
8 minute read
Water Conservation
V&A Waterfront’s journey to saving water
Residents in drought-stricken Cape Town are not the only ones who have tightened their taps. The V&A Waterfront (with 24 million visitors annually) has taken numerous steps towards saving water. By Kirsten Kelly
Advertisement
Regarded as the premier tourist destination in South Africa, the V&A Waterfront has applied green business practices throughout its portfolio. Mareli Cloete, senior manager: SHE & Utilities, mentions that the mixed-use waterfront has implemented water-saving initiatives since as far back as 2008. “We realised back then that water resources were coming under pressure. Over the years, the V&A Waterfront has committed to optimal levels of resource efficiency.”
Measuring water usage In order to improve water efficiency, one must measure water usage. The V&A Waterfront has various monitoring and metering systems and processes. These include smart metering systems, a building management system, leak detection systems, and a metric indicator dashboard that shows real-time tenanted consumption data. For irrigation, the property is divided into zones. Each zone is fitted with its own water meter, isolation valves and leak detection system, so it is easy to monitor consumption and repair leaks. The V&A Waterfront has a dedicated Utilities team that focuses on trend analysis.
Concentrating on attracting ‘green tenants’, the V&A Waterfront has implemented a ‘green lease’ that contains performance clauses on reporting and consumption. Water meters are installed in all tenant premises.
“We measure our performance against a 2010 baseline. Today, the V&A Waterfront has reduced its water consumption by almost 60% – even though the size of the property has increased by way of development,” states Cloete. A number of water-saving initiatives and tools have been implemented.
Landscaping Drip irrigation has the potential to save water and nutrients by allowing water to drip slowly to the roots of plants, either from above the soil surface or buried below the surface. The goal is to place water directly into the root zone and minimise evaporation. Cloete says that roughly 6 000 m² are fed by drip irrigation, which only makes up 12% of the total landscaped area.
“The rest of the area uses spray irrigation, where we run the system for only 30 minutes, as opposed to one hour, and we try to use non-potable water as much as possible. All irrigation is turned off during the winter months, only allowing for irrigation during summer months. We have also replaced water-thirsty plants
Mareli Cloete, senior manager: SHE & Utilities, V&A Waterfront
V&A WATERFRONT FACT SHEET
• Established in November 1988 as a wholly owned subsidiary by Transnet. • Today, it is jointly owned by Growthpoint
Properties and the Government
Employees Pension Fund (GEPF), represented by the Public Investment
Corporation (PIC). The V&A Waterfront is a mixed-use destination located in the oldest working harbour in the southern hemisphere. • As a mixed-use development, the
V&A Waterfront comprises residential and commercial property, hotels, retail, dining, leisure and entertainment facilities for both local and international visitors. • There are 23 000 people working at the V&A Waterfront itself, while total employment (including indirect jobs) is 66 000. • Over 24 million people visit the
V&A Waterfront annually. • The V&A Waterfront covers 23 hectares of land. • It has over 450 retailers. Retail shopping hours are from 09:00 to 21:00, 364 days of the year, with Christmas Day trading being optional for tenants. • It boasts more than 80 eateries, including restaurants, coffee shops and fast-food outlets. • Hosting 10 hotels, the V&A Waterfront has 1 487 rooms available.
with indigenous plants and hard landscaping.” Indigenous plants require little to no water. Areas such as the V&A’s lookout embankment are covered with many water-wise plants, as the slope does not allow for effective irrigation without water run-off. However, some of the historical gardens still contain exotic plant species (about 65% of these are palm trees) and there is a commitment to replace them with indigenous plants as and when they die.
Boreholes and greywater According to Cloete, the V&A Waterfront reduces the use of potable water by using borehole and greywater in its place wherever possible. The V&A Waterfront is fitted with two boreholes – one of which is functioning. The other will be activated once a water-use licence has been obtained as part of the water recovery programme and wastewater treatment plan.
“The functioning borehole serves to irrigate some sections of Dock Road, and contractors use this water for ad hoc work such as cleaning. The landscaping team also has a water trailer and the same water is used in areas where irrigation is done by hand. We are careful not to extract too much water, as this borehole tends to turn saline.
“Recycled or borehole water is also used for hard surface cleaning; we have retrofitted a water tank and high-pressure washer on a trailer to make this easier. All car washes use rainwater harvesting and water recycling systems. And the toilets in the Victoria Wharf, Granger Bay Court and Food Market shopping centres use greywater,” says Cloete.
Water resource recovery facility (WRRF) Cloete adds that Organica wastewater treatment technology will be used to provide the V&A Waterfront with a further non-potable water source.
