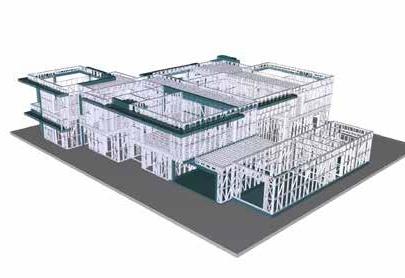
5 minute read
Building Systems
by 3S Media
Light, strong and sustainable
in steel
Advertisement
Alternative building technologies (ABT) are becoming increasingly popular as fast and costcompetitive alternatives to conventional materials like brick and concrete. When it comes to durability and sustainability, light steel frame buildings (LSFBs) compete on an equal footing, says Mitchell Walker, director, Futurecon. By Alastair Currie
The Eiffel Tower, erected in 1889, measures 324 m in height and is composed of hot rolled wrought iron sections. It stands today as a classic example of the endless possibilities of constructing in steel and was a front runner for a host of classic buildings. These include the 102-storey Empire State Building, completed in 1931. Like many icons of its day, its heavy-duty structural steel frame enabled skyscrapers to reach unprecedented heights.
At the other end of the scale, the development of far lighter and stronger cold rolled steels over the past decades have presented a host of new opportunities for residential, commercial and industrial developments, challenging other mediums as the construction material of choice. These LSFBs can be singleor multi-storey structures, with their designs in South Africa governed by the SANS 517 building code. Formed using structural trusses and walls made from cold formed thin gauge steel sections, their internal and external walls can be clad in a range of materials, including gypsum, timber and aluminium sheeting.
LSFBs are faster to construct than conventional brick-and-mortar-type buildings. Since they are significantly lighter, LSFBs also
An LSFB design schematic: schools, hospitals, libraries and commercial offices are just some of the possibilities Before and after perspectives of a warehouse and office block development constructed using LSFB techniques
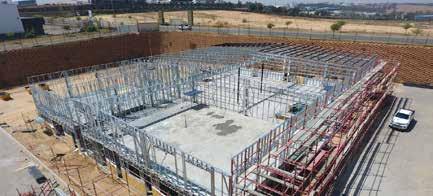
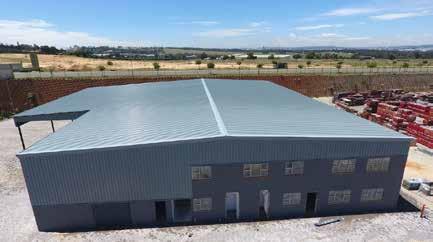
have less complex geotechnical requirements in terms of foundations. Futurecon uses 0.8 mm and 1 mm gauge steel as standard, with the option of using 1.2 mm and 1.4 mm thick sections.
“Depending on the design requirements, building plans may be modular, or purpose built for each application,” says Walker. “Within the modular space, for example, we’ve recently developed a new product line under the ‘A warehouse in a box’ brand, which enables us to manufacture, replicate and supply LSFBs to customers worldwide. A warehouse building of approximately 1 200 m 2 – essentially four walls and a roof – can be dispatched in a single shipping container.”
Within the industrial market, recent completed projects include a 2 000 m 2 warehouse with 1 000 m 2 office block development for a client in Johannesburg. Meanwhile, in Cape Town, Futurecon is currently working on a renovation project, where the scope of works entails the supply of a 2 000 m 2 roof plus 1 300 m 2 of wall cladding for an existing building.
Unsupported spans
Within the commercial and industrial space, LSFBs compete favourably with steel portal frame structures, typically composed of more robust horizontal beams or trusses that will need some measure of piling. Portal frames are designed with interspersed vertical I-beam columns to support the roof span.
Being lighter, the roof load bearing capacity of LSFB systems allows for impressive unsupported spans of up to 48 m. Roofs can be assembled in complete sections on the ground and then lifted and positioned by crane. As a further plus, external walls are around 130 mm thick compared to up to 240 mm for brick. Additionally, since the bulk of the components is delivered in sections from the factory, there’s minimal – if any – wastage on-site, which translates into further cost savings.
“In all respect, the foundations need to be perfectly level to the last millimetre to achieve flat walls with exact 90-degree corners,” says Walker.
As an integrated system, LSFBs provide exceptional thermal efficiency, with Futurecon’s standard walls achieving R values
ranging between 3.2 and 3.7. Insulation is chiefly provided by the woven glass wool filler in the frame cavities, plus the internal and external cladding specified. This greatly reduces the reliance on HVAC systems to regulate seasonal temperatures.
Comparable with brick structures, standard external and internal walls have a one hour and a 30 minute fire rating, respectively. Typically, the heat of a fire needs to rise to around 396°C before the steel buckles.
