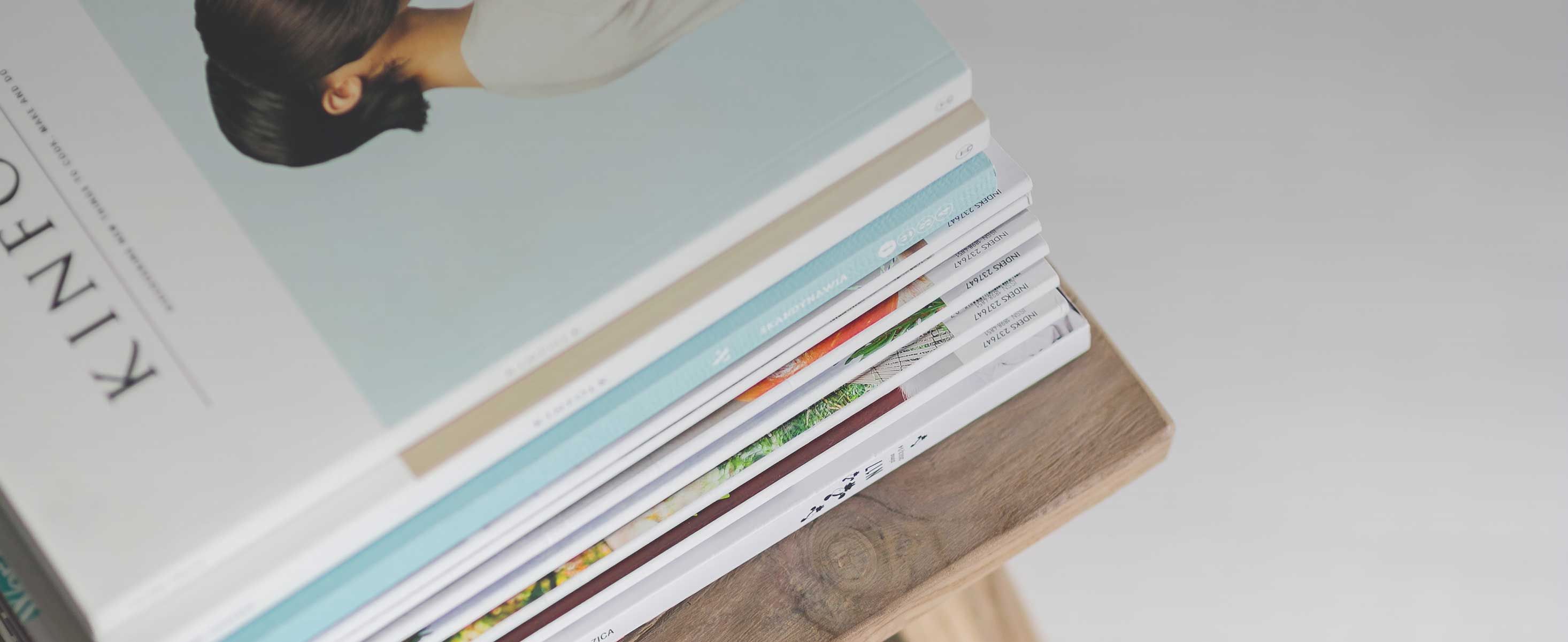
3 minute read
FOREWORD
to consider its own priorities in isolation is high. With transparency around the impacts of each challenge, mine management will be more able to adapt and change course in a way that delivers minimal disruption and maximises productivity, profitability and predictability.
Mining organisations need to implement single solutions that can automate data gathering from various mining processes and facilities using tools that can detect bad data, process it in the correct context, and output insights in a meaningful and actionable timeframe.
Advertisement
The predictive dimension
Access to and insights derived from good data are just one part of the equation. Mining companies need to leverage advanced machine learning technologies to learn from and improve in the future.
