
5 minute read
Updated specifications are needed to meet cement innovation
from IMIESA May 2021
by 3S Media
Integrated Solutions & Innovation, Lafarge South Africa South Africa cannot afford to rebuild concrete structures every few years because they were not constructed correctly the first time.
By Kirsten Kelly
Advertisement
Roelof Jacobs, head: Technical Sales and Innovation at Lafarge Southern Africa, believes that greater thought needs to be given when specifying cement and concrete products.
“Outdated cement and concrete specifications are still used. We still see tenders/specifications requesting outdated cements like PC15, which was produced in the 1980s.”
He adds that if the specifications for cement are correct, there is often a request for as little extension as possible.
“The reality is that there needs to be a fair amount of fly ash or slag to improve the durability of structures. Furthermore, there is a significant environmental advantage to using SCMs (supplementary cementitious materials). Updated cement and concrete specifications will likely lead to more durable structures that leave a smaller environmental impact.”
Ten to twenty years ago, slag and fly were used to make cement cheaper, but presently this is not always the case due to transport costs. It often costs more to produce cement with a high fly ash content than to produce cement without it. But even with the increased cost, the durability and environmental benefits of using SCMs are significant.
“Fly ash particles, for example, are smaller than cement particles, plugging any gaps. Once cement starts to hydrate, fly ash starts to hydrate and creates a gel, producing a denser paste matrix. Therefore, fewer harmful chemicals can penetrate the concrete. Like fly ash, slag can also be used to create a denser matrix, but it is usually not as fine or as readily available as fly ash,” says Jacobs.
Sulf8CEM
Sulf8CEM also assists with the durability of concrete structures. As the only registered sulfate-resistant cement in South Africa, Sulf8CEM is an ideal solution in aggressive environments (like sewage plants).
Sulfates are said to ‘attack’ concrete because they can permeate the surface layers in solution with water, and react with calcium hydroxide and tricalcium aluminate in the cement paste – making it weak and brittle.
The cement paste starts to fall away, exposing aggregates that then also start to fall away As the only registered sulfateand the concrete structure begins resistant cement in the country, Sulf8CEM is an ideal solution in to deteriorate. aggressive environments like sewage plants
Sulf8CEM is a low-heat (LH), sulfate-resistant (SR) cement that Sustainability is formulated from Portland clinker that On the environmental side, meets the CA requirement and over 36% launching a new range of eco-cements.
It has been certified to conform to the latest applicable South African and European standards (SANS 50197-1 and EN 197-1) for a CEM IV/B-V 42,5N LH SR.
Sustainability
On the environmental side, Lafarge is launching a new range of eco-cements. Lafarge is the first global building materials company to sign the Unite Nations Global Compact’s Business Ambition for 1.5°C initiative, with a 2030 SBTi-verified (Science Based Targets initiative) action plan. Lafarge plans to reach 475 kg net
industry need to change and make more conscious decisions to minimise our impact on the environment. South Africa is lagging with regard to carbon reduction initiatives, and we need to look at successes in other countries and implement them here.
There needs to be far more collaboration between industry players and government in order to achieve success,” says Jacobs.
Jacobs further believes that a mindset shift should also be applied to the construction industry’s focus on 28-day strengths.
“In our industry, the 28-day strength concept is like a religion. But why, for example, push for a structure to reach 30 MPa in 28 days when the structure only requires the strength after 56 days due to construction plans? By designing a structure to reach 30 MPa in 56 instead of 28 days, one can not only save on costs but also have a greener product – as less cement is used – and there is an opportunity to use cement with higher amounts of SCMs, which typically increases strengths over a longer period of time.”
Skills
Concrete technologists are responsible for most concrete designs and quality control in construction. In the past, most companies had these skills in-house; however, they now rely on external consultants. Therefore, there are fewer technical people in the industry. “We need good concrete technologists and concrete foremen. And while I have been encouraged by a few young concrete specialists I have worked with recently, there are simply not enough of them,” explains Jacobs.
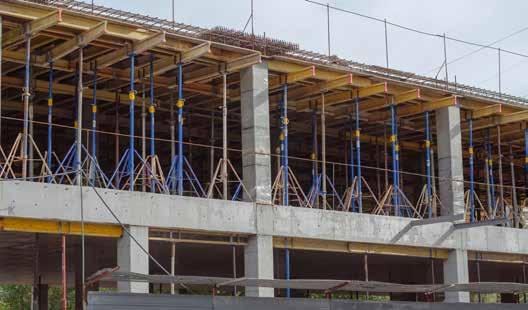
Oris software
In another effort to achieve its carbon neutral status in 2050, Lafarge has developed a software program that
CO 2 per tonne of cementitious material (net CO 2 t.cem) by 2030 and to be carbon neutral by 2050. The company focuses on the whole life cycle of its products: from their manufacture, to their placement and the lifespan of the concrete structures they create.
“Society has to have a mindset shift, where higher extended and more activated cements that are ‘greener’ alternatives to traditional cement are more commonly purchased.
We as an focuses on road design and optimisation, taking the life cycle of the project into account. This is because road design has an impact on up to 60% of the cost of a road project and up to 85% of its overall greenhouse gas emissions.
The software helps road professionals to make data-driven decisions by proposing multiple pavement designs and sourcing options. It also calculates the carbon emissions of the construction of the project and through the life of the road.
This was initially an internal Lafarge development, with IBM, but it has been opened to the industry in a bid to create greater collaboration in reducing carbon emissions.
SONA
Like all companies within the construction industry, there is very little insight as to when or how government’s allocated R226.1 billion (mentioned in President Ramaphosa’s State of the Nation Address) will be spent.
“As an industry, we need to be prepared to supply materials and technologies once these projects come online – but we are all in the dark at the moment,” states Jacobs. He adds that he is, however, encouraged by Ramaphosa’s emphasis on localisation.
“While Lafarge is a global company, and we have access to world-class innovations and support, we are very much a South African company in that we employ South Africans, manufacture locally, understand the South African construction industry, and have invested into the South African economy.”