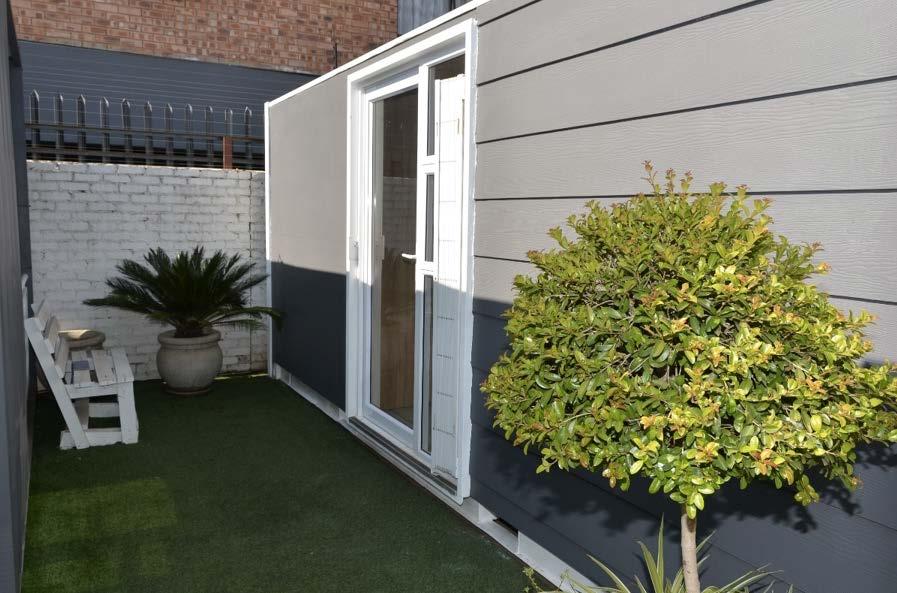
4 minute read
Homes and spaza shops reinvented
from Spotong Issue 35
by 3S Media
Why converted shipping containers outperform bricks and mortar
By Natalie Kinsley
Advertisement
Throughout Europe and the US – and now Africa – shipping containers have entered the spotlight. These containers hold huge value and, once converted into modular units, serve proudly as affordable and durable spaza shops, homes and living units, offices, garages, student accommodation, mobile clinics, creches, coffee shops, mobile mine compounds and many more applications. In South Africa, the traditional method of building homes with bricks, cement and mortar will probably always be with us, but with the desperate shortage in the housing and retail markets – and in space in general, for garages, storage, business and offices – an alternative way of building has taken the world by storm!
Durable and require little maintenance
Shipping containers are built to withstand severe ocean conditions. They are watertight and airtight because of the high-value cargo they would traditionally carry and are designed to last in extreme environments for many years. In a home environment and stable climate, these structures can last for generations and require very little maintenance. In fact, because of their sturdiness, the cost of maintenance is at least 80% less than conventional brick and mortar construction.
The modular units are constructed as a “monocoque” unit, meaning they are sealed units that cannot be penetrated by water or smoke. The material used to construct them is 1.9mm corrugated corten steel (or weathering steel), which requires no painting. The frame, cargo doors and cross members are also made from the same hightensile corten steel.
Spotong spoke to Chic Berkhout from Rebirth Modular Trends, an expert in the field who specialises in converting these containers into complete, functioning units, kitted out with plumbing and electrics, ready for delivery. The internal cladding used comprises two steel chromadek sheets filled with 40mm thick Rockwool, which is a rock-based mineral fibre insulation.
“This provides excellent insulation qualities in both extreme heat and cold conditions,” he said, adding that the ceilings are made of rigid Isoboard secured to a suspended ceiling grid, and the outside walls are cladded with magnesium fibre boards. This greatly helps with insulation and also gives the units a more traditional appearance.
Flooring options can be either ceramic tiles, laminated artificial wood panels or self-leveling rubberised rhino lining, which is fitted on top of the standard 18mm thick moisture-resistant wooden boards. All electrical and plumbing piping and services are installed and concealed behind the internal cladding. Although containers do not have windows, these are manufactured to spec when converted and are made out of white aluminium and glazed to SABS standards. Doors are either manufactured out of white aluminum or solid wood. Inside the units the doors are standard hollow-core wooden doors.
