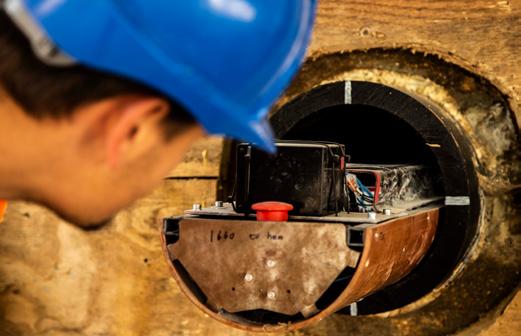
6 minute read
Can a new approach to tunnelling unlock underground construction potential?
from IMIESA June 2023
by 3S Media
As
The infrastructure in and around cities, including transportation links to better connect rural communities, is critical to successfully incorporating larger populations and driving socio-economic progress.
Advertisement
By Patrick Lane-Nott*
Inevitably, this demands the ongoing construction of new structures and buildings – from residential accommodation and healthcare facilities to the roads and railway lines. However, many cities and urban conurbations are already struggling to find hyperTunnel, the British technology company innovating underground construction, presents the world’s first entirely robot-constructed underground structure, built at the company’s R&D facility in the North Hampshire Downs the space needed to accommodate these additional building requirements. Indeed, while taller and taller buildings have become a common feature of skylines, there is only a finite amount of land that can be developed. One means of addressing this challenge is to look downwards and build underground. As a subsegment of the construction industry, tunnelling is already big business and set to expand markedly over the course of the current decade. In 2021, globally the sector was worth US$88.6 billion (R1.61 trillion) – by 2027, it is predicted to expand by more than 50% to almost $136 billion (R2.47 trillion).
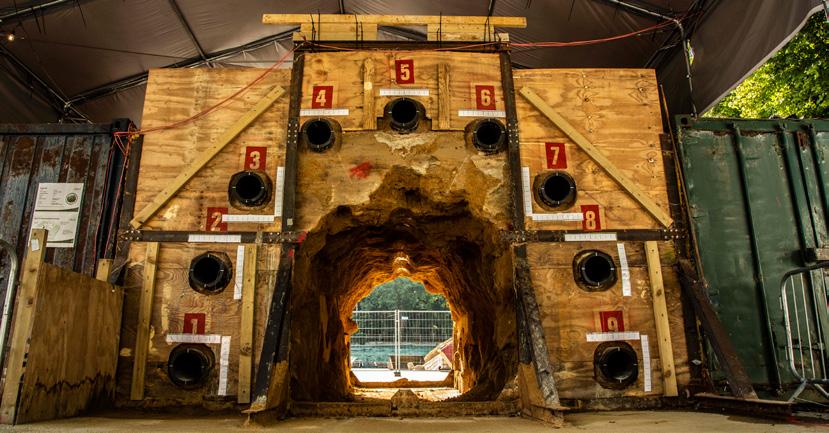
In South Africa, construction underground has been an important practice for the development of water transfer schemes and metro rail extensions, as well as enabling rapid access to mining operations to boost productivity of the sector.
Using swarm construction methods according to a digital twin of the tunnel, a fleet of hyperBot robots enters the ground via an arch of HDPE pipes. Once inside, they 3D-print the tunnel shell by deploying construction material directly into the ground
While the importance of underground construction projects has long been acknowledged by the South African government, there are several challenges to achieving sustainable, safe, cost-efficient and timely project outcomes in the region. These include issues relating to productivity such as geological constraints and challenges associated with tunnelling through hard rock terrains.

Rather than digging through the ground with a cylindrical boring machine or using a traditional drill-and-blast technique, the hyperTunnel method installs a network of HDPE pipes to provide access to the whole tunnel length so that a swarm of multifunction robots can 3D-print the tunnel
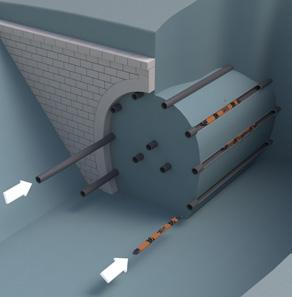
By removing much of the risk and pain related to large-scale underground infrastructure projects, such advances promise to further boost what is an already booming sector that is only going to become more important in the decades ahead.
