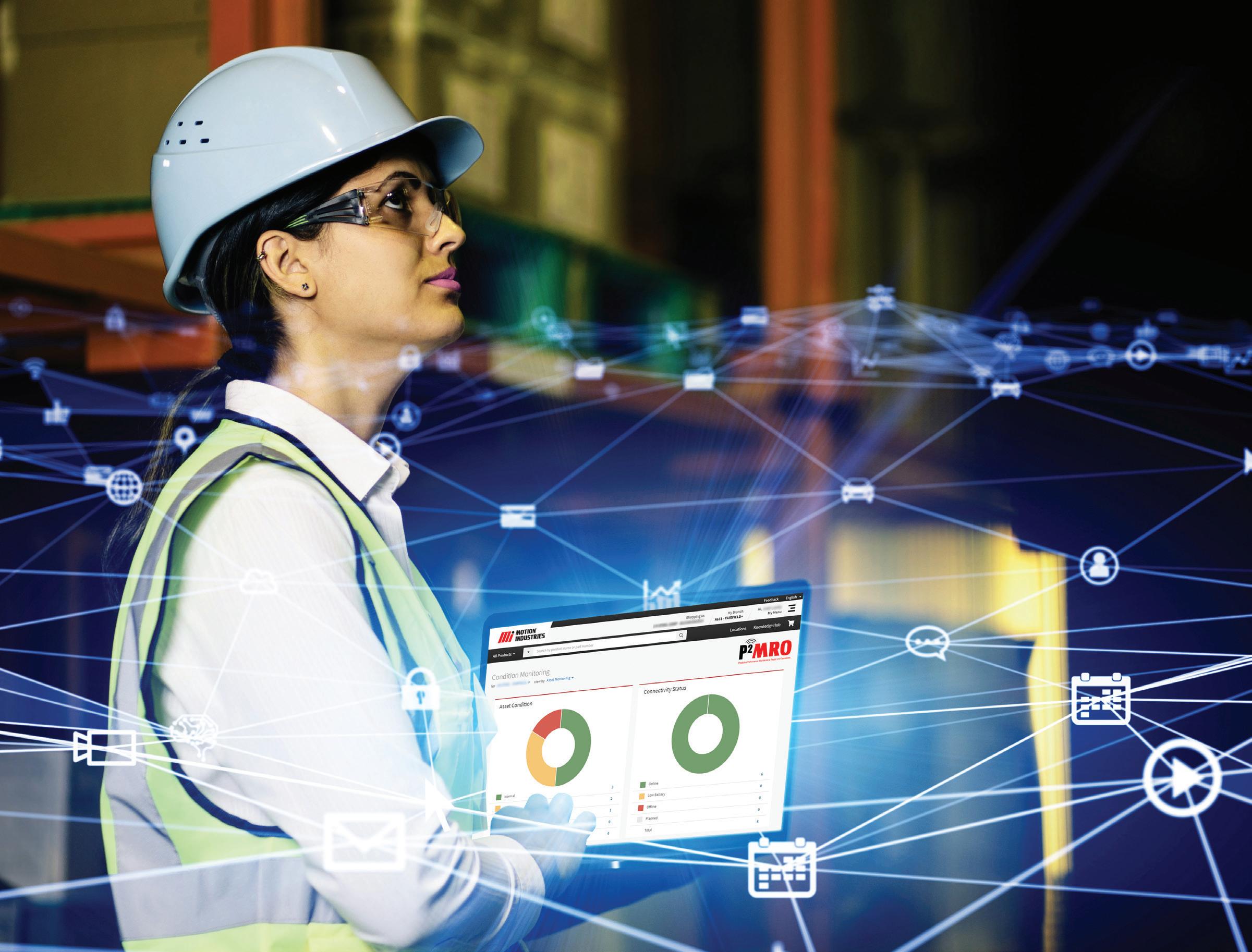
11 minute read
No More Firefighting
Imagine an industrial site or manufacturing facility that actually accomplished the mission of every maintenance and reliability professional – zero per cent unplanned downtime.
