
4 minute read
CMMS – Cloud-based versus on-site installs
Most CMMS applications fall under two categories: on-site and cloud-based.
Computerized maintenance management systems (CMMS) are a hot topic for many corporations and maintenance departments. Maintenance departments may be looking to purchase their first CMMS or upgrading their current maintenance software. Maintenance departments use different tools and resources to maintain equipment, one of the crucial ones is CMMS. Both on-site and cloud-based CMMS solutions are designed to provide an application that can plan and track equipment maintenance.
BY PETER PHILLIPS
Typically, when people think of software, the concept is, there’s an application, you install it on a computer, phone, or tablet, and use it. When a user installs software, it’s typically tied to the device. In the case of a traditional CMMS, it’s deployed onsite and is tied to the on-site hardware and is deployed on each computer across the organization.
Cloud-based solutions are entirely the opposite. The application is not tied to the company’s hardware and resources. With cloud-based systems users can access the application on any device that has an Internet connection. With cloud-based systems, fewer IT resources are required as the cloud-based solutions don’t need maintenance – everything is done by the vendor through a support contract. Finally, cloud-based solutions are typically cheaper to implement and operate.
Benefits of a cloud-based CMMS
Unrestricted access
Users are not tied to the premise or the workshop, they can access the app from anywhere and whenever the work requires them to. In contrast, older CMMS requires them to be present on the site.
Device access
Apps can be accessed from smartphones and tabloids, users only need to log-in and have an Internet connection. The maintenance planner, super visor and technicians can use their mobile devices or workstations to keep track of the maintenance tasks, assign new work orders, and provide feedback when necessary – something that’s not always possible with on-site solutions.
Reduced burden on IT resources
The solution is handled by the vendor. The IT team can show a user or provide a manual on how to access and use the CMMS cloud-based app on their devices. Maintenance team members can start using the app r ight away after logging in.
With on-site solutions, there can be issues, for example, maintenance, implementation, and operating system updates. All of these require servers, hardware, and more IT personnel, incurring costs in the process.
Seamless updates
Major updates can be long, cumbersome, and disruptive. Cloud-based CMMS software, makes updates seamless, users are notified about updates and no other actions are required by IT or user s. With on-site solutions, even the smallest updates can be time-consuming, whereas, with cloud-based solutions, the under-the-hood improvements are occurring constantly.
Faster implementation
Organizations need to ensure that required resources like the hardware and servers are available, and CMMS supporting resources and software loaded on the servers. While it might sound simple, getting management to sign off on machinery and software can be time-consuming.
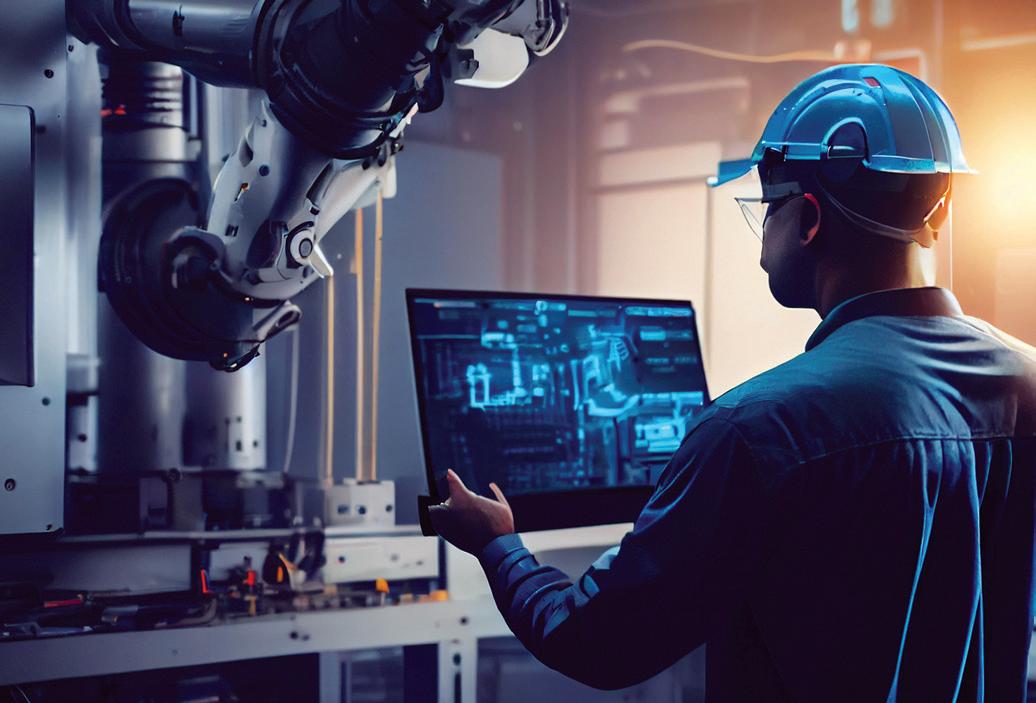
Organizations just need to make the recurring application payment to the vendor, and they will provide accounts to use the solution. Users log onto their devices on a secure Internet connection to use it, making implementation faster. With appropriate training and demonstration, maintenance team members can start using it right away.
