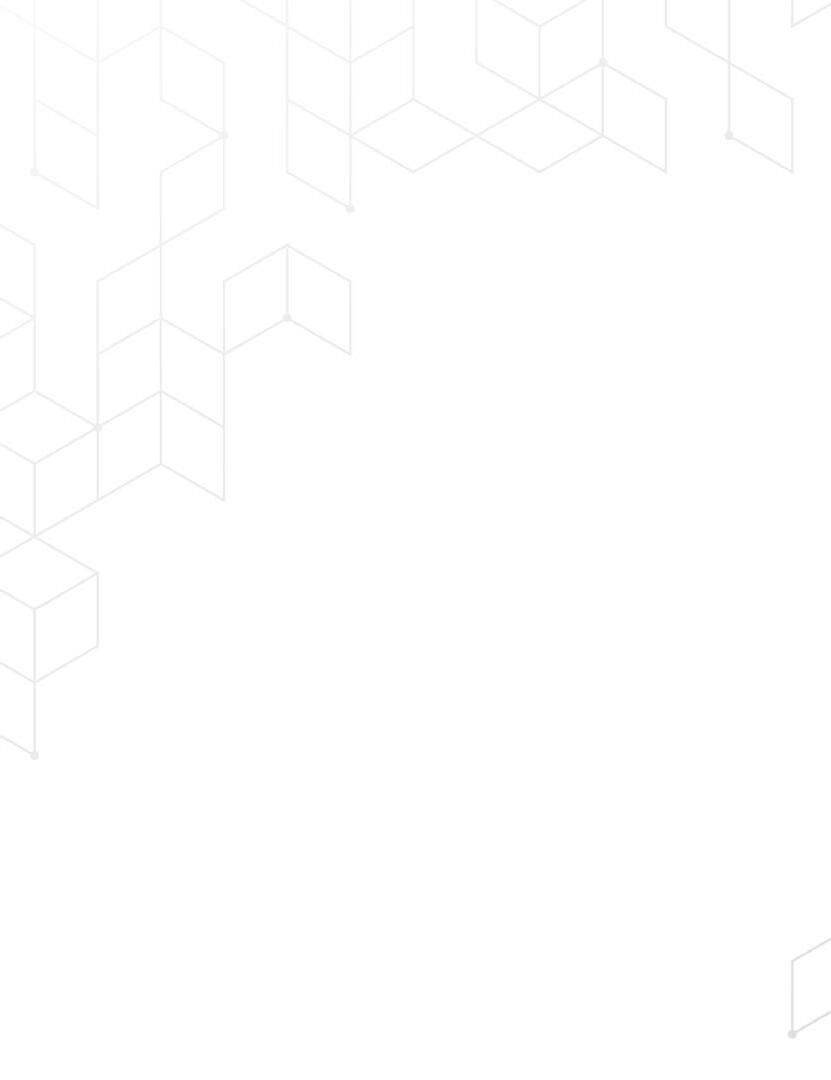
6 minute read
Emission solutions for underground mining equipment
EQUIPMENT
Emissions solutions for mobile mining equipment
Advertisement
There can be no compromise when it comes to air quality management, especially in the underground mining environment. Dispro Tech SA specialises in products and services to assist mines in ensuring they maintain underground operations that are safe for employees to work in.
Commonly deployed underground mobile mining equipment – such as load, haul dump machines (LHDs) and utility vehicles – is often diesel-fuelled and critical for the production system. Unfortunately, such equipment subsequently compromises underground air quality. Air pollution is caused by solid and liquid particles and certain gases that are suspended in the air, with many of these stemming from underground mobile equipment and other moving machinery exhausts.
The underground mining environment is unquestionably harsh. With confined spaces, minimal ventilation and underground vehicle emissions that compromise air quality underground, systems that monitor the surrounding air quality are critical for the health and safety of employees, as well as the environment.
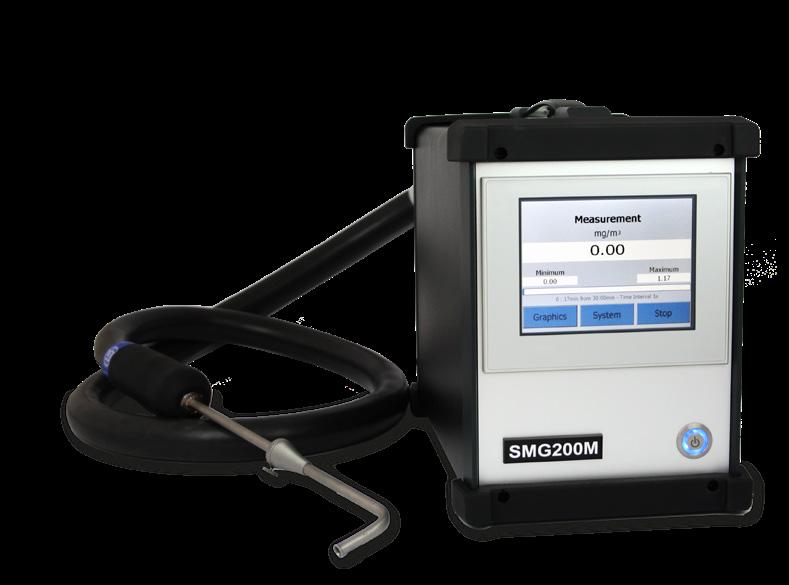
EQUIPMENT
A smoke meter used to perform a smoke opacity test on diesel vehicles
How it all started
According to Deon Du Preez, founder, co-owner and managing director at Dispro Tech SA, the Mpumalanga province and parts of Ekurhuleni have been identified as potential hotspots for poor air quality. These conditions – as well as noting the black smoke emitted from vehicles from time to time – motivated Du Preez to look into solutions to these concerns.
