of the pecking order, not necessarily in size but definitely in sustainability.”
Currently, Pure Life is licensed to sell
A look inside one of the company’s indoor growing rooms used to harvest high-quality cannabis using a combination of ambient sunlight and high-pressure sodium lamps to achieve the highest possible yields.
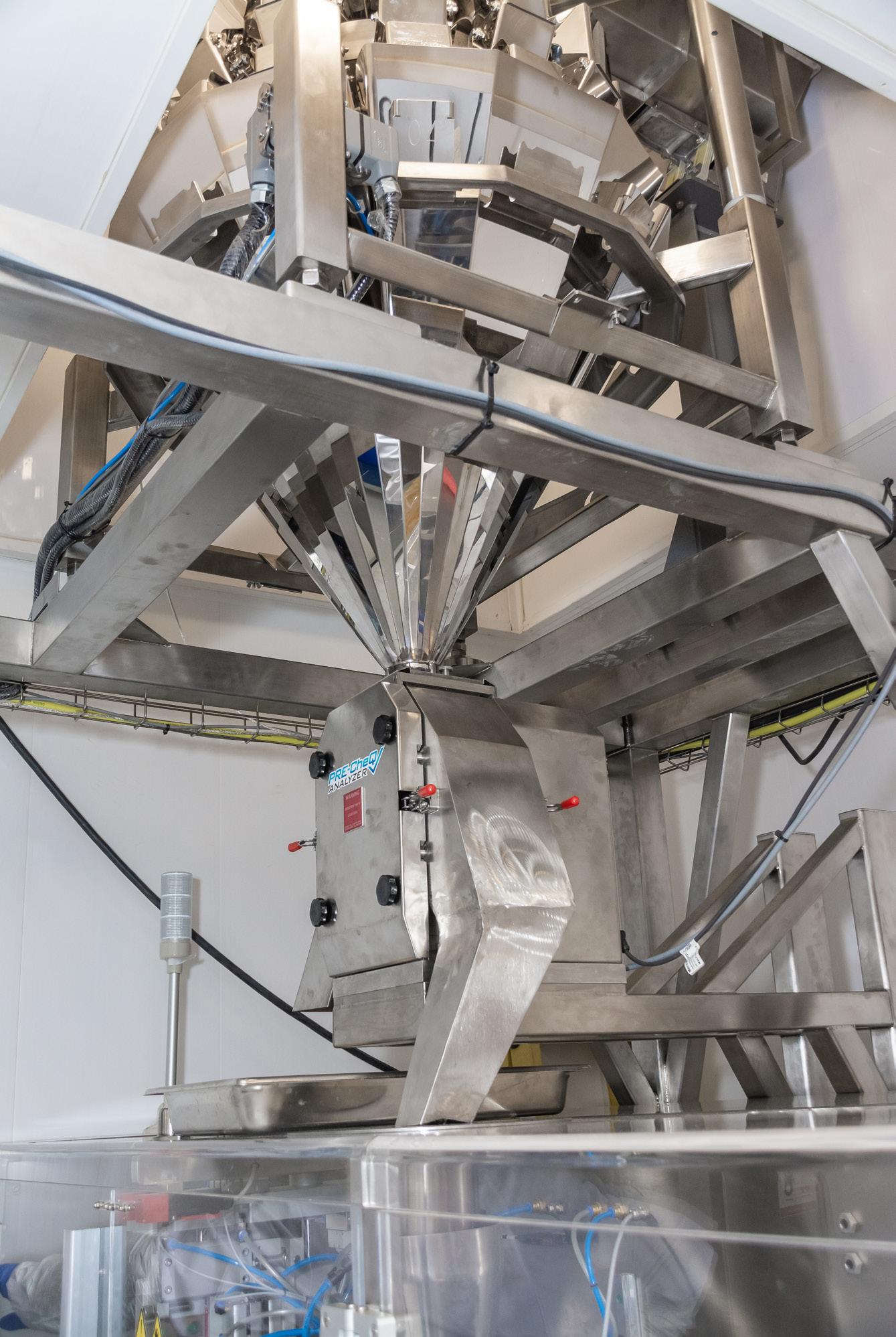
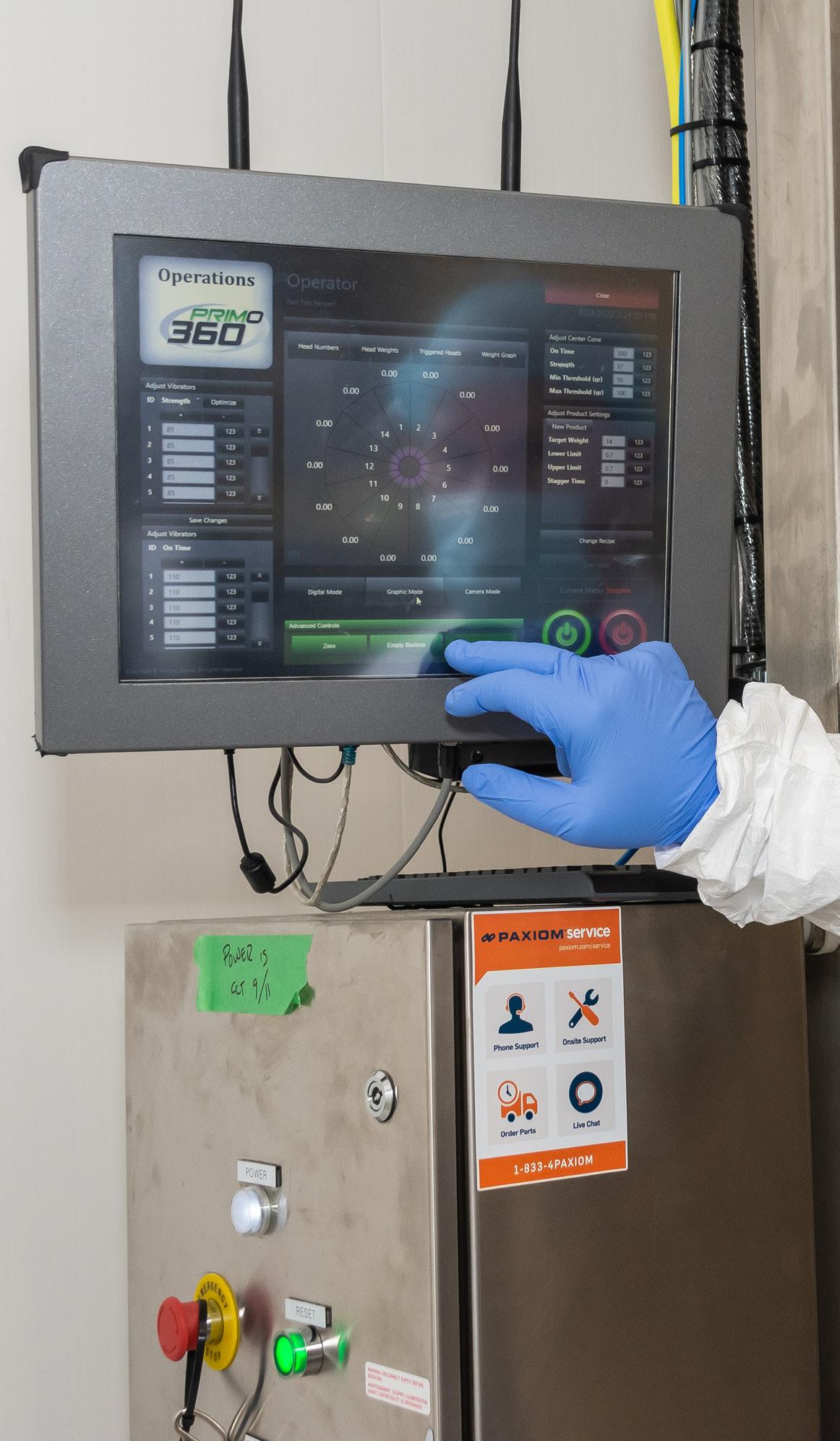
(From right) A close-up of the automatic weighscales used to dispense measured quantities of cannabis flow product down to the Swifty Bagger 3600 pouch filling machine below. Chief technology officer Jonathon Renkeme making on-the-fly adjustments to the PrimoCombi multi-head weighscales via the system’s HMI terminal.
recreational cannabis in B.C., Alberta, Saskatchewan and Ontario through local legal dispensaries, while online it is permitted sell medical cannabis for to individuals with prescriptions across the country.
The recreational cannabis is shipped to the drop-off centres in each province, which are controlled and regulated by the various provincial governments.
Currently, Pure Life regularly ships 800 kilograms of product daily to the Alberta Game and Liquor Commission, the British Columbia Liquor Board, the Ontario Cannabis Store and the Saskatchewan Liquor and Game Authority.
The company offers a different amount of SKUs (stock-keeping units) depending on the province: 12 SKUs in Alberta, three in B.C. and Ontario, and 16 in Saskatchewan.
While the flagship Pure Life label is the company’s main brand, it also markets a range of popular stains that include Cherry Death, Frozen Lemon Jack and Orange Jet Fuel.
