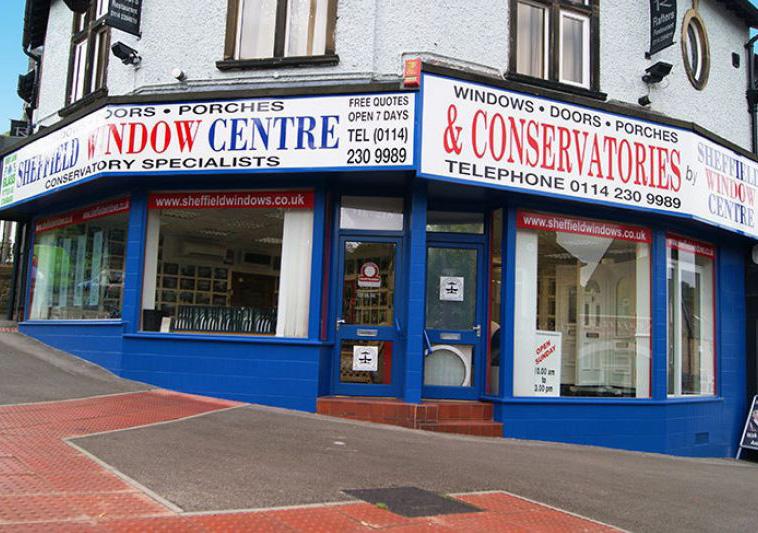
8 minute read
Machinery
EFFICIENCY IS KEY
WITH SHEFFIELD WINDOW CENTRE
Established nearly five decades ago, family-owned and operated fenestration company Sheffield Window Centre is a well-recognised, well-respected Yorkshire business. Known for its commitment to highquality finishes and courteous yet efficient customer services, Sheffield Window Centre (SWC) prides itself on being the local double-glazing company that families can trust.
Being in operation for so long means the company has gone through its fair share of fabrication machinery. Whether modernising existing machinery or replacing those at their end of life to ensure quality and efficiency, when it came time to secure new machines, SWC’s Managing Director Ian Hunter knew just which company to turn to - Avantek Machinery.
BUILDING STRONG FOUNDATIONS
Sheffield Window Centre has been an Avantek Machinery customer for nearly twenty years, back when it was still known as Wegoma GB. Over the years, Ian has built a rock-solid relationship with Avantek Sales Director Gary Mayer in particular, who has had a positive influence on most of the machinery that Ian ultimately ended up purchasing to use in the company’s fabrication operation. “I can honestly say that the advice Gary has provided us regarding window fabrication machinery has been infallible,” remarks Ian. “There have been many occasions when Avantek suggested certain machinery for our company, but we chose not to purchase at that exact time. Once we were ready and had the machine installed, however, I’d always find myself going back to Gary to say he was right about what that particular machine would do for us!”
VISITING THE SHOWROOM
Prior to the COVID-19 outbreak in 2020, Ian and his team made the short trek down the M1 to Avantek’s state-of-the-art showroom in Derbyshire, to see Avantek’s flagship Supercut cutting and machining centre in action and find out if it could work for their premises. “While incredibly efficient, the Supercut just wasn’t suitable for our factory, as we didn’t have the space required to fit either model,” Ian explains. “While we were there, however, we looked at the Wegoma 4-head Auto Welder. Gary explained all the benefits, including the potential time savings, quality consistency and energy efficiency - but like all the times before, we didn’t make the jump to purchase the welder at that time.
A SOUND INVESTMENT
“Fast-forward to 2021, our current welder was on its last legs, so we really had to invest in a new one. Once again, I trusted Avantek’s advice and made the decision to purchase the Wegoma Auto Welder. “After installation, it was easy to see why they’d recommended this model. It’s fast, efficient and literally takes the thinking out of this part of the fabrication process. I’m delighted to say it’s been a sound investment for Sheffield Window Centre,” comments Ian.
THE IMPORTANCE OF TRUST
The biggest factor in Ian’s machinery purchasing decisions really comes down to one thing – trust. Ian explains how his relationship with the Avantek team is an integral part of the process: “Having someone you can trust when you need something as crucial as machinery is invaluable for a window fabricator. Since the first time we began doing business with Avantek, they’ve never given us advice that wasn’t honest, impartial and incredibly helpful. “All the benefits we’ve been told about making efficiencies or increasing production without increasing manpower have materialised and I don’t even question them now - I trust the team implicitly.” The ongoing machinery investment at Sheffield Window Centre ensures the products it fabricates are of the highest quality. View the full range of products and services by visiting www.sheffield-window-centre.co.uk.
