
3 minute read
THAT WAS CLOSE:
Five things to examine after a near miss
WHEN YOU IGNORE a near miss, you are wasting a golden opportunity to prevent the same circumstances from arising again and causing injuries to workers. Most of us are used to the idea of reporting a hazard when we see one. We know that it is our responsibility to ensure something is done about it before anyone is harmed. We also know why it’s important to report incidents when someone has been hurt.
However, when no one notices the hazard beforehand and no injury or damage occurs, do you still need to do something? Reporting a near miss is somewhere between reporting a hazard and reporting an incident. It can be a bit confusing. A near miss is an incident in which there is no injury or property damage, but, given a slight shift in time or position, injury or damage could have occurred.
All organizations, including warehouses, need to include near misses in their health and safety reporting strategies. They provide a golden opportunity to control a hazard that you may not have known existed, without anyone experiencing an injury. A near miss report will trigger an investigation that lets you identify the root causes and develop controls to prevent what could be a costly incident that impacts both employees and the business.
Encourage near miss reporting
Near misses can be common events in warehouses. Here’s an example: an employee is walking near a loading dock, where lift trucks are emptying trailers and driving goods to other areas of the warehouse. Suddenly, a lift truck seems to come out of nowhere and very nearly hits the pedestrian, who takes evasive action. The driver and pedestrian acknowledge each other with relief, but don’t report the close call.
Non-reporting of near misses hampers your efforts to protect workers, so it’s critical to understand why workers are hesitant. It may be fear of getting themselves or others in trouble. That’s a sign that you need to develop a more positive safety culture, one where reporting is safe, not punished.
Hygiene for Workplace Safety & Prevention Services (WSPS).
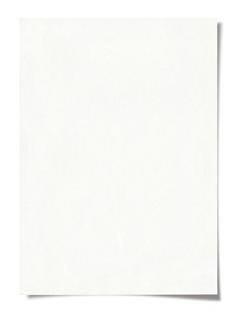
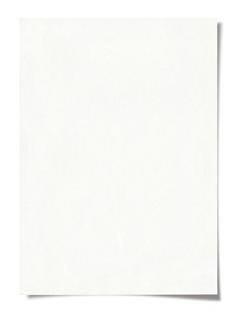
Communicate why you need near miss reports, what you will do with them, and how they can help prevent an incident from happening. Don’t discipline; commend. Give workers who may still be reluctant an easy way to report near misses anonymously.
Get to the root cause(s)
When you receive a near miss report, it needs to be analyzed to isolate root causes and identify controls. There are five elements to look at: people, equipment, materials, environment and processes. Ask questions to help you figure out all possible contributing factors.
Using the warehouse near miss example above, for instance, you could ask:
People:
Was the operator trained to provide right of way to pedestrians?
Does the operator use their horn to warn pedestrians of their presence when necessary?
Equipment:
Does the lift truck have safety features including spotter lights to warn pedestrians before the lift truck can be seen?
Do all pedestrians wear high visibility apparel?
Material:
Can the operator see over the pallet load when travelling forward?
Are pallet loads secure to prevent unwanted movement when stopping or turning corners?
Environment:
Are pallet loads stored on the floor in designated areas to reduce pallet clutter?
Are there designated aisleways for lift truck operators and walkways for pedestrians to ensure separation between the two?
Process:
Has an assessment been completed to determine “no pedestrian zones”?
Are employees permitted to walk throughout the warehouse without using designated walkways, resulting in operators encountering pedestrians unexpectedly?
Control the situation
Once the root cause(s) has been identified, the next step is to develop and implement appropriate controls to eliminate risks. These might include:
People: Provide training to both operators and pedestrians, which includes right of way at intersections.
Equipment: Install safety features on lift trucks including spotter lights and ensure everyone wears CSA approved high visibility apparel.
Material: Keep loads on forks at a height that gives the operator a clear line of sight.
Environment: Store pallet loads in marked designated areas and install floor markings to separate the lift truck aisleway from the pedestrian path.
Process: Establish “no pedestrian” zones where there is busy lift truck movement, such as loading docks, and enforce.
When you take the time to report, investigate, and analyze near misses, you greatly contribute to a healthier and safer workplace for all. If you ignore them, you waste an opportunity to protect everyone who enters your workplace.