Starting up was not easy and there were many challenges, including deals falling through; however, Du Preez’s persistence and determination eventually led to identifying a business opportunity that would see him improving air quality and protecting the environment as well.
He proceeded to do research and found that, in addition to affecting the environment, diesel particulate matter (DPM) also had health-related consequences, affecting the lungs if inhaled. In addition, Du Preez’s findings showed it was these emissions that resulted in hefty costs during vehicle maintenance. He also identified the need for a service offering in the mining industry, among others.
Using all this information, Du Preez got to work and approached institutions and organisations to collaborate with developing a product that would assist mines in monitoring air quality at their operations, as well as the emissions of mobile equipment at the mines.
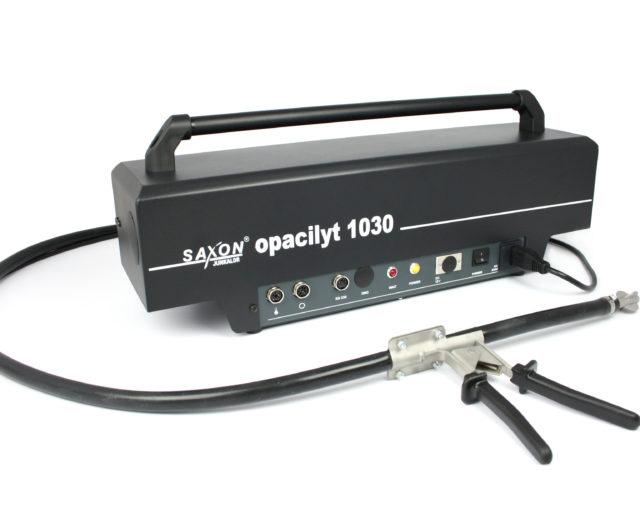
World-class technology
“I asked myself, why is it not possible to measure diesel particular matter directly from exhaust in its raw undiluted condition?” Du Preez ponders. This question was the motivation for him to find partners to collaborate with in establishing an answer.
Working together with the CSIR, Sasol, Deutz Diesel Power and Saxon Junkalor, among others, Dispro Tech SA introduced a world-first technology that measures directly from an exhaust stack. “We ran a programme to see how accurate the equipment was,” explains Du Preez.
A brief data sampling and evaluation can provide users with critical early-warning information pinpointing internal engine problems based on DPM, smoke density and opacity, and six-gas evaluation of the results, which also includes the correct diagnosis for diesel engines that are in a good and acceptable condition to receive such an exhaust aftermarket treatment system, such as a diesel particulate filter (DPF).

Solutions to address emissions in mining
As a premier diesel engine emissions monitoring company, Dispro Tech SA has the required specialised expertise not only to address underground emissions but also monitor air quality. Following 15 years of research and analysis, the company’s service offering has expanded and includes diesel combustion analysis, predictive failure analysis, predictive maintenance, DPM verification and reporting, as well as DPM legal compliance services.