As Moriarity confides, “We currently have six strains in rotation with 93 additional strains in-house, with an annual capacity of approximately 3,000 kilograms per year.”
Pure Life’s retail formats include one, 3.5, seven and 14 grams of flower per mylar pouch; along and three-, four and five-packs of 0.5-gram pre-rolled joints per tube, all sold to a very mixed bag of customers.
As Moriarity points out, “The stigma that only potheads use cannabis is no longer accurate today.
“There are many people who are moving away from alcohol and towards cannabis for social use for all kinds of health and other reasons,” he asserts.
The company’s partners began their joint journey in 2018 by vetting different buildings to look for the perfect facility—eventually securing 80 acres of land in Lamont Country.
As Moriarity recounts, “We first broke ground on the 28,000-square-foot facility located about miles outside of Edmonton.”
Shortly thereafter, Pure Life received their Cultivation, Processing and Medical Sales License in December of 2019, and Recreational Sales License in February of 2021.
The facility is designed to meet EU GMP (Good Manufacturing Practice) standards along with all the pertinent Health Canada regulations, according to Prodonick.
“We have hybrid greenhouses which encompass insulated walls, in floor heating and natural light through the defused poly-carbonate panels in the ceiling,” he says.
As Prodonick explains, the entire growing operation is fully automated with environmental controls, and the facility uses a

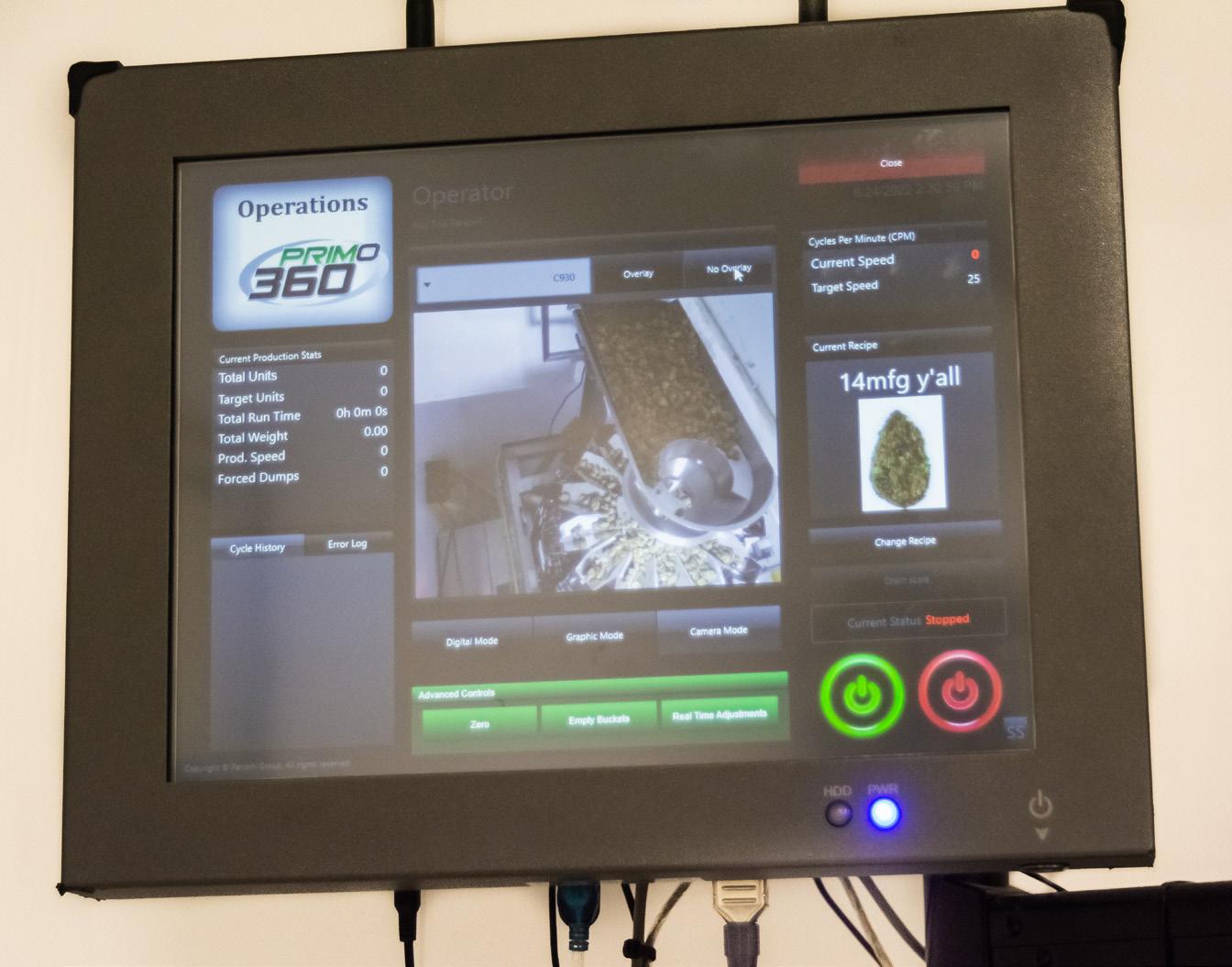
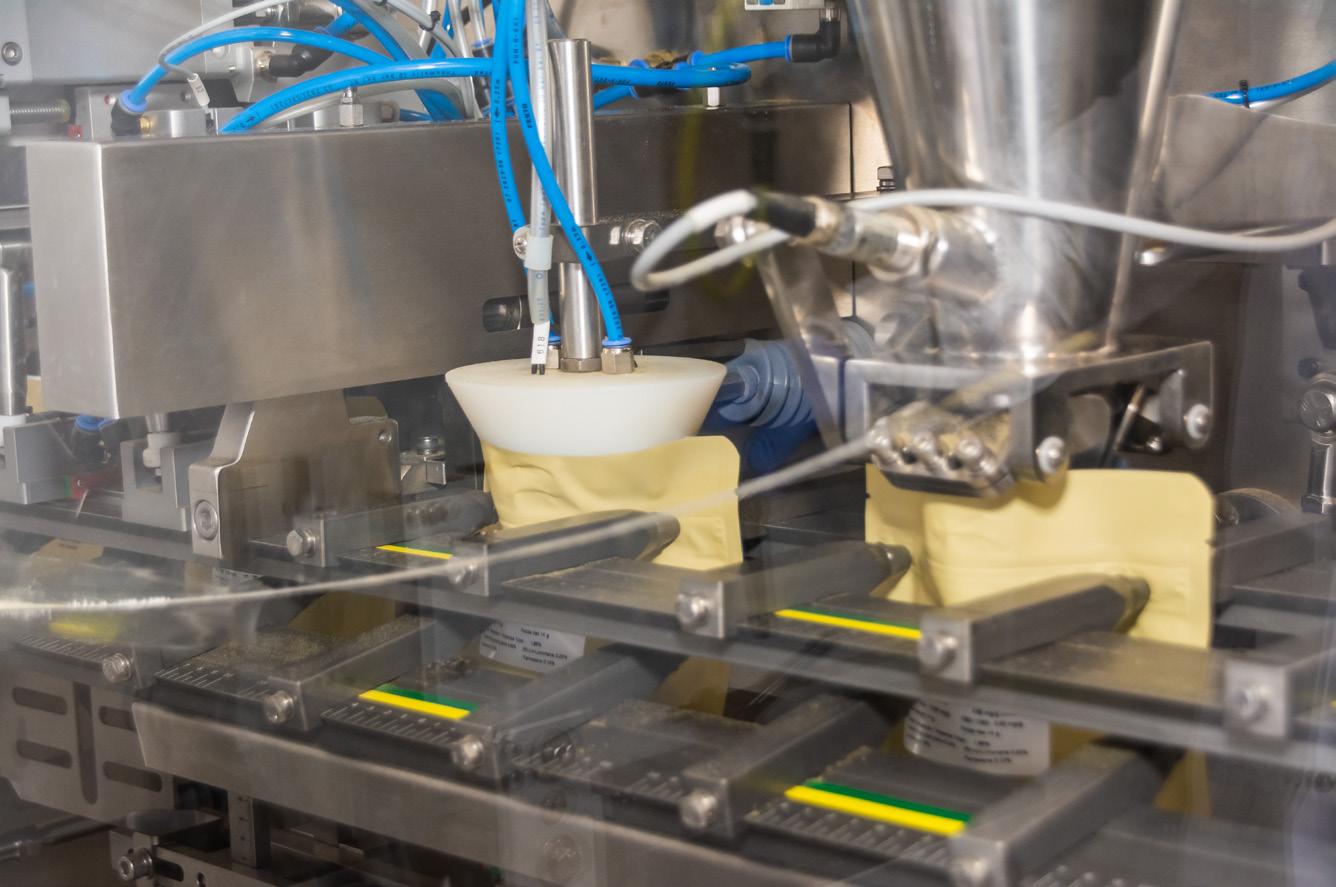
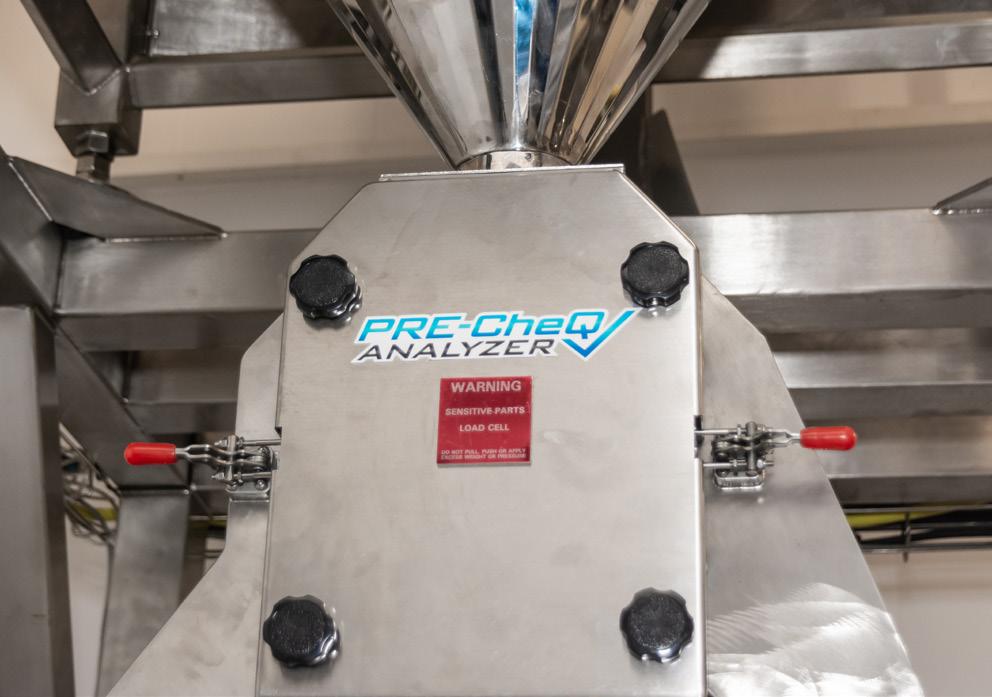
mixture indoor and outdoor lighting by way of natural sunlight and high-pressure sodium lights.
