
6 minute read
Slurry microtunnelling solutions for SA hard rock conditions
from IMIESA April 2023
by 3S Media
Global population growth and increasing urbanisation are forcing cities to develop sustainable infrastructure for traffic, utility service supply and disposal networks.
Besides the drinking water supply, wastewater handling plays a fundamental role in urban development schemes. Thus, the large-scale provision of an efficient sewerage system is a major challenge in the steadily growing cities of South Africa. Existing networks have to be expanded and new high-capacity schemes built to meet future requirements in increasing sewage volume and growing challenges in flood protection.
Advertisement
The role of mechanised tunnelling
For South Africa’s upcoming water and sewage disposal projects, mechanised tunnelling and microtunnelling are indispensable to install the required infrastructure underground, with minimum impact on the surface.
Besides segment lining, which is mostly used to build main collector tunnels (ID ≥ 3 000 mm), microtunnelling with slurry pipejacking equipment has a long tradition in trenchless construction of sewer networks and link sewers. On an international scale, technological advancements and valuable experience gained by the contractors have pushed the boundaries in microtunnelling in terms of achievable drive length, tunnel diameter and ground conditions.
In the planning stage of tunnelling projects, clients and planners need a broad knowledge about the available technologies and the feasibility limits to go for in choosing the best suited and most efficient method. Subsequently, the close cooperation of technology supplier and contractors to design the tunnelling equipment will ensure a safe and reliable project execution.
Slurry microtunnelling in South Africa
With a rising number of projects executed with slurry microtunnelling in South Africa, clients and consultants are becoming more and more aware of the possibilities this technology offers. In addition, safety aspects are becoming more important in the construction industry. Remotely controlled microtunnelling is therefore an alternative to conventional methods, especially in the non-accessible diameter range (ID < 1 200 mm).
More than 10 years ago, the first Herrenknecht slurry microtunnelling had been used for utility projects in Durban. Later on, several AVN machines (ID 800/ 1 200 mm) successfully completed sewer projects in Cape Town, such as the Cape Flats 3 Bulk Sewer Phase 2 and Southern Corridor Farm 694 Bulk Sewer, for example. Other potential projects are being planned such as Philippi Sewer and Montague Drive Bulk Sewer in Cape Town, uMKhomazi Bulk Water Supply and the proposed tunnel in Buffalo City (East London).
Hard rock conditions
The challenging ground conditions in South Africa, mainly consisting of hard rock, require special solutions for tunnelling equipment in order to make projects economically and technically feasible.
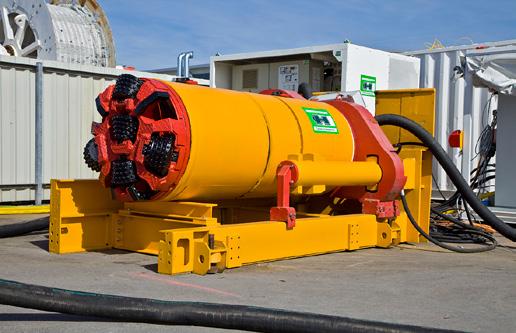
The continuous further development of slurry microtunnelling is important to cope with the varying geological conditions, including weathered rock, rock-soil transitions, as well as fractured and intact hard rock with high strength and abrasivity. In the past, in hard rock conditions, the applicability of slurry microtunnelling has been especially limited in the nonaccessible diameter range.
Nowadays, the ever-growing number of microtunnelling projects in hard rock conditions is mainly driven by recent technological developments to overcome the limitations in drive length and to improve performance.
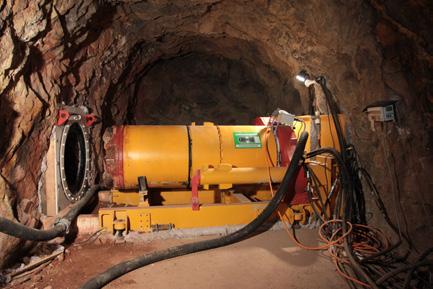
AVN 800 for hard rock
With the recent development of the powerful AVN 800 HR (OD 975 mm) for hard rock, Herrenknecht has developed a new machine type, which perfectly fits the
South African standard pipe diameter for sewerage projects. This microtunnelling TBM (MTBM) is equipped with a stronger main bearing and an adapted cutting wheel design.
The machine excavates the rock with a jacking force that is three times higher on the cutting wheel in comparison to the traditional AVN of the same size. A flushing ring at the bottom of the machine with remote-controlled ball valve prevents fine particles in the annulus, thus reducing jacking forces.
Technical improvements:
• for rock with high uniaxial compressive strength (UCS): up to 200 MPa
• extended drive length: up to 200 m
• high wear-resistance of TCI cutter discs
• increased rotation speed of cutting head: up to 26 rpm @ 260 ℓ /min
• stronger main bearing: 89 t
• compact jacking frame to achieve a small launch shaft of Ø 3.2 m
• operation by standard control container C20 possible
• flushing ring: fine rock particles to be kept away from annulus
• extension kit OD 1 295 mm with rock cutting wheel, up to 80 MPa possible.
