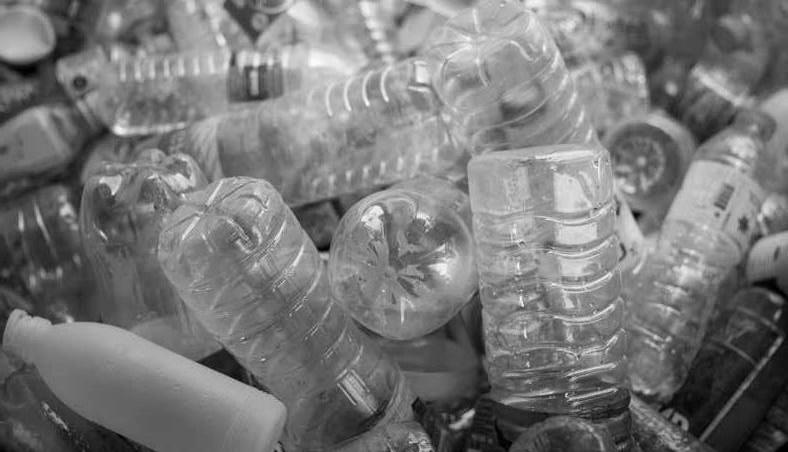
5 minute read
GREEN BUILDING
from ReSource May 2021
by 3S Media
PLASTIC WASTE
The concrete solution to PLASTIC WASTE
Advertisement
Plastic waste is an enormous global problem, with only 9.5% of plastics being recycled yearly. The other 90.5% is either incinerated, or ends up in landfills and the ocean.
By Nombulelo Manyana
nly 21% of the 1.5 million tonnes
Oof waste generated yearly in South Africa is recycled. The rest, like in many other countries across the world, ends up landfilled or in the environment. In terms of socio-economic numbers, South Africa has a severe housing shortage, with the housing backlog reportedly sitting at 2.3 million houses, and growing by around 178 000 houses a year. South Africa’s official unemployment rate has also risen to a staggering 32.5% between October and December 2020, with 11.1 million people currently out of work.
Although these statistics may seem shocking, the Centre for Regenerative Design and Collaboration (CRDC) believes that they also present a unique opportunity. With the introduction of what they call a new innovative technology, the CRDC will not only help mitigate the growing waste problem but will also create jobs, boost informal waste collection and solve some of South Africa’s other major problems by building houses, hospitals, schools and roads. RESIN8 – which is the CRDC’s groundbreaking, regenerative solution to South Africa’s unmanaged plastic waste – is a breakthrough concrete modifier made from mixed plastic waste. It can take any type of waste plastics and convert them into high-value concrete modifier that perfectly simulates construction sand.
Deon Robbertze, manager: Business Development and Communications at CRDC, says the RESIN8 technology represents a “crossindustry collaboration between CRDC, leading plastic, waste management, construction industries and NGOs.”
Who is CRDC?
CRDC is a global company with its roots in Costa Rica. Founded by Donald Thomson in 2010 as a volunteer-based beach clean-up programme, it is presently recognised internationally for its contributions towards sustainable product design. CRDC comprises a diverse, multidisciplinary group of experts in the packaging and food/beverage industries, conservationists and award-winning designers working to create products, industrial processes and economic models that provide socio-economic and environmental benefits.
The company also operates in South Africa, with a pilot plant based in Cape Town.
Through its net-zero-focused business model, REAP (Recover – Enrich – Appreciate – Prosper), CRDC has created collaborative relationships between diverse industries, where the waste stream of one can become the value stream for the next.
RESIN8
RESIN8 is a process that can turn any plastic – dirty or clean and in any form – into concrete modifier. The end results are environmentally friendly products that incorporate regenerated waste plastics, which would otherwise be destined for landfills.
Through the REAP process, all types of postindustrial and consumer plastic waste are recovered using different avenues, as shown in the figure below.
Then, while coexisting with them, natural systems can be regenerated and enriched.

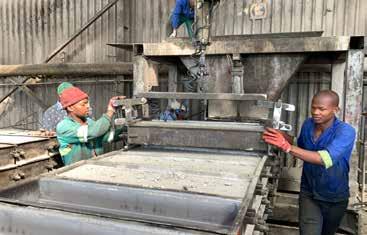
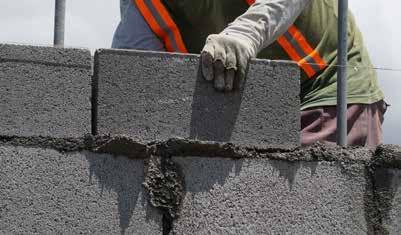
Resources can be kept in use and their value appreciated while also being preserved.