Traditional maintenance practices, for example, generally cannot deliver the benchmark equipment availability, performance and reliability required, which affects short-, medium-, and long-term schedules upon which financial projections and corporate targets are based. The ability, or lack thereof, to deliver to these projections not only has an impact on quarterly profitability but also on senior leadership’s confidence in their operational leadership –and, in turn, investor confidence in the senior leadership team running the company, as well as impact sentiment regarding the company.
That’s where modern predictive/prescriptive maintenance solutions present material advantages. The technology monitors data from sensors on and around fixed plant and equipment to develop intense, multidimensional and temporal patterns of normal operation, abnormal operation and explicit degradation conditions that precede breakdown.
Human interpretation simply isn’t capable of deriving the insights the technology delivers. Beyond providing extreme early warnings, monitoring technology can also assess the health of numerous machines every few minutes, delivering insights around equipment performance to maintenance teams, often with prescriptive advice that addresses the bad actors and known issues.
The applications monitor many variables on behalf of the workers who receive warnings to help them know what maintenance issues to prioritise, what parts to order and keep in stock, and when to order them.
Finding a solution
An asset performance management (APM) approach, with integrated predictive/prescriptive maintenance capabilities, assures mines improve reliability, availability and uptime while reducing the requirement and expense of redundant equipment.
Operations teams have often planned for lower availability – installing three machines when they only need two or operating 30 truck fleets to ensure they always have 26 up and running. With the right technology, mines can achieve benchmark reliability without the need for more people, more equipment or higher budgets. Companies can work at the required production levels and either park up or switch off redundant equipment, and do so while delivering to the short-, medium-, and long-term plans and projections the company communicates to investors and the market. Mines can also implement other aspects of APM programmes to draw on data from sensors and other sources, such as enterprise resource planning (ERP) systems, manufacturing execution systems (MES), laboratory management information systems and advanced process control (APC) systems, for example. Machine learning and other data science techniques require the delivery of available data – so, plant historians can play an important data delivery role and provide the backbone from which all data can be sourced for the rest of the organisation.
Getting processes right
Integration and interoperation between the foundational technologies are a part of the journey towards the intelligent mine. A predictive maintenance system must be fully capable of incorporating data from the APM system (to predict explicit failures) and data from the plant historian to be able to understand operational activities. Additionally, the application must offer ease-of-use and low-touch capabilities without needing expert services to ensure rapid upscaling across diverse assets in the mine. Today, the mining industry is mature enough to fully embrace and use digital optimisation technologies. Operators failing to adapt or build a strategy to use such technology will certainly struggle to compete against those that do. Predictive and prescriptive maintenance applications can quickly bring measurable results to a mining company by improving the use of capital assets and eliminating unplanned downtime, which has a direct impact on productivity and safety, as well as reliably meeting planned schedules.
Scalable prescriptive maintenance solutions add value to fixed and mobile plant and equipment across an entire global enterprise. The truly intelligent mine delivers significant reductions in unplanned downtime and reduces safety risks, while ensuring an entire mining organisation operates more efficiently and profitably.
*Mike Brooks is the global director: Asset Performance Management Solutions at AspenTech.
Multidisciplinary construction group Stefanutti
S t o c k s u n d e r t a k e s p ro j e c t s a c ro s s S o u t h
A f r i c a a n d s u b - S a h a r a n A f r i c a . W e a r e committed to achieving nothing less than our mission of across all excellence in execution of our projects.
We undertake multidisciplinary construction contracts for the following sectors: Building; Bulk Earthworks & Geotechnical; Energy Generation; Industrial Plants; Oil & Gas; Contract M i n i n g & M i n i n g I n f r a s t r u c t u r e ; Tr a n s p o r t Infrastructure; and Water, Sanitation & Pipelines.
Address: 9 Palala Street, Chloorkop, Kempton Park Johannesburg, 1619
Tel: +27 11 571 4300
Email: inland@stefstocks.com
Website: www.stefanuttistocks.com