“Environmental controls and processing are all fully automated,” he says. “ We have four rooms that each comprise 4,000 square feet of flowering bays.
“Each typically grow approximately 600 plants per 4,000 square feet of canopy.”
After Pure Life Cannabis received their Recreational License, the team was aware that operating the business without machines was no longer an option since they would be required to increase production substantially.
Moriarity explains how the company moved from its medical marijuana roots to the larger recreational demand.
“We vetted all of the machinery suppliers and settled on WeighPack Systems’ equipment from the Paxiom Group, Moriarity recalls. “The fact that they had already had cannabis production lines in operation, was a huge bill of confidence for us.”
In mid-2022, WeighPack Systems supplied Pure Life Cannabis with a turnkey pack-aging solution which included the Swifty Bagger 3600 pouch-filling machine, complete with an automatic WeightCheQ Pre-Check Analyzer, that completely automated the previous time-consuming process of filling premade pouches manually by hand—providing output rates of up 1,800 pouches of dry cannabis per hour.
In similar vein, Pure Life also desperately need to automate its tedious existing manual hand-rolling process for making pre-rolls 0.5-gram cones, which originally required six people to produce about 1,500 pre-rolls per day. After installing the WeighPack JuanaRoll pre-roll packaging (Above from top) A real-time display of all the key parameters of the weighing and dispensing process taking place inside the PrimoCombi weighscales. Pre-measured quantities of dry flower cannabis being dispensed inside pre-made pouches.
(Left) WeightCheQ Pre-Check Analyzer used to verify the weight of each pouch.
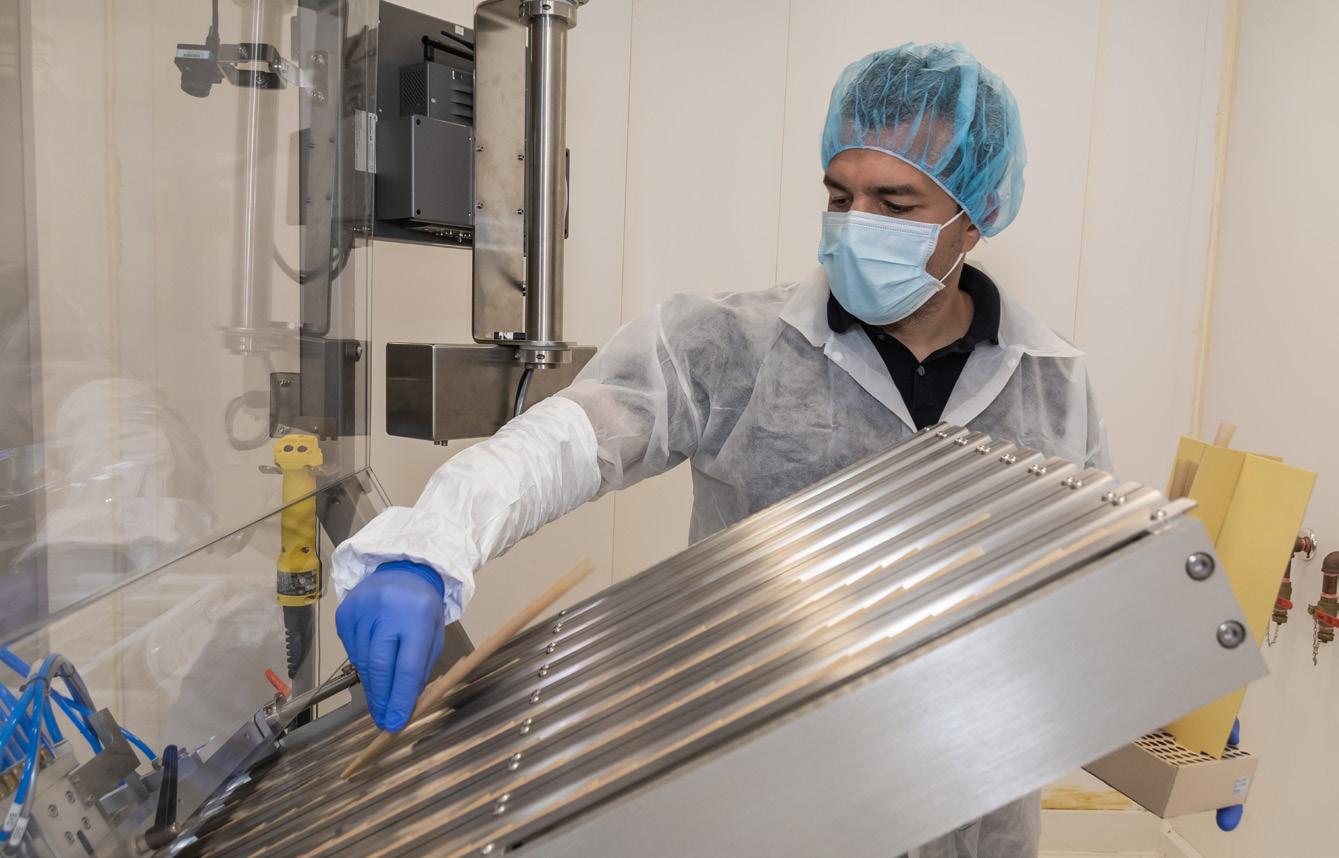
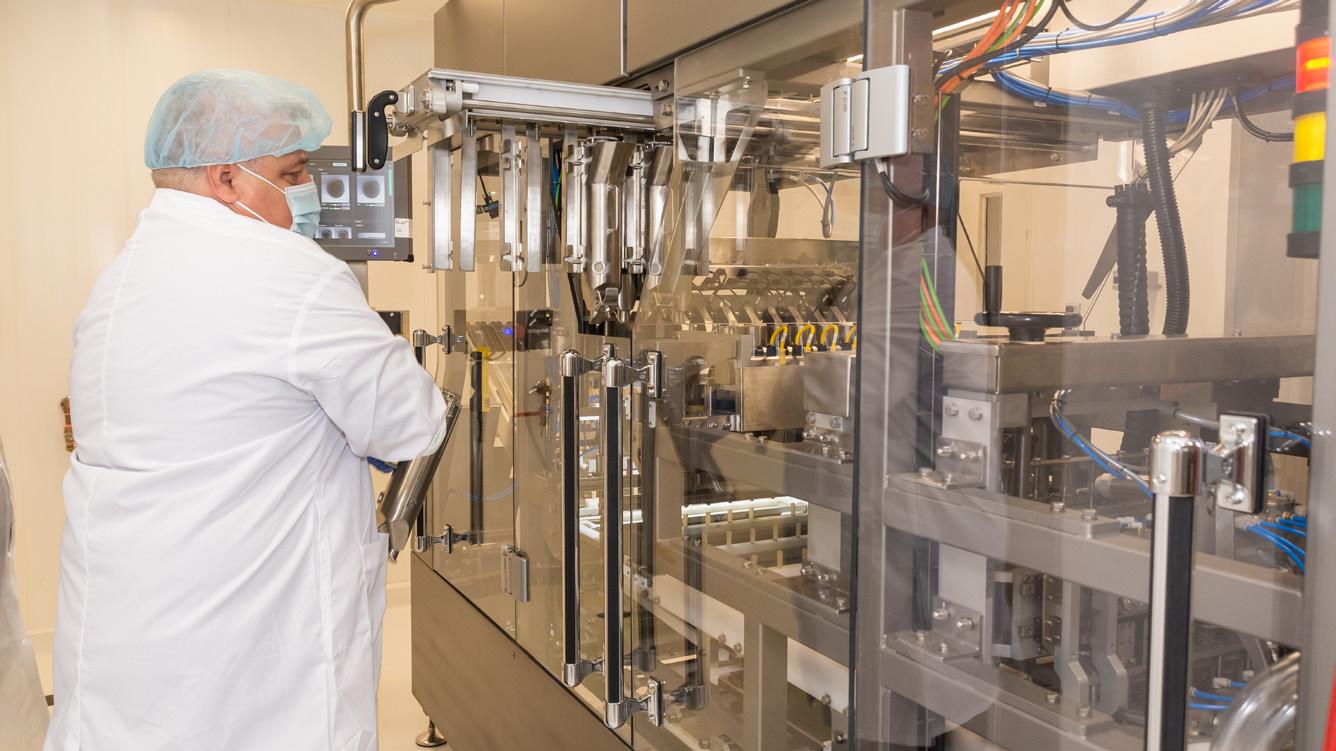
machine, the plant can new easily produced 20,000 to 30,000 pre-rolls per day.
