
6 minute read
The vital importance of laboratory concrete testing
from IMIESA March 2022
by 3S Media
All the raw materials used to produce concrete are variable. And the readymix supplier must absorb these variances in his production process to produce concrete that meets the specification. This is inherently the risk that readymix suppliers will carry, making testing a vital part of the quality validation process. By Jacques Smith, Pr Eng*
The first party that needs to know whether the readymix supplier is producing concrete within the strength requirement is the supplier himself. To that end, he will take samples normally at the plant from the back of the truck to have them tested as process control samples. It is up to the client to take samples for cube-making and testing for acceptance control for quality assurance purposes.
Advertisement
These two types of testing are very similar, yet there are fundamental differences between the two. The main difference in testing is the sampling that is done from the back of the truck at the plant for process control testing, whereas on-site sampling is done from a moving stream after the first 15% and before the last 15% of concrete has been offloaded for acceptance control for quality assurance testing (SANS 5878 para. 12.2).
The criteria for assessing these results are then also different. Normally, process control cubes are not (but may be in certain circumstances) accepted as acceptance control testing for quality assurance.
Potential problems
The following things can go wrong with the testing (of perfectly good concrete): 1. Process control cubes are too high. 2. Process control cubes are too low. 3. Acceptance control cubes are too high. 4. Acceptance control cubes are too low. In number 1 above, this would give a false sense of security and, even unknowingly, substandard concrete may be produced that could result in a failure and huge claim.
In number 2 above, the readymix supplier will increase cement contents because he is scared of a claim. The customer will be very happy with this concrete, which will give higher strengths and even earlier strengths, but this comes at the readymix supplier’s expense.
In number 3 above, it is great for everyone, until something goes wrong and cores are requested. This could then result in huge failures.
In number 4 above, the specification rules that the engineer may call for the process control test results and will then call for cores to be drilled, if the situation cannot be resolved. Ultimately, the concrete will be accepted but with mistrust and unhappiness due to delays and penalties – and the additional cost of the drilling and testing of cores. The readymix supplier will probably increase cement contents to prevent possible failures.
Concrete laboratory testing
Due to our involvement in disputes and court cases, Go Consult has been asked on a number of occasions to investigate the state of testing at a laboratory. On one occasion, eight of the eleven laboratories visited in a sample run were doing testing commercially at the time.
Not one of the laboratories included in this article was accredited by Sanas (the South African National Accreditation Systems) for concrete testing. Sanas accreditation would imply that they have a management system in place to ensure the proper documentation of everything they do, plus systems in place to ensure a repeatable test that will reproduce a similar test result every time.
Incorrect testing
At every laboratory, there were signs of incorrect crushing of cubes with tensile cracks and the cubes only being crushed on one side, with the other side failing in tension. This error will definitely give a lower result and create the impression that the concrete is of substandard quality.
This, of course, would raise the following logical questions (as the advocate would certainly ask in court): How many of the cubes were tested like that? Which ones were they and what would the effect of that be? This should result in a rejection of all test results, as we know that some results are lower, but we do not know which and we do not know by how much, so we cannot use any of these results. We, therefore, might have to drill cores to determine the
strength of the concrete. These are often incorrectly done and interpreted, which has led to instructions to break out perfectly fine concrete on numerous occasions.
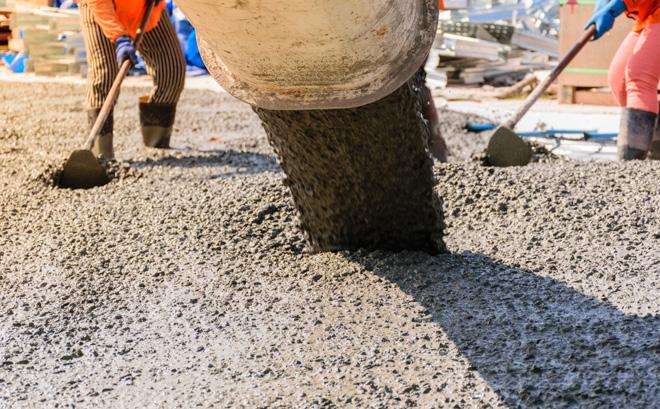
So, what can readymix suppliers/ contractors do?
The first step is to visit the laboratory that is testing for you and check the following items. The fact that you are checking should encourage the lab to ensure their methods and systems are up to standard – or so one hopes.
ITEMS TO BE CHECKED
Making
- Is every cube properly marked on the side (paper labels tend to come loose in the water)? - Are the edges sharp? - Are the cube moulds square? - Are they oiled? - Is each cube tamped enough? (25 times for two layers on 100 mm cubes and at least 45 times for three layers on 150 mm cubes.) - Is there a paper label on each cube with at least some reference number on it? - Do the two halves of each cube mould correspond (see the stamped marks on each cube)? - Do they have a slump rod or vibrating table to compact the cubes with? - Do they understand that no vibration is allowed after the cubes have been made?
Curing
- The curing temperature in the curing tank is often not correct. It should be between 22-24˚C. - Is the curing tank heating system always on and plugged in (not only in the day when the generator is working)? The specification states that site cubes that have to stay on-site for an extended period should be covered and then placed in water (at the above temperature). - Is there a pump stirring the water constantly to prevent hot spots due to heat of hydration of the cement? (This is not a requirement of the test method.) - Are all of the cubes constantly submerged in the water?
Crushing
- Is there a calibration certificate and is it less than 18 months old? And was it done by a Sanas-accredited organisation for press calibrations? - Are there locating pins on the platens to ensure that the cube is placed right in the centre between the platens? (Just marks – circles or lines – on the platens alone too often leave it to the operator to locate cubes and they do not do it correctly.) - Did they ensure that two faces formed by the cube mould were against the platens while crushing? - Is the top platen loose to swivel? - Is the machine clean? - Has the operator been trained to operate the machine? - Has the loading rate (N/s) been adjusted for the type of test? (It should be different for different sizes of cubes and even cores.) Should a dispute arise, Go Consult can assist to settle this and put it in perspective. Go Consult is also available to do an audit at the laboratory to ensure proper test results.
*Managing member and director, Go Consult

THE SCHOOL OF CONCRETE TECHNOLOGY
Professional online and classroom-based education to accelerate your career in concrete technology
