
10 minute read
PLUMBING PRODUCTS
The Teledyne Flir MR265 Moisture Meter and Thermal Imager is designed to visually scan large areas to identify and locate moisture issues, air leaks and electrical problems. The dual thermal imager and measurement tool combines a 160 × 120 resolution thermal camera, visual camera, laser pointer, and both pin and pinless moisture detection for fast leak identification and measurement. flir.com Powers, a Watts brand, has added remote connectivity to its IntelliStation Jr. digital mixing valve. Now with WiFi capability, connecting to the Watts OnSite mobile and web app for commercial facilities provides access to mixing valve data for building owners or contractors. BACnet and Modbus were already native to the valves, but now Cloud connectivity provides an additional way to view and adjust mixed outlet temperature. www.watts.com
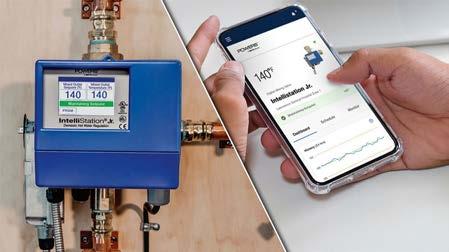

PRIER’s P-6IV irrigation supply valve for areas subject to freezing comes with a built-in elbow that swivels to allow for easy installation. Designed with the contractor in mind, it allows servicing from the exterior of the structure. A ¼-in. NPT port in elbow allows for irrigation system winterization and air blowout. The heavy-pattern cast brass hydrant with a nickel-plated body resists corrosion and offers a triple-seal positive shutoff system. The valve is available in 12 lengths. prier.com Webstone has enhanced its E-X-P Complete product line, now offering everything needed for a gas-powered tankless water heater (TWH) installation. The new kits combine E2 series or Ultra-Compact series TWH service valves with Webstone’s forged brass gas sediment trap. Each ¾-in. kit includes two colourcoded service valves, a residential pressure relief valve, the sediment trap kit with an FIP ball valve and a 24-in. gas flex line. Connection options include press, sweat, FIP, push and PEX. webstonevalves.com
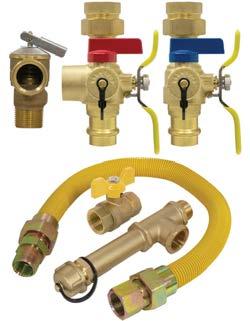