Both machines are programmed to store all production records to record every roll and bag for Health Canada, Pure Life now houses two efficient production kines incorporating the Swifty Bagger 3600 is used on the first line for pouching dry flower; and the eight-channel, JuanaRoll machine for pre-roll production.
“From start to finish, the process is a turnkey farm-to-table operation,” Prodonick states.
Initially, the flower is hand trimmed then sorted before being released into the packaging line.
Afterwards the flower is processed through the equipment where it is weighed and re-weighed in order to verify it falls within Pure Life’s level of tolerances.
Any product which falls outside of the spec is redirected to the hopper, while the product that meets the criteria are inserted into mylar pouches and sealed. \
The pre-rolled flower product is milled in-house and deposited into the JuanaRoll machine, where it is then inserted into the pre-rolled cones. Each cone is then weighed to ensure it is within spec before being approved for final packaging.
Perhaps the machine that is most critical in terms of the automation for Pure Life is the Swifty Bagger, which is truly an engineering marvel.
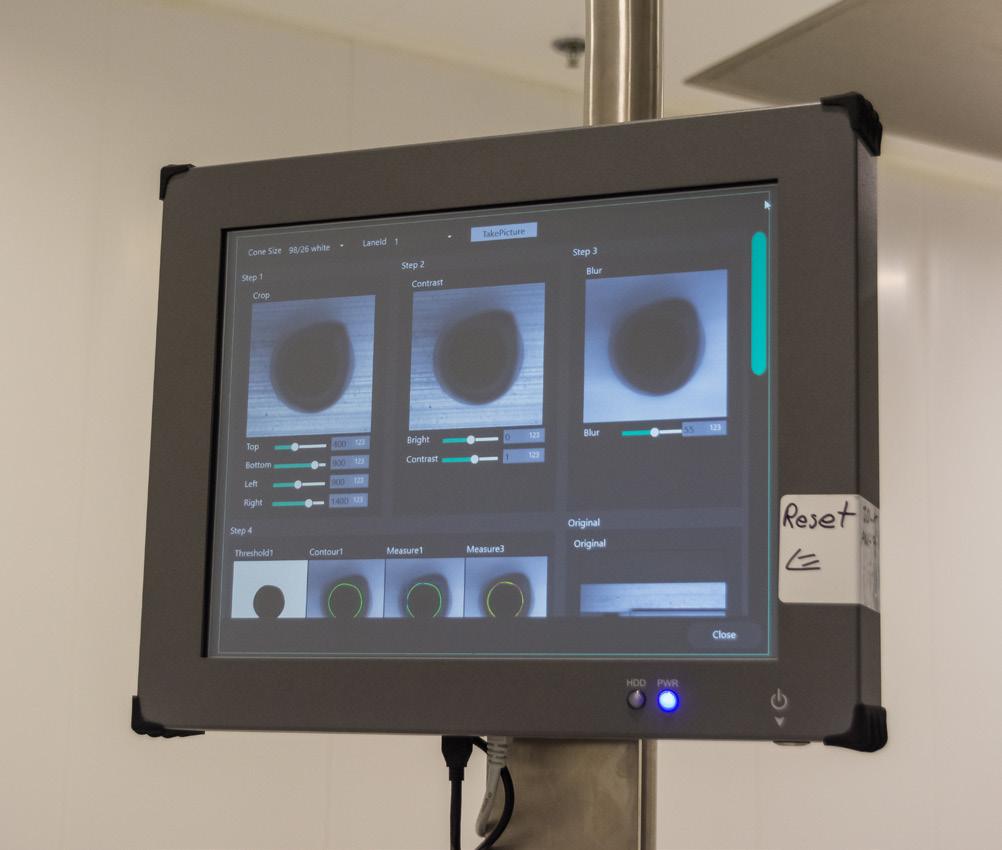
(Clockwise from left) Machine operator loading up the eight-channel JuanaRoll machine with stacks of filtered paper cones prior to production. A camera system deployed inside the JuanaRoll machine making sure each processed pre-roll meets all the required specs. Line operator keep an eye on pre-roll making process unfolding inside the JuanaRoll machine from WeighPack Systems.
Digital cutting at an industrial level.
1.5 m
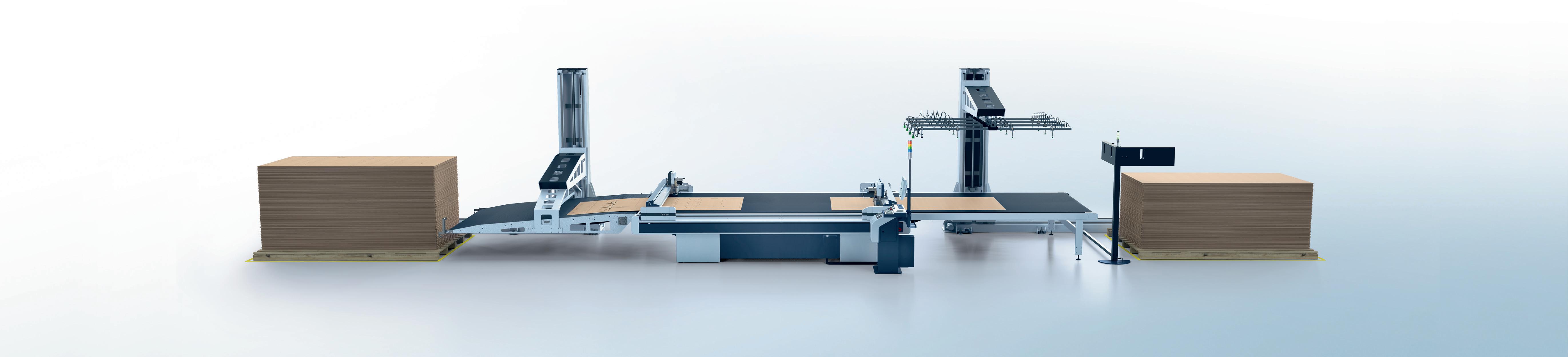
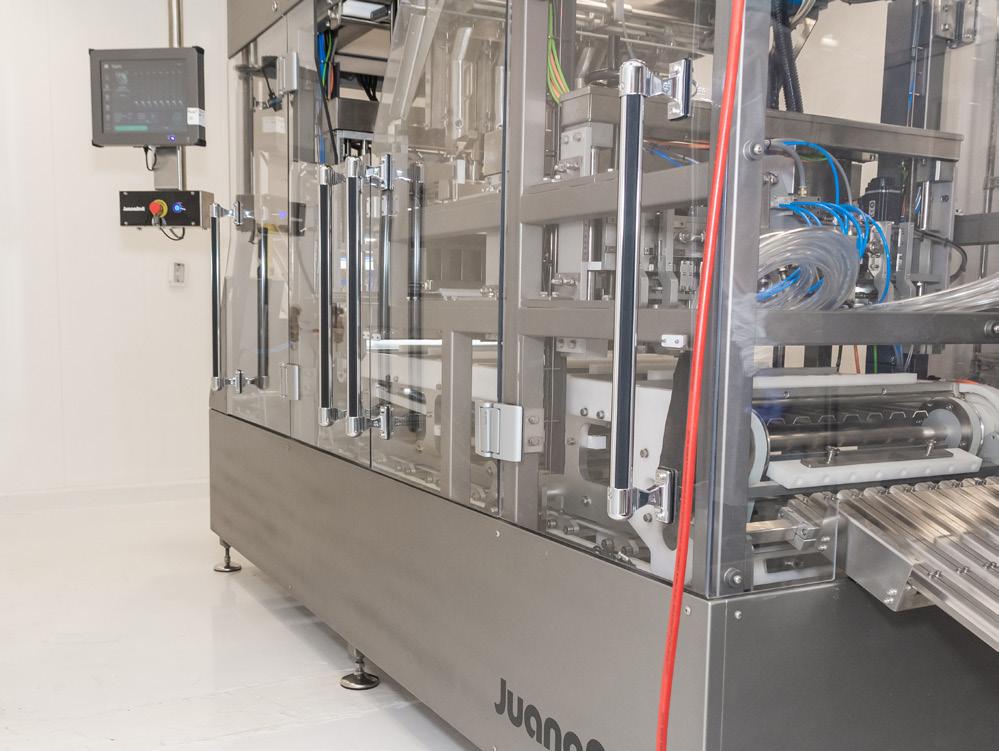
Engineered for medium to high production rates the sturdy, camera-driven, automatic bagging machines are built sturdy and can endure the high volumes and intense workloads to handle growing production demands.
