
4 minute read
Hot Seat
GOING GLOBAL WITH SLUDGE DEWATERING EQUIPMENT

Advertisement
Sludge dewatering equipment manufacturer Teknofanghi exports 95% of all manufactured units from its factory in Italy. Giampiero Donida, Head of Global Sales, speaks to Water&Sanitation Africa about the business of thickening and dewatering sludge from wastewater As an treatment. sludge Italian coming company with from the an impressive global treatment process is footprint, do you feel there sometimes more demanding are differences between the in certain areas (like big sludge handling industry in cities) and less restrictive in South Africa and the other rural areas. countries you operate in? GD There are no significant With over 30 years of differences between South experience in sludge Africa and other countries. handling, has the There are slight disparities technology changed regarding legislation. But during this period? if you look at any single Some new methodologies in country, the dewatering of sludge drying are starting to

A MONOBELT plant at the Zeekoegat WWTW
appear. But the most notable trend in the industry is the need to remotely control and monitor sludge handling equipment. Automation is important. Our clients also want equipment that is simple to operate, as they do not want to rely too much on manufacturers and suppliers for training or maintenance. Teknofanghi designs and manufactures equipment based on these demands.
What sets Teknofanghi apart from the competition? We export the majority of our equipment, so it is important that the life-cycles costs in terms of transportation, commissioning, operation, maintenance and service are as low as possible. When choosing sludge handling equipment, one has to take into account these additional costs.
Teknofanghi continually invests into research and development, where we focus on a ‘plug and play’ approach. Our machines are dispatched fully assembled. Technicians are not needed for the start-up and commissioning of our equipment. This means that our equipment is up and running with no delays and lower expenses. Furthermore, it is shipped in standard containers, making transport safer and less costly.
Dewatered sludge Giampiero Donida, Head of Global Sales, Teknofanghi
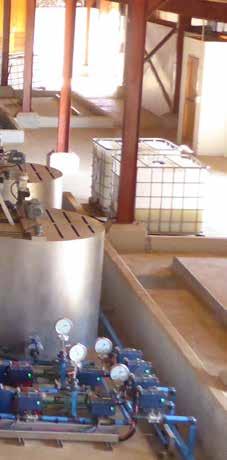

How are you contributing towards sustainable sludge management? Sludge management is only a part of our focus on sustainability – we like to look at the full picture. When developing our equipment, we consider the disposal of materials of construction as well as our equipment’s running costs in terms of electricity consumption. We have also invested a substantial amount of money into the installation of a photovoltaic system in our factory.


What types of technical support do you offer in terms of training, breakdowns, maintenance and spare parts in South Africa? As stated earlier, we have designed our equipment to be easy to install, operate and maintain, with minimal training required. Maintenance can be done by operators or local technicians. Furthermore, the South African market is familiar with our equipment and we have developed several local partnerships that can supply spares (many of which are market standard). As we have a large export market, we also make sure that it is easy for companies to purchase parts directly from us in Italy should they need them, and we do provide online support.
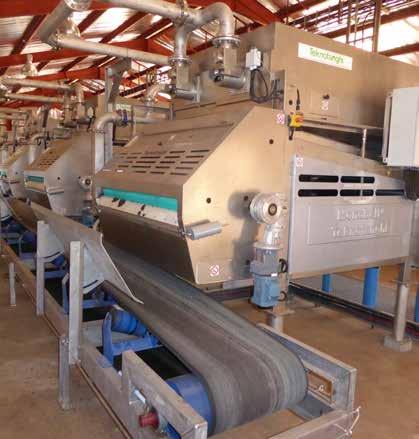
Give a brief description of your product range and tell us about your most popular product sold in South Africa and why? The range of Teknofanghi technologies covers applications in sludge dewatering from very small municipal and industrial plants to large municipal potable and wastewater treatment works. We supply: • MONOBELT belt presses for larger and very large applications • TEKNOBAG-DRAIMAD bags for smaller applications • SCRUDRAIN rotary drum thickeners with
Archimedean screw inside • SCRUPRESS dewatering dehydrator press • POLYDILUTION polymer units for polyelectrolyte preparation and mixing • other dewatering plant accessories like pumps, mixers and conveyors. We also supply package solutions that contain all of the equipment required for a working plant.
Our most successful product in South Africa has been the MONOBELT, which is ideally suited for average to large municipal wastewater treatment plants. It is a belt filter press with thickener that is combined into one machine and has its own control panel, washing pump and bottom tank.
The MONOBELT can be supplied in different sizes, ranging from 2 m3/h to 150 m3/h, depending on the quantity of sludge to be dewatered. We created special spray nozzles for belt washing to ensure that a limited amount of washing water is used. The simple design is covered by a patent and permits the use of endless belts, which grants three times longer operational life than traditional belts with clipper seams.
www.teknofanghi.it
The MONOBELT is easy to install, operate and maintain; it is used in areas where skilled operators are difficult to find or sophisticated technologies are unaffordable. In 2014, Teknofanghi supplied seven large belt presses to the Zeekoegat WWTW in the City of Tshwane, Gauteng.