For well over a century, approaches to underground construction have broadly remained the same, meaning conventional practice continues to be burdened with risk, complexity and cost, as well as a heavy carbon footprint.
However, this could be about to change. A new method of underground construction is gaining traction – one that leverages the power of swarm robotics and in-situ construction to transform the traditional tunnel boring process.
Unlocking an array of benefits
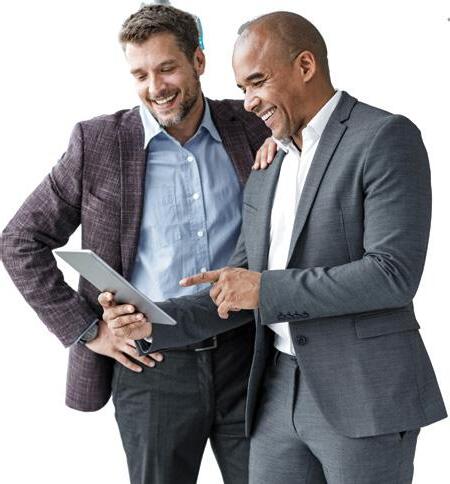
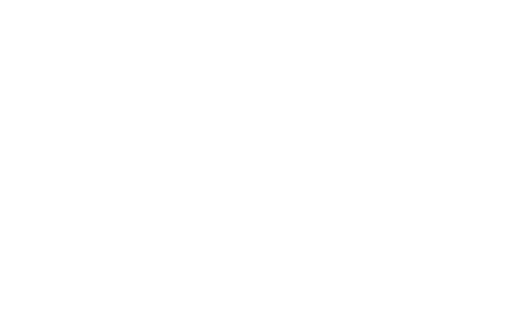
First, pilot bores are drilled and lined, and robots sent inside to inspect the geology. Core samples are taken and the geology is scanned using ground-penetrating radar (GPR). The result is a near-perfect understanding of the entire tunnel length’s geology.
Using this data, a virtual model of the tunnel structure is developed: the digital twin. With AI and machine learning, the optimum build schedule can be designed to create a sound structure in the geology.
Once the structure profile is defined, a swarm of bots is sent into the lined bores to visit planned locations in order to drill and deploy chemistry according to the AI-generated design. Thousands of robots will be used, all controlled using swarm technology to 3D-print the tunnel in much the same way that bees build a hive or termites build a mound.
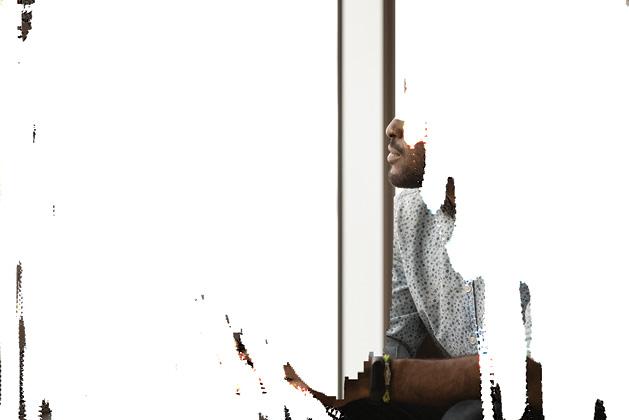
The ‘bots carve precise chambers in the geology and these voids are then filled with suitable construction material. The cast-insitu blocks interlock to create a permanent structure, block by block. The initial survey robots come back to inspect the construction, ensuring that the chemical has spread evenly and precisely matches the digital twin design. The tunnel walls are prepared for final use, leaving a smart structure that can be monitored and maintained throughout its life.
Strategic gains
This method has several key advantages. For example, costs are greatly reduced throughout the process, compared to conventional tunnel boring machines and drill and blast techniques. These savings cover labour and consumables, to the project cost gain of a shorter build duration.
By using thousands of robots running in parallel, many processes can be performed simultaneously, working throughout the structure all at the same time. Further, multiple robots can operate in each pipe as they are able to pass each other as they shuttle back and forth. This means the construction duration is determined not by a project’s physical size but by the number of robots deployed.
