
4 minute read
Sedimentation as a water and wastewater treatment process
A recently held webinar on sedimentation formed part of the WISA Process Controllers Division’s Back-to-Basics series. With most of the same principles applicable to both water and wastewater treatment, it was decided to discuss this process unit from both angles in one session.
When talking about sedimentation, it is impossible to leave out coagulation and flocculation – as without them, there would not be a proper sedimentation process,” says Mbali Sibiya, process and quality technician at Umgeni Water and member of WISA’s Process Controllers Division.
Advertisement
What is coagulation and flocculation?
Coagulation is the process of adding a coagulant (polymer, alum) to raw water to destabilise the colloidal matter in the water to allow for it to form settleable floc. This happens in the rapid mixing stage and is a key element in the removal of turbidity from water.
Flocculation is the process of allowing the floc formed in the coagulation process to grow in size by slow mixing. The process is followed by a sedimentation tank where the floc is allowed to settle out.
The factors that affect these processes include:
• Coagulant dose – the jar test is done to estimate the minimum coagulant dose required to achieve certain water quality goals.
• pH – the efficiency of the coagulant depends on the pH of the water and coagulant itself.
• Intensity of stirring or mixing (the G value).
• Time – for chemical mixing and allowance of floc formation.
“Jar testing is where we will add coagulants into the jars of the raw water that we are treating to determine the correct dosage of the coagulant and coagulant aid. It is a procedure that mimics what takes place in the actual treatment plant. It will show the coagulation process and the formation of floc,” explains Sibiya.
The process to choose the correct coagulants for the source water is a lengthy process, as only certain ones can work with certain types of raw water.
Coagulants are affected by the minerals and type of suspended solids in the raw water. This is why water utilities conduct lengthy trials with different types of coagulants. The trial typically begins with the jar test.
Sedimentation
Sedimentation is the process in which the flocs that have been formed during coagulation and flocculation are allowed to settle from the water. The flocs collect as sludge that, as it has a higher density than water, sinks to the bottom of the sedimentation tank (from where it must be removed on a regular basis).
The clean water or supernatant then leaves the sedimentation tank through collection troughs located at the top of the tank. Factors that affect sedimentation are:
• particulate and water quality (key for sedimentation process)
• changes in temperature, alkalinity, turbidity and colour
• coagulation-particle characteristics – size, shape and density
• choice of coagulant
• flocculant aids
• surface loading flow rate per unit of surface area (settled water quality deteriorates when surface loading is increased)
• water treatment residue (sludge) – frequency of desludging can affect the sedimentation process (it shouldn’t be removed too often or too infrequently).
In water treatment, the aim is to achieve the maximum removal of sediments or suspended solids in the sedimentation process.
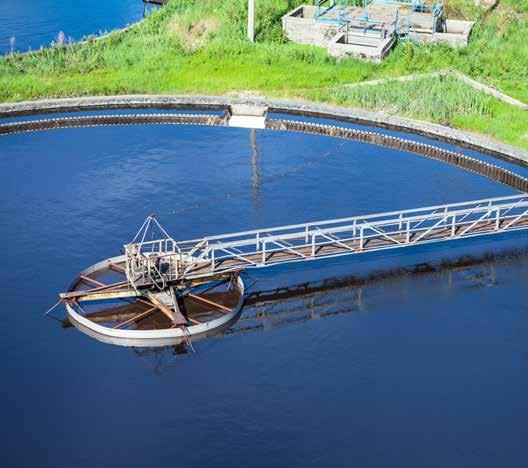
Settling tanks
When dealing with wastewater, the separation of the solid and liquid phases is just as crucial.
“At wastewater treatment works, we deal with both primary sedimentation and final settling (secondary sedimentation). Primary sedimentation is typically found before a bio-filter. The primary sludge that settles out in the primary sedimentation tank must, however, be treated to make it stable for further disposal. Secondary sedimentation is found after the activated sludge plant or biological filters,” explains Jabulani Chauke, Pr PC Water (Professional Process Controller), who co-hosted the session.
Design criteria for primary sedimentation tanks are the surface overflow rate and hydraulic detention time, while secondary settlement tanks are designed around surface and solids loading rates.
The scraper moves just below the surface to move all floating debris Primary settling tanks Primary settling tanks are physical processes used in conventional treatment plants for gravity separation of settleable solids in wastewater.
They are designed to remove a significant portion (up to 40%) of the biochemical oxygen demand and total suspended solids loading on a plant – making it easier on the secondary biological portion of the system.
Secondary settling tanks Secondary settling or clarification is required after secondary treatment has taken place in the activated sludge reactor and/or biofilters.
The purpose of clarification is to prevent biosolids from entering the receiving water body, where they could accumulate, decay, cause odours and degrade the water. In the case of activated sludge, the clarification process has the additional purpose of separating the biomass from the liquid or for it to be recycled and retained in the system – as return activated sludge.
Secondary settling tanks are named after the process that produces effluent. The two types of secondary settling tanks are:
• Humus tanks: - effluent from biofilters - remove sloughed off biofilm.
• Clarifier: - effluent from activated sludge reactor - settle out the activated sludge.