The versatile RIDGID pipe saw is transportable and cuts 1-in. to 12-in. pipe with up to a ½-in. wall thickness. Configured to cut steel and stainless steel, with a switch to an optional blade it can cut plastic and cast steel. The saw secures to the pipe with a three-point roller system that sets up and cuts up to 12-inch pipe. Well-placed handlebars and feed rate speed monitoring with an LED interface enable controlled rotation from an ergonomic position. ridgid.com The Symmons Rapid Install Bracket is a shower valve mounting bracket made of heat resistant nylon that creates a stable installation, particularly when using non-rigid supply lines, allowing installers to go back and service the valve without fear of damaging the lines. The bracket sets the rough-in depth and features over 1-in. of give for completing installation with the surrounding tile/shower wall. symmons.com
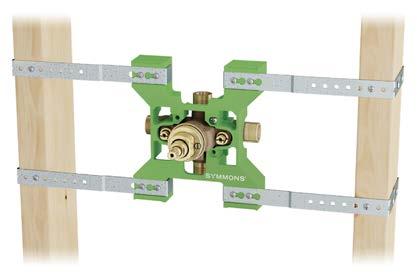
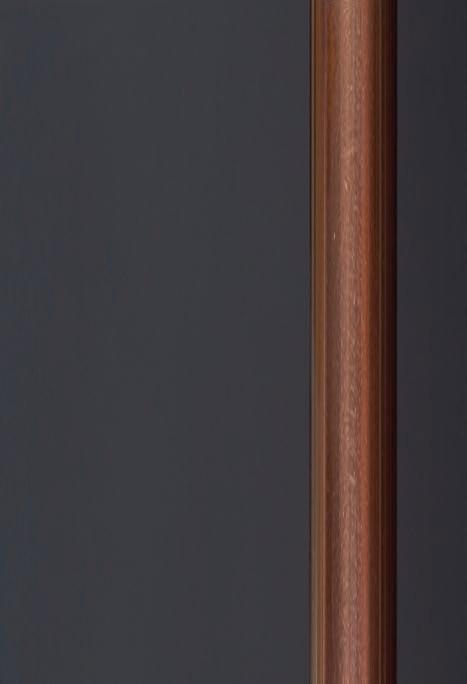
STAY CONNECTED…
Simply fax this form today or visit www.hpacmag.com and click subscribe! FREE to qualified subscribers!
Please fill in the following and fax today to 416-442-2230 or visit our website and click on subscribe www.hpacmag.com
Name
YES! I wish to receive/continue to receive HPAC Magazine absolutely FREE! No
Title
Company
Address
City Province Postal Code
Business Phone # ( )
Business Fax # ( )
Your FREE subscription also includes our FREE e-newsletter, please provide your e-mail address below:
E-mail:
Signature
(Must be signed and dated to be valid) Date / /
D M Y
1. Company Business Activity? (Check ONE only) o Mechanical Contractor o Refrigeration Service Engineer/Contractor o Fuel Oil Dealer/ Contractor o Wholesaler/Distributor/Agent o Consulting Engineers/Specifying Writer o Plumbing Inspector o Government o Hospitals and Related Institutions o Utilities o General Building Construction o Others Allied to the Field (please specify) –––––––––––––––––––––––––––––––––––––––––––
2. Do you specify, purchase and/or approve the purchase of mechanical products or services? o Yes o No
3. Company Job Sector? (Check ALL that apply) o Commercial o Residential o Industrial o Institutional
4. Number of employees at this location? o 1 - 4 o 20 - 49 o 5 - 9 o 50 - 99
o 200 - 499 o 500 - 999 o 10 - 19 o 100 - 199 o 1000 - 2499 o 2500 + o Unknown
5. Company Job Activities? (Check ALL that apply) o Plumbing (i.e DHW, Piping etc.) o Ventilation o Hydronic Heating
o Refrigeration
o Forced Air Heating o Fire Protection o Electric Heating o Air Conditioning o Other –––––––––––––––––– (please specify)
UNDERSTANDING EVAPORATORS
A fundamental element of the vapour compression cycle in refrigeration, it’s vital to revisit the basic functions of evaporators and how to keep them operating at their peak. BY DAVE DEMMA
Evaporator [ ih-vap-uh-rey-ter ] An evaporator is a device in a process used to turn the liquid form of a chemical substance into its gaseous-form/ vapour. The liquid is evaporated, or vaporized, into a gas form of the targeted substance in that process.
The vapour compression cycle is a brilliantly designed machine which, when designed and applied properly, can maintain a designated space at a temperature that is lower than that of the immediate surroundings. It accomplishes this by transferring heat from the space to a heat transfer medium—in the case of the vapour compression cycle, that medium is a refrigerant.
The ultimate goal of the vapour compression cycle is to transform the refrigerant into a saturated fluid at a temperature that is low enough to facilitate the heat transfer necessary to achieve the desired temperature in the space.
There are four required components in the vapour compression cycle, each having its own specific function which contributes to that ultimate goal:
Compressor: receives low pressure/ low temperature vapour from the evaporator and transforms it into high pressure vapour. Heat is added to the vapour during the compression process, and it leaves the compressor as a high pressure/high temperature vapour.
Condenser: receives high pressure/ high temperature vapour from the com-

Rusted and frozen evaporator coil resulting in compromised performance.
pressor and transfers heat from it. This allows it to change state from a vapour into a liquid. The liquid temperature is lower than the compressor discharge temperature, but still relatively warm.
Expansion Device: receives the high pressure/warm temperature liquid and forces it to undergo a pressure drop. Lowering the pressure allows the refrigerant to assume a new saturation temperature, which corresponds to the new lower pressure.
Evaporator: receives the low pressure/lower temperature saturated liquid from the expansion device, and it flows through the tubing in a finnedtube coil. The relatively warmer air in the space is circulated through the fins, allowing the heat from the air to be transferred to the saturated refrigerant in the tubing, thus cooling the space.
While each component in the system is of equal importance, the evaporator is where the space temperature reduction takes place, and it is simply the result of heat transfer.
Evaporator capacity is based upon several factors: • Type of refrigerant • Refrigerated space temperature • Design condensing temperature • Amount of heat to be removed (heat load) • Humidity requirements for the space
For example, if the design requirement is to keep beverages at 35F in a
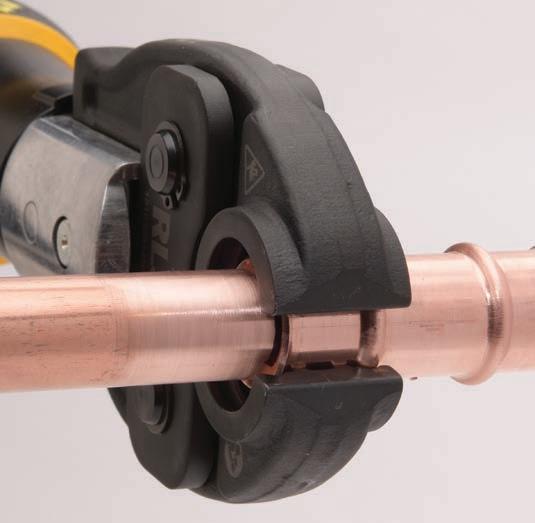
When you want a faster, safer alternative to brazing...
Trust the technology that’s been proven more than 10 million times since 2015: RLS press fittings.
While there will always be a need to braze, more and more HVAC/R contractors are also taking advantage of the time and cost savings – and proven reliability – of RLS press fittings. They connect in seconds, without the need for a torch, gas, nitrogen and everything else required for brazing (like hot work permits and fire spotters). With more than 10 million fittings installed successfully around the world since 2015, RLS technology has been proven beyond any doubt. Designed specifically for high-pressure HVAC/R systems, our patented double circular press results in two 360˚ metal-to-metal connections, creating a permanent mechanical joint every time, with no leak paths. So with RLS, you can connect with confidence!
Learn more at rapidlockingsystem.com and become a certified installer at training.rapidlockingsystem.com. RLS Advantages:
• Connects in 10 seconds
• UL Listed to 700 psi • No gas or brazing materials • No flame, no fire hazards • No burn permits • No fire spotters • No nitrogen purging • Works in tight spaces • Millions of fittings installed
Look for the flare!
That’s how you know it’s for HVAC/R.

