
6 minute read
Machinery
CRYSTAL CLEAR GROUP SET TO INCREASE EFFICIENCY AND QUALITY WITH SUPERCUT 6
Established in 1988, the Crystal Clear Group has always had a focus on providing commercial and trade customers with top of the line, high-quality PVCu fenestration products. In August 2020, in the midst of months of unprecedented demand in the industry following lockdown for the COVID-19 pandemic, Crystal Clear’s CEO Martin Randall decided it was time to upgrade his fabrication machinery. He was looking for something which would not only enhance his operational efficiency but also provide consistent quality across all products.
GETTING THE BALL ROLLING
Having scoured the marketplace to assess what was available, Martin knew he didn’t want to wait. Avantek Machinery’s reputation for investing in stock of machinery meant the team could supply Crystal Clear Group with a brand new Supercut within days, giving his business the production capability it needed. Within 24 hours of the decision, three Avantek team members made their way to Hertfordshire to visit Crystal Clear Group to meet with the team and to prepare the factory for the arrival of the 23-metre-long Supercut 6. Crystal Clear’s Operations Director Tim Goldspink commented, “The planning
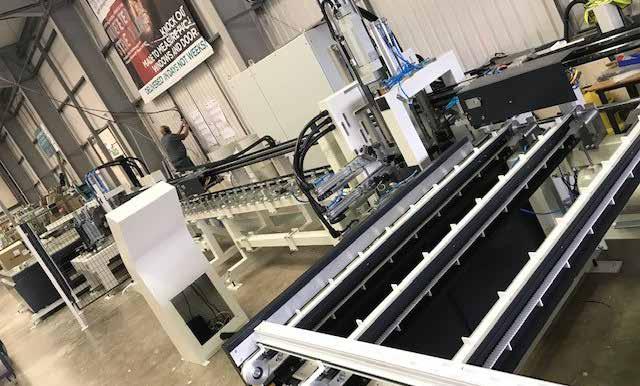
process was key. Two automated saws had to be moved out of production whilst installing the Supercut around the factory’s existing layout – and with such a large machine, we had to make sure it was installed safely. Dave Fox, Avantek’s Supercut Manager, delivered a CAD drawing of our facility and showed us the most efficient way to set up the factory, which was superb.”
WHY THE SUPERCUT 6?
Martin Randall says, “We’ve been using separate machines for cutting and machining for decades. With the need to increase production also came the need to increase efficiency without sacrificing quality – and the Supercut delivers both.
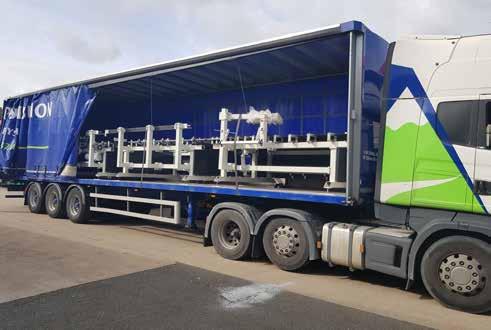
“With the Supercut 6, profiles are cut and machined in one motion, all with only one machine. It also moves all off-cuts into the waste basket for ease in recycling – which is paramount to our operations. The fact we could have all this within a few short weeks was what really swung it for me – and the Avantek team have been so easy to deal with.”
INITIAL OBSERVATIONS
The Supercut 6 was delivered two weeks after Martin’s initial telephone call to Avantek and will take just four weeks to set up from start to finish – including working with software companies and training staff to run it. Martin continues: “The Supercut replaces almost a dozen smaller, less efficient machines in our facility. It delivers the consistently excellent results that we expect and are known for. It will also allow us to streamline our operations, and further increase our productivity by up to 1300 frames per week. “We’re excited about the future and the move to invest in the Supercut 6 now will help us to manage the unprecedented demand we’ve consistently seen over the last few months.”
For more information about Crystal Clear Group visit http://crystal-direct.co.uk/. Learn more about Avantek Machinery’s Supercut 6 Cutting and Machining Centre by visiting www.avantekmachinery.co.uk/supercut/.
WEATHERBREAK WINDOWS INVESTS IN SECOND KOMBIMATEC MACHINING CENTRE
Luton based fabricator, WeatherBreak Windows, has responded to a marked increase in demand for its high-quality aluminium product range, with the addition of a new AMC308 machining centre from Kombimatec.
