
5 minute read
The evolution of the student pod
from IMIESA Nov/Dec 2020
by 3S Media
Nkosi Johnson House, Stellenbosch University, The evolution Tygerberg Campus South of the Africa’s backlog in student housing, student podestimated to be around 300 000 beds, presents new opportunities for Sean Kenealy, director, innovative building technologies (IBTs) that STAG African can accelerate the process without compromising on quality and the living experience. Spearheading the change is STAG African, a multidisciplinary leader in student accommodation. By Alastair Currie
The starting point for any student housing project is the cost of construction and how much clients can afford to spend. Other key considerations include the future operational and facilities maintenance expenses, plus the return on investment for property owners. “We don’t introduce a product or building system without first researching what the market can afford,” explains Sean Kenealy, director and professional architect, STAG African. “Our starting and end point is to ensure absolute efficiency in terms of the design, technology and methodology, whether the client opts for a
Advertisement
FIGURE 1 Permeate flow per element conventional concrete-framed brick and mortar structure, or an IBT prefabricated approach,” he continues, adding that STAG African is a signatory to the African Green Campus Initiative.
Worldwide, the demand for IBT systems is growing, largely due to their lower cost and faster build times. “The scale and scope of the project will best determine the construction technique; however, in the case of both conventional and IBT, green technologies still apply,” adds Kenealy.
Within the IBT space, STAG African has gained extensive experience over the past decade in executing light steel frame buildings (LSFBs). This has had a major influence on the direction of its research and development (R&D) initiatives on student pod accommodation designs.
Since many components of these systems are made to order in the factory, the key advantage of LSFBs is a major saving on construction waste

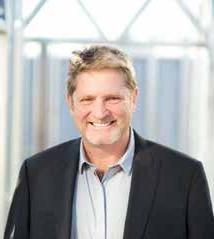
– typically less than 0.1% of building bulk. That compares to some 25% for traditional brick and mortar. Being made of steel, LSFBs are also recyclable.
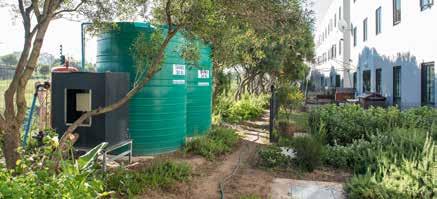
Facilities management
However, the construction cost is just one part of the equation. Institutional building administrators also need to know what it costs per month per bed to run student residences.
When STAG African designs its projects, the future operating cost projections are incorporated into the model. That has a direct bearing on the materials and products specified during construction, as well as the energyefficient technologies employed. Examples of the latter include STAG African’s specification of alternative hot water heating systems. For recent projects, these have included heat pumps. Now, the company is investigating the potential of inline water heating, which only activates on demand, passing on electricity savings.
“Including the facilities management team at the initial project planning stage is a crucial part of optimising the overall life-cycle costing,” Kenealy explains.
Stellenbosch University
LSFB milestones for STAG African include
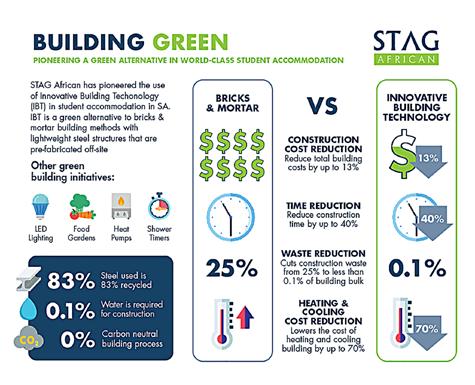
The Nkosi Johnson House project has a facility to recycle greywater
the development of three residences for Stellenbosch University. The most recent is Nkosi Johnson House, completed in 2017, which received an EDGE green building rating. An innovation of the World Bank Group’s International Finance Corporation, EDGE stands for ‘Excellence in Design for Greater Efficiencies’ and is a highly soughtafter accolade.
“Our design for Nkosi Johnson House incorporates a host of green features. These encompass the use of natural ventilation, solar energy, greywater reuse, rainwater harvesting, low-flow water fittings, and LED lighting, with the LSFB cladding panels manufactured from recycled materials,” Kenealy explains. Each self-contained pod within this three-storey building caters for eight separate, singleoccupancy bedrooms.
By ruling out the use of mechanical ventilation, and optimising thermal efficiencies, the heating and cooling costs have been reduced by almost 70%. Then, from a facilities management perspective, all services are mounted externally to maximise ease of maintenance.
Precast pods
While LSFBs clearly have their advantages, STAG African’s R&D team has been investigating even more affordable and efficient IBT alternatives for pod designs. Working with Cape Town-based manufacturer Concretex has led to the development of a lightweight, cellular, concrete-wall-panel system.
Each 150 mm thick wall panel is formed in a mould under strict quality control conditions, with the final product incorporating electrical conduits and plumbing connections according to specific building design layouts.
“We’ve built a prototype two-storey building using the wall technology, so we know it works in terms of concept and assembly,” says Kenealy.
The ground-floor surface bed is established conventionally by forming a concrete slab and brickwork foundation wall. The panels are then installed in their planned sequence, without the need for any scaffolding on-site.
Proof of concept
Having brainstormed and refined the optimal building methodology with the contractor, structural engineer and its technology partner, STAG African is now moving to the proof of concept stage.
This will entail the construction of a 24-bed, three-storey building in Rosebank, Cape Town, which will aim to attract University of Cape Town students. Each floor will comprise one self-contained pod, comprising eight doubleoccupancy beds. Construction is scheduled to commence in January 2021.
STAG African will be using the same contractor currently employed on its 2 050-bed student accommodation village project for the University of Fort Hare in Alice. This is believed to be the largest student housing project undertaken at a public university to date in South Africa. The final phase of the project is due for completion in December 2020.
“On every project, our objective is to create a living environment that promotes student well-being and a sense of community, as well as contributes to academic success. Our latest pod design meets these performance criteria and presents one of the most affordable solutions to date in the IBT field,” says Kenealy.
“Ultimately, we believe it’s going to be a game changer in helping to fill the student housing gap, providing a proven, credible and affordable alternative to conventional walling,” he concludes.