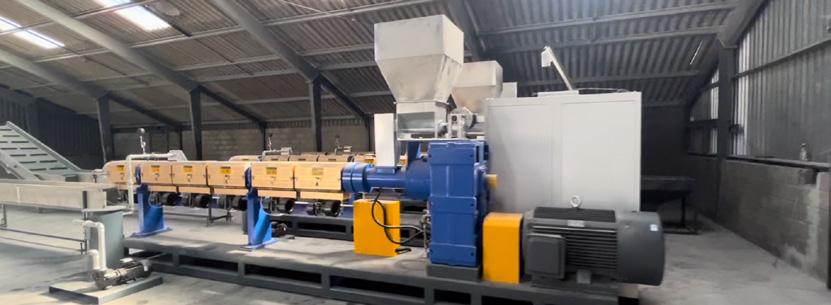
5 minute read
The concrete solution to plastic waste
from IMIESA May 2023
by 3S Media
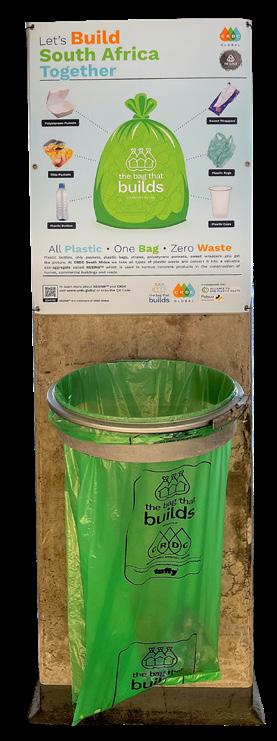
The scale of South Africa’s plastic pollution problem came to the fore during the April 2022 floods in KwaZulu-Natal, when mountains of waste ended up on Durban’s beaches. It’s a worldwide problem and one being addressed across the globe by a multitude of stakeholders and organisations, ranging from beach clean-ups to manufactured interventions.
Advertisement
By Alastair Currie
CRDC’s ‘The Bag that Builds’ programme is one of the key sources of its production waste materials
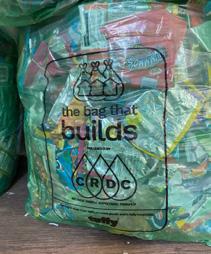
CRDC’s focus from the onset has been on protecting the environment by creating a productive use for non-recyclable plastic waste (resins 1 through 7) that would otherwise be incinerated, disposed of at landfills or end up as general litter, threatening our rivers and oceans. Worldwide, CRDC research indicates that only 9.5% of plastic waste is being recycled. In South Africa, the figure is around 21% out of an estimated 1.5 million tonnes produced annually, which underscores the importance of CRDC’s initiative.
Foremost among the plastic waste pioneers is the Center for Regenerative Design & Collaboration (CRDC Global), founded in 2018 by Donald Thomson initially as a small non-profit community outreach programme in a fishing village in Costa Rica that has subsequently spread its wings to become a construction materials innovator. Today, CRDC Global has operations in Australia, Costa Rica, Hong Kong, Mexico, New Zealand, Samoa, the UK, USA and South Africa – with the latter operation established in 2019.
“Their breakthrough is RESIN8™, a patented lightweight plastic eco-aggregate for concrete, which is rapidly gaining ground in the world of construction,” says Abraham Avenant, CEO, CRDC South Africa (CRDC SA). “Based on a CRDC study, if the world as a whole were to use just 2.8% RESIN8 in all concrete products, the planet’s plastic pollution problem could be solved.”
A seasoned civil engineer and business leader, Avenant immediately saw the benefits for the local market. “The whole concept of sourcing the materials for RESIN8 is what makes the process unique,
CRDC SA’s RESIN8 manufacturing plant in Blackheath, Cape Town
CRDC Global’s focus from the onset has been on protecting the environment by creating a productive use for non-recyclable plastic waste (resins 1 through 7) that would otherwise be incinerated, sent to landfill or end up as general litter because it entails partnering with communities, general industry, waste companies, waste pickers and municipalities to find a very viable alternative. Along the way, the environment wins, jobs are created and cost-effective structures are built,” he explains.
“Plus, the collection process is greatly simplified by the fact that our solution accepts all types of mixed or dirty plastic waste, so separation at source is not required. The one proviso is that our manufacturing process can absorb up to 10% contamination,” Avenant continues.
Ideal for structural and nonstructural applications
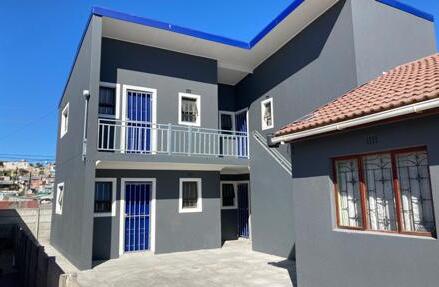
Virtually indistinguishable from standard construction aggregates, RESIN8 is designed to be used as a natural aggregate replacement in all structural and non-structural concrete products. Typically, 2% to 10% of natural aggregate can be replaced with RESIN8 in structural concrete applications and up to 50% in non-structural applications.
