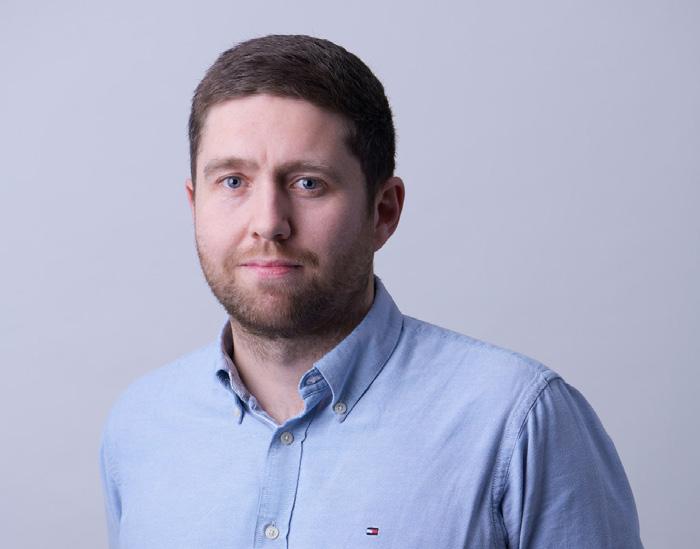
9 minute read
What Door?
NEW SITE OPENS DOORS FOR NEXT STAGE OF VIRTUOSO DOORS BOUNCEBACK
An intensive programme of factory upgrades following a site move is putting Gateshead-based composite door manufacturer Virtuoso Doors back on the path to renewed growth. The company is now producing up to 200 doors per day, despite the backdrop of the pandemic, materials shortages and escalating customer demand.
Virtuoso Doors manufactures high quality composite doors and PVCu door panels through a mix of precision engineering and workshop finishing supplying doors with stunning detail and unrivalled quality. The company moved from its original Chester-le-Street manufacturing site to the new purpose-built site at Follingsby Park, Gateshead at the start of 2021. The site, formerly the clothing warehouse for Barbour, has a 120,00 sq. ft. footprint and will double the capacity and manufacturing capability of Virtuoso Doors. Over the course of the year the site has had a power upgrade to meet manufacturing requirements, a new compressed air system, and state of the art extraction system installed. In addition, a new automated paint line has come online allowing for a greater choice of custom colours to be chosen by customers. New lift assist systems allow the factory technicians and craftsmen to work on the door units quickly and safely, without compromising on the crafted precision ethos of Virtuoso Doors.
Furthermore the move to a more modern building is allowing for a number of improvements to staff facilities from the catering and break areas to the office space. As most manufacturing businesses are experiencing 2021 has not been without its challenges, as ongoing supply chain issues and the need to carefully manage the needs of employees returning to more normal working patterns as COVID-19 restrictions ease, have been met with incredible consumer demand for home improvement products. However Virtuoso Doors has been able to adapt to the circumstances, has managed to secure a firm supply of the all-important door slabs needed for production and is well positioned to finish 2021 strongly. Virtuoso is now able to produce at a capacity of 200 doors per day. Tony Craggs, Managing Director, Virtuoso Doors: “With our teams having to adapt to changing conditions on a daily and weekly basis, it is important we don’t lose sight on how much has been achieved this year to put Virtuoso Doors on the front footing. We’ve moved from a cramped site to a state of the art location with significantly more space and ability to grow further, which will help us create new jobs over time. Every purchase has been made with a view to improving the quality and precision of our manufacturing processes, and the doors that we deliver to customers at the end of each day. “There is never a good time to move home, but for our team to have done this during the pandemic under the COVID-related restrictions, and then continued to apply their talent and skills to bring the machinery on site up to speed, while others have adapted to the new supply chain realities to secure a source of necessary components, it is a very proud achievement for us.”
MODPLAN REPORTS SIGNIFICANT GROWTH IN PATIO DOOR SALES
Trade fabricator Modplan has reported considerable growth in its patio door sales. Heidi Sachs, Managing Director of Modplan, commented: “Our customers tell us that retail sales of patio doors remain very strong at the moment as homeowners look to upgrade and improve their spaces. The quality, turnaround and versatility of our sliding door offer ticks all the boxes for our customers.”