Reduced costs upfront
A dedicated IT person is not required. There are no additional servers or hardware required, the application is easy to implement, and can be used from any compatible device. As a result, organizations that use cloud-based solutions are saving up-front costs. The payment model is quite simple –organizations need to pay a certain amount based on the number of users.
Better support and security
Security and maintenance is taken care of by the vendor. This relieves the IT personnel from having to troubleshoot problems with on-site CMMS solutions. When a user identifies a problem with the cloud-based solution, they only need to report it to vendor support.
Scalable
A unique benefit for dynamic organizations is scalability. For instance, if an organization has few maintenance team members now, it needs a solution that can match the lower workload. However, if the same organization aims to expand its maintenance team significantly, it needs a solution that must be able to match the increased workload and maintenance tasks.
Enhanced productivity
The maintenance team is completely mobile with work orders on their tablets and access to parts inventory and equipment information through the app. The users just need to log-in to the authorized devices and they’re good to go, they get access to crucial information, such as spare parts availability, assets, vendors, and tasks. These modern maintenance management apps cut down response time to unexpected equipment breakdowns and prevent production disruptions.
Improved collaboration
Cloud-based CMMS applications ensure that asset, vendor, spare parts, and technician information are kept in a centralized location in an organized manner. Moreover, authorized users can monitor the progress of technicians, work orders, and repairs. While the maintenance supervisor can add further work details and schedule work, technicians can update the status of their assigned work orders using the app.
Regular workers including production supervisors and operators can also submit work requests. Robust maintenance management apps also allow them to add images or videos to show the precise problems with the faulty equipment. Maintenance supervisors, upon verification of the work request, can assign technicians to work order for action or can add it to the maintenance backlog. All in all, a cloud-based CMMS helps improve collaboration between the production department and streamline maintenance efforts.
CMMS vendors list potential benefits of their software, they include:
• Reduce equipment downtime;
• Increase productivity;
• Lower maintenance costs;
• Improve inventory management;
• Schedule preventive maintenance;
• Increase life of equipment;
• Enhance work order management;
• Generate custom reports;
• Make data driven maintenance decisions; and,
• Meet compliance and safety standards.
The trick to choosing a CMMS for your company, is finding a system that fits the maintenance department’s needs and ease of use and provides reports and KPIs to guide the maintenance team to effectively maintain the equipment and spare part inventory, and to fit the maintenance department budget.
Peter Phillips is the owner of Trailwalk Holdings Ltd., a Nova Scotia-based maintenance consulting and training company. Peter has over 40 years of industrial maintenance experience. He travels throughout North America working with maintenance departments and speaking at conferences. Reach him at 902-798-3601 or peter@trailwalk.ca.