The Swifty Bagger comprises an easy-access bag magazine for convenient pouch loading, an automated zipper opening device, a bag shaker at the fill station for product levelling, and a combined exit conveyor.
For its part, the JuanaRoll Pre-Roll Packaging Machine It adopts edge weight cell technology with 2/1,000-gram resolution, an integrated PreCheQ Check Weigher and separate inline stations for compacting, tamping, twisting, trimming and crowning.
The machine features built-in no cone/no fill detection capability, enhanced with a cone open camera vision system and two digital cameras, with free online sup-port and training.
The JuanaRoll includes a user-friendly HMI (human-machine interface) terminal for limitless recipe set-up and precise control over compaction and twisting. Real-time production reporting can be seen with the touch of a button, while all key data is easily exported to a USB or via email.
So far, Prodonick says he is more than satisfied with the JuanaRoll purchased by Pure Life.
“It’s very modifiable and you can update the programming and the parts,” he says. “Our product tends to have a little more powder than others, which can be a little challenging for the machine.
“But thanks to quick and reliable support from Chris Widomski the installation/service technician from Paxiom, we were able to find a good recipe combination.
“The equipment was tweaked and modified to run at its maximum capacity.”
Says Prodonick: “It is often the tech support that will make or break a customer and we’ve had the best support for any machine I’ve ever purchased.”
As a true story of an underdog beating the odds, Pure Life Cannabis offers a compelling example of a company striving to achieve a noble cause by helping fellow veterans to overcome war-time traumas and build a normal life for themselves.
To do so by deploying state-of-the-art automation technologies and staying true to its roots as a high-quality craft cannabis producer, is really all the proof anyone needs that this is one company that is more than prepared than ever to become a major player in the cannabis industry.
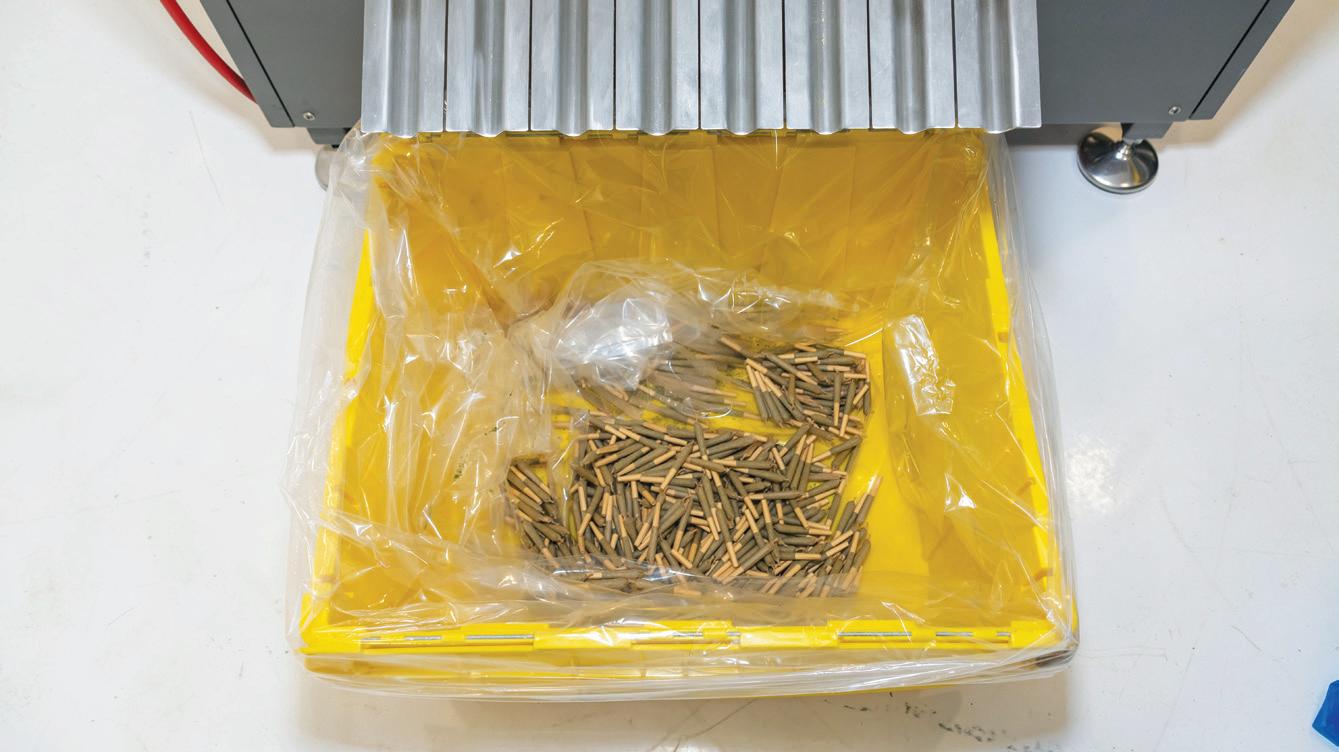
SUPPLIERS
WeighPack Systems, Inc. Paxiom Group
Please see a video of the WeighPack Systems equipment in action at the Pure Life Cannabis production facility on Canadian Packaging TV at www.canadianpackaging.com The addition of the automatic eight-channel JuanaRoll pre-roll making machine from WeighPack Systems has enabled the Pure Life Cannabis plant to completely automate its production process, while boosting its capacity to 20,000 to 30,000 pre-rolls per day, depending on current demand requirements.
The Board Handling System BHS150.
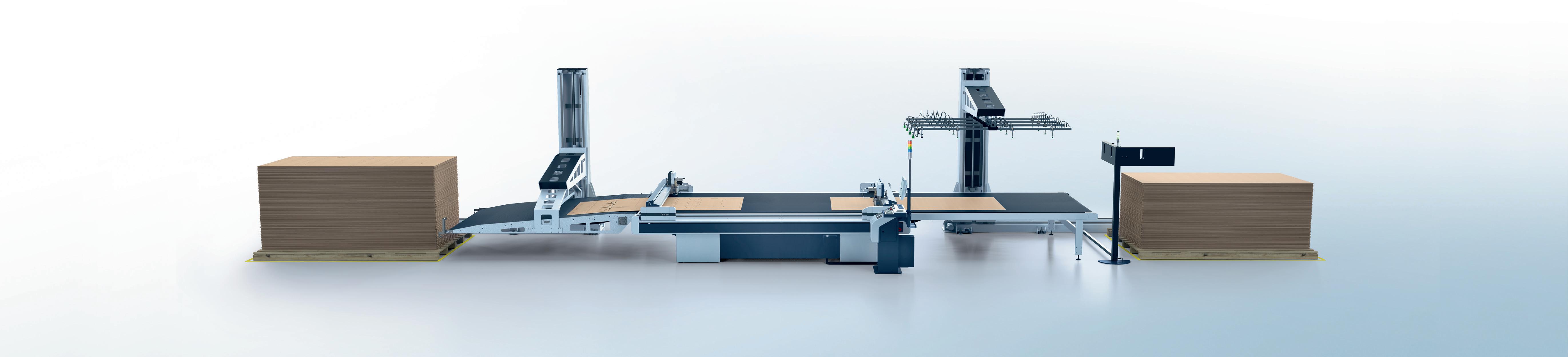
NOVA Chemicals Corporation, Calgary-headquarter producer of plastic films and resins for packaging and other industrial applications, has appointed Danny Dweik as the company’s interim chief executive officer.
Flexographic plate-making equipment manufacturer Miraclon of Rochester, N.Y., has appointed Evan Spinosa as regional commercial director for the U.S. and Canada.
Flint Group, globally operating manufacturer of inks and coatings for packaging printing and labeling applications, has appointed Terry Davis as vice-president of strategic account for the company’s North American flexible packaging business.
Kendall Packaging
Corporation, Mequon, Wis.-headquartered manufacturer of flexible packaging products for the food, pet food and personal care industries, has appointed David Roche as chief financial officer; Adam Osterhaus as controller; and Daren Roberts as plant manager at the company’s production facility in Pittsburg, Ks.
Industrial automation solutions provider Beckhoff Automation LLC of Savage, Minn., has appointed Doug Schuchart as global intralogistics industry manager, responsible for the company’s business development efforts worldwide in the distribution/fulfillment center, parcel/post and related e-commerce segments.