Modplan manufactures the VEKA PVC-U patio door system and its versatility is a strong selling point. The system is available in two, three and four pane options. The maximum size for a four-pane door is 5,400mm x 2,200mm, which delivers the huge expanse of glass that is so popular with homeowners. The doors are available in sculptured or chamfered options and are compatible with all Modplan’s VEKA manufactured products. There are 29 colour combinations, giving installers confidence to promote a wealth of choice when it comes to colour. There are handle choices too, including high-quality stainless-steel options if required. As you would expect from a Modplan manufactured product, security is exceptional and the doors have a stainless steel, multi point, Yale locking system as standard. A secured by Design option is also available.
Heidi commented: “We’ve partnered with VEKA for 25 years because they are consistently at the forefront of window and door system design and allow us to manufacture the value-added products our customers need to grow their businesses. The patio door system is the perfect example.” As Modplan’s customers know, impressive products are just the starting point. Modplan manufactures its patio doors in their dedicated door factory to ensure outstanding quality and competitive lead times. To drive customer service, their internal Control Hub gives at-aglance information on the status of every order across their multi-site fabrication centres, giving customers a greater level of transparency to help them plan their jobs with accuracy. Customers also benefit from the company’s partnership approach that delivers marketing, technical and training support that adds value to an installer’s business.
Overall, it’s an offer that explains why Modplan is approaching 50 years in business and why so many installers choose the Newport-based company to support their growth in a strong market. Tel: 01495 246844 www.modplan.co.uk
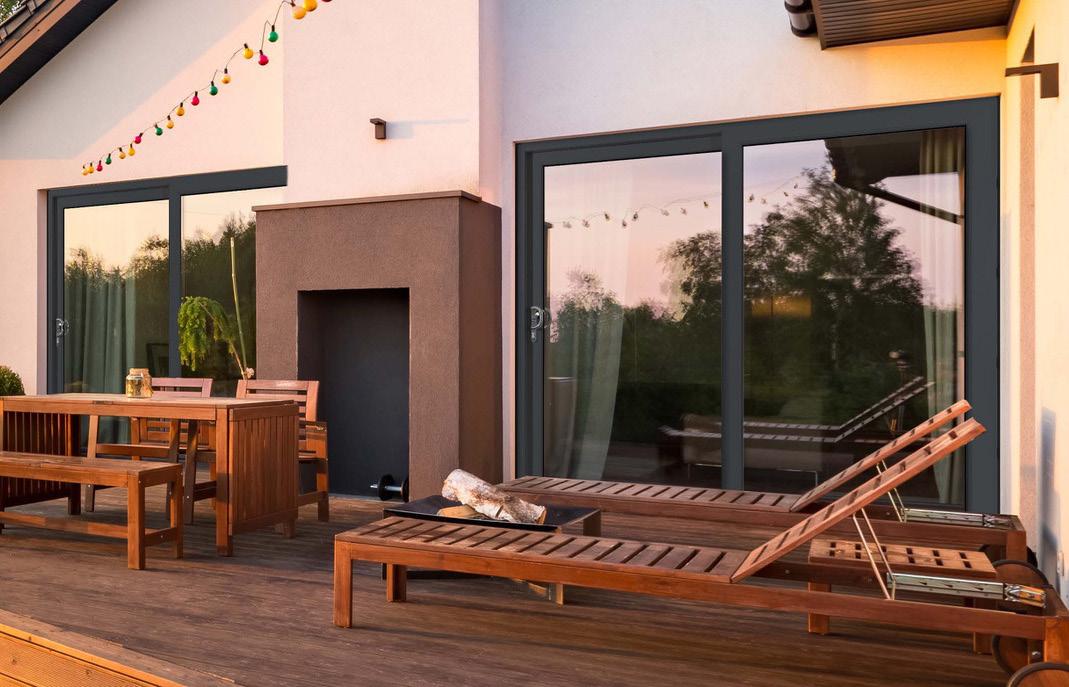
SUCCESS BREEDS SUCCESS FOR APEER AND WINDOW & DOOR CENTRE NORTH EAST
A new front door for a residential refurbishment in Bishops Auckland, Co. Durham resulted in added insulation, security and aesthetic appeal for one happy homeowner – plus increased sales for the Apeer trade partner after photos of the project were shared on social media.
