
5 minute read
Why pipe jacking is a niche profession
from IMIESA August 2022
by 3S Media
A walkthrough inspection of a completed tunnel section
Pipe jacking – which is a technique used to tunnel medium to large services under roads, railways and other infrastructure – is a highly specialised field requiring expert application knowledge to yield optimal results, says Byron Field, director, BLOC Contractors.
Advertisement

On one of BLOC’s recent pipe jacking projects, the company completed an approximately 24-month contract working as a subcontractor on an extensive Rand Water maintenance and upgrade programme within the greater Johannesburg area.
BLOC’s scope entailed the execution of specialist subcontract works on key sections of Rand Water’s S4 and H47 pipelines. This comprised a total of 822 m of large-diameter pipe jacking over 15 No. crossings. Sizes were predominantly 2 800 mm diameter reinforced concrete pipe sleeves, with some smaller at 2 160 mm.
“These underground sleeves were necessary so that Rand Water could install their massive steel pipelines – some of which are up to 2 m in diameter – underneath critical infrastructure such as roads, railway lines and existing pipelines without having to disrupt the operations of these services,” Field explains.
BLOC is well positioned to handle largediameter pipes and culverts – where sections can weigh up to 10 tonnes – thanks to its fleet of heavy-duty gantries, which are uniquely designed to handle such large elements. Once the main pipeline contractor had installed the steel pipes, BLOC’s team went back to grout them in place to eliminate any voids.
“BLOC mobilised six teams to the various contract sites, some of whom worked day and night to achieve the tight deadlines,” Field continues, adding that ground conditions varied from waterlogged collapsible sands to very hard rock exceeding 180 MPa.
Due to the sensitive nature of various overhead structures, especially rail infrastructure, conventional blasting of hard rock zones was not always permissible during pipe jacking operations. Where these conditions were encountered, BLOC employed a combination of proprietary lowvibration blasting (suited to confined space work), as well as specialised hydraulic rock splitters.
Responding to variable ground conditions
On any pipe jacking programme, one of the major threats is a potential catastrophic failure of the tunnel front face. That needs to be avoided at all costs.
“To illustrate the point, during the pipe jacking programme for the 2 800 mm sleeves on the Rand Water project, the excavated front face of the tunnel measured some 6.5 m2. This front face must be kept constantly under control. When tunnelling through rock, that’s much less of an issue, but where collapsible soils are encountered – together with high water tables – it’s a different story altogether,” Field explains.
“This is where the proficiency and experience of the pipe jacking specialist is crucial to prevent potential settlement of aboveground structures like buildings, roads and rail. Clearly, that’s the whole purpose of employing this trenchless technology in the first place – to optimise time and cost efficiencies compared to open-trench options – but perfecting the approach is what sets the benchmark locally and globally,” Field continues.
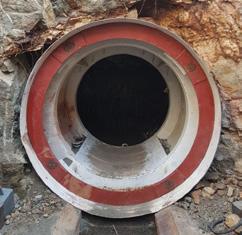
Method statement
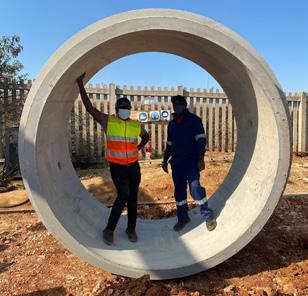
The method statement starts with a determination of the jacking capacity required, based on the length, diameter and geology. As part of the temporary works, a thrust wall is then constructed (anchored into the ground) in the launch pit to accommodate the horizontal jacking loads. “Getting these temporary works calculations correct is essential for a successful launch, especially on longer and larger-diameter pipelines,” Field explains.
Custom shield designs
Spearheading the tunnel excavation is the pipe jacking shield, which needs to be configured specifically for every project in terms of known and anticipated ground conditions. Shield designs vary greatly, ranging from high-tech tunnel boring machines with multiple rotating cutting heads, to more simplified drilling and/or backhoe excavation configurations. In all cases, though, the shield preserves the integrity of the front face as pipe jacking incrementally progresses.
“Depending on the ground conditions, we may need to dewater ahead of the shield, or we may need to grout ahead and above the tunnel excavation. Every pipe jacking job presents its own specific set of challenges. Responding requires decades of experience, backed by a comprehensive toolbox to match the varying geology, and at times unexpected encounters with unmapped services,” Field explains.
Reinforced concrete pipe sleeves employed on BLOC Contractors’ Rand Water project Installation of the pipe jacking shield resting on its guide rails. As excavation progresses, highpowered hydraulic jacks attached to the thrust wall push the concrete sleeve sections ahead to form the tunnel
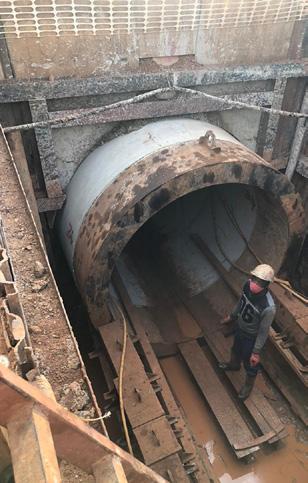
Concrete jacking sleeves for the Rand Water project were predominantly 2 800 mm in diameter, with some smaller at 2 160 mm
Meeting the challenge
A prime example is the solution BLOC developed to overcome an obstacle on its Rand Water project. On one of the sections, BLOC’s jacking team had already advanced some 15 m underneath a main road when its progression was blocked by a previously unidentified stormwater pipe crossing the tunnel face.
One option would have been to abandon the existing work and restart the tunnel at a different level, which would have incurred major additional costs for the client. The solution BLOC presented was to partially reverse the installed tunnel. To achieve this, BLOC built a temporary wall in the front to jack the sleeves back, while installing temporary propping to support the tunnel.
“Once we’d moved back far enough, we then adjusted the grade downward and jacked underneath the stormwater pipe on to a new level to complete this pipe jacking phase,” Field explains.
“It’s highly unusual to reverse a jacked pipe, and this underscores our ability to innovate, while adhering to rigorous health and safety practices,” Field concludes.
In places, hard rock exceeding 180 MPa was encountered. This was cleared using a combination of proprietary lowvibration blasting (suited to confined space work), as well as specialised hydraulic rock splitters
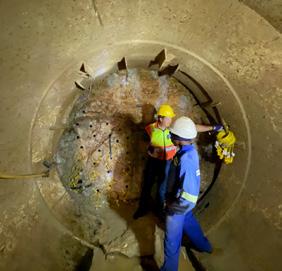
Pipe jacking launch pit
