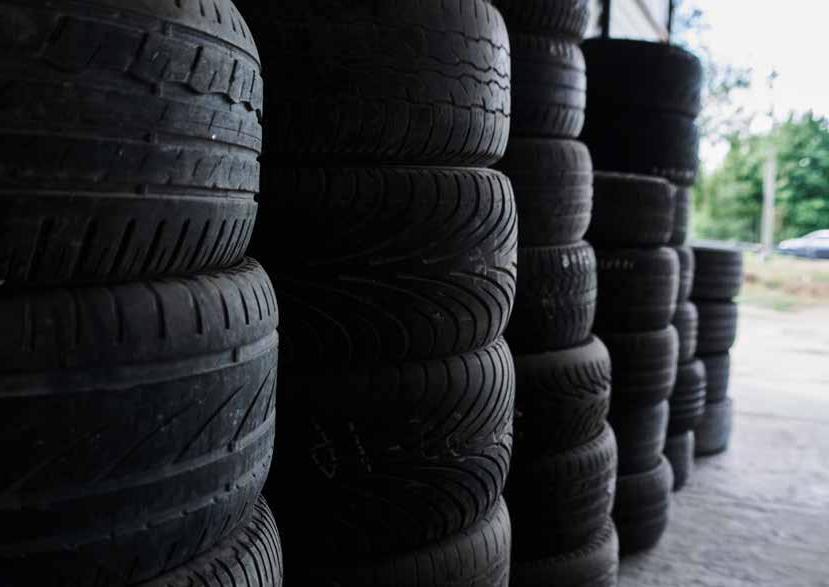
4 minute read
Driving sustainable practices in the tyre industry
from ReSource August 2021
by 3S Media
South Africa’s recycling rate for vehicle tyres increased from 4% to 60% in the space of three years after the implementation of the Waste Tyre Management Plan. The strategy was developed where used tyres were collected from dealers, brought to dedicated depots, and then transported to processing plants for recycling.
All activities were funded by introducing a tax instrument that placed a levy on all new tyres. The environmental tyre levy, which is implemented through the Customs and Excise Act (No. 91 of 1964), allows for:
Advertisement
• the tyre manufacturing industry to pay the levy directly to the South African Revenue Service, for depositing into the National Revenue Fund, as with all other environmental related taxes.
It is estimated that millions of waste tyres are lying in South African dumps, as stockpiles, or simply scattered across residential, industrial and rural areas.
• the revenue raised through the levy to be appropriated to the Department of Forestry, Fisheries and the Environment (DFFE) via the national budgeting and appropriations process, for funding the implementation of the tyre waste management programme to contribute to reducing waste tyre disposal on landfills and to build a viable circular economy from the recycling of end-of-life tyres.
A fee of R2.30/kg is levied on all new tyre rubber. The proceeds are used to establish infrastructure for tyre collecting and downcycling, and pay for its administration. The DFFE is the current custodian of the industrywide plan.
The SATMC
Nduduzo Chala, managing executive at the South African Tyre Manufacturers Conference (SATMC), says local tyre manufacturers have always supported the implementation of the levy to fund the proper treatment and disposal of waste tyres.
“It is critical for the tyre industry to ensure that waste tyres are disposed of correctly in order to limit the impact on the environment and ensure that they do not find a way back into the market,” he says.
Waste tyres that are resold are not only illegal, but pose a safety risk for consumers, Chala emphasises.
The SATMC is the official industry body and trade association of the four local tyre manufacturers – Bridgestone, Continental, Goodyear and Sumitomo. They are the voice of the local tyre manufacturers and represent them on trade, economic and environmental policies, and tyre sector regulations.
They are currently focusing on four main areas of improvement – the proper mutilation and disposal of waste tyres, a reduction of materials used in manufacturing tyres, the sustainable sourcing of materials, and a reduction in carbon emissions.
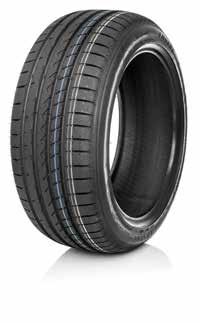
Environmentally friendly tyre
Bridgestone has introduced the new Ecopia tyres, which are environment-friendly and fuel-efficient. This tyre reduces fuel consumption and boasts a quieter ride and improved roadholding, while reducing carbon dioxide emissions.
Sustainable sourcing of materials
Goodyear’s overall corporate responsibility includes the sustainable sourcing of materials. The company is exploring using a soybean oil tread compound in four of its tyre lines to create more sustainable rubber with added traction benefits. It also uses rice husk ash silicate, which helps to deliver similar performance to traditional sand-based silica with less environmental impact and waste to landfills.
Reduction in carbon emissions
Sumitomo Rubber SA has installed a 1 MW solar system on its truck and bus radial production facility roof in order to reduce its emissions from electricity consumption. Additionally, Continental Tyre South Africa won the Industrial Corporate Project of the Year award for innovative industrial energy management projects and outstanding contributions to the energy industry. Continental received this award for a heat recovery project that saved 4.5 million kWh of energy and over R1 million in 2019.
A new dawn
The Waste Bureau was appointed by the DFFE with the responsibility for tyre waste management since October 2017, after the withdrawal of the Recycling and Economic Development Initiative of South Africa (Redisa) plan. However, the Bureau has been challenged with processing capacity since it started managing waste tyre operations. Its processing performance was further affected in 2020/21 due to Covid-19.
Chala emphasises that although the industry has been diligently paying the levy, these issues with the collection and disposal of waste tyres have impacted the tyre recycling industry negatively. “We need to put in place a sustainable recycling mechanism, so that tyres do not end up at landfills but are utilised effectively through recycling.”
The SATMC and other players in the tyre sector are currently working with the DFFE to finalise the details of an updated/new draft industrywide plan.
“As the local tyre manufacturers, we will continue to be responsible and work with government to ensure we comply with regulations and put in place measures that limit impact on the environment; however, the DFFE, as the custodian, needs to take more ownership of the plan and implement proper measures to dispose of waste tyres, seeing as the industry is funding it,” Chala concludes.