
4 minute read
Rehabilitating Solomon Mahlangu Drive’s concrete pavement
from IMIESA April 2020
by 3S Media
Raubex KZN is in the process of successfully resurfacing one of South Africa’s most strategic commercial links. The scope entails the upgrading of the M7 (Solomon Mahlangu Drive) between South Coast Road and the N2 freeway, with labour-intensive techniques and SMME training forming core components.
By Muhammad Kader*
Advertisement
The M7 is a major truck route extending from the Port of Durban to the N3, linking Gauteng and the Free State, and the N2 North and South. The road was not originally designed to handle the current volume of heavy motor vehicles, resulting in the rapid deterioration of the road surface.
The road in question is currently undergoing structural failure through the concrete layer, as well as the asphalt interlayer between the old (lower) concrete and new concrete slabs on the road surface. The design of the rehabilitation entails the removal of the concrete layer, as well as the asphalt interlayer, using the old concrete layer as a base on which to rebuild the road using EME 20 (High Modulus Asphalt with a 20 mm nominal stone size).
Once awarded, Raubex KZN proceeded to compile a programme of works to encompass not only the technical requirements for reconstruction, but also to provide consistent community development throughout the project duration.

Subcontractor selection
Prior to the commencement of the project, we approached business support for the selection of local subcontractors. Business support then approached the relevant ward councillors for their appointment. Once these subcontractors were selected, their company profiles were submitted for approval before we could establish on-site. We have a list of 60 subcontractors to appoint on this project, of which we have already employed 29 on-site.
Major failures on a section of the existing concrete surface An aerial perspective of the M7
Removal of concrete
We are implementing a labour-intensive approach in order to remove the existing concrete road. The first process involves the removal of the first layer of concrete above the steel, which is generally 70 mm below the surface. Where necessary, we are removing a further 20 mm of concrete to get as close as possible to the steel reinforcing. Beneath the steel, another 50 mm of concrete is milled off and thereafter a final asphalt layer of 50 mm.
We currently have 11 subcontractors working to break and remove the steel, each employing four local labourers, contributing large amounts of the contract value to the CPG spend. These subcontractors are all at CIDB level 1.
We are assisting them all with upgrading their CIDB grading to level 2. The goal is to uplift their status in the industry and teach them valuable skills to assist them in succeeding independently after the completion of the contract.
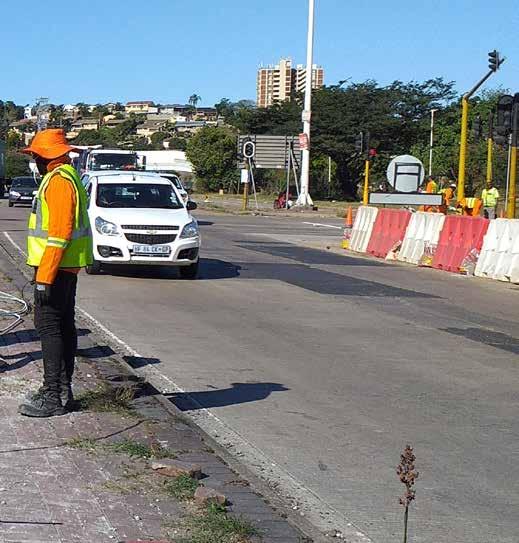
We have assisted them with setting up a safety file and are constantly teaching them how to update it, complying with OHS rules and regulations. Furthermore, we have sent individuals from every subcontractor for health and safety training. We have assisted them in putting a quotation together at a marketrelated rate that they will get paid for the work they do on-site.
They work directly under our supervision on-site so that we can teach them the most efficient and safe way to utilise the equipment. They take measurements on-site of their work done and compile a monthly Payment Major failures on a section of the existing concrete surface Certificate for their invoices.
This is all done under our supervision and guidance. Our goal is to assist small business owners in getting a solid foothold in the industry and providing them with all the necessary training and skills for them to progress in the future.
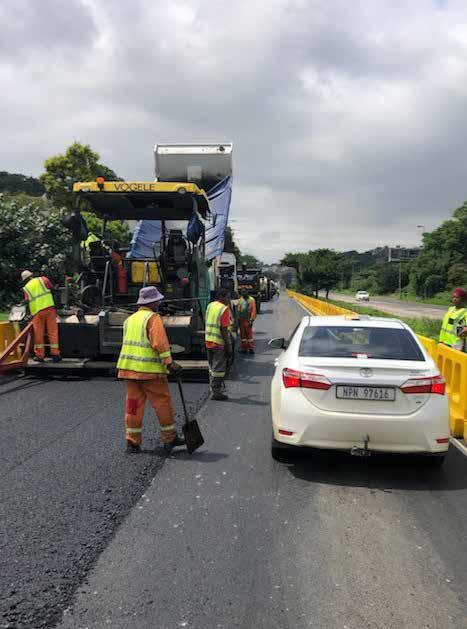
Paving
EME 20 exhibits superior load spreading characteristics, which is ideal for the M7, being a heavily trafficked truck route. We are replacing an average of 210 mm of concrete with three layers of EME 20 (approximately 70 mm thick), in order to ensure adequate compaction of the asphalt during the construction process. Once the EME base has been reconstructed, a wearing course of UTFC and SMA will follow, providing the final road surface.
Conclusion
The project will be completed within the allocated budget and project time. It is getting nearer to its final stages of completion, with a friction course still to be constructed and minor auxiliary works to be addressed.
Our aim of arresting the utter collapse of this corridor and bringing its condition to a functional state has substantial benefits to the local and national economy. Based on the requirements of this project, the noted trajectory indicates that it will be a tremendous success, with all aspects such as contractor participation goals, enterprise development, community upliftment, sustainability and expenditure being met. In addition to that, the final high-standard pavement delivered by the municipality will greatly benefit commuters.
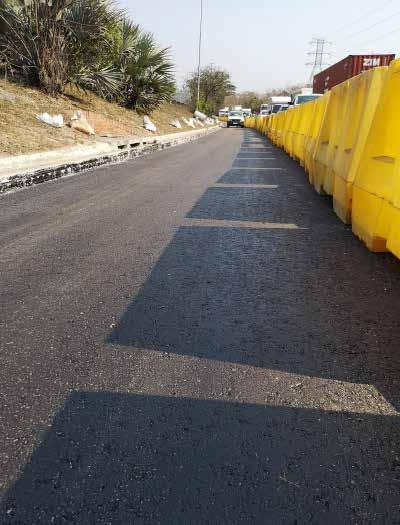