Fully manufactured offsite
While there are numerous benefits of modular homes and spaces, two things stand out and really set modular units apart. Firstly, the units are fully manufactured and fitted with kitchen, bathrooms and built-in cupboards in the factory. This means that a home or garage or retail shop space or offices are ordered, and within a few days, the unit arrives. One day there is nothing, and the next day your home, office space, or garage is delivered, turn-key and ready to use. The unit is secured, the electrical and plumbing systems are connected, and the keys are handed over. No mess, no fuss, no construction. Chic noted that the speed at which these units are completed is at least 75% faster than a similar size home built with brick and mortar.
Mobile spaces that can move with you
The other big benefit of modular homes and spaces is that they are ultimately mobile. If an owner needs to move to another province, for instance, he can arrange to uplift the home with specialised equipment and take it to his new location. The commercial options for these units are vast. With the pandemic still not over, things like mobile clinics, testing stations, temporary accommodation, ablution facilities and isolation facilities have really proven that this is the way of the future. Once the need for the facility is no more, then the units can be uplifted and moved to where they are needed. Another very popular application are things like small mobile spaza shops, mobile coffee shops, mobile hair salons and all manner of business uses. The units are extremely well built and tough and are a real deterrent to burglars.
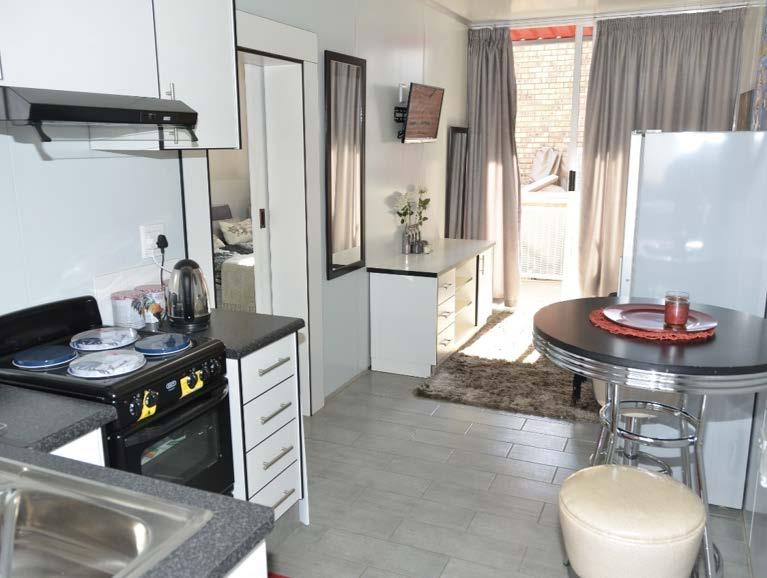
For more information, please contact Chic at Chic@zenithcpm.co.za
Modular units – quick facts
• The smaller unit is 2.4 x 6 metres (14.4 m2), and the larger one is 2.4 x 12 metres (28.8m2). • Units come ready to use with all plumbing and electrics ready to be connected to the mains. Plug and play! • The units are mobile and can be moved should the owner require. • The uses of the modular units are endless – a home, additional living space, granny flat, offices, garages, spaza shops, storage, etc. • The units are durable and require very little maintenance. • The units are smart and sophisticated in their appearance. • As far as security is concerned, these units are very secure and deter burglars. • The units come with rock-based mineral fibre insulation.

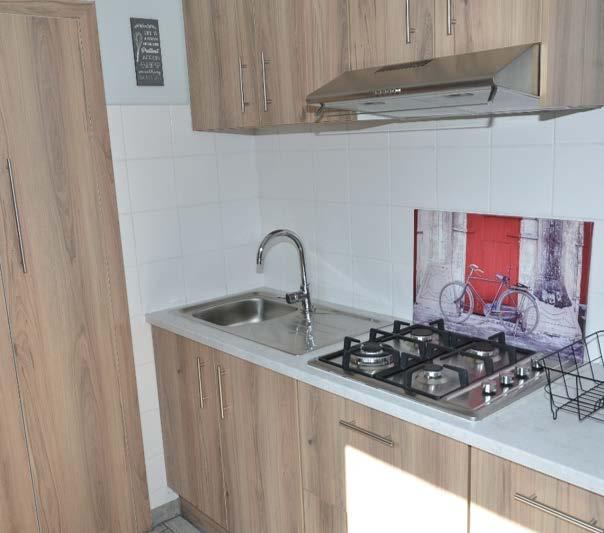