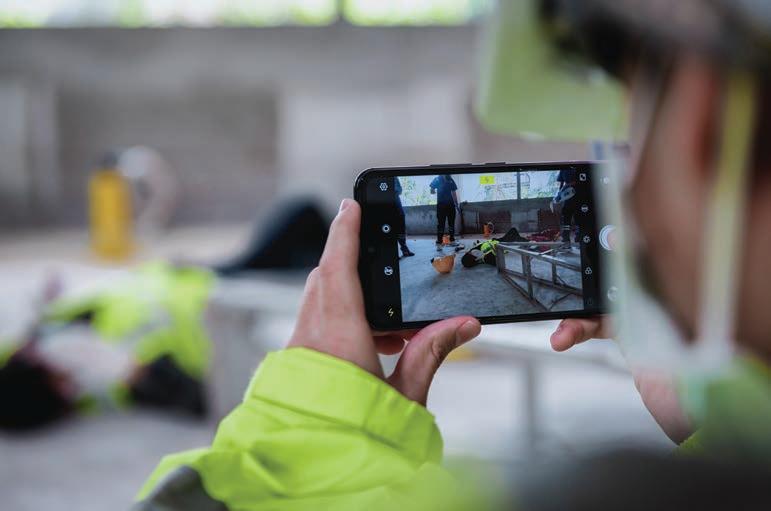
8 minute read
Health & Safety
LOSING PAPER TO IMPROVE SAFETY
Five advantages of electronic data capture and analysis for safety processes.
BY GREG NORRIS
Safety is a top priority at almost every construction company, but many overlook the risks of relying on paper as a cornerstone of their safety processes. Making the switch to electronic forms and an online, mobile solution for the distribution, collection and analysis of safety related data can help minimize risk and increase compliance.
It can also reduce the administrative burden on their employees by moving away from paper-based safety processes, while gaining the ability to turn real-time data into actionable intelligence.
GETTING INFORMATION TO THE FIELD
Regular safety meetings, or toolbox talks, are a proven tool that helps prevent injuries, improve compliance with regulatory requirements and sustains a culture of safety. Managing this process can be an ongoing administrative headache, however. Delivering safety materials and forms to the field can limit portability and accessibility, and may create lag times.
With an electronic process, users in the office can distribute safety information and forms instantly. Users in the field can access them right away.
CUSTOMIZING YOUR FORMS
Electronic forms provide the flexibility to generate safety forms quickly and easily, and to customize them. Contractors can add, delete and create new fields and sections as needed to capture the exact information they need about a specific activity, process or piece of equipment. The updated forms can then be immediately distributed to those who use them during their work.
With paper, contractors are often forced to settle for generic, one-size-fits-all forms. And images, attachments, time stamps, and GPS information can also be included with electronic forms. These can validate safety data from the field, providing a much higher level of detail and utility.
PREDICT AND PREVENT
When contractors use paper forms to document accidents, incidents, near misses and other safety-related events, analysis is a manual process. That can take a lot of time and administrative effort. Turning data into actionable intelligence may be delayed and deferred as a result.
Electronic forms for data capture and analysis make it easy to aggregate safety information automatically and populate routine or customized reports and dashboards. Contractors can then use these valuable tools to measure their safety performance and drive continuous improvement. They can also identify trends that could potentially help them to predict and prevent future incidents.
For example, a report that compares injury, near-miss and toolbox talk statistics across the enterprise could reveal a need for increased training or compliance steps at specific jobsites. Similarly, efficient analytics could identify an accident trend involving a single person, alerting supervisors that additional training is needed. far-reaching utility and advantages across digitized construction workflows. These tools, made possible through the switch from paper to electronic forms, can improve safety too. An event like an injury or an accident reported on a form field can trigger an immediate alert.
A foreman checking “yes” on an accident form field asking if there was bodily injury could prompt an immediate message to a superintendent or safety officer or an operator using a similar piece of equipment. Getting the information right away can help them to respond appropriately or prevent a similar incident.
IMPROVING INSPECTIONS
Inspections are an everyday process for most contractors. Documenting progress, driving quality and cutting costs are primary goals, but there are important safety aspects to site and equipment inspection processes as well. Catching problems as quickly as possible can prevent injuries.
When paper is part of the inspection process, it may take a week or two for inspection forms to reach someone who can take action, and lag time could be catastrophic. Since electronic inspection forms can be submitted instantly, they help close the time gap between the field, the shop and the office. Potential risks identified in a site inspection can be addressed promptly, in a more timely manner.
SELECTING SAFETY FOOTWEAR
What to look for in a new work boot.
BY ROBIN SKILLINGS
It can be tough to let go of a favourite pair of work boots. Those comfortable standbys have worked hard for miles and become so broken in, it’s hard to understand how they may not be working to their optimal performance anymore.