“The Organica Food Chain Reactor is a combination of activated sludge and fixed-film technology that improves the performance of wastewater treatment plants. While still

All V&A car washes use rainwater harvesting and water recycling systems
A D V A N C E D W A T E R P R O D U C T S
U L T R A V S O L U T I O N S

using activated sludge in suspension, an additional surface area is introduced into the reactor through the introduction of plant roots as well as artificial supporting media. The plant roots (up to 1.5 m deep) and artificial supporting media act as fixed-film carriers. This allows for many more microorganisms to be compacted into the same volume and the natural plant roots increase the biodiversity within the reactor – further improving its performance.”
Organica biomodules act as the artificial supporting media and are installed next to reactor plants to allow for the migration of a vast diversity of microorganisms throughout the entire reactor. This enhanced habitat stimulates the formation of food chains in the reactor, leading to predation that results in the disposal of smaller amounts of excess sludge.
Still under construction, the WRRF will consist of various process units: • Raw wastewater will be collected into existing sumps, where a portion will be abstracted, treated and then used as irrigation water. Non-biodegradable particulates will be removed through fine screening and grit removal. • The screened wastewater will then flow to the reactor, which consists of various zones – each with their own aeration requirements. As the wastewater flows through the reactor, it will be treated by different microorganisms that are adapted to each zone for the most efficient treatment. With the microorganisms located in fixed-film structures, less energy is required to keep them in suspension. Air is therefore used for the purpose of oxygenation instead of mixing. • The reactor consists of two anoxic zones for denitrification and four aerobic zones for the nitrification and
decarbonisation of wastewater. • The mixed liquor from the reactor will then be coagulated and flocculated and transferred to the hydro cyclone for liquid/solid separation. • Underflow (sludge) is then partially returned to the reactor and partially wasted back to the municipal sewer. • Overflow (treated effluent) is again flocculated and filtered, before being disinfected with ultraviolet light and a sodium hypochlorite solution. This disinfected water is then ready to be reused as irrigation water. Additional water saving fittings were added: • Toilets and urinals – The V&A Waterfront has a combination of waterless toilets and urinals, as well as toilets and urinals fitted with an air-propelled system (technology that creates a vortex when flushed, therefore only using one litre of water). • Water sensor taps in all bathrooms – An aerating water-restrictor is fitted to each tap and the sensor timings adjusted to a minimum. Bathrooms across the properties are fitted with plumbing accessories that have reduced the water flow from 6 ℓ/minute to 1.25 ℓ/minute. • Air-conditioning plants – Seawater cooling is used for all the air-conditioning plants in the Silo District and Clock
Tower buildings. A district cooling plant produces chilled water at a central plant when seawater goes through a heat exchanger and cools via a closed loop. Cool water is then distributed to cool the buildings, therefore not making use of the conventional method of using potable water for air-conditioning purposes.
Proactive maintenance and leak detection Finding and repairing water leaks has always been a priority for the V&A Waterfront because they have the potential to cause massive water losses. “We aim to repair all leaks within 24 hours of reporting and often do so even earlier. Since we have installed pressure-reducing valves in our water lines, there have been fewer burst pipes and leakages, as well as a 30% reduction in incoming water consumption. Furthermore, there is a system in place where we can monitor water consumption in real time, and this provides valuable guidance on where to focus our conservation efforts. If abnormal flow rates are detected, alarms will notify us and cut off the system – further reducing our repair times and water losses.
Cloete concludes that due to the perceived cost factor, many people think that green buildings are more expensive than non-green buildings. “This is not the case. Apart from green buildings being cheaper to operate, current technologies have advanced to such an extent that the return on investment period has been shortened immensely.”
Further water saving plans Looking to the future, the V&A Waterfront plans to implement: • A desalination plant will be completed by early 2022. It will be a permanent installation that can produce 3.2 Mℓ/day of water. • A blackwater treatment plant, in the form of an on-site sewage facility (septic system), will treat the water before discharging it into the greywater tank. • The district cooling plant will be connected to the Victoria Wharf
Shopping Centre. • Greywater storage systems, water filtration systems and boreholes will be included in all new build development specifications.
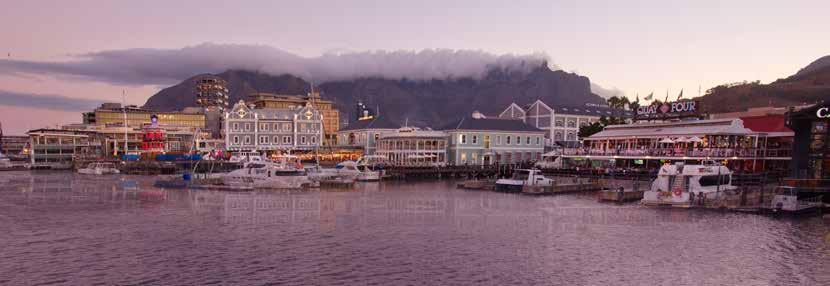