If you’re looking to make efficiencies in your fabrication operation, need advice about factory layout or machinery or want to upgrade machinery that is coming to its end of life, contact Avantek Machinery at sales@avantekmachinery.co.uk or visit www.avantekmachinery.co.uk.

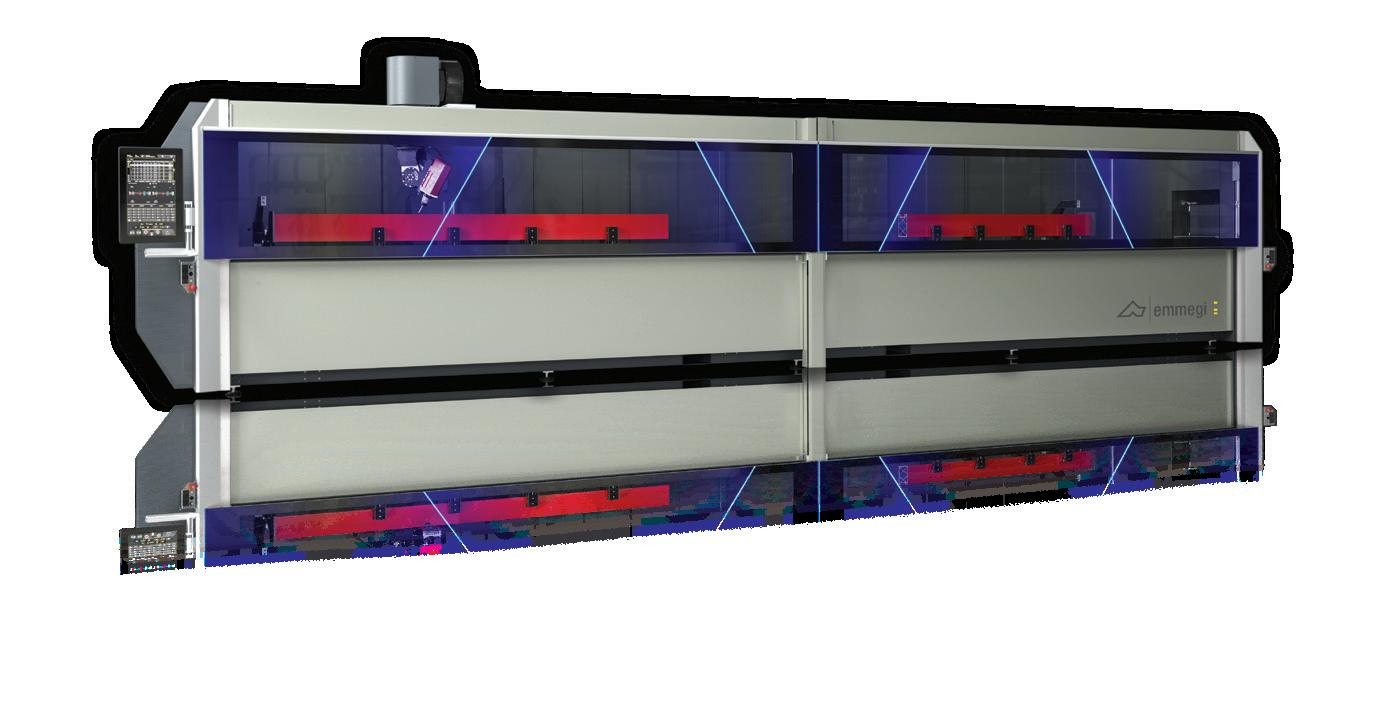
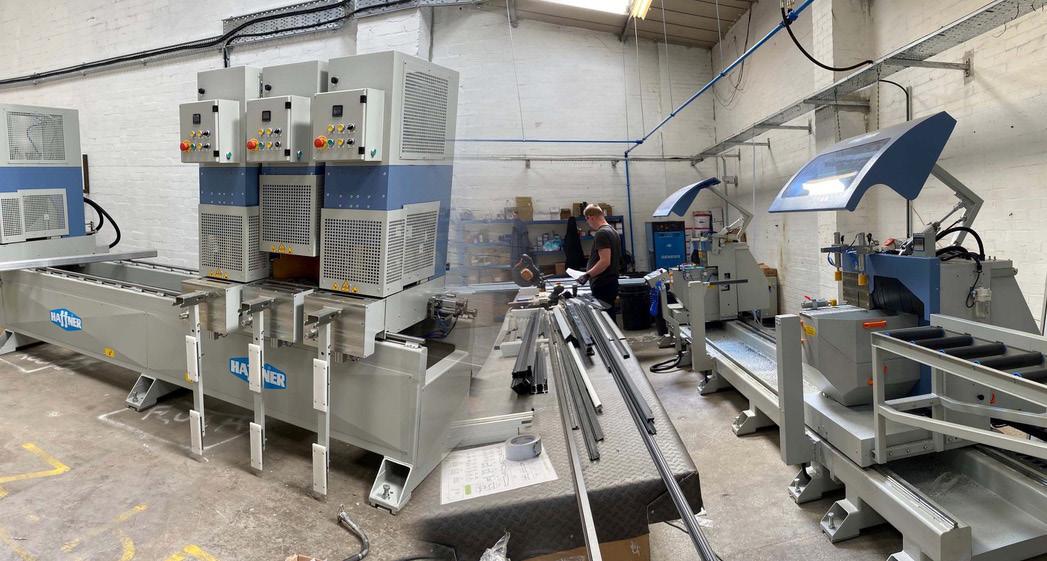
BEDFORDSHIRE WINDOWS CONTINUES TO INVEST WITH HAFFNER
Trade and retail fabricator Bedfordshire Windows has invested in a new SMR-4 Four-Headed Welder and TT425 Double Mitre Saw from award-winning machinery experts, Haffner. The new machinery package is the third largescale machine investment with Haffner, and the latest machines will further support Bedfordshire Windows’ growth strategy.
Gary Walker, Director at Bedfordshire Windows, said: “We have seen a large upturn in demand for our products, and the new automated machines from Haffner will allow us further to improve our production efficiencies in line with customer demand.”
The new machines come hot on the heels of the company’s investment in a Haffner TT405 Double mitre saw in December 2020, which further upscaled their production output. Gary commented: “We have purchased several automated machines from Haffner in the past and we did not hesitate to turn to them to help support us in our latest manufacturing expansion.” Haffner’s SMR-4 Four Headed Welder drives fast and accurate inline welds, bringing further efficiency to Bedfordshire’s manufacturing operation. As well as features to speed up production, the SMR-4 is designed to improve product quality and cut waste. It is factory set each time and has automatic