Housing market
“Interestingly, in warmer countries like Australia, steel frame homes have been one of the preferred construction methods for generations,” Walker continues. “And we’re starting to see this trend developing locally, including growing demand for high-rise rooftop conversions.
“We’ve even filled orders for a few tiny homes – some trailer mounted – and mostly for the leisure market. However, it does underscore the fact that LSFBs are a good option for a broad spectrum of residential developments in South Africa. These include low-cost and affordable housing,” he expands.
In more simplified forms, LSFBs are well suited for self-build programmes. Singlestorey homes can subsequently go up a level, as well as expand laterally. The same is true for any conventional property requiring modernisation or renovation, such as schools and hospitals, where the South
LSFB methods provide self-build and SMME opportunities in the human settlements sector, where there is a pressing need to address the housing backlog
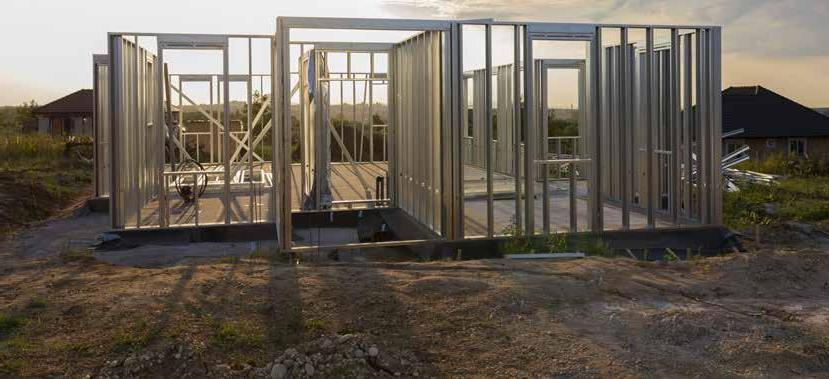
African government is placing major emphasis on ABTs to accelerate the roll-out of critical infrastructure. This makes a strong business case for LSFBs. A prime example is a current public hospital project in Gauteng where Futurecon is supplying some 10 000 m 2 for a series of buildings.
Rust-proof
Extending the life of building assets and lowering maintenance costs is a core concern for any property owner. In this respect, steel goes the distance since the sections are galvanised to prevent rust.
The durability of LSFBs has been confirmed via various long-term case studies, including the Southern African Light Steel Frame Building Association’s Rust Report. This includes reference to a school in Cape Town where only minimal traces of rust were detected on screw connections after 10 years. The frames themselves were rust-free.
“It’s important to stress here that specifying the correct components for every section is an essential part of ensuring the building’s long-term integrity,” adds Walker. Going forward, the design
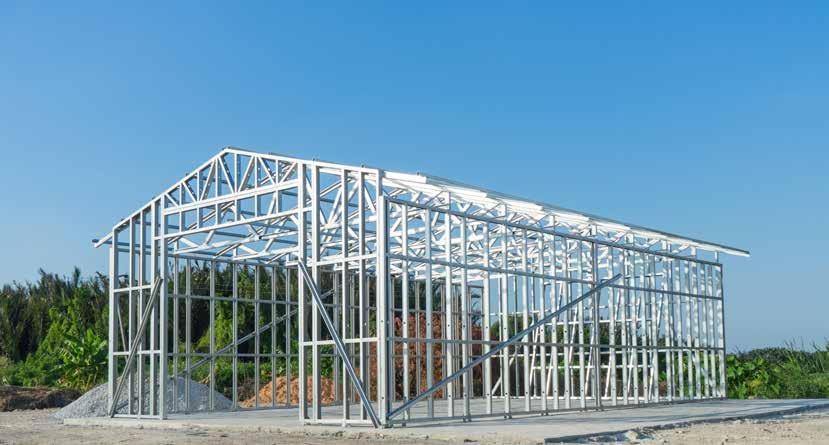
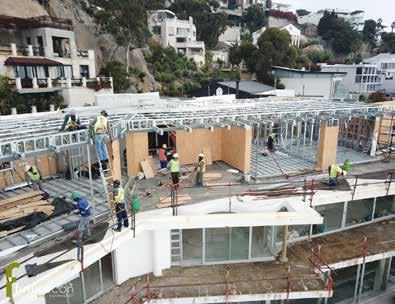
Internal and external cladding systems being installed on a housing development
possibilities are endless and Futurecon continues to work with architects and property specialists to develop new model variants, including so-called hybrids. An example is a potential project that has ground-level concrete and basement structures topped by a multi-storey steel frame building, which combines I-beams with LSFB techniques.
“Given the strength of steel and its proven durability, it’s an ABT that deserves far greater attention in South Africa,” Walker concludes.
Compared to portal steel structures, LSFB designs make provision for larger unsupported roof spans