BY JUSTIN LESLEY
That nirvana seems so distant to most of us, that we don’t even consider it a real possibility. As farfetched as it may seem, let’s indulge ourselves and think of what it would take to realize our dreams and master our equipment. Theoretically, accomplishing zero per cent unplanned downtime is dependent on management’s ability to meet two criteria: 1) to properly plan maintenance activities during scheduled downtime; and, 2) having the proper resources (parts, people, and know-how) to execute those jobs.
Can we ever get there? Can we ever convince company leaders to approve funding for the tools we need to revolutionize our operations and improve reliability metrics to approach perfection? The only hope for success and funding is a relentless commitment to data.
What does it mean to be committed to data and why is data so integral to planning and executing maintenance efforts? Being committed to data means that we must leverage modern tools to record all maintenance tasks, to collect machine performance data, to track spare parts inventory, and to assign dollar figures to breakdowns and events that interrupt production.
That last part is an area where maintenance and reliability professionals rarely shine; generally, because we are too busy fixing broken equipment that is costing a lot every second it’s out of service. We can all relate to the madness of being called out to investigate a catastrophic failure on a production line in the middle of a shift, or worse, a component within the facilities infrastructure that affects the entire plant.

In the best-case scenario during a you to prioritize and schedule down- PdM solutions, which has created a race breakdown, you and your team can iden- time before catastrophic failures inter- among incumbent industrial providers tify the problem and have the tools and rupt production. as well as new technology players. Each parts required to repair it, but that’s not Maintenance management software of these solution providers must comalways the case. For example, if a store- and CM solutions have been around for pete in the marketplace based on cost, room doesn’t have a spare pillow block decades, and they have been continuous- functionality, ease of use, field support, bearing to replace the one that (hypo- ly improving in both functionality and and interoperability with existing techthetically) seized, and even if the part is accessibility as new providers vie for mar- nology infrastructure. available at the distribution centre across ket share. This is a wonderful trend for With regard to CM solutions, wireless town, the waiting game for spare parts users, as modern technology tools now communication has drastically reduced can get expensive quickly. The cost of have more functionality; they are more the cost of installation and enabled downtime could be in the thousands or user-friendly and are more cost-effective. seamless scalability. Additionally, sentens of thousands of dollars per hour, de- The “Industrial Internet of Things” sor technology has been enhanced and pending on the industry and particular (IIoT), and Industry 4.0 have produced machine learning algorithms have been asset that is down. Such costly interrup- a wave of demand for sophisticated incorporated into solutions to automattions can unfortunately happen all too often. Do you know the value of production time in your facility? Do you know what it is per department or even per line?
Every business management decision must equate to financial drivers, which is why it is imperative to track the cost of downtime. Maintenance and reliability professionals have to clearly understand the financial Grasp your implications of lost production, and use data to put ourselves in a position to succeed. In practice, being in position to succeed means having the right resources Industrial performance to do jobs effectively: technology, people, and support from leadership to plan downtime, prioritize repairs, and make upgrades.
Here are two technology resources that maintenance and reliability teams should be using to enhance their effectiveness. • Maintenance management software – If you are still using paper work orders and/or simple spreadsheets to manually track maintenance activities, you are robbing yourself of the ability to track critical metrics. Modern maintenance management software simplifies records, and integrates with ERP systems to capture the cost of maintenance including labor/time and materials/inventory. • Predictive maintenance (PdM)/ condition monitoring (CM) solutions – Transitioning from time-based to condition-based maintenance (CBM) is key to efficiently managing resources. PdM solutions enable your team to detect failure trends of www.total-canada.ca 1 800 463-3955 degrading equipment, allowing

ically detect and interpret trends in performance metrics.
If you haven’t had experience with modern CM solutions, you may be wondering how they will complement your team of mechanics, electricians, engineers, and technicians who currently bear the burden of ensuring your facility runs smoothly. The basic idea is that leveraging these tools puts your team in a position to work smarter. They will be able to target problematic equipment before it fails, skip the guessing game of diagnostic inspections, prioritize work based on remaining equipment life data, and ensure appropriate spare parts are in inventory ahead of shutdowns.
