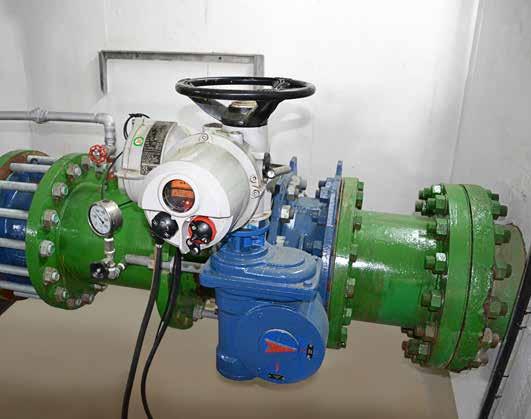
6 minute read
It was said in WASA
A leader in fluid control solutions, APE Pumps was appointed by Umgeni Water to manufacture, supply, deliver and commission Pump 4 at Verulam Pump Station.
Valves, actuators and instrumentation
Advertisement
New mechanical/ electrical installation at Verulam and La Mercy Pump Station
Located in La Mercy, the Verulam Pump Station lies within eThekwini Municipality about 27 km north of Durban, close to King Shaka International Airport. The Verulam and La Mercy Pump Station is part of the Hazelmere Water Treatment Works and has six pumps – four pumps dedicated to the La Mercy area and two pumps for the Verulam area. Water from 18 HC) – complete with piping, auxiliaries, valves, instrumentation and a motor. The pump was specifically designed to fit into the footprint of the old pump,” says Peter Robinson, a director at APE Pumps who managed the entire project.
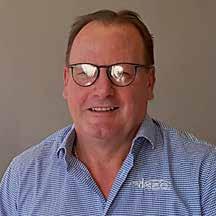
the Verulam side of the pump station is pumped to a holding tank at Grange that distributes to surrounding areas. The La Mercy side of the pump station also acts as a backup to the Avondale Pump Station that supplies Ballito. Water from the Verulam side services a population of 70 000 people.
“APE Pumps replaced a split-case pump with a new vertical turbine pump (APE Variable-speed drive (VSD)

Pump 4 was fitted with a 650 kW VSD, where, instead of running two pumps in line, only one pump would be used. This is because Pump 4 can deliver in excess of what the two pumps could currently achieve.
“The VSD will help to minimise life-cycle costs because the pumps will not be switched on and off repeatedly. By reducing the pump speed, the water flow is reduced and the reservoir level is maintained. The pump will therefore run for longer at lower speeds and heads. Then as water demand increases, the pumps will run at increased speeds to meet the demand,” explains Robinson.
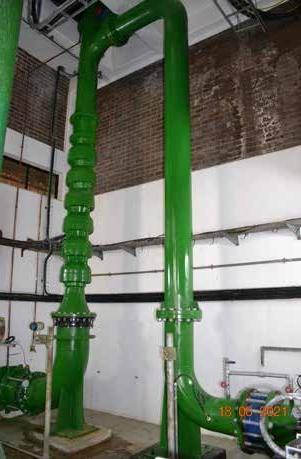
ABOVE Pump suction and delivery lines, manufactured by APE
FAR LEFT Peter Robinson, director at APE Pumps
LEFT Kelwyn Davidson, project manager at OBS
After problems were experienced with the switchgear and induction motors, APE Pumps was further tasked with replacing the medium-voltage switchgear from the 6.6 kV, 2.2 kV transformer. Six 500 kW soft starters were installed – an extra one was included for future expansion plans.
The 490 kW motor was replaced with a 650 kW motor and the pumps can run from 1 200 rpm to 1 650 rpm. Auxiliaries and pipe work to Pump 4 were supplied new, as was the instrumentation.
It was important to keep a flow of water to both Verulam and La Mercy. The pump station had to remain functional while the work took place, so APE Pumps worked around the parameters of Umgeni Water.
Avondale Pump Station had operational issues and shutdowns, with La Mercy pumps acting as backup supply. “Shutting down the La Mercy pumps was not possible, and this required flexibility on the part of all players, with strict adherence to windows of opportunity for shutdowns. These very tight timelines were set to prevent any shortages of water supply to any of the systems and reservoirs.
