
2 minute read
Leak detection for renewable energy
from IMIESA July 2023
by 3S Media
Pipeline gas can consist of various renewable and non-renewable gases. There has been a massive uptake in natural gas consumption, and an increasing need for leak detection systems. The reliable and timely detection of gas leaks is critical to ensure the reliability of the natural gas infrastructure.
leak rates are typically 0.5% and below. Leak detection time is in seconds and confirmation is within minutes.
Advertisement
Case studies
The leak detection system was installed on a power-to-gas project in Germany, which was the world’s first demonstration plant for storing wind energy in the natural gas grid. PipePatrol was selected due to its ability to measure a product even in small leak quantities.
Some pipelines transport 100% hydrogen while others a blend with natural gas. CO2 can be transported as gas, liquid or in supercritical state. Therefore, the leak detection system needs to be able to work with these different mixtures and phases.
This is a problem for traditional leak detection systems. Negative pressure wave leak detection systems are affected due to damping in gas. Classical statistical systems are affected due to compressibility and linepack changes. This leads to long detection times or high thresholds. The systems react with a loss of sensitivity or, in the worst case, with false alarms.
Systems based on the real-time transient model (RTTM) try to consider all the different products and pipeline properties in its calculations. However there will be false results if the fluid cannot be accurately modelled by the system.
PipePatrol – E-RTTM
KROHNE’s PipePatrol uses extended real-time transient model (E-RTTM) technology that has signature analysis technology to make the system less sensitive against inaccuracies in RTTM calculations. Therfore, it can cope with challenging pipeline conditions and product parameters or mixtures like hydrogen blends.
PipePatrol creates a virtual image of a pipeline and uses standard process instrumentation for flow, temperature and pressure measurements. The hydraulic profiles along the virtual pipeline are calculated from the measured pressure and temperature values. The model compares the calculated flow values with the actual values from the flow meters. If the model detects a discrepancy, the leak signature analysis module determines whether it was caused by changing pipeline operation, an instrument error or a leak. The technology is used for liquid, gas and slurry applications. The smallest detectable
Process scheme: leak detection on a CO 2 pipeline from an LNG plant
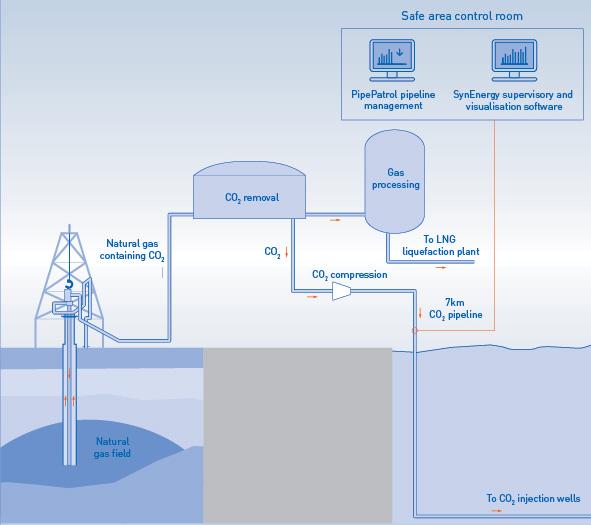
On another project in Australia, PipePatrol was used on a 7 km long pipeline that transports CO2 from the LNG liquefaction plant to the CO2 injection wells. This involved unique conditions, such as the properties of CO2 in a supercritical phase and flow measurements done by orifice plates with limited rangeability. Here, PipePatrol provides timely and accurate leak information for the pipeline segments between the LNG plant and drill centres.
KROHNE – a manufacturer of measuring technology and established supplier of systems to the pipeline industry – has more than 35 years of experience in leak detection and localisation systems.