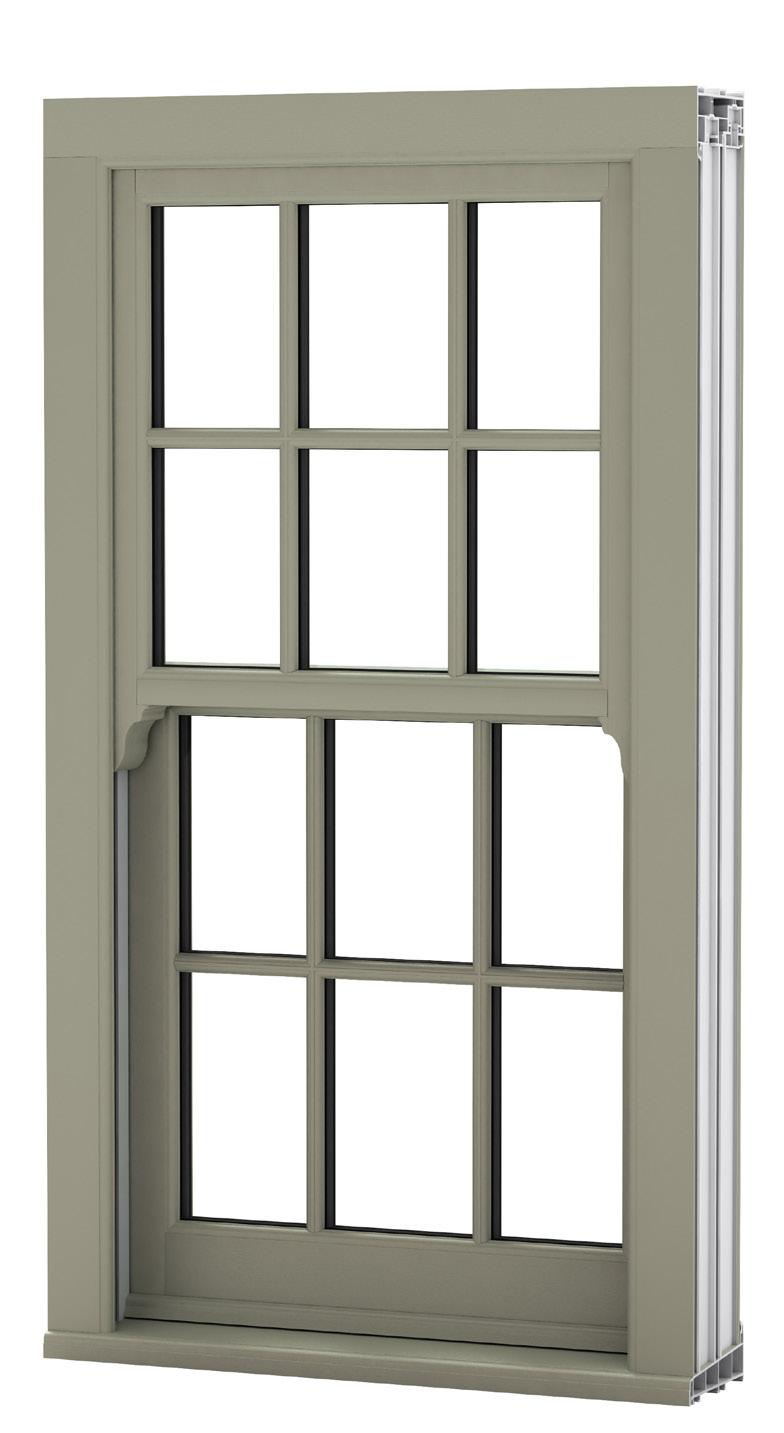
2 minute read
AT THE CUTTING EDGE
focussed our efforts on how we can ensure we are doing what we need to do in order to stay ahead of the game.