“We could not shut off the pump station; it is a large system and the taps have to have water in them at all time. We had to carefully plan our work. APE Pumps would cut off a panel and work on one side of an incomer, and transfer cables from one side to the other, so that everything was running on one system. The La Mercy and Verulam areas would be fed by one pump while we worked on the other pump. damage to the pumps and assists with preventative maintenance.
The new La Mercy Pump 4 now produces between 600 m3/h and 1 100 m3/h, and 24.6 Mℓ/day, working on the VSD.
We had to take the transformer and the available kilowatts into consideration,” says Robinson.
APE Pumps was responsible for the transportation and offloading of equipment on-site. It was found that the existing crane could not accommodate the weight of the existing and new equipment, so we had to replace it.
During the project, various outside factors influenced the programme of works – the obvious being Covid-19 and the strict protocols in place. Access was restricted at times to the plant at Hazelmere.
Ageing infrastructure and equipment made the transition from the old to new equipment a challenge at times. Two existing Verulam pumps were removed and refurbished, with new valve spools on the delivery lines supplied to eliminate or minimise potential problems in the foreseeable future. A split-case pump was sent to APE Pumps for refurbishment, and the motor was serviced at LHM in Durban. Furthermore, a brand-new APE 18 HC pump and motor was supplied, to ensure a backup pump is always ready to replace Waterloo Pump 2 in the event of any mechanical failures of the refurbished pump.
Instrumentation was installed on all pumps to evaluate pressure, vibration and temperature, as well as a humanmachine interface (HMI). The pumps will automatically be turned off when their pressure, vibration and temperature move outside set parameters. This prevents serious Contract Participation Goals
“APE Pumps has been fortunate enough to work with OBS Mechanical Electrical Turnkey Projects, a Level 1 BBBEE company, for transformation purposes. We trained a number of young people during the manufacture, installation and commissioning of Pump 4,” says Robinson.
Kelwyn Davidson, project manager at OBS, says APE Pumps and OBS have developed a seamless partnership. “Furthermore, Umgeni Water was fantastic to work with – they embraced suggestions to improve the basic day-to-day running of the systems and methodology to safeguard the ageing equipment. Everyone worked as a team. I look forward to future projects with both APE Pumps and Umgeni Water.”
OBS has already partnered with APE Pumps on a number of Umgeni Water projects. The company has expertise in many areas of engineering, along with water movement and treatment.
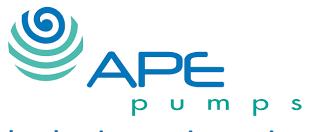
www.apepumps.co.za
APE VERTICAL TURBINE PUMPS
Manufactured locally, APE vertical turbine pumps have the following features: • Civil work is easier and cheaper • Installation is easier • There is no suction valve, with consequent cost and pressure-loss savings • Efficiencies are good • Net positive suction head (NPSH) problems are eliminated • Space is saved and, by using weatherproof motors, no need for a building to be erected • There is no danger of flooding the electrics • By adding stages, a very wide range of duties can be covered with standard parts, thus making for cheap and readily available spares • The pumps generally have a non-overloading kW characteristic, and a steep head quantity curve • There are no radical loads on the bearings or glands, so they last longer and maintenance is reduced • In dirty water, grit tends to fall vertically out of the wear areas and so does less damage
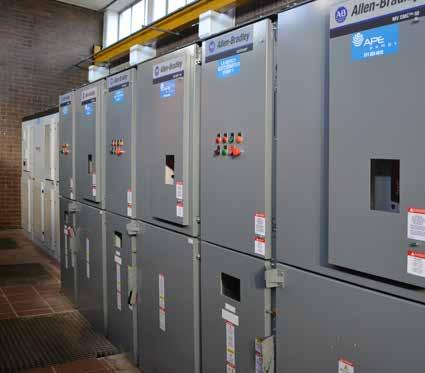
500 kW soft starters