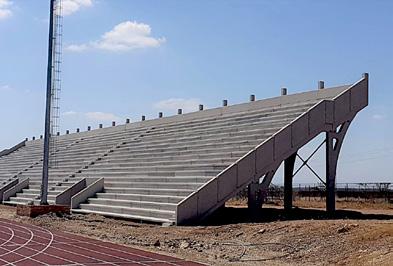
2 minute read
Building precast stadiums
This grandstand is designed to seat 3 500 people Using precast concrete techniques significantly lowers the cost of construction
The employment of precast concrete technology for the construction of municipal stadium grandstands provides a faster and more cost-effective means of construction compared to more conventional approaches, as underscored by a recent project in Limpopo.
Advertisement
By Kobus Kotze* & Willie de Jager**
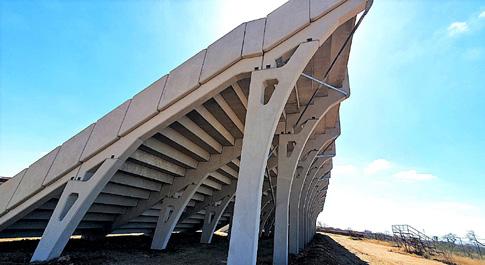
One of the major benefits of the precast concrete grandstand system is that it is helping to empower emerging contractors. While subcontracting the construction of the precast concrete grandstand to a specialist in the field, emerging contractors are involved in all other aspects.
Among others, this includes the earthworks and site terracing, the installation of the various services and perimeter fencing, and the construction of the buildings and the pitch. There are also many opportunities to train and develop community members located within the construction footprint – the beneficiaries of the final infrastructure.
A current project example is a sports and recreational centre constructed for a municipality in Limpopo. It features a grandstand equipped to seat 3 500 people and is the largest structure of its kind designed to date by Infinite Consulting Engineers and subsequently erected by specialist precast concrete innovator Corestruc. This stadium features a roof comprising galvanised structural steel elements, fixed to the concrete structure at strategic positions.
Constructing the grandstand using a precast methodology provided an almost 40% reduction in construction costs for the municipality. This was achieved by eliminating elements that include the need to manufacture bespoke shutters, as well as the requirement for a tower crane.
The grandstand was erected in as little as four months. This is opposed to the 10 months it would have taken to build a similar structure using conventional in situ concrete techniques. Material procurement, such as the special shutters for the seating benches, columns, raker beams, side panels and closures, and establishing the stacking area, alone, would have taken almost four months using cast-in-place methods.
It would also have taken three months just to construct the 9 m high-back columns. This includes setting up the shutters and support, as well as the reinforcement and concrete works. Constructing the 20 bottom, middle and top raker beams and the seating using traditional cast-in-place methods would also have been an onerous, seven-monthlong process.
Precast fabrication
Corestruc’s sister entity, Coreslab, commenced manufacturing of the precast concrete elements for the grandstand in midOctober 2021. The manufacture of the 20
The grandstand is the most complicated aspect of sports and recreational centre projects
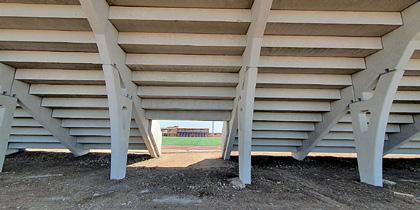
The grandstand was erected in just four months
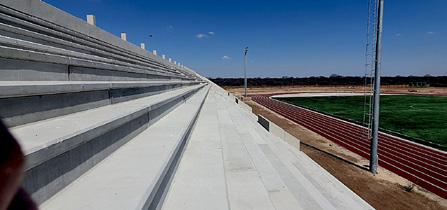