“For us, the solution was a move to further automation in production to standardise quality and increase our capacity and efficiencies – but of a very individual kind which will give us the flexibility going forward to develop the right products that we know our trade partners want.” having to consider lots of elements such as steel types, steel positioning and screw positioning, for example. “Because it is unlike any off-the-shelf cutting centre, it required bespoke software,” says Ben. “It truly is a unique machine which will
It was back in April 2021 that Quickslide first began talking to Winmac about purchasing a bespoke machining centre from Schirmer that would enable the leading PVCu sash window manufacturer to achieve its aims: for greater automation to increase production, speed and efficiencies while ensuring consistent and repeatable high quality for every vertical slider that comes off the end of the production line. What started as a conversation turned into a purchase in December and then became a practical plan to bring the first machine of its kind to UK shores from Germany. Six large lorries took three days to deliver the load, which took a week to assemble and a further four weeks to get it fully commissioned.
“At £1.5m this purchase represents our biggest investment to date,” says Quickslide’s Managing Director Ben Weber. “Rising material costs since Covid, along with our desire to make sure we are producing the best products needed to keep at the forefront of our industry, have really
So advanced is the new machining centre that Quickslide’s software supplier Business Micros had to build reinforcing into their software for it. This is no mean feat, enable us to change the way we produce vertical sliders.”
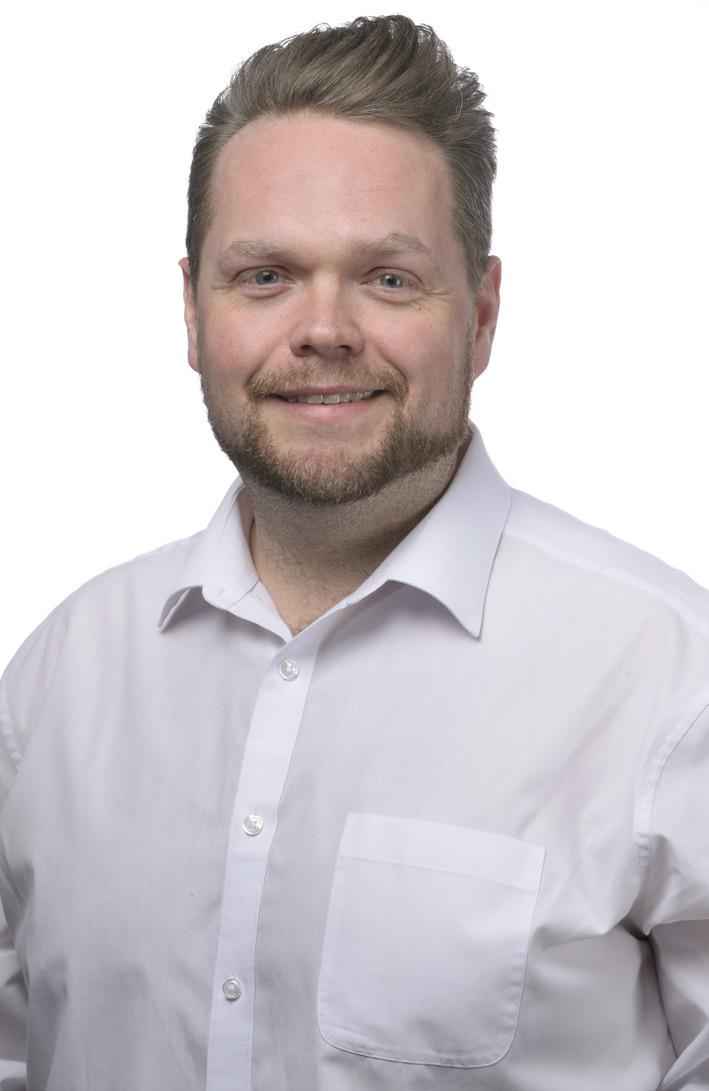
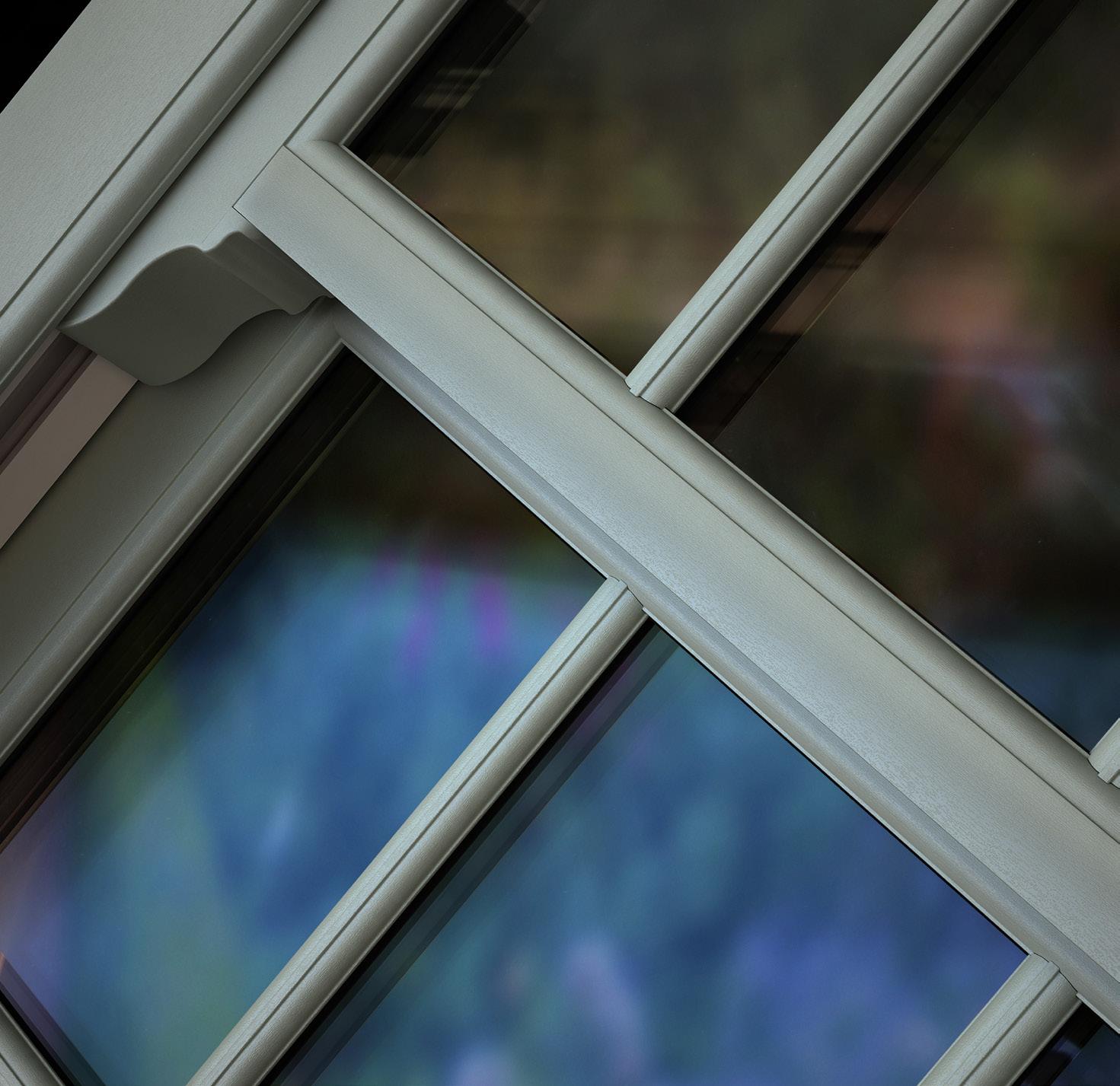
Twice As Good
The new machining centre comes with two milling stations. “This will really increase our capacity for authentic heritage VS, particularly when it comes to mechanical joints,” says Ben.
“There are so many complex features involved in fabricating a VS window. Having two milling stations not only means we can consistently achieve the high standards we and our customers demand every time, but it also means we can do that without adding to our lead time.