Window & Door Centre North East Ltd undertook the eight week project after a customer came into their showroom and went straight to the anthracite grey Silka Wilton door on display. A survey was booked, further products were also ordered, following which work on the house began. The resulting installation not only updated the building’s exterior, the fitting of the 70mm insulated door also helped improve the home’s insulation and security. Photos from the finished project were then shared on the company’s social media, which generated interest from other potential customers as well as resulting in follow on sales. Window & Door Centre North East has been an Apeer customer for more than eight years, supplying Apeer composite doors, in particular from the Apeer 70 and Silka ranges. “Our customers like the style and designs of Apeer’s doors, especially the smooth texture of the Silka doors,” said Managing Director Eddie Wood. “The quality of the products speak for themselves: Apeer has a wide and varied range of doors and styles. Their glazing design options and colour matching services are also a great selling point for us.” As an Apeer trade partner, Window & Door Centre North East benefits not just from the quality products but from Apeer’s support throughout the sales process: “Apeer’s after sales and customer service are always supportive and on hand to assist us,” added Eddie.
Apeer’s Managing Director Asa McGillian said: “We know customers love our products, but we also rely on the excellent installations from our trade partners, such as Window & Door Centre North East. This is why we always make it a priority to give them any additional support that they may need to deliver successful projects, such as this one.” www.apeer.co.uk
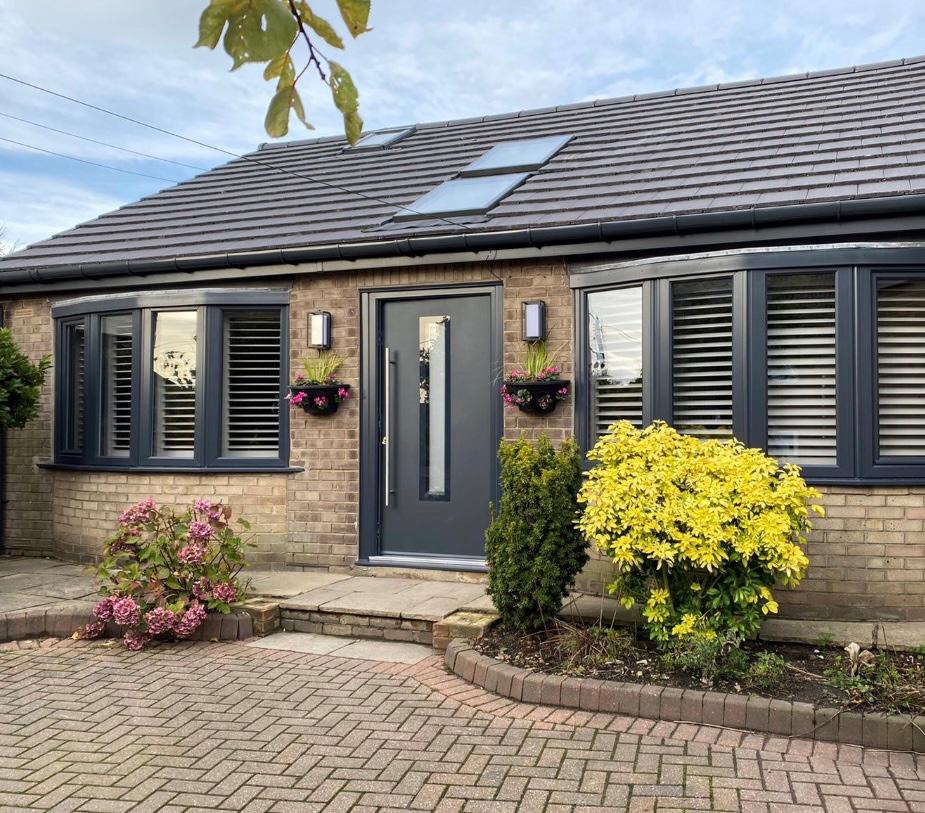
A REVOLUTION IN CUSTOMER CARE FROM ENDURANCE
The quest for an ever-better customer experience continues at Endurance Doors with the introduction of Amicus, a new automated ticketing system which improves the flow of information to and from Installer Partners.