transom fences, automatic corner fences and automatic transom and mullion alignment, all features that add exceptional value to the fabrication process. Equally impressive is the Haffner TT425 double-mitre computerised saw’s credentials which provides superb length, angle and cutting accuracy thanks to its robust construction and linear bearing system. Gary commented: “The benefits of automation and the reliability of Haffner’s machines is second to none and allows us to scale up production as and when we need too.”
Having trebled their turnover in 2020, Bedfordshire Windows is showing no signs of slowing down. The company has been established for over four years and manufacture a wide range of window and door products to exceptional standards, and offer a quick and reliable turnaround. Bryan Dando, Area Sales Manager at Haffner, said: “One of the clearest indications of a reliable and trustworthy business is how previous customers are willing to return when they need to make a new investment. We are delighted to have supported Bedfordshire Windows once again.” Haffner’s returning customer rate is exceptionally high, and Gary’s comments show precisely why the company is fast becoming the industry’s go-to machinery experts. Tel: 01785 222421 – www.haffnermurat.com
DOOR AND WINDOW SYSTEMS CONTINUES ITS PRODUCTIVITY DRIVE WITH A FIFTH NEW KOMBIMATEC MACHINE
Door and Window Systems (DAWS), a Liverpool-based fabricator, continues to increase productivity in response to customer demand, with the recent installation of its fifth new Kombimatec machine in 18 months – this time, the AMC308 Automatic CNC Machining Centre.