Leading German strapping and bundling machinery manufacturer MOSCA Group has appointed Leo Maiello as chief executive officer of the company’s MOSCA Strap &
Consumables GmbH and
Co. KG subsidiary.
Admix, Inc., Londonderry, N.H.-based manufacturer of hygienic and industrial mixing equipment for food, beverage, chemicals, cosmetics and pharmaceutical industries, has appointed Tim Dining as its new chief operating officer.
Green Bay, Wis.based Paper Con-
verting Machine
Company (PCMC), part of BarryWehmiller’s Converting Solutions platform, has appointed Scott Bean has joined as executive vice-president of operations; Jason Hilsberg as vice-president of life-cycle support; and Kelly Morgano as global vice-president of people.
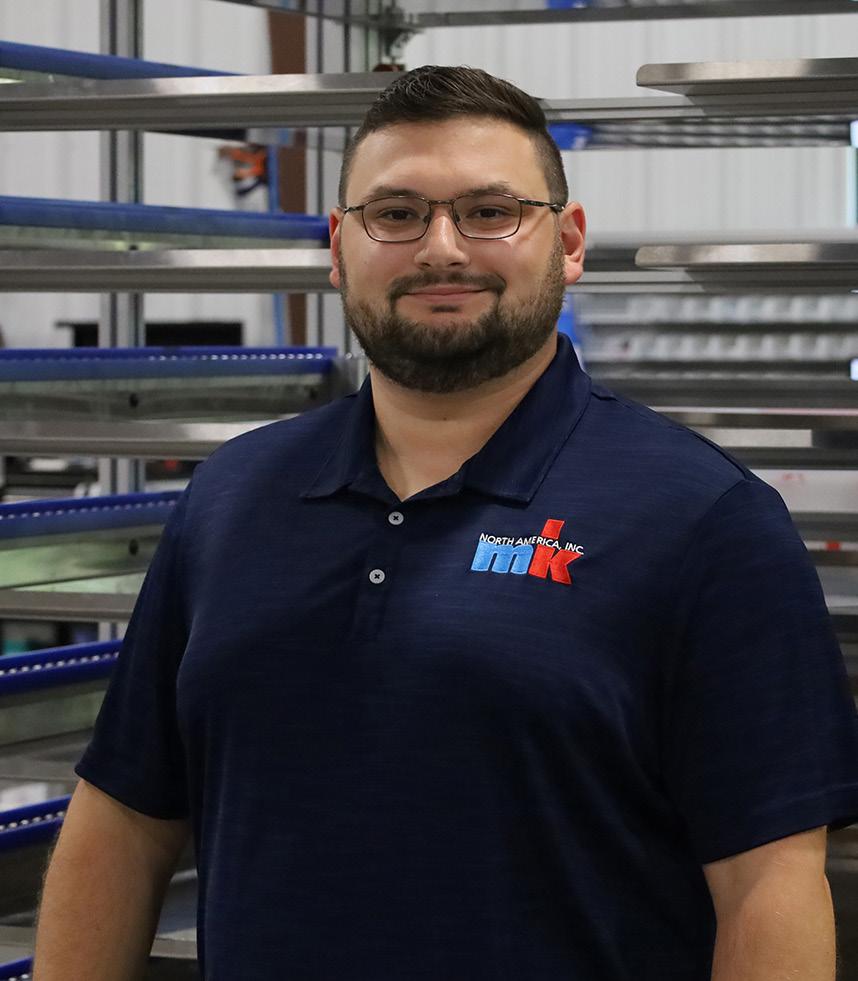
mk North America, Inc. has promoted Scott Blais, Jr. to a sales leadership position within the company, effective September 19, 2022. Scott Blais, Jr. assumes the Sales and Business Development Manager role vacated by Eugene Shaw. Blais will report to Andreas Haussmann, President; and will lead all North American inside and outside sales activities. “Scott will work closely with customers, regional sales managers, and distributors in each territory, and oversee the sales and applications team that works closely with mk customers to develop industry-leading conveyor and material handling solutions,” said Haussmann. “We welcome Scott to his new role and are very confident that the company will continue to flourish with this change in leadership.”
The excitement about Blais’ role is mutual. When asked what he saw for the company and sales team going forward Blais said “mk North America has an incredible team in place to which it is an absolute privilege to collaborate with. I am excited to work tirelessly with our group to deliver the best customer experience possible by focusing on effective communication and improved departmental procedures. I am confident we will achieve our goals as a unified team as we continue to deliver better products and better solutions, each and every day.”
860-769-5500 mknorthamerica.com
2023 JAN. 24-26
Atlanta, Ga.: IPPE (International) Production & Processing Expo) 2023. At Georgia World Congress Center. To registedr, go to: www.ippexpo.org
FEB. 8-9
London, U.K.: The European Biopolymer Summit, conference by ACI London. To register, go to: www.acieu.net
FEB. 9-11
Bangkok, Thailand: Labelexpo Southeast Asia 2023, exhibition and conference by Tarsus Group Limited. At Bangkok International Trade & Exhibition Center. To register, go to: www.labelexpo.com
MARCH 12-14
Boston, Mas.: Seafood Expo North America, exhibition and conference by Diversified Communications. Concurrently with Seafood Processing North America. At Boston Convention and Exhibition Center. To register, go to: www.seafoodexpo.com
MARCH 28-30
Las Vegas, Nev.: SIAL America 2023, global food and beverage business showcase by Comexposium. Concurrently with International Pizza Expo. At Las Vegas Convention Center. To register, go to:
www.sialamerica.com
APRIL 25-27
Toronto: CPMA 2023, annual convention and trade show of the Canadian Produce Marketing Association (CPMA). At the Metro Toronto Convention Centre. To register, go to: www.convention.cpma.ca
MAY 4-10
Düsseldorf, Germany: Interpack 2023, global showcase for packaging and processing technologies by Messe Düsseldorf GmbH. At Messe Düsseldorf fairgrounds. To register, go to: www.interpack.com
MAY 10-11
Boston, Ma.: Robotics Summit and Expo, concurrently with Healthcare Robotics Engineering Forum. Both at the At the Boston Convention and Exhibition Center. To register, go to: www.roboticssummit.com
SEPT. 11-13
Las Vegas, Nev.: PACK EXPO Las Vegas, international exhibition and conference by PMMI, The Association for Packaging and Processing Technologies. At Las Vegas Convention Center. To register, go to:
www.packexpolasvegas.com
2024 MAY 28 – JUNE 7
Düsseldorf, Germany: drupa 2024, global trade fair for printing technologies by Messe Düsseldorf GmbH. At Messe Düsseldorf fairgrounds. To register, go to:
www.drupa.com
Ensuring Complete Product Packaging Integrity in Liquid Pharmaceuticals
By Davor Djukic, National Sales Manager – Product Inspection, METTLER TOLEDO
L
iquid pharmaceutical manufacturers operate under great scrutiny and must set high standards of product quality to ensure that products are safe for consumers and compliant with regulations.
Step 1: Safety First – Getting dosage sizes and pack completeness right
Quality assurance in liquid pharmaceuticals is a matter of life and death, and as such, potential consequences are bound to keep manufacturers on their toes. It is essential to drive high standards in product quality and maintain these standards through the filling and packaging processes that ultimately deliver the finished product.
An advanced checkweigher is the best option to verify dosage sizes and perform careful product handling to ensure extreme accuracy. METTLER TOLEDO’S StarWeigh™ Checkweigher, comprised of high-performance load cells, has the required level of sensitivity to work with lightweight products and to ensure that all products are a uniform weight. To ensure fragile glass bottles and vials are handled carefully during processing, the StarWeigh™ Checkweigher has sophisticated product handling capabilities, including sorting and rejection mechanisms, to minimize risk.
Alongside this fill level of control, another key part of quality assurance is the product completeness check. A sensitive checkweighing system can identify that a packaged product has been completed with all the components that need to be included before a product is shipped to market. This can help businesses ensure significant financial and reputational costs, resulting from product recalls, are avoided.
Step 2: Serialization is the Key to the Digital Supply Chain
The pharmaceutical supply chain is a digital one and cannot operate without serialization – giving each product its own unique and verifiable code – and aggregation of batches of products under a similarly verifiable code. Serialization provides manufacturers with access to an audit trail of events and stages in an individual product’s progression through manufacturing and packaging to distribution. If a recall must be made, the manufacturer can be much more targeted in the scope of its recall, calling back just the specific products that it knows have been affected, rather than entire batches. This helps to limit both recall costs and the impact on the brand’s reputation
Serialization is followed by aggregation, where large batches are grouped together in a box and additional assurance is provided by checking these secondary boxes at key distribution points. Aggregation is made possible through achieving a verifiable, high-quality and readable, code.
Vision inspection systems are responsible for reading and quickly identifying packs with incorrect or poor-quality codes. METTLER TOLEDO also has serialization technology, such as the T33 Automated Serialization, that provides a full 360 degree view of the product surface, so that serialization codes can be verified. This technology allows for the product to be viewed from all sides, regardless of the orientation and thus verifies the serialized codes on the package.

