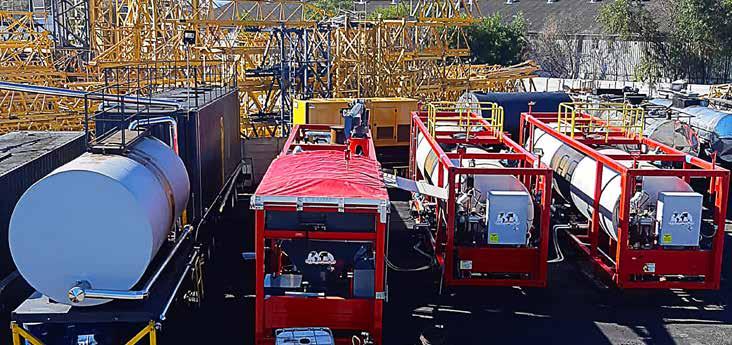
3 minute read
Putting old tyres back on the road, sustainably
from IMIESA October 2021
by 3S Media
The advantages of using ground tyre rubber (GTR) in asphalt – including a more flexible pavement with increased fatigue resistance, and reduction in ageing of the binder – are well known.
Only 20% of rubber tyres are recycled in South Africa, and the reuse of waste rubber in asphalt has the potential to significantly increase this figure and support greater economic sustainability.
Advertisement
AECI Much Asphalt has supplied several road projects with asphalt mixes containing GTR in the past year, notably in eMalahleni, Mpumalanga, and the Western Cape. The increased attraction of this more sustainable solution to asphalt surfaced roads has also led AECI SprayPave – an AECI Much Asphalt subsidiary – to manufacture binder containing GTR in-house, using technology that adds significantly to the shelf life of the binder and saves energy costs.
While this technology is not new to South Africa, it is making pavement mixes containing waste tyre rubber increasingly popular.
Ultra-thin porous surfacing with A-R 2 (warm mix ground tyre rubber binder) on the N5 in Harrismith, supplied by AECI Much Asphalt Bloemfontein
Longer lifespans
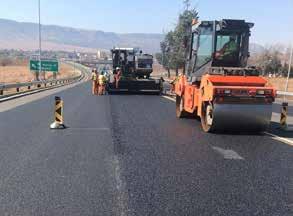
Joanne Muller, manager: Gauteng Regional Laboratory, AECI Much Asphalt, explains that the use of GTR enables the use of more binder in the asphalt without the risk of bleeding or excessive deformation due to increased binder and subsequently mix viscosity. Increasing the amount of binder – together with the elastic properties of the binder and the crumbs themselves – provides longer lifespans for roads and lower rolling noise on the asphalt surface.
“The wet process of using GTR in asphalt typically would have between 18% and 22% of GTR in the binder, which in turn typically constitutes between 5.5% and 7% of the mix,” says Muller. While this doesn’t seem like much, the quantity of rubber tyre used in a mix increases exponentially with the large quantities of asphalt produced for major road surfacing projects.
She explains that the production of hot mix asphalt with GTR requires production of the binder on-site at the asphalt plant, as its use is time sensitive. Digestion tanks and blenders are required, as well as feeder pumps and a header tank to supply the binder into the asphalt plant. For warm mix asphalt, however, the binder does not have to be mixed on-site and can be hauled to the asphalt production plant and utilised without the need for additional equipment. Warm mix asphalt has the added advantage of a lower energy requirement in the manufacturing process and less environmental and social impact.
Production facility
In 2020, AECI SprayPave commissioned a new mobile blending unit, currently located at its Cape Town facility, with the capability to produce bitumen at a rate of 25 t/h, incorporating 25% rubber crumbs sourced from waste tyres. Danashia Munsamy, manager: Quality and R&D at AECI SprayPave’s Alberton plant, says the new plant is using between 50 t and 150 t of waste rubber from tyres per month depending on orders for its rubber bitumen product, EBR (Extended Bitumen Rubber).
“The EBR blends are produced on an order basis and demand has significantly increased in the second half of 2021,” she says. “We are using revolutionary technology that combines rubber crumbs and other additives to give the bitumen a longer shelf life, while simultaneously building moisture-resistant, long-lasting and maintenance-free roads.”
Munsamy says the advantages of EBR include reductions in carbon footprint, energy consumption and emissions. Spray temperatures are lower, and the product has reduced viscosity and longer workability than conventional GTR mixes.
AECI SprayPave’s mobile blending unit can produce bitumen at a rate of 25 t/h, incorporating 25% rubber crumbs sourced from waste tyres
Danashia Munsamy, manager: Quality and R&D at AECI SprayPave’s Alberton plant
Joanne Muller, manager: Gauteng Regional Laboratory at AECI Much Asphalt