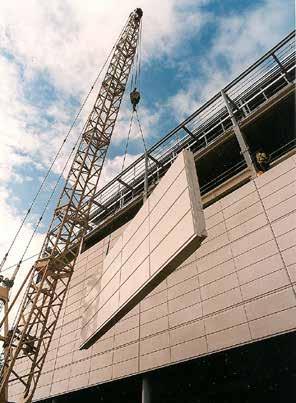
2 minute read
Durable precast concrete cladding cuts costs and time
by 3S Media
CEMENT & CONCRETE
Durable precast concrete cladding cuts costs and time
Advertisement
Economical precast concrete cladding not only offers designers unlimited scope for creativity, but also provides exceptional durability, as well as thermal insulation and construction efficiency, says Gary Theodosiou, structural engineer at Cement & Concrete SA.
Theodosiou states that precast cladding has significant cost advantages, with studies having shown precast concrete elements to be, on average, at least 23% cheaper than cast-in-place equivalents.
“Then, for architects, there's the aesthetic factor. In precast cladding, there are a wide range of options and finishes available to meet both design and budget requirements. In off-the-form finishes, the mould detail is mirrored in the concrete surface and can, for example, produce board-marked, ribbed or rope-patterned finishes,” he explains.
“Exposed aggregate finishes can be specified to reflect the natural colour of the aggregate. Architects are basically spoilt for choice with alternative finishes, such as reconstructed stone, and panels with a polished stone or ceramic tile finish also available,” Theodosiou continues.
High quality is achieved through robust formwork, specific concrete mix designs and manufacturing expertise. Precast elements are cast to tight tolerances controlled in the factory prior to delivery to site.
“The repetition of elements can make the most intricate panel shapes relatively affordable. Furthermore, samples of the proposed cladding can be pre-approved by the client and utilised as a benchmark for quality at the precast operations. Potential human concrete errors on-site are generally removed by factory panel production,” Theodosiou explains.
Standing the test of time
Durability – a prerequisite for any structure – is another highly desirable element of precast cladding. Several South African buildings erected many decades ago (even close to the ocean) still testify to the cladding’s superior durability. The landmark Johannesburg Civic Centre in Braamfontein, completed 60 years ago, is just one striking example.
With extreme weather conditions now increasingly being experienced globally, designers will also be influenced by the fact that concrete retains its structural integrity in flood conditions. Precast elements can also be designed to limit water ingress through the joints.
The use of concrete sandwich panels, incorporating thermal insulation, can also reduce the need for expensive airconditioning or heating equipment in the working environment, while the panels’ superior acoustic quality helps minimise the intrusion of traffic and industrial noise.
Speed of construction and low maintenance
Using precast elements reduces on-site requirements for scaffolding and formwork. With tight construction programmes now generally the norm, precast cladding panels – lifted into place with standard cranes – provide exceptional construction speed to limit building costs.
“The panels can, in fact, already be manufactured while the foundations of an office block are being laid,” Theodosiou points out.
Precast cladding requires minimum maintenance with no need for frequent cleaning, and non-combustible concrete’s exceptional fire resistance is well known in the design and construction sectors. Supplementary cementitious materials are now also widely used by precast producers to reduce the cement content, thereby lowering the carbon footprint of concrete cladding.
Cladding categories
Theodosiou says architectural concrete claddings generally fall into two categories: • Claddings that purely serve as enclosures.
In this application, the claddings are applied as self-finished panels or as backing components to other facade materials, such as brickwork. • Claddings that form an integral part of the framework of a building. These