
4 minute read
Technicrete opens specialist plant in Polokwane
from IMIESA January 2022
by 3S Media
material, which is used to get final levels and clear, straight lines without any highs or lows.
Obstructions such as roots and projecting stones must be removed prior to the placement of the river sand ‘bedding’ layer. Poor preparation will be reflected in the finished surface and leave high corners that will create friction points and turbulence in the flowing water. “This is an important factor,” says Justin Kretzmar, technical sales and new product development engineer at Technicrete.
Advertisement
“The channel profile must be level in order for the water to flow smoothly and the blocks correctly interlocked in order for the Armorflex system to stay together and resist the uplift of individual blocks,” he explains.
A geotextile (woven or non-woven) is then placed on top of the levelled river sand layer. “This must extend wider than the block width of the channel and be continuous (or overlapped) along the length of channel. It is imperative that the geotextile extends into the embankment and is anchored and protected against water ingress below this layer. When flowing water gets under the geofabric, the channel has started to fail, and large sections could be washed away,” Kretzmar continues.
Another feature of Armorflex specifically relevant to this project is the capacity for water to flow vertically up or down through the openings in the blocks. Accordingly, the high levels of groundwater in this area will be able to seep up through the block voids and into the channel, where it will flow away. The geofabric resists migration of bedding sand when water flows up and block infill sand when water flows down, ensuring continued structural integrity of the layerworks.
Greening and maintenance
Among the fundamental advantages of Armorflex are the small sleeve openings inside each block that run perpendicular to the direction of water flow. These openings typically accommodate a 3.5 mm to 4.5 mm galvanised steel wire, threaded through the system after installation of the blocks. This wire assists with the overall stability of the system until the natural vegetation can grow and take root – typically one to two rainy seasons.
Maintenance is a simple annual process of ensuring that the vegetation growth is cut back to block level. Overgrowth will cause the settlement of silt, which then spirals into larger islands of vegetation and silt, eventually blocking free flow dynamics within the channel. It is important to note that the vegetation must not be removed, just cut down, as the roots assist in locking the blocks to the channel bed.
“For this project, with steep vertical sides to the channel, Technicrete’s earth-retaining Florawall blocks have been proposed for placement on top of the edge blocks to protect the embankment from eroding when stormwater volumes exceed the base flow of the channel,” says Kretzmar.
Florawall can be filled with concrete, soil or vegetation to improve the overall aesthetics, while still maintaining its earth-retaining function.
“We are very satisfied with the support from Justin and his technical team, who were on-site ensuring that all blocks were laid correctly and that the channel profile and levels were at the required ‘smoothness’,” adds Moruke.
“The delivery scheduling from Technicrete was spot on. Not only do we now have a strong, effective and long-lasting solution in place for stormwater control, but we have also upskilled many members of the surrounding communities,” Moruke concludes.
Technicrete opens specialist plant
in Polokwane
Technicrete has opened a second kerb manufacturing plant based in Roodepoort, Polokwane. This will enable Technicrete to meet the demand in and around Polokwane and from neighbouring provinces.
“The new Technicrete kerb plant is the first of its kind in the province. Many years ago, Technicrete invested in specialised machinery from the UK, becoming the first South African company to introduce pressed kerb technology into its kerb manufacturing processes,” says Christo van Zyl, sales and marketing director of Infrastructure Specialist Group (ISG). Technicrete and Rocla are ISG group companies.
Traditionally, kerbs are made using moulds in wet cast, which has a longer manufacturing time and requires curing time, before being recast for another batch. The pressed kerb technology involves the manufacturing of kerbs utilising machinery that have three moulds, enabling kerbs to be manufactured on one machine. This saves on production time and increases cost efficiencies.
“It is a quicker process while still meeting volume demands and maintaining a consistent quality of kerb,” adds Van Zyl.
Technicrete offers 11 ranges of kerbs for various applications. These range from barrier kerbs to semi-mountable/mountable kerbs and standard industrial offerings.
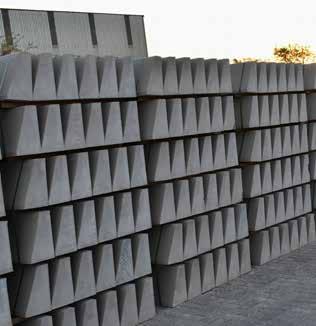
The pressed kerb manufacturing process entails the utilisation of specialist technology employing three moulds, which enables kerbs to be manufactured on one machine
PROFESSIONAL AFFILIATES