Significantly, concrete formed using RESIN8 exceeds ASTM international standards, as well as SANS standards. Another plus is that concrete containing RESIN8 can be safely crushed and recycled without any associated environmental risk – an example being microplastic contamination.
The manufacturing process is waterless and begins with the shredding of the waste plastic. The mixed waste is then pre-conditioned with proprietary mineral additives to eliminate all pathogens and odours. Then during the heat extrusion phase, the pre-treated mixture melts and becomes a completely inert construction material. The bulk RESIN8 is then granulated
RESIN8 is granulated into the size, shape and gradation required by standard concrete mix designs for both precast and cast-in-situ (wet mix) applications
This M190 concrete block looks identical to a standard product made from cement and stone aggregate; however, some 10% of the standard aggregate has been replaced with RESIN8 eco-aggregate without compromising the block’s performance in any way into the size, shape and gradation required by standard concrete mix designs for both precast and cast-in-situ (wet mix) applications.
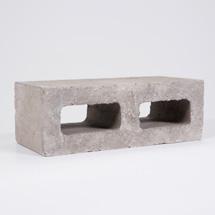
“The rough and open-cell structure of RESIN8, combined with mineral additives, enhances both the mechanical and chemical adhesion with the cement paste,” Avenant explains. “This results in exceptional performance properties in terms of compressive strength – equally comparable with standard concrete – along with maintained fire resistance, best-in-class thermal values and acoustic suppression.
“A further plus is that concrete made using RESIN8 is lighter than standard concrete, with obvious benefits in terms of product transport and design, due to the fact that RESIN8 is approximately 3.5 times lighter than natural aggregates. So, as an alternative building system, it ticks all the right boxes. RESIN8 is green and highly cost-effective.”
Pilot phase
In 2020, CRDC SA set up a pilot plant in Blackheath, Cape Town, in preparation for its commercial launch, with over 100 different plastic waste streams tested in collaboration with various waste management and FMCG entities. The global business case has already been proven – backed by more than US$2 million (R38.2 million) worth of research and development by CRDC Global – but South African companies new to the RESIN8 concept still needed to be convinced.
The waste collected during this engagement enabled the production of more than 85 t of RESIN8 (up to 500 kg/day being produced by the pilot plant), which was supplied to local concrete product manufacturers and universities for trial product development and analysis.
These tests were highly successful. Concrete products such as kerbs, channels, bricks, blocks, pavers, pipes and toilet structures were manufactured within the requirements of the various SANS and ASTM specifications. RESIN8 was also successfully tested for castin-situ applications such as foundations and floor slabs.
Bitprop, a Western Cape-based affordable housing developer, was one of the early RESIN8 adopters, applying a combination of precast and cast-in-situ applications for the construction of its two-storey buildings in township communities designed to accommodate six 18 m2 units.
CRDC SA specified a 2.5% RESIN8 composition for the foundations and ground floor slabs, while the 14 MPa masonry bricks have a 10% component. For each 108 m2 building, that equates to some 6.2 t of plastic being absorbed.
“Our engagement has extended to include all built environment professionals in the public and private sector – ranging from architects and consulting engineers to housing practitioners and road and stormwater specialists,” Avenant explains.
Funding drive and production ramp-up
Positive market feedback subsequently led to CRDC SA securing funding for the upscaling of the pilot facility to a full-scale RESIN8 plant during 2021. Some 70% of the capex and opex has been funded by Polyco, and the remaining 30% by Alliance to End Plastic Waste (AEPW) – a global nonprofit organisation.
“We have now received our waste management licence and, with the acquisition of the required equipment, we expect to start production in June 2023, ramping up progressively as market demand increases,” says Avenant.
By October 2023, the target is to process some 610 t/month of plastic waste, equating to around 725 t of RESIN8. The factory setup is designed so that production can easily be doubled by adding additional extruders.
The Bag that Builds
In parallel, the pilot phase provided the ideal opportunity to introduce CRDC’s ‘The Bag that Builds’ (TBTB) programme, a social initiative that also provides an income.
“The concept is simple and a key part of the RESIN8 concept globally, where everyone at all levels of society can make a difference, alongside the sustainable waste streams being supplied by industry and municipalities. In terms of the TBTB programme, anyone can fill our recycled plastic bags with all types of plastic waste, which is especially significant for waste pickers that at present cherry-pick saleable recyclable waste and randomly dispose of non-saleable, non-recyclable waste in the general environment,” Avenant explains, adding that general households and schools are being incentivised to participate in a pilot programme funded by AEPW.
In collaboration with various waste collection partners, CRDC has so far managed to incorporate TBTB into 18 collection hubs across the Cape Peninsula. This has enabled CRDC to collect 85 t (53 000 bags) of plastic waste through TBTB since November 2022.
“Going forward, we see huge potential for RESIN8 in the South African construction sector, and for TBTB to be rolled out nationally, supported by the manufacturing industry, municipalities and general society, to eradicate non-recyclable plastics from our environment and create a market for an eco-aggregate that adds real value from a sustainability and job creation perspective,” Avenant concludes.