When it comes to preventing injuries on the job and ensuring the best in performance and comfort, knowing when it is time to start shopping for a new pair can be critical. With so many options to choose from, it can be overwhelming to select new footwear that not only satisfies safety requirements of the job at hand, but also offers the performance and comfort features that will help get the job done over the course of a long day of work.
SIGNS YOUR BOOTS SHOULD BE REPLACED
Sometimes knowing when it is time to replace an old pair of work boots can be self-explanatory. If work boots have visible holes and cracks or are literally falling apart at the seams, it is time for a new pair.
However, when it comes to boot replacement, there are some less obvious indicators to look out for as well. For example, an overly pliable boot suggests that the shoe no longer has the structural rigidity it possessed at the time of purchase. Delamination of the outsole is another sign and is visible when the outsole of your boot starts separating from its leather or fabric upper. This occurs when the cement construction of the shoe wears out due to either the age of the glue or exposure to caustic materials.
Even protective toe caps can become damaged over time and need replacement. This is especially important after a cap takes a blow regardless of any visible 46 / JUNE 2022 damage as micro-cracks can develop making toe caps significantly less effective.
SELECTING NEW SAFETY FOOTWEAR
When the time finally comes to unlace a pair of boots for the last time, there are many factors to take into consideration when it comes to looking for new footwear. Different work sites have unique requirements for personal protective equipment (PPE) and that includes safety footwear.
In addition to choosing a shoe that meets the specific safety demands, performance and comfort enhancements should not be ignored. You are wearing these boots all day, after all! These features must also be considered to not only maximize productivity over the course of a long workday but improve foot health as well.
In Canada, a few factors to consider include:
CSA certification: A prerequisite for Canadian jobsites is a CSA-certified boot. Puncture-resistant outsoles are a critical component of this certification, and help prevent sharp objects, such as nails, from piercing through the outsole and causing injuries underneath the foot.
In the past, this extra layer of protection, which can be found in the boot’s midsole, were constructed from metal plates such as steel. However, thanks to material advances, this layer can now be constructed from high-tensile strength woven fabrics, which are lightweight and flexible as well as non-metallic options that offer the necessary puncture resistance for the jobsite.
Slip resistance: Slips, trips, and falls are some of the most common injuries on the jobsite. In fact, according to Onatrio’s Workplace Safety and Prevention Services, one in five lost-time injuries result from falls.
Slip resistant outsoles minimize this

risk through an interlocked tread pattern ingrained under the outsole. This pattern channels liquid away from the foot, providing increased surface area and better overall traction.
In Canada, CSA certification also requires the labeling of slip-resistance performance data on all safety footwear. Reviewing a boot’s box and label or checking the brand’s website to find the CSA seal of approval is essential prior to purchase.
Toe protection: Safety toe caps are often required on jobsites, especially when working with heavy machinery or lifting heavy objects. Traditionally, safety toes were made of steel or aluminum, however carbon-fibre toes are the latest safety cap to enter the market.
Carbon-fibre safety toes are 15 per cent lighter than steel, which provides a new-found mobility and comfort for workers. Additionally, these caps are non-metallic, which is extremely beneficial for workers whose jobs require them to pass through metal detectors throughout the day. At my company, both comfort and safety are paramount, which is why safety toes are asymmetrical to provide a roomier and more comfortable fit.
Unique safety features for the job:
Every job has its own specific requirements for potential risks. Depending on the potential hazards of the individual jobsite, there is likely a safety footwear option that offers the needed protection.
These features could include everything from abrasion-resistant outsoles for worksites where water, grease or any other liquids are common, to Kevlar fibre for resistance against open flames. Whatever presents potential danger at a jobsite, it is essential to select footwear with the safety features that correspond with the job at hand.
Seasonality: Although many work boots are made for year-round use, there are benefits to purchasing boots specific for the summer or winter months. For example, insulated and waterproof boots are important in the colder months to keep feet warm and dry. However, as summer rolls around, transitioning into a work boot that is lighter with more breathability may be attractive when it comes to keeping feet cool during the warmer months.
FINDING THE RIGHT FIT
Selecting a work boot that fits well is crucial in order to prevent injuries and maximize comfort over a long day on your feet. When it comes to shopping for a new boot, we recommend trying shoes on at the end of a shift. This is because the feet naturally swell over the course of the day, so this is when they will be at their largest.
Additionally, when determining the best fit, it is important to try on new boots while wearing the socks that will be worn while on the job. Companies are constantly innovating new footwear enhancements so there are increasingly more options when it comes to underfoot support, improved performance, and even extended lifetimes of work boots.
Robin Skillings is the vice-president and global general manager at KEEN Utility, a leading industrial and service footwear brand.

Moving Forward in Construction with Avetta
In an industry where all eyes are on compliance, Avetta keeps job sites safe and TRIR rates down – while still protecting ROI.
The Avetta platform provides access to a roster of industry-leading professionals, vetted and verified to meet your team’s standards.