DAWS is a family-run business specialising in the manufacture of high-quality aluminium doors, windows, bi-folds and rooflights for both the domestic and commercial markets. The company was looking to increase productivity and boost its business growth cost effectively without the need to take on new staff – and Kombimatec provided the solutions. When its latest addition of the AMC308 machining centre joined the fabricator’s manufacturing plant in Bootle, it was immediately among friends as almost every machine DAWS has is a Kombimatec. Within the last 18 months alone, the company also purchased a DGS500 Electronic Double Mitre Saw, CC120 Power Crimper, AFV362 Variable Angle End Miller and MGS460 Upstroke Mitre Saw. The AMC308 machining centre was developed by Kombimatec for both aluminium and PVC-U profiles. Manufactured with a solid steel construction using high quality components, it incorporates advanced CNC control with CADCAM software that provides exceptional levels of precision and reliability during production. DAWS version comes with a 5HP electro-spindle inverter driven to 180000 rpm, closed loop servo driven system, automatic safety guard, and voltage monitor for electrical protection. Like all Kombimatec machinery, the userfriendly AMC308 machining centre is a cinch to operate and program, so all the staff at DAWS are able to use it with ease. An automatic multi-tool changer allows the machine to process complex tasks without interruption, and it automates traditionally time-consuming tasks – including all drilling, routing, slotting, and milling functions – allowing staff to get on with other jobs. Its faster processing speed increases output while the machine’s accuracy reduces wastage too. According to Dave Harrison, Director at DAWS, “The AMC308 is a benchmark for fabricators establishing a window fabricating business in our industry. Previously we used manual copy routers to complete the prep work and it got to the point where we had one person working the router all day. From a cost point of view this machine will easily pay for itself in 2 years. For us, the main benefits are accuracy and efficiency. The CNC has enabled us to increase our output massively.” Operations on the production floor are now super-efficient as the whole team has benefited from the improved processing, with the aim to increase efficiencies and processing