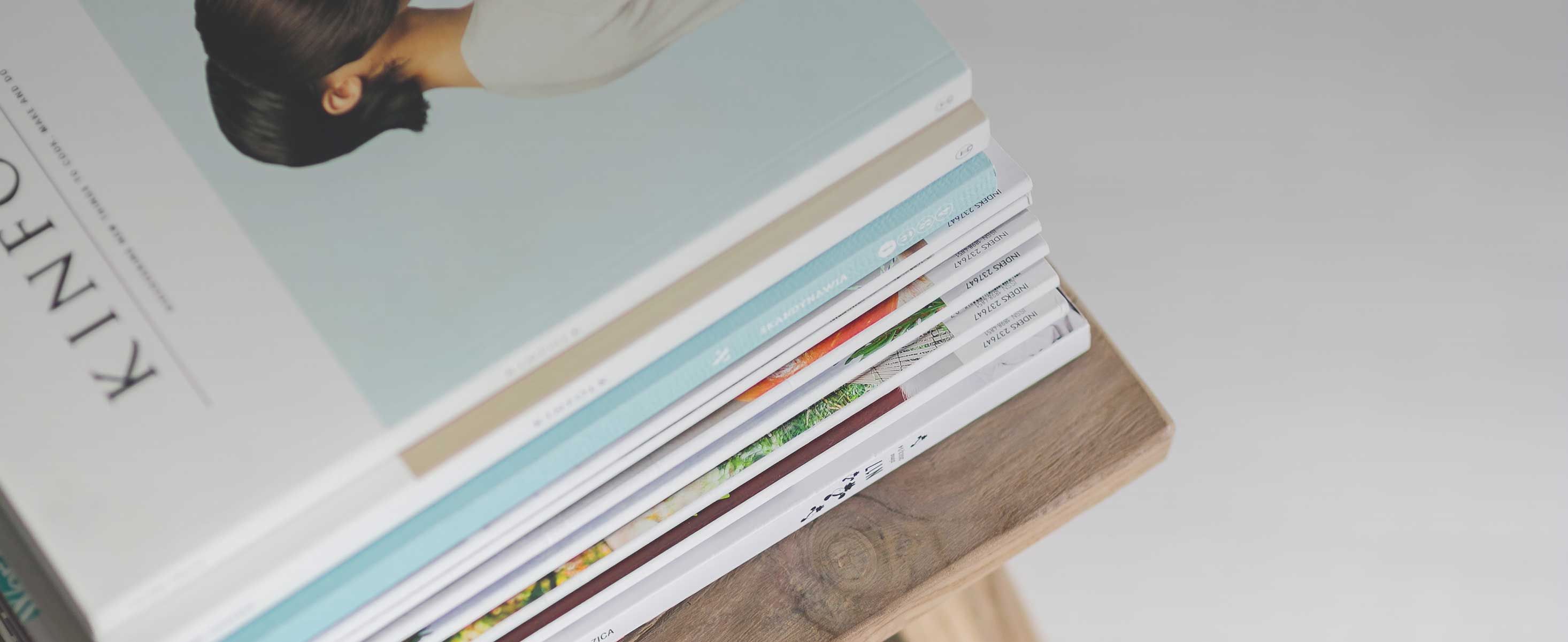
4 minute read
Glass News Interview: DOORCO
INNOVATIVE DOORCO.
THEIR GRIPCORE DOOR AND FLIP GLAZING CASSETTE SYSTEM PROVE THE POINT.
An interview with DOORCO’s Dan Sullivan is always illuminating and Glass News’ Editor, Chris Champion, talks with him about the new products that the DOORCO team has been working on during the period of the Covid-19 lockdowns. Yes, they’ve been putting this time to good use!
DOORCO has always been pretty selfsufficient, not relying on manufacture of their GRP composite door through third parties but having their own manufacturing facility in Korea. Now with two new products in the DOORCO armoury, have they managed to maintain this selfsufficiency? As Dan Sullivan openly admits, production of the new GRiPCORE solid 44mm door blank has required a new partnership with experts in hardwood door production, again from the Far East. “We are using the 4mm GRP skins that Tony and his team manufacture at DOORCO Korea but adding these to a hardwood blank. Our Indonesian partners are very experienced in engineering timber and are high end timber door manufacturers, in their own right, so having them assemble the end product makes sense.”
GRiPCORE is a one-size-fits-all door being 914mm that will cut down through 762mm and right down to around 680mm. Dan is quick to give credit for the idea to one of his customers and the result is this one size door that is rigid, thermally efficient and won’t crack, bow or delaminate. DOORCO is warrantying the door for 10 years and saying that 3mm is the maximum thermal movement.
It’s interesting that the movement associated with the foam filled composite door is accentuated by the modern designs that require cutting away so much of the door blank to accommodate large cassettes and IGUs but a solid door, such as GRiPCORE, will allow for these modern designs while maintaining the rigidity. Six different styles and four stock colours are available now but the door can be painted in any colour, either by DOORCO or the fabricator. GRiPCORE is sold either as a slab for warehouse customers or as a prepped option. The door is definitely overkill with solid timber covered in 4mm GRP skins but, as Dan says, all their doors have the 4mm skin simply because the tooling is set up and making new tooling for thinner skins would not be economic. So it’s a heavy but very, very secure door! Asked about transportation and the current issues of cost, both of containers and raw materials, Dan Sullivan is very open. Yes, life is tricky. However, as a well-founded and well-run company, DOORCO can do what is needed to maintain supplies and get product to the UK. It requires a lot of paying upfront for both materials and to secure shipping slots. And this influenced DOORCO’s decision to manufacture their other new product in the UK. This new product is FLiP. A completely new cassette system that benefits from being ‘last to the party’ as Dan describes it. This has given DOORCO the advantage of assessing the various cassette systems and producing a ‘new age’ product that satisfies the current and future needs of the market. FLiP is not a single design cassette with lots of different shapes – it’s three different designs to satisfy the traditional, contemporary and flat grained look that are all in demand. With a UK design team that took FLiP through the mechanical process for the clip together system and the laser print modelling, the tooling was made in China and, bearing in mind the issues of the last year, it was decided that manufacture in the UK would mean control was maintained and would cut lead times.
For me, the advantage of being ‘last to the party’ is seeing how DOORCO has produced a system that is quick and easy to use by incorporating Foam in Place - a foam seal that negates the use of tape and sealants. This is a big advantage to the fabricator both in time and cost. It also means the cassette is completely reusable after deglazing plus it is adjustable for 24mm or 26mm units. The DOORCO design team have pretty much thought of everything including corner protectors to prevent flaring at the corners of the cassette. So just a screwdriver to fit these new FLiP, Through Colour glazing cassettes, and a choice of design and shape….with many more shapes to come. What’s not to like? Oh, and if you are wondering, these cassettes have been tested for water ingress to 1,000 pascals! DOORCO has always been known for being innovative and, with the new GRiPCORE door and FLiP glazing cassette, this is certainly continuing. Has it been exciting? “The concept and design stage was exciting,” says Dan. “Now I just want to sell the products!” And what of the future? Watch out for new door designs. DOORCO never stand still!