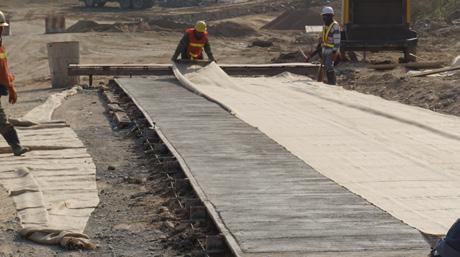
3 minute read
Methods and sealing materials for effective concrete curing
To start with, water curing entails the continuous or frequent application of water through immersion, ponding, sprays, steam or saturated coverings such as burlap or sand.
Fog spraying or sprinkling with nozzles or sprays provides excellent curing when the temperature is well above freezing. Furthermore, sprinkling is effective where water run-off to surrounding areas is not a concern. However, the possible disadvantages of sprinkling are the cost of the water and equipment, as well as potential damage to the latter under site conditions. Additionally, intermittent sprinkling is not suitable if the concrete dries between the wetting periods. Soaking hoses that discharge a slow trickle of water or a fine mist are useful, particularly on vertical or near-vertical surfaces. But the erosion of the surface should be prevented where water runs over the surface of the newly placed concrete.
Advertisement
Ponding or immersion
Ponding is only practical for flat slabs such as floors, culvert slabs, bridge decks, pavements, flat roofs or where a pond of water can be created by a berm or dike of earth or other material at the edge of the slab. The curing water should not be more than about 10°C cooler than the concrete, as surface temperature stresses could cause cracking.
A most effective method of water curing is total immersion of the concrete unit, but this is basically only possible with small precast units.
Burlap or hessian
Burlap, hessian and other coverings or absorbent material can be used to hold water on the surface, whether horizontal or vertical, but these materials must be free of high levels of substances (such as sugar or fertiliser) that may discolour the concrete. The burlap should also be thoroughly rinsed in water to remove any soluble substances.
The heavier the burlap, the more water it will hold, which will reduce the frequency of the wetting process. Burlap that has been treated to resist rot and fire should be considered when it is to be stored between jobs.
Double thickness of burlap or hessian, and lapping the strips by half-widths, will provide increased water retention and help prevent displacement during high wind and heavy rain.
Sand
Clean, wet sand has been effectively used for curing, especially on comparatively small sections of slab or floor. The sand should be free of particles larger than 25 mm and should not have excessive amounts of organic matter or other substances that could stain or damage the concrete.
Sand is particularly useful where operations must take place on the surface during the curing period as it will protect the surface against physical damage.
Sealing materials
Essential in achieving a quality end-result, sealing materials are sheets or membranes placed on concrete to reduce the loss of water through evaporation. Common sealing materials include plastic film and liquid membrane-forming curing compounds.
Plastic film
Plastic film is lightweight and available in various colours. However, it should be thick enough to prevent damage during use. White plastic provides substantial reflection of the sun’s rays, whereas black plastic has advantages in cold weather because of its heat absorption but should be avoided in warm weather in exterior placement.
The plastic film should be placed over the wet concrete surfaces as soon as possible without marking or damaging the surface, and should be placed so that it remains in contact with the surface during the specified curing period. If not adequately held in place, wind blowing under the film may create a wind tunnel effect, causing severe drying. For flat slabs, the film may be suspended over the concrete surface on battens until it can be placed on the surface without damage.
Liquid membrane-forming curing compounds
These compounds basically consist of waxes or resins together with solvents of high volatility at atmospheric temperatures. Pure resin and solvent compounds are more effective than those in emulsion. They can be applied by hand or power sprayer; if the project size warrants it, mechanical applications offering speed and uniformity of distribution should be considered.
Liquid membrane-forming compounds must be applied after finishing as soon as the free water on the surface has dispersed and no sheen is visible. The application must be done before the compound is absorbed into the concrete. Importantly, pigmented compounds must be adequately stirred to ensure even distribution.
Providing they are non-absorbent, the forms can be left in place and this is an acceptable method of sealing during curing. The key aspect to note though is that using steel forms left in place may result in high concrete temperature build-up in summer and very low temperatures in winter. A simple way to get around this is by releasing the forms slightly to allow a flow of water between the form and concrete to prevent such temperature extremes.
Observing these and other tried and tested techniques is the key to best-in-class concrete performance and sustainable infrastructure.
School Of Concrete Technology 2023 Training Courses
The Cement & Concrete SA School of Concrete Technology (SCT) will be running 10 standard courses in 2023. These range from basic topics such as an ‘Introduction to Concrete’ to more specialised training in various fields including ‘Concrete for Industrial Floors’ and ‘Concrete Road Design and Construction’. All the courses are presented live in Midrand, with some also scheduled for Durban and Cape Town. Continuing Professional Development (CPD) points are awarded for selected courses.
On an advanced level, the UK Institute of Concrete Technology’s two highly respected Concrete Technology and Construction courses – ‘General Principles’ and ‘Practical Application’ – as well as the pinnacle of concrete training, ‘Advanced Concrete Technology’, will continue to be offered in 2023.
The SCT 2023 Training Programme can be downloaded at www.cemcon-sa.org.za.