orders and accelerate business growth – all while ensuring the everimportant consistent high quality and precision of the results. “Like many of our loyal customers, DAWS prides itself on supplying the best quality, premium door and window products on time every time – and Kombimatec are proud to continue to provide the solutions to help them achieve that,” said Kombimatec’s Director David Parsons.
Kombimatec have been an industry-leading manufacturer and supplier of precision machinery used to fabricate windows and doors for over 35 years, delivering machines for working PVC-U and aluminium profiles in the UK and worldwide.
For further information on Kombimatec’s range of CNC machining centres call directly on 01582562218 or email sales@ kombimatec.com.
www.kombimatec.com
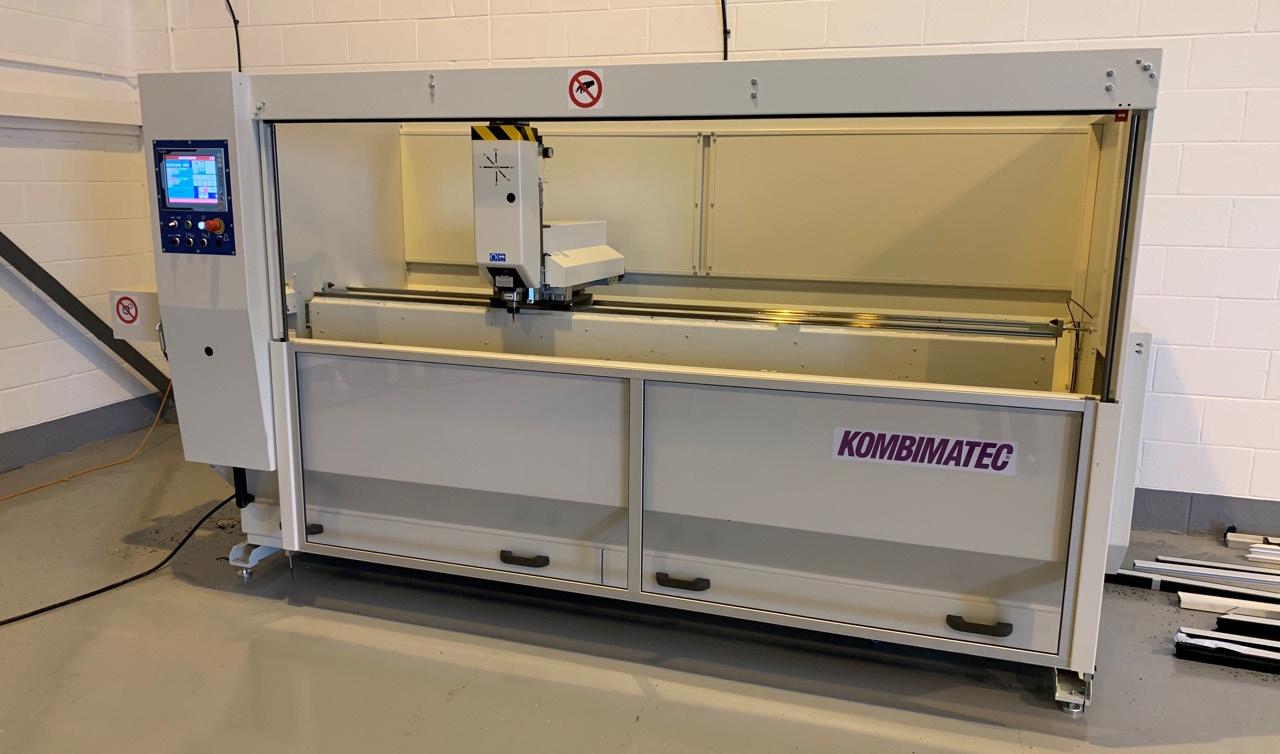
The UK’s Leading Glass & Glazing Newspaper
TRADE NEWS DELIVERING THE BEST
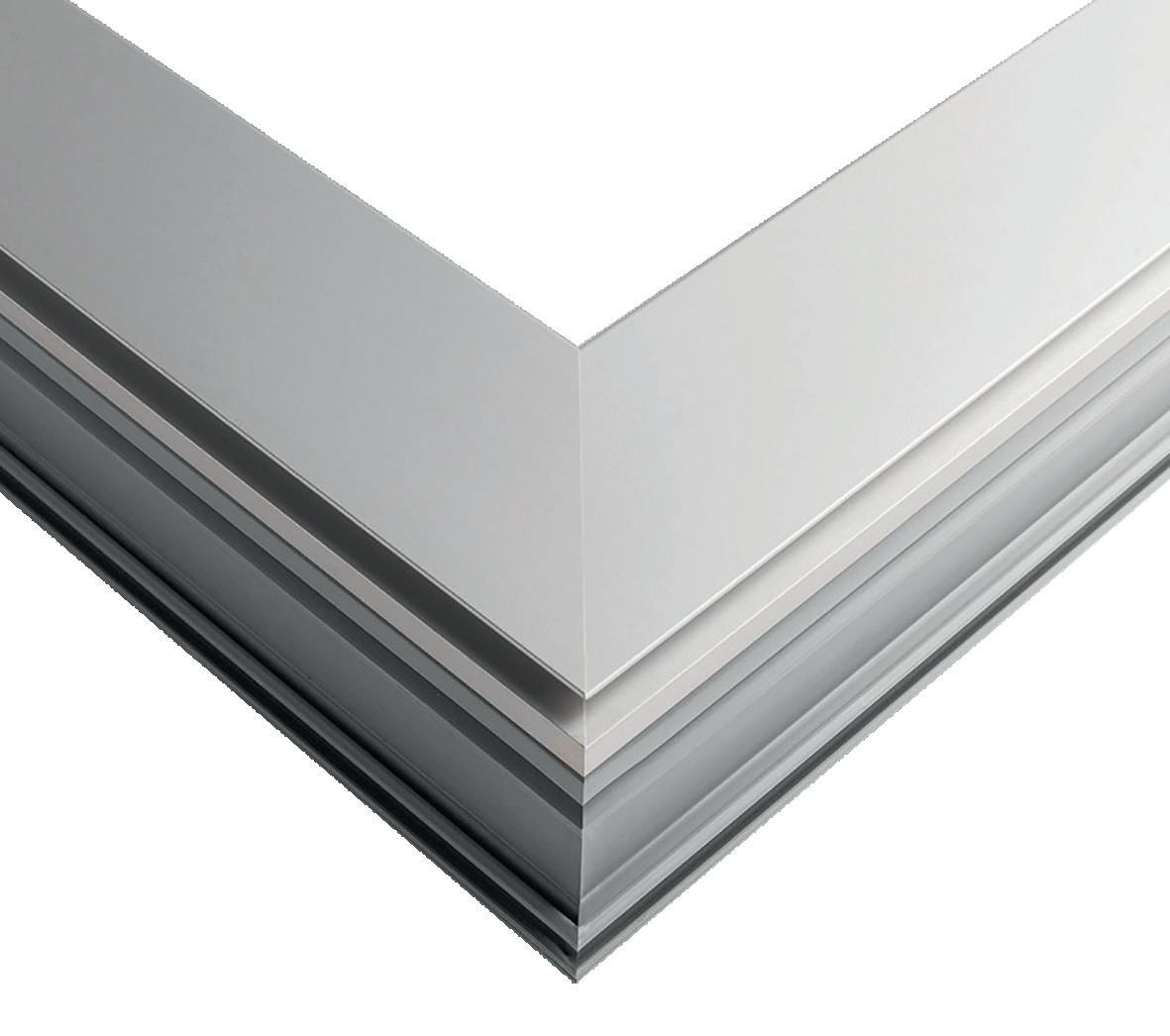
IN SEAMLESS WELDING TECHNOLOGY
STAND H21
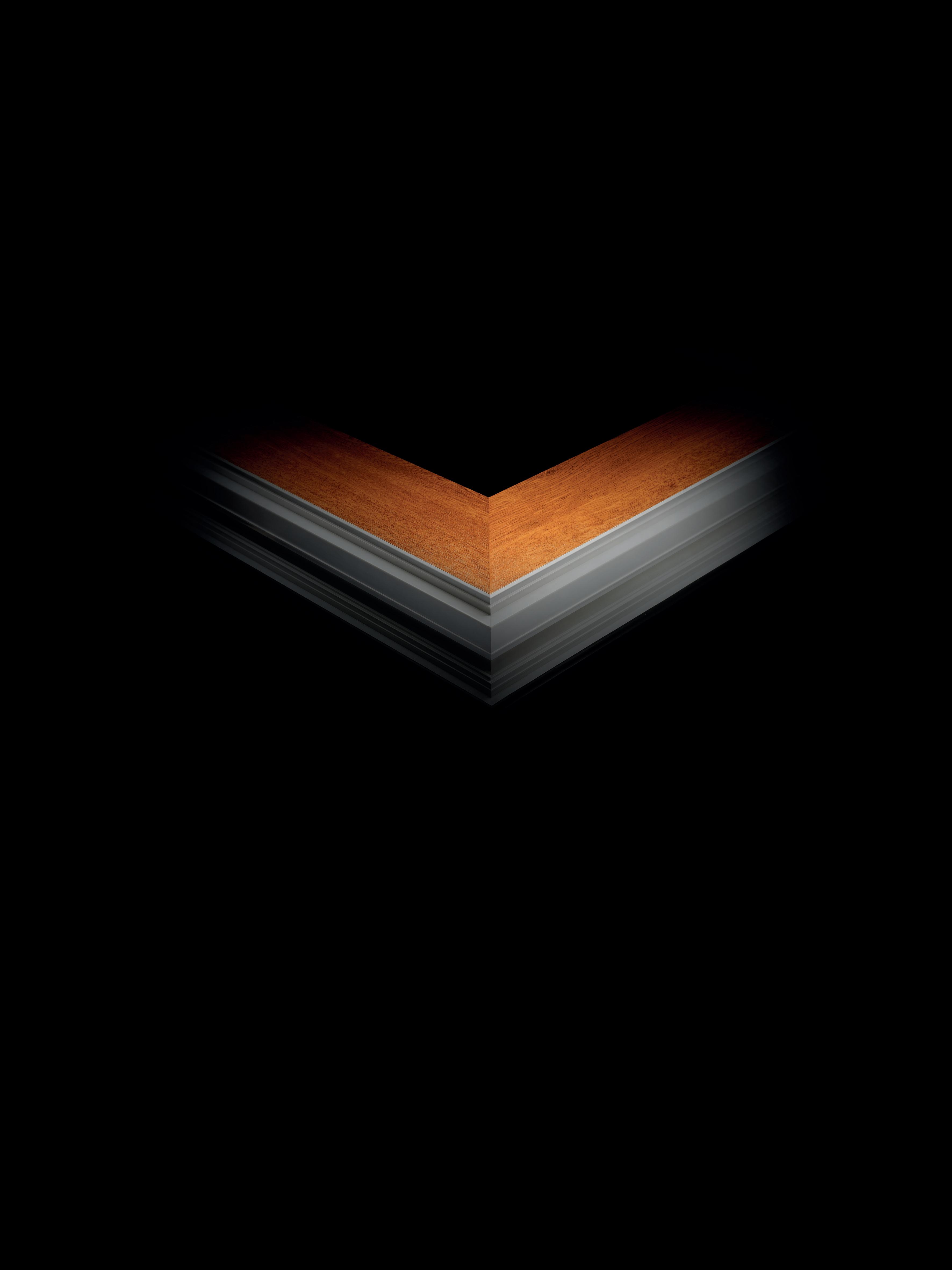
• Superior transom welding quality • Utilising patented V-Perfect® transom welding • Precision accuracy – delivering a perfect weld every time • Weld seam elimination