Step 3: Connectivity gives Product Data its True Digital Meaning
Equipping product inspection systems with the right software connectivity is important because it gives manufacturers a chance to gain a real-time picture of production, processing and packaging lines, allowing them to spot potential problems in advance. The data gained through software connectivity is useful for ensuring that good manufacturing practices are being followed and that compliance requirements of different levels of regulations are being met. Without this access to digital data, real-time process monitoring and inventory management cannot meaningfully happen.
Pharmaceutical manufacturers will typically deploy checkweighing and vision inspection, to make additional quality checks as needed. Track and trace is a requirement for serialization and may be optional for aggregation (depending upon the region). Utilizing all three of these technologies will help in supporting top-quality production methods and compliance.
The key point to understanding quality assurance for liquid pharmaceuticals is that strong product inspection capabilities are at the centre of any effective quality assurance program. They help in making the production of liquid pharmaceutical products safe, complete, trackable and compliant with all levels of regulations. They play a critical role in creating and maintaining a transparent and connected digital supply chain while also ensuring brand integrity at all steps along the way.
METTLER TOLEDO Inc.
in Mississauga, Ont.
Packaging toy stories make for a fitting festive gift/Naomi Hiltz
In a little over six weeks families across the globe will be celebrating Christmas, Chanukah and other gift exchanging holidays. Chrismukkah— a blend of Christmas and Chanukah—is a term coined by the character Seth on the popular television show The OC. What could be better than getting presents for eight straight days, and on the morning of
December 25, additional presents underneath a decorated tree? Before the big holiday bas,h however, Santa has a lot of shopping to do. Choosing gifts at this time of the year is no easy feat as companies are under a great deal of pressure to provide the most enticing packaging to attract our young buyers.
Over the last few years, Orbeez have been the new “it” toy. They have become all the rage for elementary school kids and are one of the most popular sensory toys of this decade. These absorbent polymer sensory beads offer umpteen hours of pure enjoyment, which have spawned hundreds of sequels, including The Orbeez Color Meez. This creative, interactive toy from by Spinmaster is sold with a giant bottle of clear Orbeez and three different colored dyes to decorate them with. The box, which encases the toy illustrates a myriad of exciting photos and artwork on all sides with vibrant colors that will certainly engage kids of all ages. The front and back of the box highlight photos of happy children with smiles of joy, holding and playing with the product. The writing on the box outlines the step-by-step instructions of how to set up the toy in a simple, child-friendly way. Another interesting feature is the corrugated board the product is packaged in. Being 100-percent recyclable and biodegradable, the cardboard does not lose durability or stiffness over time, and is also more economical than some other packaging materials. Perhaps the best packaging feature of the Orbeez Color Meez is the cut-out window on the side of the cardboard, which allows buyers to preview the toy before purchasing. At $16.99 each, this product is well worth the investment.
Next on the shopping list is the Zuru Cotton Candy Slime. The packaging concept for this toy is brilliant, as the company has incorporated the packaging as part of the toy itself. This scented, fluffy, stretchy slime is sold in four different colors and stretches over 3,000 per cent in size. The plastic-shaped cotton candy resembles the ‘real’ treat one would normally purchase at a fair. The top portion of the cotton candy slime is covered by a wraparound plastic seal with double perforated lines for easy removal. This wraparound plastic depicts the toy’s visual advertising, and is used like a canvas to reveal all of the amazing attributes associated with it. The advertising details everything and anything you could want to know about the product, including the slime’s stretch size, the cotton candy scent and most importantly, a photo of a happy girl playing with her slime. The fonts and graphics displayed resemble similar styles one may discover at an amusement park. Perhaps the most intriguing aspect of the packaging is that it can be used over again to store the product after each use. Making the packaging part of the toy is both creative and cost-effective.
Funko Pops are the action figures of the next generation. They are comparable to figurines but based on movies, video game characters, comic books, popular culture, and other icons. The last product on our shopping list was the Ravanger Thanos Funko Pop, based on the popular Marvel franchise, “What If…?” series. This special- edition package portrays the Marvel logo on the packaging along with photos of the character and other collectables in the series. During the 1980s, my generation had this odd impulse to play with our toys - especially the Star Wars action figures. Years later, we learned that it would become devalued if it was opened. Today, everyone is a collector and the Funko Pop marketing people are aware of this. Fo this reason, they’ve strategically designed the packaging to protect the figures from sunlight and dust, with the sole intent of allowing the toy to stay in mint condition for as long as possible. For the past 40 years, the majority of these action figures have been available in transparent packaging that was not well though out in terms of maintining the toy’s long-term resale value. The issue with this type of packaging style is it allows dust to collect easier, making the toy more susceptible to damage by sunlight. Moreover, the the plastic on top of the figurines often tended to soften over time, undermining the overall quality with time. So kudos to. Funko Pop for correcting this packaging design flaw by creating a paper box which encases the figure with a transparent, plastic window—allowing the toy to be seen. The figure itself is also enclosed within a plastic tray for additional protection. The paper box is not only 100-percent recyclable but is less likely to be ruined by dust and over- exposure from the sun. As with most pop culture toys, Funko Pop’s fonts and graphics are loud and colorful, attracting their targeted young buyers and collectors.
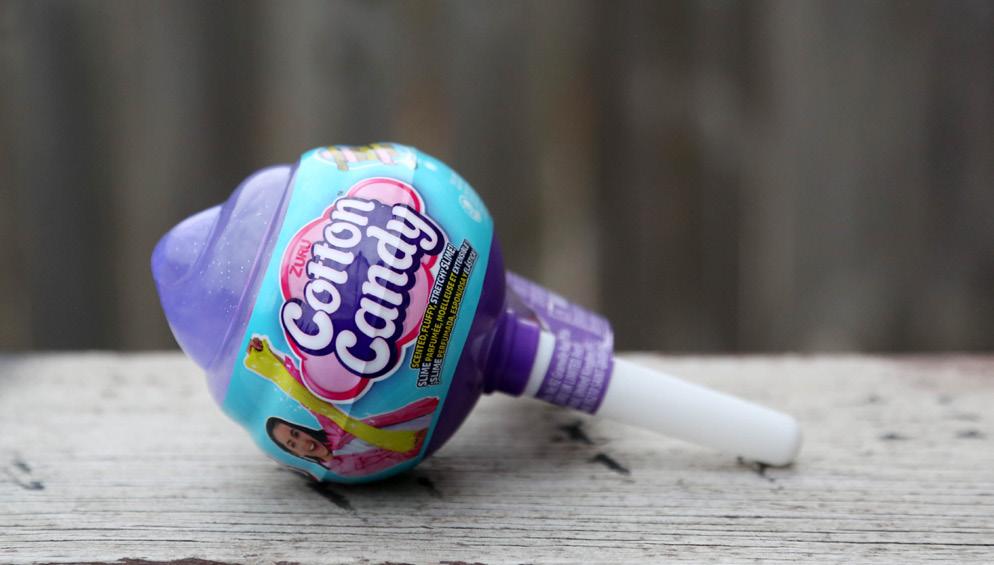
(Clockwise) Popular toys for this season’s festive gift-giving include the Zuru Cotton Candy Slime; the Orbeez Color Meeze coloring kit, and Marvel’s Ravanger Thanos Funko Pop action figure.
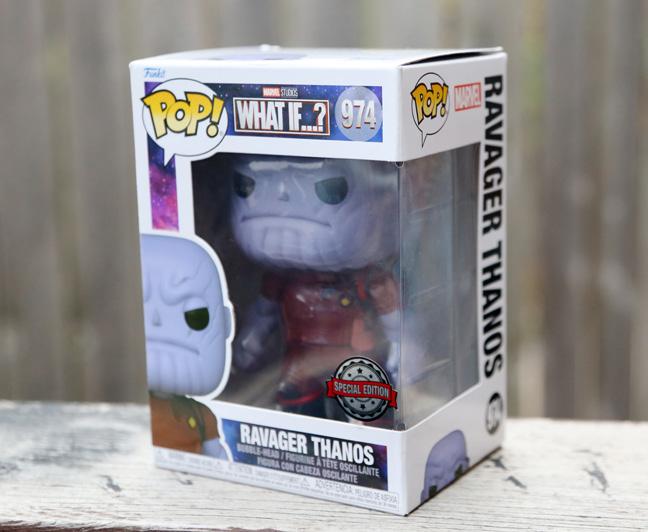
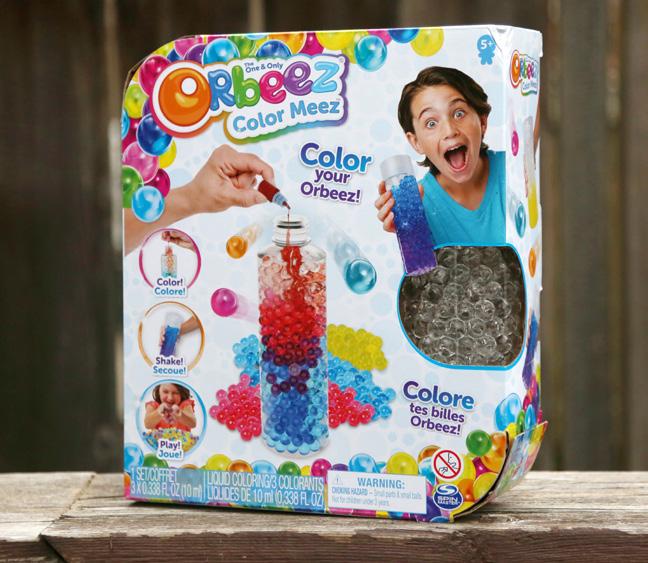
NAOMI HILTZ is a freelance photographer living in Thornhill, Ont.