Along with the technology trend, there is a more alarming trend in progress related to maintenance and reliability human resources. Industrial and manufacturing environments are becoming more automated, meaning there is more machinery to maintain. At the same time, fewer young people are entering maintenance-related fields of study or directly entering the workplace. The resulting reality is that we must maintain more motors, pumps, fans, gearboxes, bearings, compressors, and the rest of the equipment within plants with less people. The only way we can accomplish that task is to leverage technology to work smarter and use maintenance management software to rationalize our planned downtime practices.
Though PdM solutions can become indispensable tools in your overall reliability strategy, implementing them can be a significant challenge. Solution providers have been through generations of development with a significant design focus on ease of use. Even so, not all sensor solutions are compatible with certain environments or applications. When investigating PdM solutions, some of the features to evaluate are battery life, wireless communication range, IP and hazardous area ratings, alert/notification functionality, sensor size (for confined space areas), sensor temperature ratings, installation method, commissioning and setup process, scalability, and on.
The good news is that the market for PdM solutions is expanding, and providers are focusing on specific applications and/or equipment types in order to meet the needs of the market. As the offerings continue to expand and diversify, training and system integration could become significant factors to consider before implementation. A professional evaluation of your facility and a review of applicable PdM solutions to address specific needs may be the best place to start the journey into the future of maintenance where downtime is always planned.
Two modern technology tools – maintenance management software and PdM/ CM solutions – can drastically improve maintenance and reliability efforts when used properly. Therefore, a company’s culture could have more to do with its success than any sensor or software solution. A cultural commitment must be made to fully leverage the functionality of maintenance and reliability systems, in order to generate and analyze asset management data.
That means believing in the value of data analytics, and training people to trust the results when trends are detected. Additionally, make sure to be grounded in the reality that virtually no process can run continuously without being maintained. A cultural commitment to reliability means building space in the schedule to take equipment offline for maintenance, and the only way to accurately plan downtime efforts is with a relentless commitment to data. MRO

Justin Lesley, Industry 4.0 Innovation Manager at Motion Industries, directs IIoT strategy and partnerships related to the MRO industry. His career centres on operational efficiency supported by his Lean Manufacturing and Six Sigma certifications combined with his engineering credentials.
WHAT’S NEW IN PRODUCTS
ABB SafetyInsight ABB Ability SafetyInsight digital software applications support companies through the lifecycle of process safety management. The software digitalizes early engineering technology (ET) data to create a process safety digital twin, using this data to give context to data generated through IT and operational technology Endress+Hauser platform Endress+Hauser platform approach for real time monitoring of critical parameters and collection of true representative samples for lab testing. With Promag flow measurement, the monitoring solution based on Liquiline platform provides risk mitigation to avoid incurring violations and pen
A complete platform includes four Memosens sensors (for pH, turbidity, spectral absorption coefficient for organics and dissolved oxygen) connected to a Liquiline CM44x series Festo VTSA-F-CB Festo VTSA-F-CB, with serial communications added to existing parallel communications capability. VTSA-F-CB’s internal bus system allows users to actuate up to 96 valve addresses, in four zones, on one valve terminal and one fieldbus node. VTSAF-CB can mix 18 mm and 26 mm valves on the same manifold, reducing size and cost of the manifold.
VTSA-F-CB features four CPX/ pneumatic interfaces: basic interface when safety control is not required, two integrated PROFIsafe versions, and a version that makes it possible for an external safety fieldbus module to (OT) systems.
SafetyInsight enables engineering data to be digitalized, and accessible by operation and maintenance teams. The addition of IT/OT data provides near real-time updates. The suite has process safety dashboards to provide the information.
