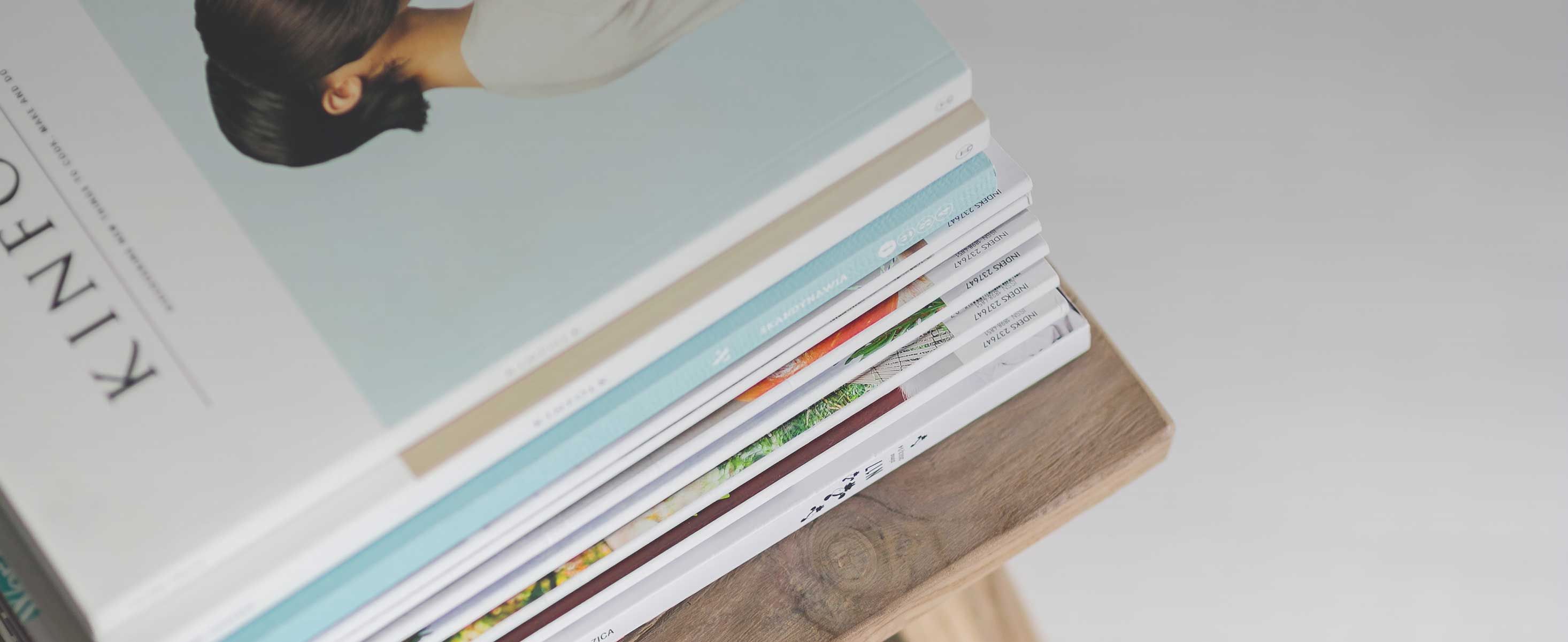
2 minute read
Replenishment Fundamentals (Executive Summary
EXECUTIVE SUMMARY
Inventory is a substantial investment in an industrial business and requires management. Structural Inventory is caused by faulty or non-responsive system processes. Inefficiencies in replenishment systems cause Transaction Created Inventory; the subject of this paper.
Inventory management is affected by Inventory Costs which include Item Cost, Soft Costs, Carrying Costs, Storage Costs, and Risk Costs. There are transaction costs associated with ordering, packaging, and stockouts that are embedded in inventory cost. Transportation costs can be affected by replenishment design in that they are usually borne at a purchase order level. There is also a noninventory system management cost to manage the variables in replenishment systems.
Inventory can be controlled using ABC Class Codes. Such codes can stipulate Service Level and other managerial objectives for groups of parts with common management denominators. Service Level is affected by both supply and demand conditions. Independent ordering systems, which decouple supply and demand, can also create inefficiencies in replenishment. ABC Class Codes are derived from Inventory Ranking, which is a process of grouping parts into common denominator groups. In addition to Service Level, Turnover (i.e. inventory turns) is another key performance indicator that measures a replenishment system’s effectiveness. There are a variety of statistical concepts and standards that can provide an analyst a means to rank inventory.
The five primary steps in replenishment are Recognition, Evaluation, Buying, Configuring, and Order
Execution. RFQ (Request For Quote) is a wasteful process as part of a normal replenishment scheme. There are four primary independent ordering systems ─ MIN/MAX; Order Point/Order Quantity (OP/OQ); Up To (also known as Period Order Quantity); and Economic Order Quantity (EOQ). MIN/MAX and OP/OQ use static variables for replenishment that require attention and management. Up To and EOQ use dynamic variables that change with business conditions. The Order Point is calculated the same in both processes. EOQ uses a formula to calculate Order Quantity that considers the intersection of Order Costs, with Carrying Costs. EOQ is considered the superior method.
Epicor P21® has a variety of tools and some limitations, but largely supports all four replenishment methods. Conversion, Cost Pages, Carrier ID Codes, Terms Codes and Purchase Target Value (PTV) are useful tools to automate Purchase Order Entry and configuration.
Setting up an effective replenishment system involves using these tools to develop inventory ranking and to apply replenishment methods to the proper Class Code strategy. The actual design process is completed at the Supplier level first, and then at the Item level, using Class Codes developed in the Inventory Ranking process. A system of continuous improvement known as “yield management” , following implementation, will ensure that Service Level is optimized and inventory is minimized.