refrigerated cabinet, then the system should be providing 25F saturated liquid refrigerant to the evaporator inlet. This will allow a 10F TD (temperature difference between air entering the evaporator fin-tube bundle and the saturated refrigerant flowing through the evaporator). This 10F difference allows the heat content in the higher temperature air to be transferred to the lower temperature refrigerant.
The amount of refrigerant necessary (mass flow rate) will depend on the type of refrigerant, the refrigeration load and the ambient condition. Of course, the design load is the maximum amount of heat transfer necessary to keep the product or space at the design temperature on the absolute most miserably hot and humid day in the summer time.
For the remainder of the year the equipment will be oversized. Yet, within a 24-hour period of any given day there will be continuous variations in the load (box doors being opened, product being loaded, changes in ambient temperature, etc.). To compensate for the varying load condition a thermostatic expansion valve (or electric expansion valve) will modulate open/closed regulating refrigerant mass flow in response to the load at any given moment.
Factors that affect evaporator performance can be broken down into two categories, air flow and refrigerant mass flow.
AIR FLOW
Evaporator capacity is, in part, based on the quantity of air flowing through the finned-tube bundle measured in cubic feet per minute (CFM). If any condition exists that would cause a reduction in the CFM, this will result in a reduction in evaporator capacity. For example: 1. Dust and dirt particles floating in the air are circulated through the exterior of the evaporator by the evaporator fans. These particles will accumulate on the evaporator fins and tubes. If evaporators are not cleaned periodically this buildup can seriously impede the air CFM, resulting in
a loss of evaporator capacity. 2. Air conditioning systems will employ filters to reduce the amount of dust/dirt that can foul the evaporator surface.
Should these filters become restricted with a large buildup this will result in an air CFM reduction. 3. Return air ducting, if undersized, will result in an air CFM reduction. 4. If an evaporator fan has been replaced with a blade of the wrong pitch, this will result in an air CFM reduction. 5. If an evaporator fan motor has been replaced with a motor with a lower RPM than the original motor, or a multispeed motor incorrectly set up to operate at the wrong speed, this will result in an air CFM reduction. 6. Evaporators utilizing belt drive motors are always susceptible to worn/slipping belts, which will result in an air CFM reduction. 7. Evaporators with belt drive motors may utilize adjustable drive pulleys. If the pulleys are not adjusted correctly, this will result in an air CFM reduction.

REFRIGERANT MASS FLOW
Evaporator capacity is also, in part, based on the refrigerant mass flow. At a given refrigerant saturation temperature there is a finite amount of heat that can be transferred to each lb. of refrigerant mass flow. As such, there will always be a specific requirement of refrigerant mass flow to meet the load demand at any given time. If any condition exists that would cause a reduction in the necessary refrigerant mass flow this too will result in a reduction in evaporator capacity. 1. Many reduced refrigerant mass flow issues can be directly traced to an underfeeding thermostatic expansion valve (TXV). This can be the result of an incorrectly sized expansion valve, a faulty valve adjustment, contaminant buildup inside the valve causing a restriction in flow, a defective thermostatic element (which reduces the valve opening force), incorrect thermostatic charge, or in some cases bulb charge migration (where the element head is colder than the element bulb, and the charge migrates to the colder area). 2. There is a certain percentage of liquid refrigerant that flashes into vapour during the expansion process and is