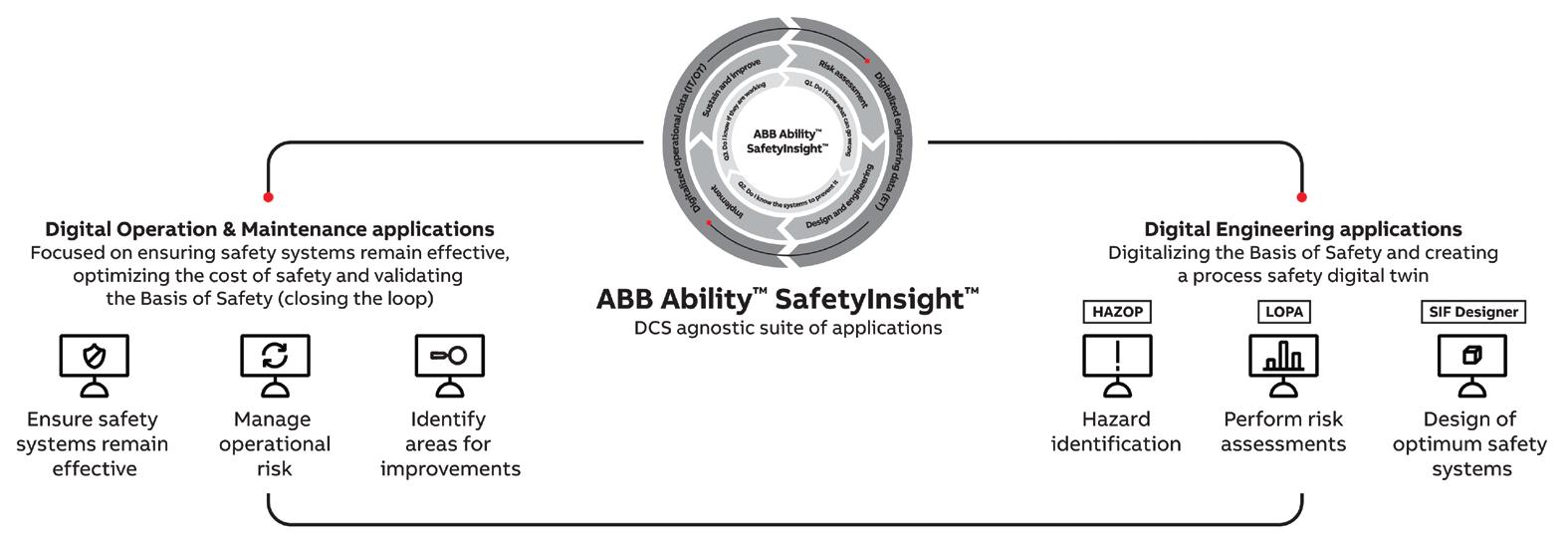
www.abb.com
transmitter, with Liquistation CSF48 and CSF34 monitoring stations, and CA80 series colourmetric analyzers for phosphorus and ammonia.
www.ca.endress.com
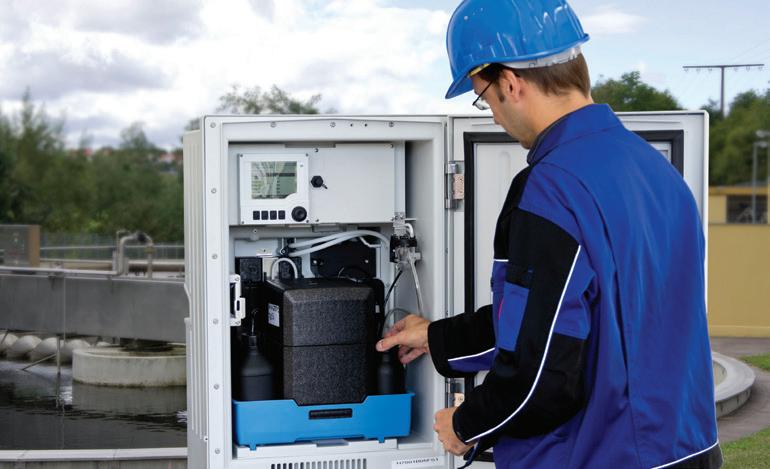
directly control three pneumatic safety zones.