AD INDEX
Abbey Equipment Solutions 26 AGFA Inc. 24 Fortress Technology Inc 9 Harlund Industries Ltd 11 Heat and Control IFC Imperial Dade Canada Mettler Toledo mk North America
OBC 39, IBC 38 Paxiom Group Inc 7 Pilz Automation Safety Canada, L.P. 8 Plan Automation Regal Rexnord Reiser / Robert Reiser & Co. Shawpak Systems Stock Packaging Canada
6 20 5 31 10 Syntegon Packaging Technology, LLC 2 Uline Canada Corporation 25 VC999 Packaging 14 Videojet Canada 1 Zund America, Inc. 36, 37
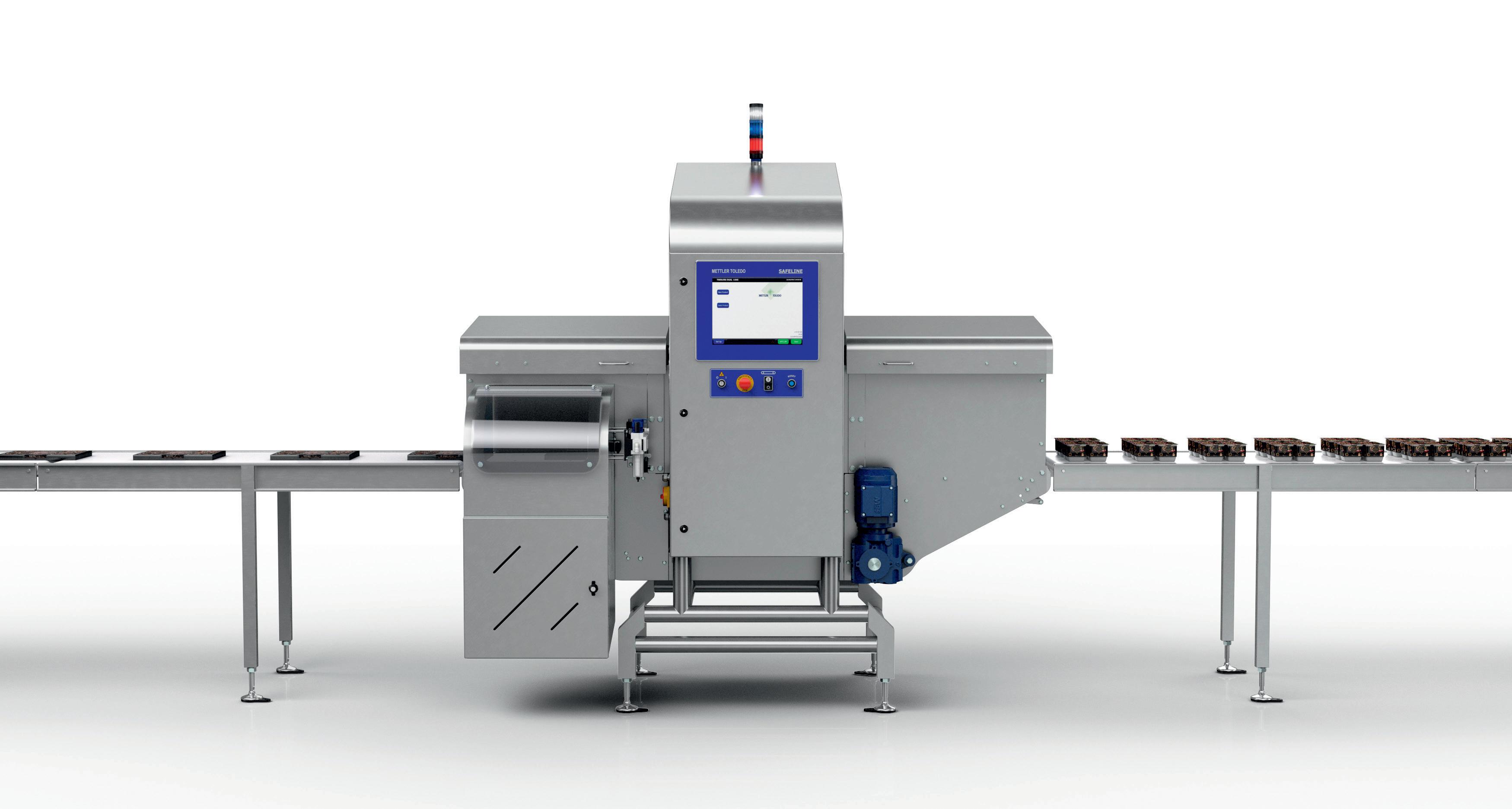
Revolutionary DXD Technology to Detect Hard-to-Catch Contaminants
Capable of detecting hard-to-find contaminants, METTLER TOLEDO’s new DXD and DXD+ dual energy detectors can be fully integrated into the X36 X-ray system. These highly advanced technologies support brand protection and compliance, even in the most challenging applications, while increasing production productivity.
METTLER TOLEDO’s dual energy detector solutions deliver: • Unrivaled detection capabilities • Optimized performance for challenging applications • Intuitive, user-friendly software • Flexibility to suit unique production demands
Learn more about how the DXD and DXD+ can enhance product integrity and brand protection by visiting www.mt.com/ca-dxd-wp
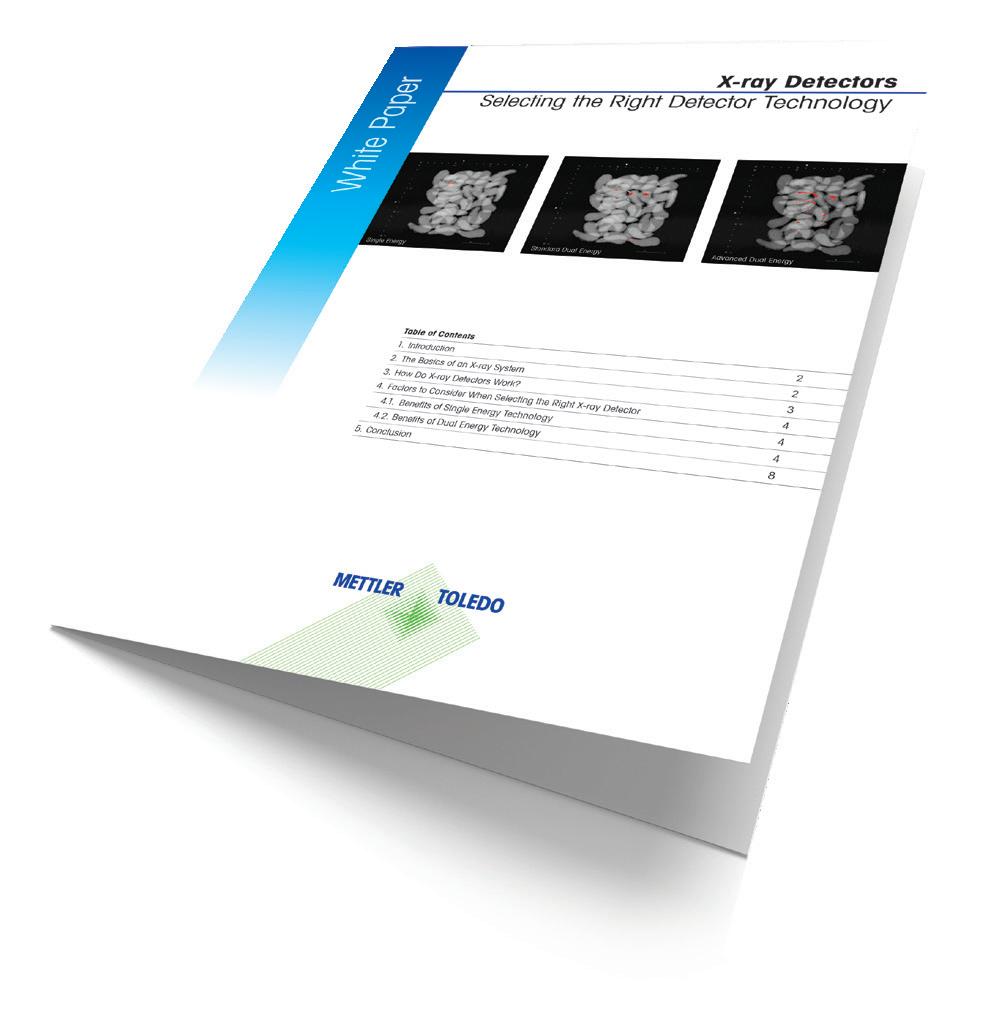