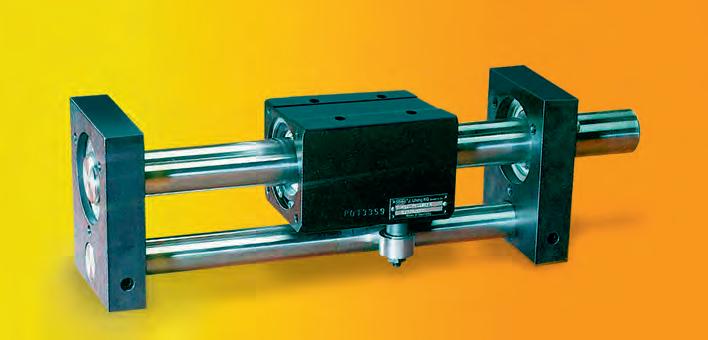
1 minute read
Rolling Ring LINEAR DRIVES
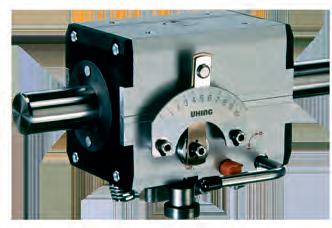
the final shape is reached or to polish to a consistent finish.
One huge advantage is that any tool can be used for support removal and finishing. If it is already known what tools work well with the materials or the types of supports printed, the same exact tools can be attached to a robot to automate with more confidence. With today’s technology, the steps to add a new custom tool are basically like adding a new type of endmill to a CNC machine and doesn’t require a system integrator that charges by the hour.
Rivelin Robotics, which specializes in metal AM post-processing, already has products that do this. The company specializes in the development and installation of robots for a wide range of AM post processing applications. In the context of removing supports from metal additively manufactured parts, Rivelin offers advanced robotic solutions that are specifically designed to perform this task reliably and accurately.
The company’s robots provide a range of benefits over traditional CNC machines, such as improved speed, accuracy and repeatability when applied to support removal and finishing. They are also highly flexible, which allows them to be easily adapted to different applications and processes.
Rivelin’s robots are also designed with safety in mind, with protective casing and safety features that reduce the risk of accidents and injuries. Moreover, power and coolant requirements are far lower than is the case with CNC machines, which helps increase resource efficiency and energy efficiency while at the same time reducing waste.
To summarize, robots are emerging as a superior solution compared with CNC machines for the automated removal of supports from metal AM parts due to their speed, efficiency, flexibility, accuracy, repeatability, safety, cost-effectiveness, and sustainability.
The use of robots in this process not only results in a better finished product, but also provides a safer, more sustainable and more cost-effective end-to end manufacturing process. |DE www.rivelinrobotics.com