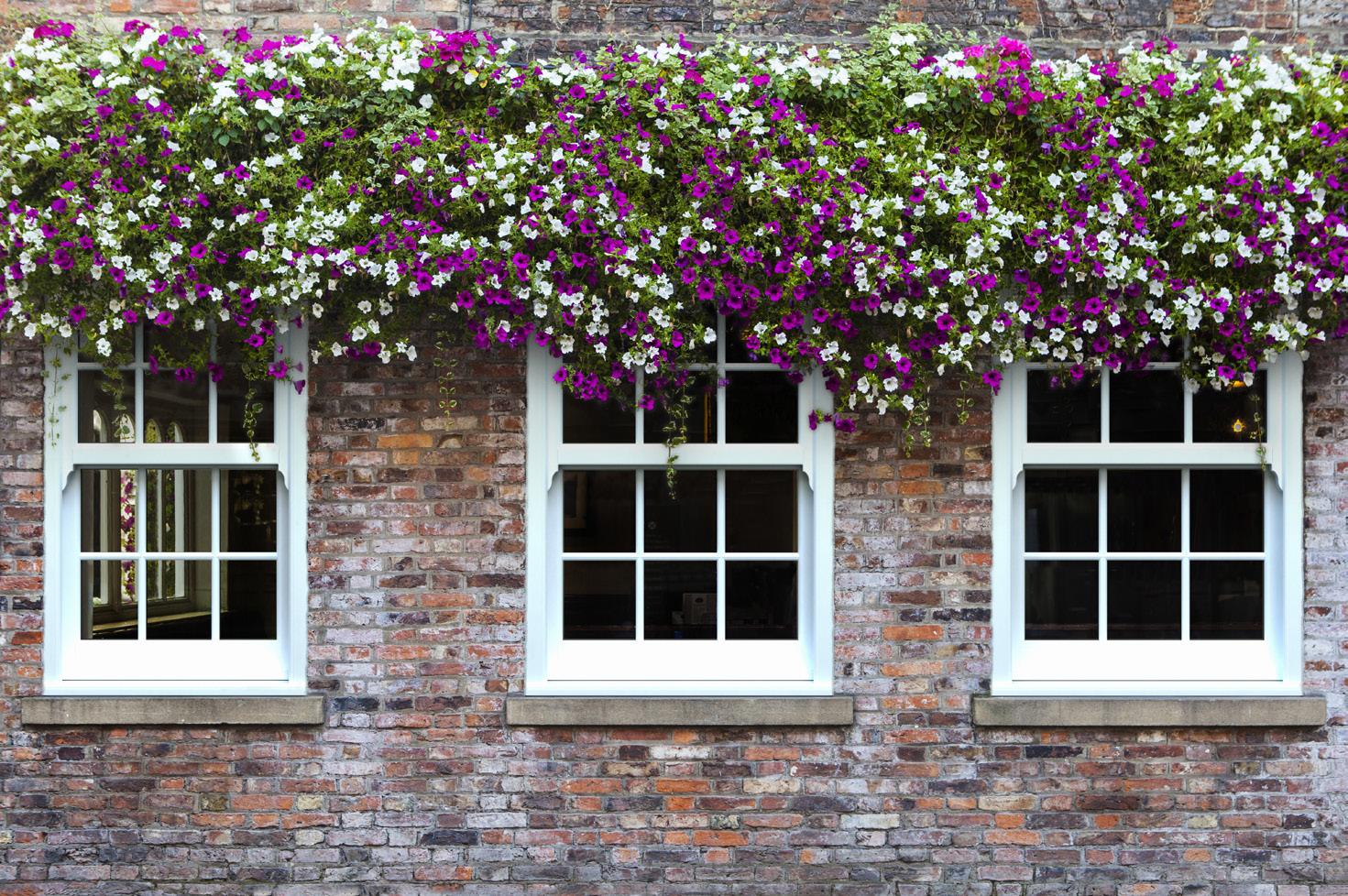
“Our new machining centre also enables us to improve our efficiencies, not just in optimising material usage but also in our staffing. For example, we used to have six people employed on the reinforcing process – automating this means they can now be redeployed elsewhere in our business where they are most valuable.”
It has also meant the previous Schirmer cutting centre that Quickslide bought only three years ago has now been moved into PVCu casement production, where it too will increase efficiencies.
“We anticipate we’ll improve material optimisation by 12-15% by moving our milling process in casements to the cutting centre. Using offcuts more efficiently than can be done by hand means we’ll waste a lot less profile, which is better for us, our customers, and the planet.
With the new machining centre now up and running in Quickslide’s Brighouse HQ, the results are already starting to show. Ben says: “The best thing about the new machine is that its benefits can be seen both immediately and in the scope, it gives us the flexibility to develop our product range for the future. To that end, we already have further exciting developments planned for our vertical sliders which we anticipate announcing later this year… so watch this space.” www.quickslide.co.uk