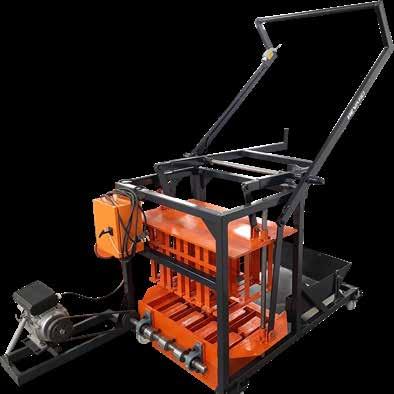
4 minute read
Affordable technology that builds brick businesses
from IMIESA July 2021
by 3S Media
Catering for SMME brick and block manufacturers requires an in-depth understanding of their production and end-user requirements. IMIESA speaks to Reyno van Rooyen, managing director, Revaro Concrete Equipment, about the company’s custom and off-the-shelf solutions.
What are some of your more popular brick- and blockmaking machines?
Advertisement
RvR Depending on each unique situation, we have machines suited for all types of SMME and start-up businesses. Very small start-ups, especially in rural areas, have had great success with our range of manual egglayers. Our range consists of the REL3-1, REL4-1, REL5-1 and REL8-1, priced between R20 000 to R110 000.
Among these is the REL4-1 manual egg-layer. This machine produces 14 stock bricks per drop and 3 780 bricks per ninehour shift. This is perfect for areas where electricity is scarce, as you have a manual, petrol or 220 V electric option, which does not require three-phase power. It is important to note that it is recommended to produce any bricks on a concrete slab, but they can also be produced on level ground. With interchangeable moulds, our clients have more opportunities to cater for different customers according to their needs. This one machine can create up to five jobs.
What’s the next step up for more established operations?
If you have a larger budget, our RS (Revaro Static) range of machines would be suitable, as they vary between R82 000 and R900 000. An example of one of our start-up machines is the Revaro RS5-2.5. This unit features an auto-mould feed with a dual-electric vibration motor to ensure the best compaction for high-quality concrete bricks, blocks and pavers. The RS5-2.5 is only complete with the addition of a 350 ℓ or 500 ℓ pan mixer, 6 m or 8 m conveyer belt to feed the concrete mixture, plus a wet block stacker. But Revaro offers a tailor-made solution that suits your budget and delivers on your production demands. This being said, we even supply the equipment needed to move larger quantities of bricks and aggregates like forklifts and loaders. From a manufacturing throughput perspective, we’d also recommend our plywood production pallets and brick trolleys to move the ready-stacked pallets with bricks to the curing area for drying. Our RS5-2.5 requires 8 to 10 people to run the full production line – from the aggregate transport to the packing of the complete bricks and blocks.
Revaro also offers a wide range of diesel generators to keep production running during loadshedding or power outages.
The REL4-1 manual egg-layer produces 14 stock bricks per drop and 3 780 bricks per nine-hour shift
Does Revaro offer tailor-made solutions for customers?
Yes, this is one of our core specialisations. Our in-house engineering team offers a machine manufacturing and customisation service. We offer standard moulds for hollow blocks, interlocking pavers, bevel pavers, inland and coastal maxi bricks, and stock bricks – and can always customise to your exact requirements.
What type of support and advice do you offer SMMEs?
Before we even start with the sales process, we go through the requirements for each machine with our client. We assess their situation, budget and surroundings, and advise on critical elements such as the size, layout, materials and other basics they will need to get their production line up and running. We help them with a costing sheet to realistically show the potential of each machine so that a well-informed decision can be made.
There are many aspects to site preparations needed for our machines to function optimally and these details are given to the client in advance as a pre-installation requirement checklist. Once this checklist is complete and signed off by the client or a site manager, as well as a third-party electrician arranged by the client, we are ready for installation. Revaro sends its highly trained and experienced technicians to go
The RS5-2.5 machine features an auto-mould feed with a dual-electric vibration motor to ensure the best compaction for high-quality concrete bricks, blocks and pavers. Complete with a 6 m or 8 m conveyor and mixer
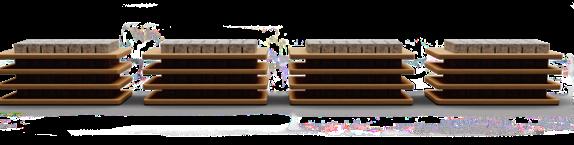
through the entire setup of each machine and plant.
Once the production line is set up, a soft start is done to calibrate and adjust the system; then the first hard start gets under way. From there, our technician spends the next few days – depending on the setup complexity – conducting in-depth training while running production, with the customer’s staff responsible for the day-to-day running of the machine. We also recommend that the owner or manager attends this training to ensure the skills handed over are performed as instructed. Examples include daily maintenance checks and the ability to troubleshoot small snags, thereby ensuring seamless productivity.
What happens after the sale and installation?
Our service doesn’t end with commissioning and training after installation. We have seven field services support teams that are available to assist customers if the need arises. Our lead time, depending on where the site is located, is within 48 hours and we send our best technical minds to solve any problem. We also stock and manufacture all the parts needed to avoid any delays and downtime.
Every machine we sell goes through a rigorous quality assurance inspection at our factory, and again at the customer’s site to verify that the commissioning is perfect. From there, we’re always on standby to assist with any advice and to help grow our SMME start-ups into leading brick and block suppliers to the industry.
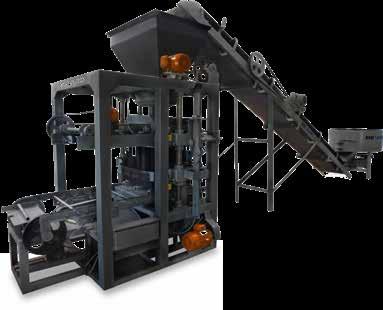