Dispro Tech SA will take a series of emissions measurements from the exhaust discharge and
EQUIPMENT
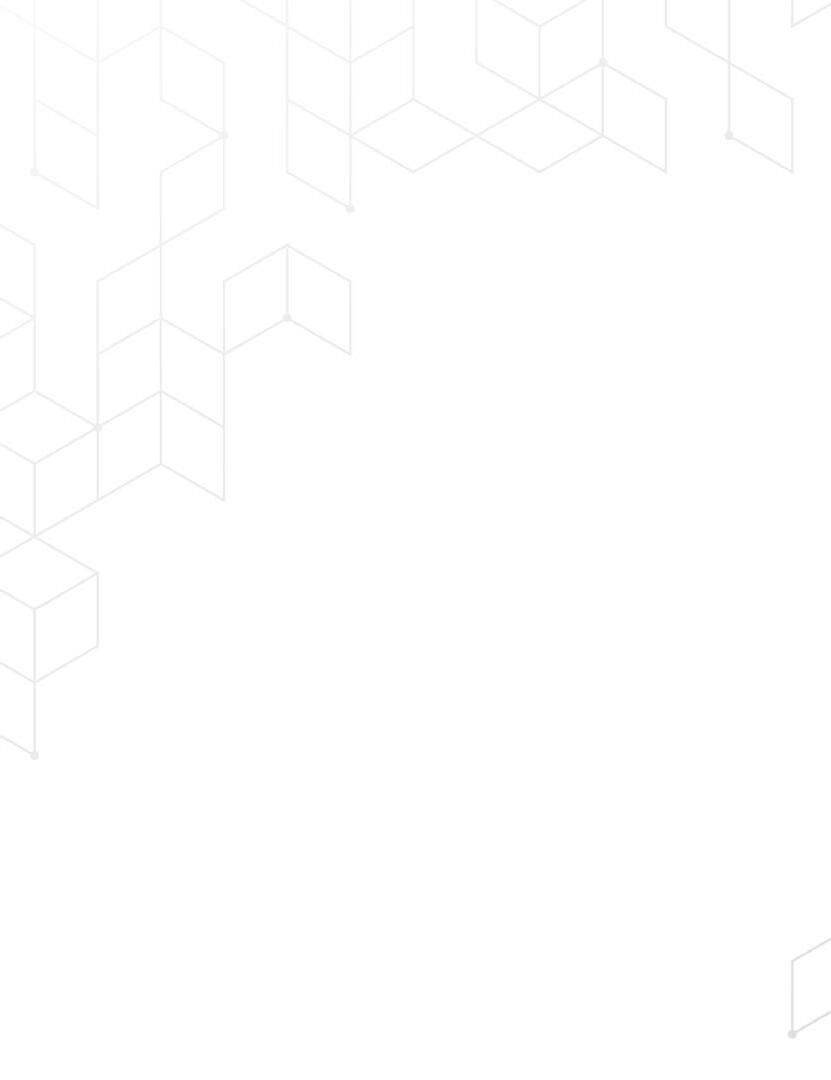
from installed measuring points, to gather samples – from raw gas (RG), pre-exhaust gas after treatment, conditioned gas (CG) and postexhaust gas after treatment of diesel-powered equipment – from both surface and underground machinery.
The company’s permanent technicians work closely with the mine’s engineers on-site. Between them, a test schedule is established whereby the tests are conducted full-time on a monthly basis (weekly service schedule). All tests will be performed in both the surface and underground workshops. RG & CG tests are undertaken on all LHDs, DRGs and utility vehicles at the mine.
Once all the tests are completed, the data is safely stored on an online portal, which can be accessed by relevant engineers, managers and foremen. A comparison graph and data sheet will also be available on the portal to guide engineers daily. All this information facilitates improved critical decision-making.
A step-by-step process for measuring and testing equipment
For the best and most accurate test result, the measuring and testing of equipment follows a stringent step-by-step process: 1. Technicians make use of measuring and testing equipment to gather data and information as required by the customer. 2. The performance of aftermarket products on exhaust systems is verified. 3. Customers are provided with analysed data from the company’s internal data portal. This data details any issues and provides solutions, pinpointing combustion problems and providing suggestions to rectify concerns. 4. The data is then compared data with the data available on the supplier’s web-based portal. 5. Condition monitoring is undertaken on diesel engines. 6. Results are reported showing where gaseous emissions by diesel engines exceed prescribed and/or pre-agreed acceptable limits.
Industry experts delivering positive results
Not only does Dispro Tech SA’s product and service offering reduce vehicle emissions, but it has also shown to have proven results. These include a 95% reduction in DPM – which translates to improved air quality at mine operations.
The company is an independent supplier of measuring and monitoring equipment that cannot be found anywhere else. Clients can be assured that the products are of OEM quality. According to Du Preez, the equipment complies with ISO 3930:2009 (instruments for measuring vehicle exhaust emissions; metrological and technical requirements; metrological control and performance tests).
In addition to providing industry-changing solutions to the mining industry, Dispro Tech SA has also made a meaningful contribution to the industry at large. The company was among the advisors on the Mine Health and Safety Council’s circular regarding DPM.
Dispro Tech SA’s product and service offering has assisted mines in complying with underground air quality regulations, and has reduced maintenance costs of mobile mining equipment thanks to predictive failure analysis and predictive maintenance. The company’s service offering provides a bird’s-eye view of an operation’s fleet to authorised mine personnel. “They can pull the information at any given time,” Du Preez notes.
Dispro Tech SA’s customer base includes some of the biggest mines in South Africa’s gold, platinum and diamond sectors. The company has also done work outside of South Africa in Zimbabwe and Botswana. “I did some baselines with mines across our borders and we firmly believe it will take off next year,” Du Preez concludes.
CONTACT
For more information, contact Dispro Tech SA: Telephone: +27 (0)13 243 5753 / +27 (0)13 243 1851 Website: www.dispro.co.za
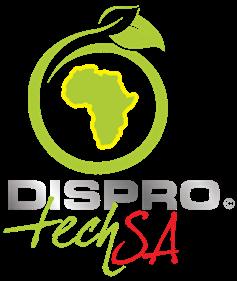