VTSA-F-CB configuration options include a pilot air switching valve, and a safety soft start/quick exhaust valve. New vacuum generator VTSA-F-CB has an air saving feature with ejector pulse.
www.festo.com
For more product news, visit www.mromagazine.com/products
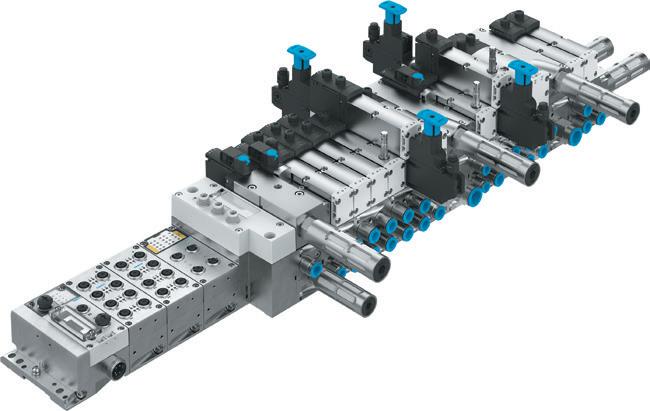
Schneider Electric TeSys island Schneider Electric TeSys island is a digital load management system, that digitally integrates multifunction motor starters into machine control panels. TeSys island features a catalog of TeSys avatars that act like a digital twin on top of the physical device.
In operation with EcoStruxure Machine solution, TeSys island minimizes machine stoppages by providing access and diagnostic data by generating pre-alarms when unusual electrical load behaviour is detected. Information can be accessed remotely. TeSys island provides device health, load level energy consumption, and application-specific protection data.
The system manages motors and other electrical loads up to 80A, and electrical and mechanical configurations can be updated throughout a machine’s life cycle.
www.se.com
OZ Lifting Stainless Steel Trolley OZ Lifting Products LLC stainless steel push beam trolley, available in one or two ton capacities. The push beam trolleys fit most common I-, S- and W-beams. It is adjusted using supplied, in addition to an owner’s manual and test certificate.
The trolley does not require maintaining beyond that of a traditional steel product. Additional features include individual test certificate and serial number; stainless steel identity tag; antidrop plate; and precision ball bearing trolley wheels. The trolley is designed for use in corrosive environments.
www.OZLiftingProducts.com
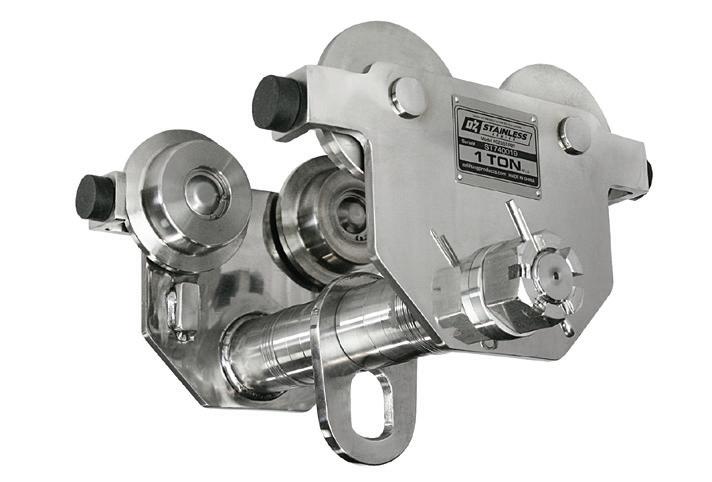
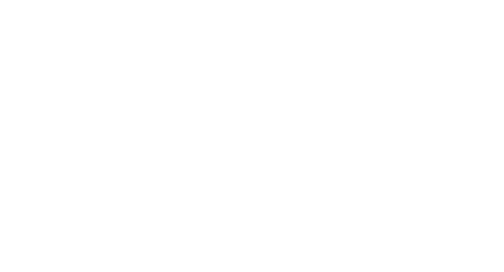
The Podcast for MRO Professionals

The podcast features conversations with industry experts about maintenance, reliability, and operations. Topics that are of utmost importance to MRO readers. Previous guests and topics have included: Doc Palmer – Focus on Scheduling and Planning of Maintenance; James Reyes-Picknell – Managing Maintenance and Reliability; and Shawn Casemore – Engaging Your Employees in a Safety Culture. MRO
Mr. 0, The Practical Problem Solver
Asset Information Management Having worked with maintenance and HSSE professionals for over 25 years, we see the struggles organizations have with data qualities. Inaccurate data causes a number of problems that range from safety to unnecessary downtime. Therefore, it is vital for any organizations to manage their maintenance data properly.