Several environmental benefits can also be realised. First, less energy, water, raw and composite materials are required versus conventional tunnel boring techniques. In addition, worksites are smaller and better suited to urban environments, while the spoil from the tunnel interior is uncontaminated and therefore easier to use locally without processing. With South Africa committed to reaching net zero by 2050, sustainable
The hyperTunnel team has developed its hyperBot robots in-house at its Basingstoke, UK, headquarters, and outdoor learning environment (the hOLE) and Geolab in the North Hampshire Downs construction techniques will no doubt have their role to play if this ambition is to be realised.

Crucially, in-situ construction using robots is safer because the structure is sound before a human enters it. In terms of project risk –another factor affecting cost – the construction design is more accurate due to the superior amount of data gathered. Geological certainty provides full knowledge of the tunnel path. Therefore, it’s much less risky.
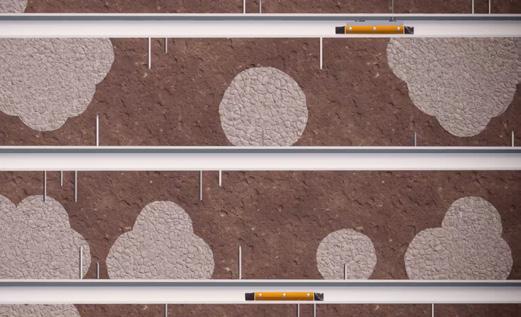
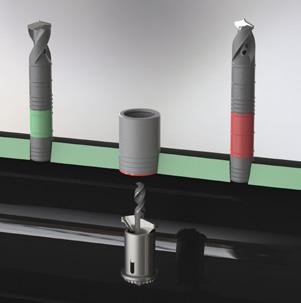
In-situ automated construction can also be used to extend and maintain existing underground assets with minimal disruption. The robots simply gain access via the same network of pipes to carry out their work. This means that, in many cases, roads or railways do not have to be closed. It is also an ideal solution for when direct access from above ground is difficult, which is often the case in urban areas.
From concept to deployment into the real world
At hyperTunnel, we are determined to bring this new vision of construction to life. In 2022, we revealed the world’s first entirely robotconstructed underground structure at our R&D facility in the UK. This has been delivered as part of a project with Network Rail, the body responsible for maintaining the UK rail infrastructure, which is eager to explore technologies that are key to low-disruption tunnel repairs. We are now currently surveying a site for Network Rail to populate a digital twin in planning for repair works.
Meanwhile, earlier this year, hyperTunnel received funding from Global Centre of Rail Excellence (GCRE) in Wales to carry out a feasibility study into building an underpass at its site using their approach. If the project progresses successfully, hyperTunnel’s system will be tested on a real site in the form of a 10 m long pedestrian-sized tunnel built under GCRE’s test track, with the railway able to remain open throughout.
Alongside these advances, development of the fleet of hyperBots continues to gather momentum. This is being turbocharged by the backing of a grant from the European Innovation Council, with the key objective being to demonstrate swarm robot behaviour in an operational environment within the next two years.
Conclusion
Underground construction and repair, be it for transportation infrastructure, access to mines or many other applications in between, will play an important role in South Africa’s onward development.
As the need to accommodate growing populations and improve productivity of major economic sectors intensifies, new methods that deliver enhanced speed, safety, sustainability and value for money will be sought after. Tunnel boring has, without doubt, delivered tremendous advances by enabling underground construction – the time has come for the next generation of construction technologies to emerge.
*Director of Engineering at hyperTunnel
Swarms of hyperBots are sent into each bore to build the structural shell, deploying an additive manufacturing process, similar to 3D printing provides the interface to host, manage and broadcast live as well as on-demand webinars.
87% of marketing professionals use video as a successful marketing tool.
Marketers making use of video get 66% more qualified leads per year.
Video engages users for longer on a website. The average user spends 88% more time on a website with video content.
Our pla�orm ensures the highest quality video and audio technology. This ensures flawless digital broadcas�ng by using enterprise-grade streaming solu�ons.
Book your webinar today and participate in robust thought-leadership panel discussions and anchor desk interviews with captains of industry.
Webinars are ideal marke�ng pla�orms for product launches, training events and industry announcements. Our pla�orm ensures the highest quality video and audio technology.
Novus Print (Pty) Ltd t/a 3S Media is a registered member of National Treasury’s Central Supplier Database for Government.
Supplier Number: MAAA0016423
Unique Registration Ref Number: FFA60BC9-37E6-4596-89D9-A00025D4C50F