A tonne of mixed plastic waste can, through the RESIN8 process, produce around 4 000 concrete blocks, while 1 000 tonnes will equate to 4 000 000 concrete blocks.
RESIN8 has multiple applications, namely concrete blocks and pavers, precast concrete and poured-in-place concrete.
It is the only material made from plastic waste that maintains or improves the performance of concrete products. It is tried, tested, in operation, has low capex requirements and can be scaled to regional remediated plastic waste volumes.
RESIN8 supports 12 of the 17 United Nations’ Sustainable Development Goals and is the 2020 Winner of the DOW Impact Award.
In Costa Rica, 400 houses have already been built in partnership with Habitat for Humanity and Costa Rica’s leading concrete company, Pedregal. Here in South Africa, Martin&East will be building about 4 000 Breaking New Ground homes over the next four years for the Western Cape Provincial Government, with the project set to have started around the end of March 2021.
Those houses will have RESIN8 in the concrete blocks, making them stronger and increasing the thermal characteristics of the concrete blocks by 25%.
“This means that you will need less heating and cooling in that house. With climate change, that is another added value of the product,” said Robbertze.
Other key benefits
The porous composition and gradation of RESIN8 improves both the mechanical and chemical bond to cement. It has numerous key benefits, which include the following.
Within concrete and construction:
• increase in strength • 8% to 16% decrease in weight (with 5% or 10% RESIN8) • increase in thermal properties • same fire resistance as with standard concrete • reduce cement industries carbon footprint.
Environmentally:
• supports and grows the UN Sustainable
Development Goals • reduces carbon footprints by eliminating plastic to landfill and plastic pollution • all types of plastic can be regenerated into
RESIN8 – no separation required • supports zero waste to landfill, extended producer responsibility and government programmes or initiatives.
Social and economic:
• SMME and job creation from waste plastic collection, plastic shredding and transport • cleaner cities and healthier environments • helps support the building of better housing with a product that benefits the environment and society.
Prosper
In terms of the last step in the process, Robbertze says that beyond creating better housing and infrastructure for those that need it, the aim is to ensure that jobs are being created for people living in informal sectors.
“It is absolutely critical to create jobs and build better infrastructure in this country. And we take our inspiration from nature – it doesn’t waste.”
CRDC’s full-scale plant, which is expected to use up to 1 000 tonnes of plastic waste per month and convert it into RESIN8, will be up and running by the third quarter of 2021. The company also plans to have 21 plants across South Africa in the next five years.
“Now that we have a zero-waste solution to our unmanaged plastics problem, we have a massive responsibility to make it happen at scale,” says founder Donald Thomson.
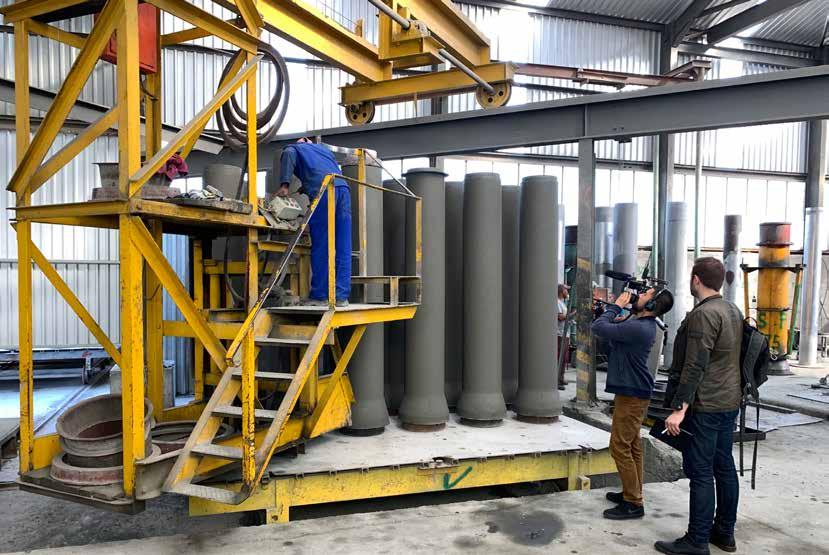