In this connected age, where technology advancements seem to always be at the forefront, it can be easy to lose sight of what business need underlies these innovations. What can be even worse is that managers and executives lose control of what really drives business – information. In its simplest form information leads to sufficient knowledge and ultimately drives decisions, and then actions, at all levels of any organization.
Decision making in asset management is driven in part by key performance measurements that are derived from transactional data through the work management processes. Underlying this data is the master data that exists for every asset. It is well established that inaccurate master data can be the source of a broad range of problems including health, safety, and environment risks, regulatory compliance and reduced uptime. MRO
- Richard Beer, TRO Maintenance Solutions

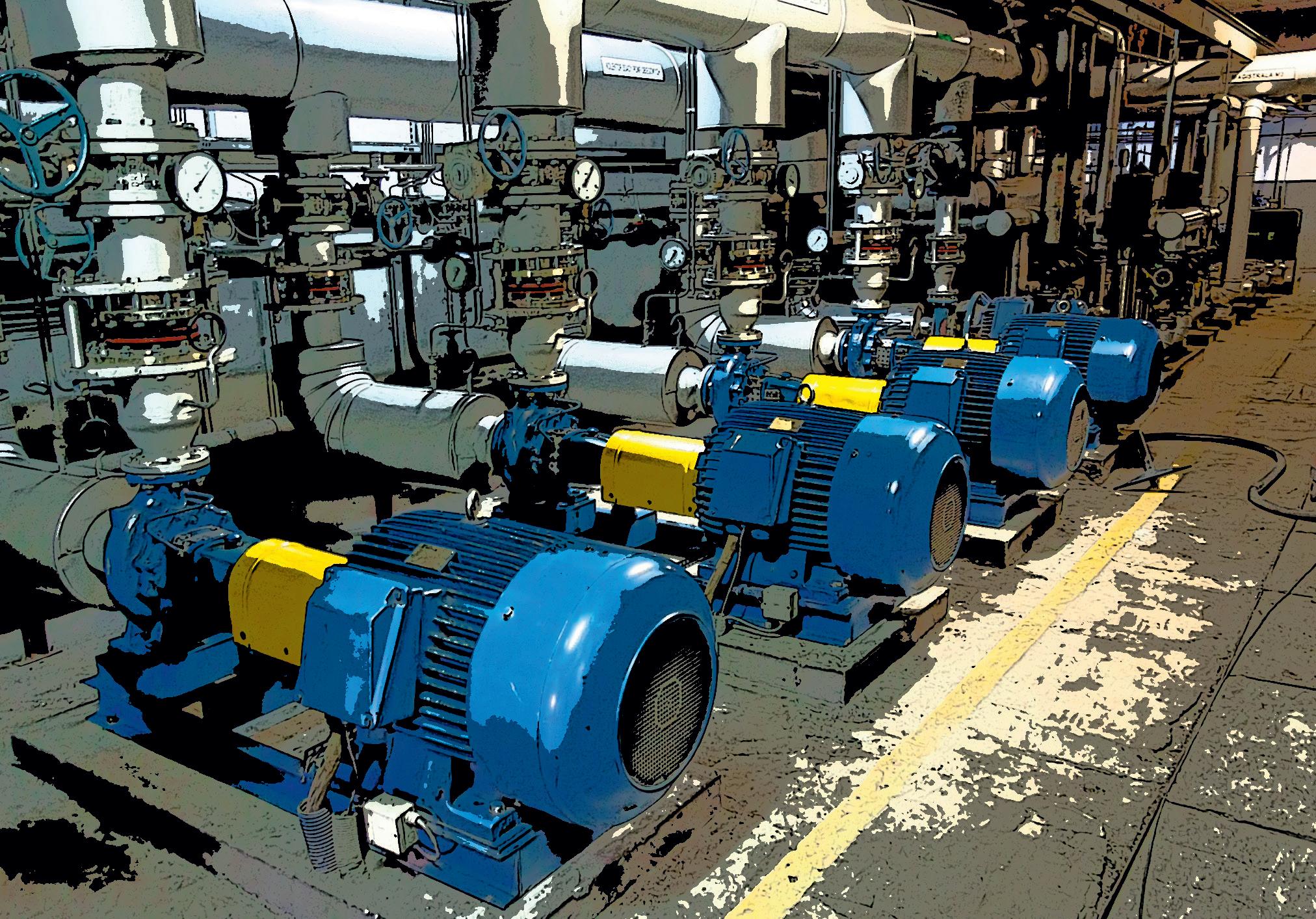
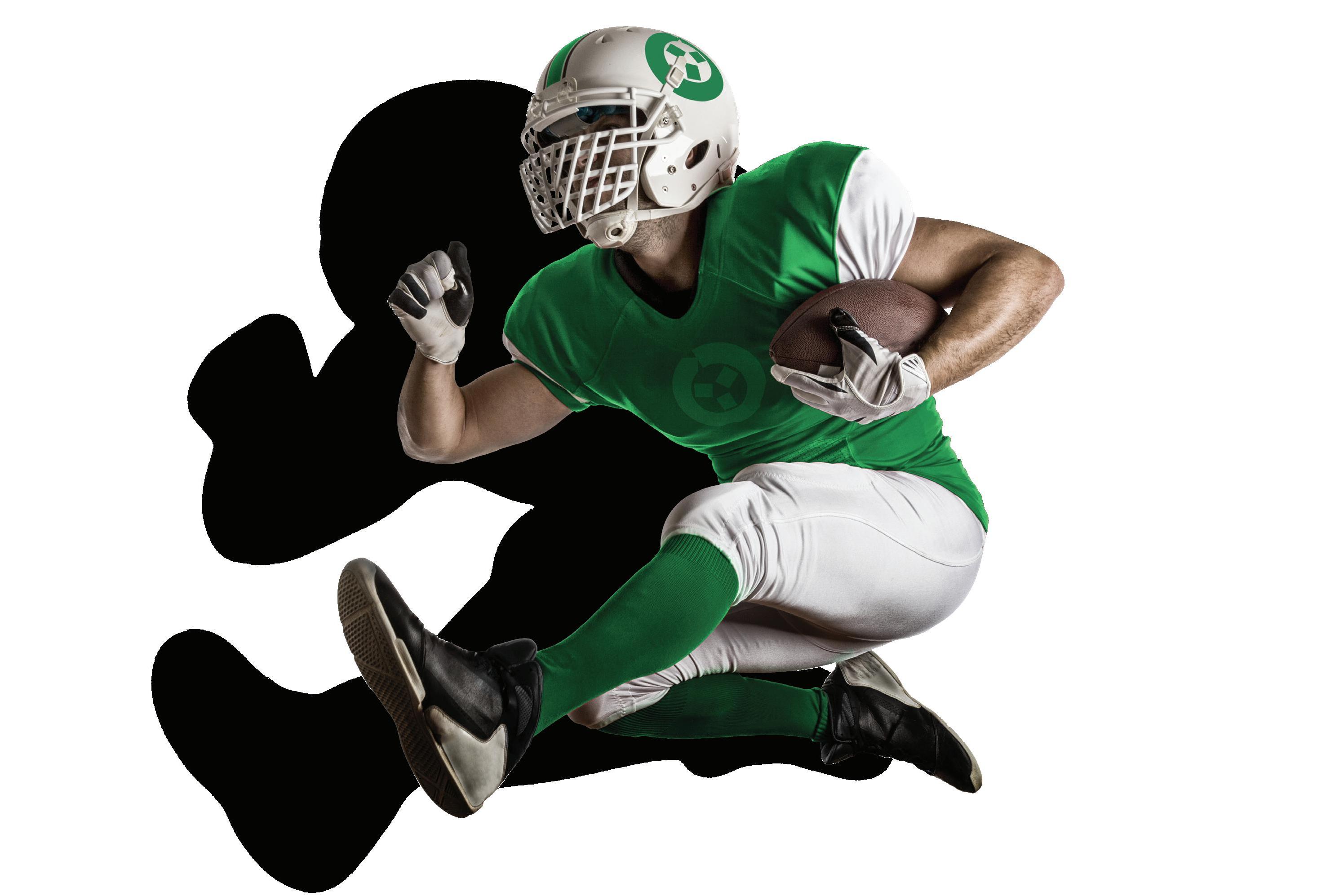

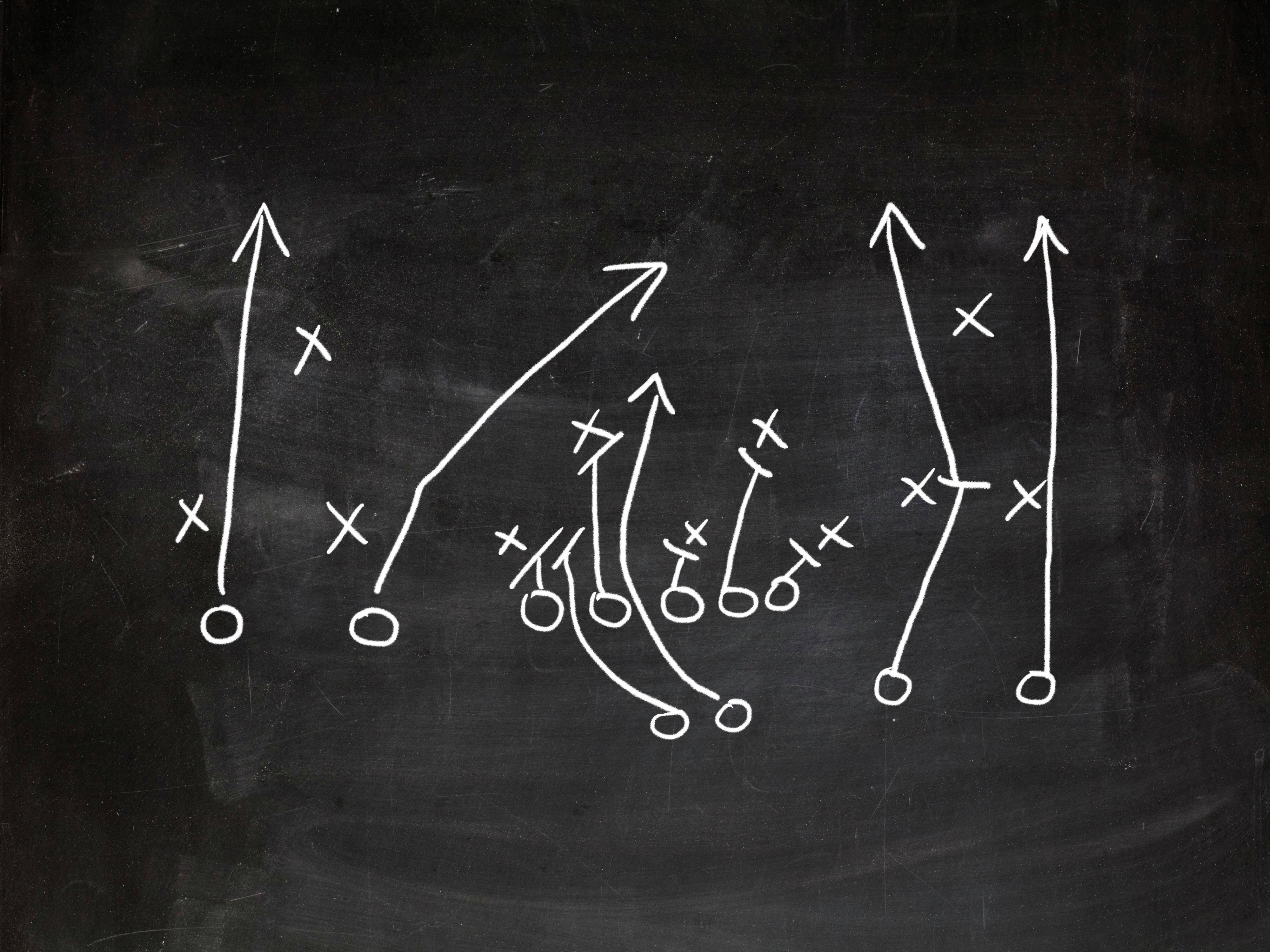