Cutting wheel design and tooling
The cutting wheel’s tooling composition is the most critical part in rock applications. Tool size and arrangement are determined based on the rock properties in order to obtain reasonable rock chip sizes that can be handled by the discharge system. Three main cutting tool types can be considered for MTBMs: disc cutters, TCI cutters or milled tooth cutters.
The most common cutting tool remains the disc cutter, which is well known from large-diameter hard rock TBMs. However, due to space constraints, the disc cutter is normally modified into a double or triple disc cutter, which decreases the spacing and therefore leads to faster chipping of the rock.
On the other side, the larger number of rings on cutters decreases the available thrust force per ring and therefore decreases the probability of creating tensile cracks that lead to chipping. This makes it important that
EXHIBITORS: Book your stand NOW
Secure your stand now and have the opportunity to:
• present your company, products and services to a target audience
• gain industry insight and meet potential partners, suppliers and clients
• interact with key decision-makers and industry peers
25-27 October 2023 86 TH IMESA Conference
BOARDWALK HOTEL Gqeberha (Port Elizabeth)

SIGN UP FOR a Sponsorship
NOW
Sponsor a unique aspect of the conference and enjoy great benefits such as:
• free exhibition stands
• complimentary delegate registrations
• brand representation at the event, promotion of your company in the conference proceedings magazine and online
• free entry for guests at the social evening and much more.
Contact Us For Details
t: +27 (031)266 3263 e: conference@imesa.org.za marketing@imesa.org.za www.imesa.org.za small-diameter hard rock AVN machines have a capability of high jacking forces and both a strong main bearing and cutter bearing.
If this problem cannot be solved with a technical solution, or if a high requirement on the lifetime of the cutters exists, TCI or button cutters are recommended. This cutter type has also been chosen for the AVN 800 HR.
TCI cutters exert a point load force on the rock, resulting in numerous small chips. Due to the tungsten carbide insert, the TCI cutter is considered especially wearresistant, which is beneficial for long drives in small diameters, where cutterhead interventions are not possible.
AVN 800 HR in operation
The first tests of the AVN 800 HR equipment took place in early 2017 in Germany. In the meanwhile, several AVN 800 HR MTBMs are or have been in operation worldwide –e.g. in Australia, Brazil and Scandinavia.
One example of a successful reference project is the Water Main Improvement Project in Hong Kong in 2020. Slurry microtunnelling was selected as the preferred method to install the 107 m long section, with a constant radius of 153 m on a sewerage project, owned by the Water Supplies Department.
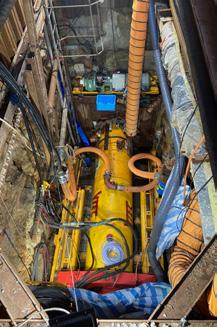
The complete tunnel alignment led through granitic rock with a maximum UCS of up to 200 MPa. Due to these hard rock conditions and the small diameter of only 960 mm (OD), an AVN 800 HR for hard rock was selected. As cutting tools, conical 317 mm cutters with TCI inserts were selected.
The AVN 800 HR has an installed power of 90 kW, enabling a maximum cutting wheel rotation speed of 26 rpm and a maximum torque of 55 kNm. Thanks to the innovative cutting tool choice, it took only 60 days to complete the drive, including several idle days.
Impact for the trenchless industry
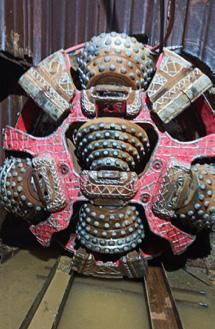
This AVN 800 for hard rock will push the boundaries of what is possible in smalldiameter microtunnelling in terms of feasible drive length in hard rock conditions. Longer drives make microtunnelling a more economic and environmentally friendly construction method. The number of shafts can be reduced, impact on the surface can be minimised, and the construction of larger tunnels only for access reasons can be avoided in certain projects.
About Herrenknecht Ag
Herrenknecht looks back on 45 years of experience in mechanised tunnelling. As the world´s leading manufacturer of tunnelling equipment, Herrenknecht maintains a close partnership with its customers, who have successfully completed countless tunnelling projects worldwide. Based on an international service network and reliable technology not only for tunnelling, but also for pipeline, mining and shaft sinking applications, Herrenknecht provides mechanised solutions for ambitious upcoming projects and their successful completion.
solutions, the boundaries of small-diameter slurry MTBMs in hard rock are continuously being pushed.
Furthermore, new opportunities for clients and consultants in the planning of tunnel routes for different infrastructure installations can be considered, making trenchless technologies even more competitive and cost-effective, while improving public acceptance at the same time.
Conclusion
Thanks to major technical developments such as innovations in machine performance, cutting tool design, peripheral equipment and digital
Water Main Improvement Project, Hong Kong: (A) Job site surroundings, (B) launch shaft, and (C) AVN 800 HR after breakthrough
In recent years, the trend towards smaller diameters and longer drives has been increased, which puts a larger focus on the design and selection of efficient MTBM equipment. This does not only serve the tunnelling industry in delivering infrastructural projects in growing South African cities like Johannesburg or Cape Town. Technological advances in tunnelling technologies will also be of great importance to the mining industry, with impact on the feasibility of future projects and applications. A B C