Installed at the end of August, WeatherBreak’s new AMC308 machining centre is the second machine of its type to be ordered from Kombimatec and has been introduced to bolster the aluminium window and door line at the manufacturer’s state of the art 30,000ft2 facility. Featuring CNC control with a colour touch screen display, WeatherBreak opted for the 3m version of the 3-axis AMC308, which is suitable for both aluminium and PVC profile. Integrating an auto rotating work bench and an automatic multi-tool change cabinet, the AMC308 also combines a 5HP motor spindle, a quick change ISO30 tool system, electronic variable speed control, pneumatic rotating of the work piece through 90-0-90 degrees with adjustment for intermediate angles – plus a host additional of features that result in a highly capable, cost effective and easy to use machine. Peter Hedges, WeatherBreak’s managing director, commented: “We manufacture a full range of Smarts aluminium products, from Alitherm casements – including Alitherm Heritage – to the Visofold sliding/ folding and bi-fold doors and curtain walling offering. “We’ve experienced a significant uptake in demand across our aluminium range, and the Kombimatec AMC308 has proven to be a real asset to our production facility. It’s really easy to operate, it’s reliable and it does everything we want it to do, but without the excessive cost of other machines on the market. “Kombimatec is based just 5-miles from us”, continued Peter. “The quality of service we’ve received from David Parsons and his team has been excellent, and we’ve been extremely happy with the investment we’ve made in both our AMC308 machining centres,” he concluded. “For the future, we are expecting demand for aluminium to continue to rise. I would have no hesitation in purchasing more machinery from Kombimatec to ensure that our production facility is properly equipped to continue to deliver the high level of quality and service that our customers have come to expect.” Founded in 1982, WeatherBreak Windows has been manufacturing aluminium products alongside its market leading PVC-U offering for over 15-years and has built a reputation within the trade for exceptional service that has been developed on continual investment in product, people and equipment. For more information contact the Kombimatec sales team at sales@kombimatec.com or call 01582562218.
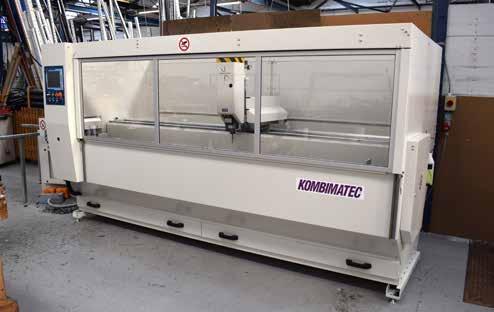
LINIAR STAYS AHEAD OF FOIL DEMAND WITH INVESTMENT IN LAMINATION TECHNOLOGY
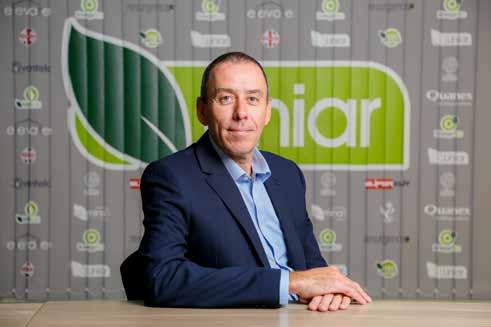
Innovative PVCu systems company Liniar is ramping up its capacity for foiled profiles, with the purchase of one of the most technically advanced lamination machines on the market.
The £750k investment in the Luna R Automatic Profile Wrapping Machine from Italy has been specifically designed for Liniar and will help the extrusion company speed up the production of foiled profiles, thanks to major time savings on set up time and increased output. Liniar already offers one of the best foil ranges in the UK today, with 36 foils across 5 substrates – giving a possible 3,330 colour combinations. Its in-house, purposebuilt lamination department has seen unprecedented demand over recent years and in particular recent months. The decision to purchase this machine was made during 2019 as part of Liniar’s long term strategic plan to offer unrivalled service of foiled products – for example, increasing its range of stock items and offering shorter, market leading lead times on made-to-order products. The new machine will be fully operational by November and will offer the capacity of two standard lamination machines, thanks to high automation and productivity – effectively halving overall energy consumption – in line with Liniar’s focus on manufacturing efficiency and environmental standards. Production Director Eddy Webb explains why the new addition is important for Liniar and its customers: “We’ve all seen the huge increase in demand for foiled products as consumers become more aware of what’s available. Liniar has always been at the forefront of introducing
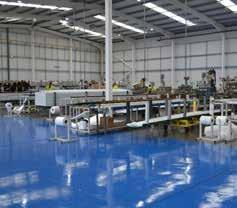
new colour ranges to the market, and our plans for 2020 included looking at ways to increase the range even more towards the end of the year. “The demand spikes following the COVID-19 lockdown have had the effect of accelerating our plans and we’re delighted to receive the machine earlier than planned. “It’s our aim for the Luna to run the work of two existing lamination machines – allowing the team greater flexibility to focus on special orders. This will result in huge benefits for Liniar customers in the coming months.” The investment is the second large purchase Liniar has announced during the pandemic, following the introduction of several million pounds’ worth of additional extrusion machinery in June. It will be teamed with another 2 extruders, which are also due for delivery in October. This continued focus on investment cements Liniar’s position as one of the most well invested, stable and reliable partners in the industry. Get in touch with Liniar at sales@liniar.co.uk.