This investment in Amicus, which is part of a wider programme of new IT infrastructure, has been implemented to help streamline the whole customer query process and the ticketing system will ensure that all communications are fully traceable and trackable. It’s also the same sort of platform that’s used by some of the most trusted and respected consumer brands in the UK. Any customer query that’s raised online will be followed by the receipt of a formal acknowledgement within minutes and subsequently a member of the customer care team appointed to that ticket within Amicus. Early beta testing of this software has shown that it speeds up communications between Endurance and their Installer Partners significantly and without the issues of staff absences and holidays which can hamper the traditional operations of a customer care team. It’s also part of a programme to build a worldclass customer care programme as Kayleigh Startup, Customer Relationships Manager of Endurance Doors explains: ‘The Amicus ticketing system is part of a wider investment programme that’s been partly driven by customer demand, through important feedback that we’ve taken on board. We’ve got a thirst to be the very best at what we do not just in terms of producing an outstanding composite door, but in every other way that we engage with our Installer Partners.’ Stephen Nadin, managing director of Endurance Doors added: ‘After much testing I’m delighted to introduce our latest service initiative so that our Installer Partners can access the Amicus ticketing system 24 hours a day and 7 days a week, whilst also helping us to improve in other ways across the business. Data is now very much part of the way in which this business will evolve, yet without ignoring the human touch which helps makes this business so special.’ For further information on the Endurance Solid and Secure composite door range, including the latest colours and finishes, please call the sales office on 01652 659259, visit https://endurancedoors.co.uk, or e-mail marketing@endurancedoors.co.uk. You can also add to the Twitter following @EnduranceDoors.
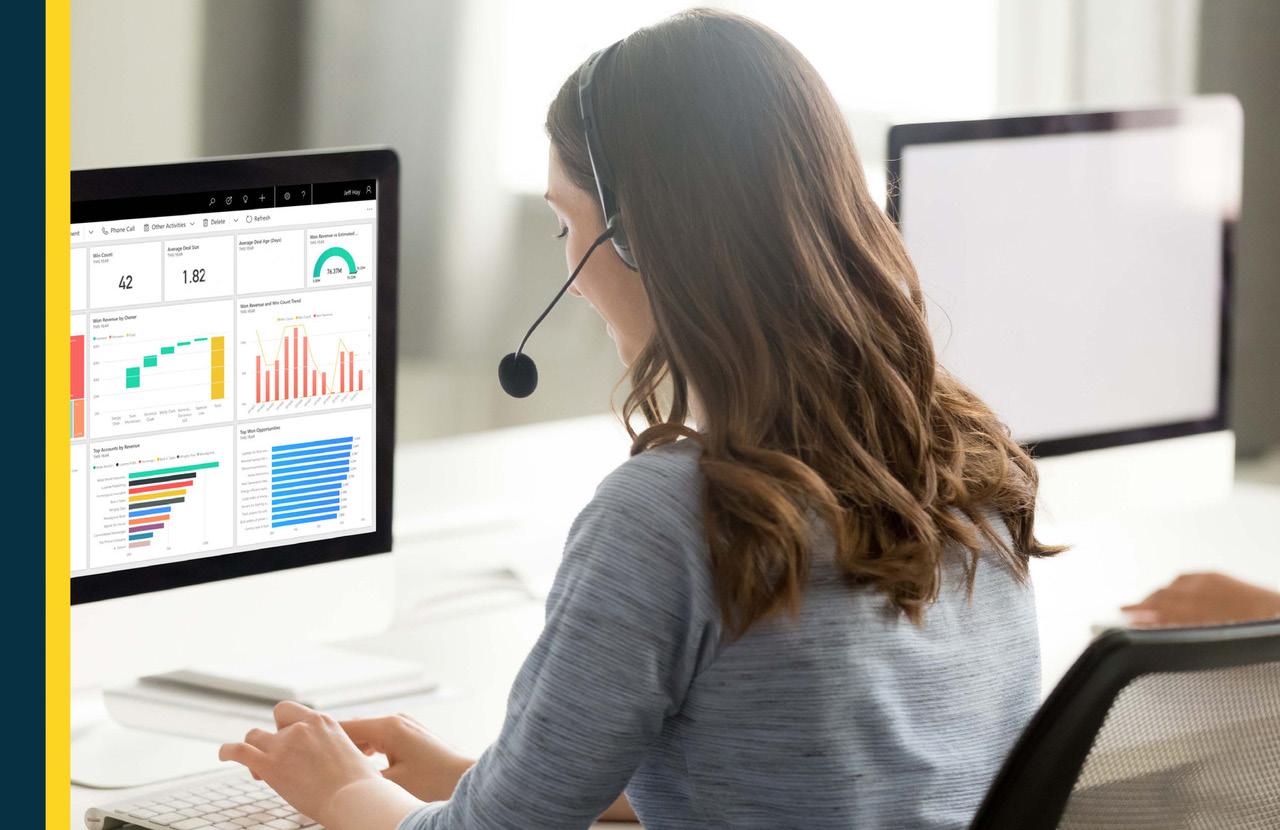

Monza II Augusta Long Door Built With Monza II Augusta Long Door Built With InnovationInnovation
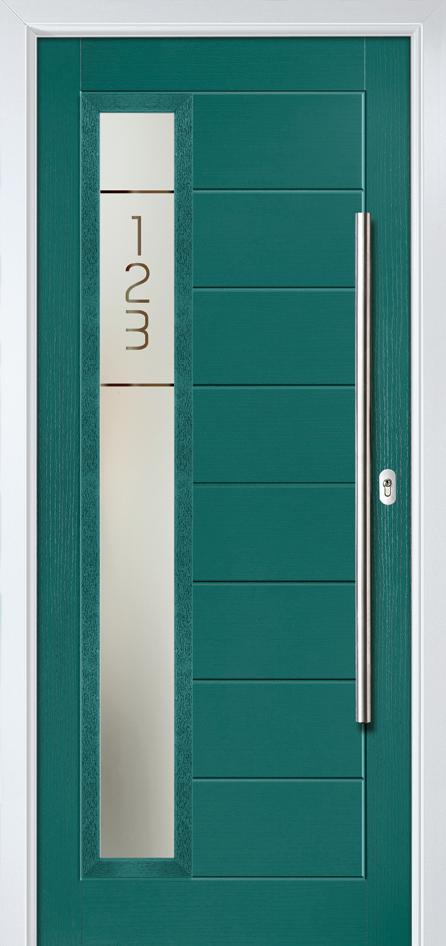
Brought to you by DoorCo, the ultimate composite door is engineered Brought to you by DoorCo, the ultimate composite door is engineered with GRiPCORE technology - a hybrid of traditional & modern with GRiPCORE technology - a hybrid of traditional & modern materials engineered to deliver a stronger, heavier and more robust materials engineered to deliver a stronger, heavier and more robust door and designed with FLiP Flat Grained, our innovative glazing door and designed with FLiP Flat Grained, our innovative glazing cassette with Foam In Place technology.cassette with Foam In Place technology.
Find out more →Find out more → door-co.comdoor-co.com
Email. info@door-co.com | Call. 01625 428955Email. info@door-co.com | Call. 01625 428955 DOORCO, M6 Motorway House, Charter Way, Macclesfield, SK10 2NY DOORCO, M6 Motorway House, Charter Way, Macclesfield, SK10 2NY